段取りとは? 効率的に作業を進めるための準備
決められた期限までにゴールイメージを確実に実現するために、仕事を進める準備を整える事を「段取りをつける」と呼びます。
「段取り」は、もともと歌舞伎の構成や展開のことを示す言葉だったといわれています。今ではもっと広く、さまざまな分野で物事を行う順序や手順、準備のことを指す言葉として使われています。
工場での段取りとは、必要な道具を揃えておいたり、手順、工程の順番まで決めておき、いつでも取り掛かれるようにし、切り替え時間を短縮できるように準備しておく事をいいます。
段取りの定義
段取りは種々の意味で使われていますが工場で使われている段取りはJIS*(日本工業規格)で定義されている“段取り”です。
具体的には、JISZ814『生産管理用語』では「作業開始前の材料、機械、治工具、図面などの準備及び試し加工のことであり、段取は、機械又はラインを停止しないで行う外段取と、機械又はラインを停止して行う内段取に大別される。また、10分未満の内段取をシングル段取という。」
又、JSBO112『鍛造加工用語』では「生産していた製品を異種の製品に変更するために行う金型の準備及び後始末作業。」と定義されています。
言い換えれば、現製品から次製品を生産するための準備作業や生産品種切り替え作業、後始末作業といった現製品の生産終了から次製品の適合製品を生産するまでの一連の作業を総称して段取りと呼んでいるのです。
ここで現製品から次製品へ段取りした具体例を示すと、下図のようになります。
段取りがなぜ必要?
製造メーカーのほとんどは、単一製品のみの生産ではなく、複数種類の製品を生産しています。
複数の製品を生産するのにそれぞれ専用の生産設備または生産ラインを構築してしまったら、製品の種類分だけ生産設備または生産ラインを持たなければならなくなってしまいます。これではヒト、モノ、カネ、情報といった経営資源がいくら有っでも足りず、とても新製品の開発などに経営資源を配分することができなくなってしまいます。
これら問題を解決するためには、同一の生産設備または生産ラインで複数種類の生産対象品を生産したり、別のカテゴリ一の製品を加工できるようにして、製品の種類よりも生産設備または生産ラインの数を少なくする必要があるのです。
このように、ある生産設備または生産ラインが、複数種類の製品を加工できるようにするために、段取りが必要となるのです。これによって設備投資費用を抑えるとともに、生産スペースが少なくてすむようになるのです。
段取りのメリット
ある生産設備または生産ラインで段取りを実施して複数種類の製品を生産することによって、少ない費用で複数の品種の製品が生産できる、専用ラインをもたなくてすむ、設備の稼働率を向上できる、所要スペースが少なくてすむ、など下図のような多くのメリットを得ることができるようになります。
そのため各メーカーとも効率的、経済的な生産を実現するべく段取りを実施して、企業経営上の多<のメリットを享受しているのです。
段取りの構成
現在生産している製品から次に生産する製品へと生産品目を切り替える段取り作業は、一般に準備作業、交換作業、調整作業ならびに後片付け作業の四つの作業から成り立っています。
準備作業とは、次に生産する製品用の段取り部品や工具類、ワークを取り揃えて機械、設備に準備する作業の事。
準備作業のポイントとしては、製品ごとに必要な段取り部品や工具類をーか所にまとめておく、5Sやロケーション管理を実践するなど、すぐに取り出して運べる状態にしておくことが挙げられます。
交換作業とは、今までの製品の生産に供していて次製品の生産には使用することができない段取り部品や工具類を当該生産設備や生産ラインから取外しで、次製品生産用の段取り部品や工具類に交換・取付ける作業の事。
交換作業のポイントとしては、ボルト類の種類や数を減らしたり、使用工具数を減らしたりする。などを挙げることができます。
調整作業とは、次に生産する製品に求められた要求仕様を満足するように必要個所に手を加える作業を言い、品質確認が含まれます。
調整作業のポイントとしては、芯出しや位置決め、クランプ、平行出し、倒れ修正などの作業を簡素化できるよう再現性の向上などを挙げることができます。
一方、後片付け作業とは、先述の交換作業で取外した段取り部品や工具類、余ったワークなどを所定の位置に片付けて、次回の生産に備える作業を言います。
後片付け作業のポイントとしては、段取り部品の保管場所確保やセット保管など、次の生産にいつでも正常・良好に使える状態にしておくことなどが挙げられます。
これらの一連の作業は下図のような段取り作業サイクルのようになります。
段取りの区分
外段取り(英語:off-Line Set-Up)とは
機械設備を止めなくてもできる段取りのことをいう。つまり作業を中断しなくても段取り作業が進められる。
たとえば次に生産する製品用の段取り部品や工具類、ワークなどを対象となる生産設備や生産ラインが稼働中にあらかじめ準備しておいたり、交換した段取り部品などを後片付けしたりすることを外段取りと呼んでいるのです。
外段取りを行なうことによって、当該生産設備または生産ラインの稼働率や生産性を向上させることができます。
しかし手作業が多い生産設備や生産ラインの場合には、当該作業者はそちら作業
にかかりきりになってしまい、外段取りにまでは手が回らないケースが多く存在します。
このような場合には、責任者や段取り専門作業者が段取り応援を実施して外段取りを担当し、生産設備または生産ラインの稼働中に外段取りを実施することが大切となります。これによって、生産設備や生産ラインの停止時間を少なくすることが可能になります。
内段取り:(英語:on-Line Set-Up)とは
今まで生産していた製品(現製品)から次に生産する製品(次製品)へと生産品目を切り替える際に生産設備または生産ラインを停止して行なう段取り作業を総称して内段取りと呼び、その作業を内段取り作業、その作業に費やす時間を内段取り時間という。
内段取りをしている間は、当該生産設備や生産ラインを稼働させることができませんので、効率的、経済的な生産を推進するうえでは、内段取り時間を短縮することが重要となります。
内段取り時間を短縮するために、準備作業や後片付け作業に要する時間を短縮するとともに段取り前や段取り後の生産中にそれら作業を行なう、いわゆる内段取りの外段取り化を推進することが重要となります。
そのうえで生産設備や生産ラインを停止させないとできない交換作業や、調整作業に要する時間を短縮して段取り時間を短縮させます。
調整時間:
設備の条件を次に流す製品に合わせて調整する時間をいう。 段取り作業の一部である調整作業は、次に生産する製品に求められた品質要求事項などの生産仕様を満足するように、交換作業で交換した段取り部品や工具類の位置や寸法などの必要個所に手を加えて、正規状態にする一連の作業のことを言い、内段取りで行なわれることの多い作業となっています。
具体的な作業としては、交換部品の芯出しや方向決めといった位置決め、寸法出し、平行出し、倒れ修正、試加工などの一連の作業が該当します。
これら段取り畤の調整作業は交換作業とセットで実施され、品質確認まで行なう必要があります。
内段取りの外段取り化とは
内段取りで行なっていた段取り作業の一部を、生産設備または生産ラインが稼働中でも行なえるように該当する段取り作業の順序を入れ替えたり、やり方を変えたりして外段取りで行なえるようにすることを、内段取りの外段取り化と言います。
具体的には段取り作業中の生産完了した製品用の取外した段取り部品や工具類、ワークなどの後片付け作業、次に生産する製品用の段取り部品や工具類、ワークなどの準備作業が該当します。
これらの作業を当該生産設備または生産ラインが稼働中に並行して行なうことによって、段取りのための設備停止時間を少なくすることができるようになるのです。
このように内段取りの外段取り化は、段取り作業者の段取り意識を改革して短時間に段取りするための創意工夫を促すといったようにあまりコストをかけずに段取りによる設備停止時間を短縮できる方法となっています。
つまり、設備改善をすることなく作業改善で大きな効果を得ることができる方法なのです。このため内段取りの外段取り化は、段取り改善の基本となります。
段取りの種類
生産現場で実施されている段取りは、新規生産品に対応するための段取りと既存製品に対して行なう段取りの二種類に大別することができます。前者はスポット的な段取り、後者は日常的な段取りとも言えます。
新製品対応や生産変更、需要変動などの新規生産品に対する段取りには、新製品の生産立ち上げなどの新製品対応段取りや設計変更による段取り、生産変動による段取り、特急対応による段取などといった種類があります。
一方、日常的に行なっている段取りとしては、シングル段取りやゼロ段取り、タクト内段取り、ワンショット段取り、ワンタッチ段取り、秒のシングル段取り、自動段取りなどといった段取りを挙げることができます。
1.シングル段取りとは10分未満、いわゆる1桁の分単位の時間内で行なう段取り
2.ゼロ段取りとは通常1分以内で行なえる段取り
3.タクト内段取りとはタクトタイム内に行なう段取り
4.ワンショット段取りとはサイクルタイム内に行なう段取り
5.ワンタッチ段取りとはワンタッチクランプの採用など、段取り部品を一度の動作で交換できる段取りのこと
6.秒のシングル段取りとは10秒未満、いわゆる卜行の秒単位の時間内で行なう段取り
7.自動段取りとは生産設備が自動的に行なう段取り
なお、段取り改善を実施する際の目標として加工職場ではシングル段取り、組み立て職場ではワンタッチ段取りを設定している職場が多いです。
誰が段取りを実施するか?
生産設備または生産ラインの段取りを現状で誰が行なっているかを見てみると、当該生産設備や生産ラインの操作に長けた作業者、または当該職場の責任者が段取りを行なっているケースが一般に多くなっています。
何故ならば、段取り作業中に当該生産設備や生産ラインの作業者に手待ちの発生を抑制して、少人数で多品種を生産できるように指向しているからなのです。
そのため、当該生産設備や生産ラインの生産を任せられるようになった作業者には、次のスキルアップとして段取りを行なえるように教育・訓練を施しているのです。
これによって、当該作業者に多種類の製品の生産を任せることができるようになるとともに、当該製品のモノ造りに責任感をもって主体的に取組んでもらうことができるようにしているのです。
作業者自らが段取りを行なう生産設備や生産ラインでは、当の作業者が生産を行なっている間は段取りに着手することができません。しかも段取りの最中は、既に生産を完了した生産設備や生産ラインが停止して待機状態になっています。
つまり、作業者が段取りをしている間は、他の生産設備または生産ラインを稼働させることができずに停止させてしまい、稼働率や生産性を落としてしまうといった問題を内包しているのです。
そのため当該生産設備または生産ラインの能力不足と、判断されてしまう危険性を併せ有しているのです。
また、他者に段取りを任せたとすると、当該製品のOCDに対する責任があいまいになり、作業者の責任感が希薄になってしまうおそれもあります。又、段取り作業そのものが生産設備や製品によって異なるため、段取りを任せられる作業者を育成するのに時間がかかる、などといった問題点も出てきます。
これらの問題点を解消させるために、段取りを任せられる作業者を組織的、計画的に育成したり、段取りそのものをなくしたり簡素化した、などと段取そのものの見直し改善を全社的な観点て推進していく必要があるのです。
段取りのキーポイント 再現性
段取り時間を短縮するには再現性を向上させる必要がある。
再現性とは、ある事象を成立させている要素や要因といった環境を同じ条件にすれば、同じ結果が再度現われてくる性質のことを言います。
繰り返し生産を遂行する時間の中で、段取り時間そのもののばらつきは大きく、同じ段取り作業者が同じ段取り作業を実施しても、それに要する時間には、ばらつきが発生してしまいます。ましてや、段取り作業者が異なれば、段取り時間に大きな差が出てしまうのです。
なかでも調整作業に再現性が乏しいことが大きな要因として挙げられます。たとえば、加工位置などを調整する場合に一発で寸法がOKになったり、何度も寸法調整を繰り返さないとOKにならなかったりして、調整作業時間が大きくバラツクことがあるのです。
このように効率的、経済的に段取りを行ない短時間で製品切り替えを完了させるには、段取り時の再現性を向上させることが不可欠となっています。
これら再現性を向上させる具体例としては、生産設備などに突き当て基準を設置したり、選択ストッノパーを採用したりするなどして、交換部品の位置や寸法などの再現性を上げていくのです。
これによって、段取り時の調整作業における調整そのものを簡素化し、作業者の負担を軽くして効率的、経済的な段取りが行なえるようにしていくのです。
段取りのための準備と手順
強い生産体制の構築の為には現状の生産実績、段取り実績を把握し、あるべき姿と比較することにより各種の問題点が明確になり、効率的な改善に繋がり、生産リードタイムの短縮、在庫の削減、原価低減等の対策が可能になります。
段取り準備
- 作業手順の標準化:
- 作業手順を標準化し、誰でも同じ方法で作業できるようにします。これにより、ばらつきを減らし、効率を向上させます。
- 工具や材料の事前準備:
- 必要な工具や材料を事前に準備しておくことで、作業中の無駄な動きを減らします。工具や材料の配置も整理整頓しておくことが重要です。
- 内段取りと外段取りの区別:
- 内段取り(機械を停止して行う作業)と外段取り(機械を動かしながら行う作業)を明確に区別し、可能な限り内段取りを外段取りに変えることで、生産停止時間を減らします。
- 5S活動の徹底:
- 整理、整頓、清掃、清潔、しつけの5S活動を徹底することで、作業環境を整え、効率的な作業を実現します。
段取り手順
- 段取り替えの計画:
- 段取り替えの計画を立て、必要な作業をリストアップします。計画には、作業の順序や時間配分を含めます。
- 段取り替えの実施:
- 計画に基づいて段取り替えを実施します。作業手順に従い、効率的に作業を進めます。
- 段取り替えの時間計測:
- 段取り替えにかかる時間を計測し、データを収集します。これにより、改善点を見つけ出し、次回の段取り替えに活かします。
設備故障や品質トラブルなどの予期せぬ問題等で後日、生産状況を検証したするうえでも、生産設備や生産ラインの日々の生産実績や段取り実績などを記録に残しておくことが、必須です。
この生産実績や段取り実績を記録する方法の一環として、下に例示したような生産実績表兼段取実績表を作成し、記録に残します。
これによって、いつ何製品を何個生産しその後に誰が次製品の生産用にどのくらいの時間を要して段取りを実施し、品質確認を誰が行なって次製品の生産を開始したのかがわかるようにしているのです。
このような記録を残すことによって、担当作業者たちに責任感をもって生産に取組んでもらうようにするとともに、予期せぬ問題が発生した場合などに解析の基礎データにします。
下記をクリックするとファイルがダウンロードできます。
- フィードバックと改善:
- 段取り替えの結果をフィードバックし、改善点を共有します。継続的な改善活動(Kaizen)を行い、段取り替えの効率を向上させます。
これらの準備と手順を実施することで、段取り替えがスムーズに進み、生産効率の向上が期待できます。
工場での段取り 時間短縮 改善の進め方と改善事例
TPMでは段取り改善について、図表のような7ステップが用意されている。
1 | 分 析 | 段取リ替え作業の内容を分析する |
2 | 「探す」の排除 | 5Sのうち、整理・整頓を徹底する |
3 | 内段取リと外段取リの区分 | 外段取リ(事前準備・事後始末など)機械・ラインを止めなくてもできる段取りはないか |
4 | 内段取リの外段取リ化 | 内段取リ機械・ラインを止めなければならない段取リを外段取リ(プリセッティング)にできないか |
5 | 内段取りの改善 | その1二変数の定数化品種によって変わる寸法や位置、変数を一定の寸法や位置、定数にする |
その2:位置決め、寸法出しの改善ワンタツチセツトにできないか | ||
その3:着脱の改善ワンタッチ着脱、着々作業の検討 | ||
その4:並行作業の実施を検討する | ||
6 | 調整の排除 | ここまでのステツプの改善でなお残る調整を排除する |
7 | 段取リ替え作業の標準化と訓練 | 段取リ替え作業の十分条件動作ができるまでの訓練を実施する |
ステップ1:段取りの分析
実際の段取り作業の内容を、手順ごとに所用時間を計測し、下図のような表を使って見えるように整理する。
ビデオカメラで段取り作業を撮影すると、繰り返し確認できるし、また詳細な分析が可能になる、会議室での改善案検討時にも活用することができる。
改善の4原則
調査内容から作業毎のムダ・ムラ・ムリの摘出、外段取り化の
検討やECRSによる対策案の検討などを行う。
ECRSとは改善の4原則である。
E(Eliminate) :排除…その作業を止められないか
C(Combine) :結合…AとBの治具を組み合わせられないか
R(rearrange) :置換…aとbの作業を入れ替えられないか
S(Simplify) :簡素化…簡単にできないか
ステップ2:「探す」の排除と改善事例
1)「探すムダ」の排除
探すムダを排除するための基本的な考え方は、5S、定置管理を徹底することである。 5S面では、「整理(いるものといらないものを区分する)」と「整頓(いるものがすぐ取り出せ、戻しやすい状態)」を順をおって実行する。
2)「移動・運搬のムダ」の排除と改善事例
治具・工具・部品の「移動・運搬のムダ」は、点在する置場のレイアウトの悪さも1つの要因である。段取り場所のできるだけ近くに設置し、ロスを少なくする。また、運搬する場合は一度の運搬でできるようキット化し、専用台車で運搬する。
段取りに使用する工具は、工具棚から準備するのではなく、段取りする場所に専用化し設置するとよい。
ステップ3:内段取りの外段取りの区分
1ステップで調査した内容をもとに、内段取りと外段取りに区分する。内段取り、外段取りのルールが不明確なため、大きなロスが発生していることを見逃さないことが重要である。
ステップ4:内段取りの外段取り化
外段取り化の改善対象は、対象作業が機械を止めないとやれないのか、止めずにやる方法はないのかを検討することである。
事前準備を徹底することで、外段取り化が達成できるのである。
たとえば、次の生産に使用する金型、治具、工具、刃具のプリセット化などに加えて、部品の準備までできるのではないだろうかを検討する、また、生産後の品質記録も加工開始後に実施すれば外段取りとなる。
内段取りの外段取り化の改善事例
ステップ5:内段取りの改善
(1)基準の統一|変数の定数化と改善事例
機種によって変わる寸法、位置を一定の寸法、位置に定数化できないか検討する。その着眼点は加工基準の統一や、位置決めに対する基準を定数化することである。
また、設計面で検討を加えることにより、お客様と打合わせのうえで加工に必要なクランプのための「余肉」をつける等の検討し可能な限り機種によって変わる変数(寸法、位置等)を統一する。
改善前:袋の種類 8種類 改善後:4種類
(2)位置決め、寸法出しの改善と改善事例
次に「一発で位置決めできないか」「ワンタッチでセットできないか」「目盛を見ないでできないか」などを検討する。すなわち、調整作業を排除するための方法を見つけ出すのである。
(3)着脱の改善事例
着脱作業の効率化は、取付け・取外し作業のすべてに対しワンタッチ着脱化を図ることである。着脱に使用する工具、ボルトなどの締付け具毎に着目する。昔から言われていることだが、「ボルト1本親父の仇き」というくらいの気持ちで行う。
(3)並行作業の実施と改善事例
大型設備やラインの段取り作業は、作業範囲が広く歩行ロスが大きなウェイトを占めるケースが多いものである。そうした場合は、複数人で作業を行えば要する時間は短くなる。作業範囲や時間的タイミングを考慮し、互いに待ち時間がないか確認しながら、どうしたら並行作業が可能か検討する。
ステップ6:調整の排除
目盛を読んでの寸法調整は止め、ワークごとにブロックを作り、基準部に突き当て一発で寸法決めをする。
更に位置決めの改善などで見つけた基準値の設定を改善すれば調整作業は排除できる。
段取りがうまくいけば、調整はやらないこともある・・・
ということは、本来やらなくても良い作業です。
調整の排除の改善事例
ステップ7:段取リ替え作業の標準化と訓練
改善された段取り作業の内容は、従来の標準書とは様変わりしているはずである。
ベストの状態を維持するためには、段取り替え作業手順書や基準書を作成し、それに基づいて誰もが同じ手順で、同じ時間で作業ができるよう訓練を繰り返すことが必要である。
段取リ替え作業の標準化の改善事例
時間的な段取り
生産タイミングを合わす:時間を同期させる
生産量を可能な限り平準化(均一化)する為に前もって生産体制の日程調整(スケジューリング)することも大切です。
前もって時間的に多忙な時期を把握してその体制を事前に準備してください。
又、停滞待ちが断続的に発生しないように他のライン、設備等と同期させて連続的に繋がるようにし、停滞待ちを有効に活用できるよう改善してください。
時間的段取り 改善事例
改善前は加工機の号機はバラバラに運転しており運搬、OP作業が同期しておらず、バッファーとして余分な仕掛品が必要であったが改善後は一時間一回のサイクルで運搬経路、時刻を決めたので仕掛品が不要になった。更に手待ち時間がまとまったので他の付帯作業が可能になった。
段取りマンの役割と育成
段取りマンは、製造現場において段取り替えの効率化と標準化を担当する重要な役割を担います。具体的な役割には以下のようなものがあります:
- 段取り替えの計画と実施:
- 段取り替えの計画を立て、効率的に実施します。作業手順を標準化し、誰でも同じ方法で段取り替えができるようにします。
- 工具や材料の準備:
- 必要な工具や材料を事前に準備し、段取り替えの時間を短縮します。
- 内段取りと外段取りの管理:
- 内段取り(機械を停止して行う作業)と外段取り(機械を動かしながら行う作業)を明確に区別し、可能な限り内段取りを外段取りに変えることで、生産停止時間を減らします。
- 5S活動の推進:
- 整理、整頓、清掃、清潔、しつけの5S活動を徹底し、作業環境を整えます。
- 段取り替えの時間計測と改善:
- 段取り替えにかかる時間を計測し、データを分析して改善点を見つけ出し、効率化を図ります。
育成方法
段取りマンを育成するためには、以下のような手法が有効です:
- 教育と訓練:
- 段取り替えの基本的な知識や技術を教育し、実際の作業を通じて訓練します。定期的な研修やワークショップを開催することが効果的です。
- OJT(On-the-Job Training):
- 実際の作業現場での指導を通じて、段取り替えのスキルを身につけさせます。経験豊富な作業者が新人を指導することで、実践的なスキルを習得させます。
- 標準作業手順書の作成:
- 段取り替えの標準作業手順書を作成し、全員が同じ手順で作業できるようにします。手順書を基に訓練を行うことで、ばらつきを減らします。
- フィードバックと改善:
- 段取り替えの結果をフィードバックし、改善点を共有します。継続的な改善活動(Kaizen)を行い、段取り替えの効率を向上させます。
これらの手法を組み合わせて実施することで、段取りマンの役割を効果的に果たし、生産効率の向上が期待できます。
段取り改善における課題
段取り改善における課題には、以下のようなものがあります:
- 標準化の難しさ:
- 作業手順を標準化することは重要ですが、現場ごとに異なる条件や作業者のスキルレベルに対応するのが難しい場合があります。
- 内段取りと外段取りの区別:
- 内段取りを外段取りに変えることは効率化に繋がりますが、全ての作業を外段取りにするのは難しいことがあります。
- 工具や材料の準備:
- 必要な工具や材料を事前に準備することが重要ですが、これが徹底されていないと段取り替えの時間が長くなります。
- 5S活動の徹底:
- 整理、整頓、清掃、清潔、しつけの5S活動を徹底することが求められますが、現場全体での意識統一が難しいことがあります。
- 作業者の教育と訓練:
- 作業者のスキル向上が必要ですが、教育や訓練に時間とコストがかかるため、継続的な実施が難しい場合があります。
- 段取り替えの時間計測と分析:
- 段取り替えの時間を計測し、データを分析することで改善点を見つけ出すことが重要ですが、データの収集と分析が十分に行われていないことがあります。
これらの課題を克服するためには、現場の状況をよく把握し、継続的な改善活動を行うことが重要です。
段取りと自動化の関係
段取りと自動化は、生産効率を向上させるために密接に関連しています。以下に、段取りと自動化の関係について説明します:
段取りの効率化
段取りの効率化は、自動化の導入により大きく改善されます。
- 内段取りと外段取りの区別:
- 内段取り(機械を停止して行う作業)を外段取り(機械を動かしながら行う作業)に変えることで、生産停止時間を減らします。自動化により、外段取りの作業がさらに効率化されます。
- 工具や材料の自動供給:
- 自動化されたシステムにより、必要な工具や材料が自動的に供給されるため、段取り替えの時間が短縮されます。
- 自動化による標準化:
- 自動化されたシステムは、作業手順を標準化し、一貫した品質と効率を実現します。これにより、段取り替えのばらつきが減少します。
AI・自動化の導入
AI・自動化は、段取りの効率化だけでなく、全体の生産プロセスの改善にも寄与します。
- AIロボットの導入:
- AIロボットを導入することで、段取り替えの作業を自動化し、作業者の負担を軽減します。これにより、作業者はより高度な作業に集中できます。
- 自動化された監視システム:
- AI自動化された監視システムにより、設備の状態をリアルタイムで監視し、異常を早期に検知して対策を講じることができます。
- データの活用:
- 自動化されたシステムは、大量のデータを収集し、分析することで、段取り替えの改善点を見つけ出し、効率化を図ります。
これらの手法を組み合わせて実施することで、段取りと自動化の相乗効果により、生産効率の向上が期待できます。
*Chat Gptによる段取り改善は下記の記事が参考になります。
関連記事:Chat Gptで段取りを爆速化:方法論・プロンプト大全・業種別改善事例
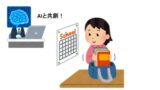
まとめ
TPM(Total Productive Maintenance)における段取り改善は、生産効率を向上させるための重要な取り組みです。
標準化の難しさ、内段取りと外段取りの区別、工具や材料の準備、作業者の教育と訓練等の課題がありますがこれらの課題を克服するためには、現場の状況をよく把握し、継続的な改善活動を行うことが重要です。
関連キーワード:
OEE 5S なぜなぜ分析 TPM 予防保全 5S活動
無料ダウンロード 資料『段取りの改善』
Googleスライド 『段取りの改善』無料ダウンロード
Googleスライドから無料で『段取りの改善』の資料がダウンロードできます。
slideshare ダウンロード資料(PDF)
パワーポイントで作成した資料です。
引用文献:
今日からモノ知りシリーズ トコトンやさしいTPMの本
現場力を高める実践的TPM入門【改訂版】
わかる!使える!TPM入門 〈基礎知識〉〈段取り〉〈実践活動〉/日本プラントメンテナンス協会
わかる!使える!TPM入門 〈基礎知識〉〈段取り〉〈実践活動〉/日本プラントメンテナンス協会
コメント
[…] 参考サイト:段取りの改善 […]
[…] 関連記事:段取りの改善 […]