TPMにおける個別改善の重要性と実践方法
TPM(Total Productive Maintenance)は、生産システムにおけるあらゆるロスをゼロにすることを目指す活動です。その中でも、「生産効率化の個別改善」は、生産ラインや設備ごとにロスを調査・定量化し、個々の問題を解決することで、全体的な生産性を向上させるための重要な取り組みです。
個別改善のポイント
- ロスゼロを目指した極限追求: 災害ゼロ、不良ゼロ、故障ゼロを目標に、効率を阻害する要因を徹底的に追求し、ロスをゼロにします。
- 要因追求の徹底: ロスが発生する原因を深く掘り下げ、根本的な解決策を見つけることが重要です。
- 自主保全との連携: 個別改善は、自主保全活動と密接に連携することで、より効果を発揮します。
- 4M(人・物・方法・機械)の分析: ロス発生の原因を、人、物、方法、機械の4つの要素から多角的に分析します。
- PDCAサイクルの活用: 計画(Plan)、実行(Do)、確認(Check)、改善(Act)のサイクルを回しながら、継続的に改善を進めます。
個別改善の具体的な事例
- 設備の改善: 設備の故障頻度を減らすための予防保全の実施、生産スピードの向上のための設備改造など
- 工程の改善: 工程間の待ち時間を減らすためのレイアウト変更、作業の標準化、ムダな動きを削減するための改善など
- 品質の改善: 不良品発生の原因究明と対策、品質基準の厳守など
- 安全の改善: 安全事故防止のための対策、安全意識の向上など
個別改善を進める上での注意点
- 現場の意見を重視する: 現場の従業員が問題点に気づきやすく、改善策も提案しやすい環境作りが重要です。
- 小さな改善の積み重ね: 大きな改善だけでなく、小さな改善を積み重ねることも大切です。
- データに基づいた改善: データを収集し、分析することで、効果的な改善策を立案することができます。
- 全従業員の参加: TPMは、全従業員が主体的に参加する活動です。
個別改善の効果
- 生産性の向上: ロスの削減により、生産性が向上し、納期遵守率が向上します。
- 品質の安定化: 不良品発生率が低下し、製品品質が安定します。
- コスト削減: 設備の故障が減り、無駄な作業が削減されることで、コストが削減されます。
- 従業員のモチベーション向上: 改善活動への参加を通じて従業員のモチベーションが向上します。
TPM 故障ゼロの改善プログラム
TPM(Total Productive Maintenance)における「故障ゼロ」の改善は、生産システムの安定稼働と生産性の向上に不可欠な要素です。故障ゼロを目指した活動は、単に設備の故障を減らすだけではなく、設備の寿命を延ばし、品質の安定化にも大きく貢献します。
故障に関する一般的な課題
TPM(Total Productive Maintenance)において、故障は生産性低下、品質問題、コスト増大など、様々な問題を引き起こす要因となります。故障に関する一般的な課題を以下にまとめました。
製造部門の関心が低い
・工数上、作業者に生産以外のことはやらせない
・安全上、設備に触れさせない
・仕組みができてない

製造部門の関心
故障解析の取り組みが弱い
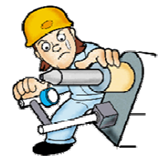
設備故障解析
・壊れた部位のスケッチが十分になされてない
・故障品を分解していない
・故障原因の追究が不十分、交換でのみで終了
・再発防止、歯止め、水平展開がされておらず
・現場での故障解析が不十分
保全システムとその運用が弱い
・点検周期・点検箇所・点検方法・判断基準などの基準不備
・部品交換、給油等が一目でわかる保全カレンダーの不備
・故障の履歴システム
予知保全に対する取り組みが弱い
・予知保全は設備について定期的に状態及び測定値の変化を観測し異常を判定 する方法(簡易診断と精密診断がある)
・簡易診断の定着後、精密診断を実施
・精密診断・・・振動量、電流負荷、タイミング、動作時間、温度、音等を数値化 し、管理し変化点を常時把握できる体制にする
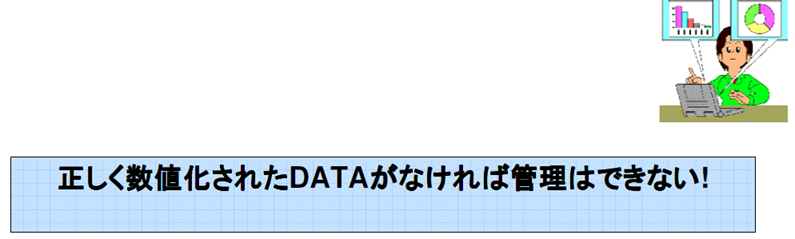
DATAにて予知保全の診断
故障低減の考え方
TPM(Total Productive Maintenance)における故障低減は、単なる設備の修理ではなく、生産システム全体を最適化し、長期的な安定稼働を実現するための重要な取り組みです。
故障低減の3つの柱
故障低減には、大きく分けて以下の3つの柱があります。
- 予防保全: 故障を未然に防ぐための活動です。
- 定期点検: 設備の定期的な点検を行い、摩耗や劣化を早期に発見します。
- 潤滑油管理: 適切な潤滑油を使用し、定期的に交換することで、摩耗を防止します。
- 部品交換: 寿命が近い部品を事前に交換することで、突然の故障を防ぎます。
- 予兆管理: 故障の前兆を早期に検知し、対策を講じる活動です。
- 振動診断: 設備の振動を測定し、異常を早期に検知します。
- 温度管理: 設備の温度を監視し、過熱による故障を防ぎます。
- 性能監視: 設備の性能を監視し、低下を早期に検知します。
- 自主保全: 現場の従業員が主体的に設備の保全活動に参加する活動です。
- 清掃: 設備を清潔に保ち、異物混入による故障を防ぎます。
- 異常発見: 普段から設備に触れることで、異常を早期に発見できます。
- 改善提案: 改善点を見つけ、積極的に提案します。
故障の分類整理
・簡単な故障と困難な故障を分類し、簡単な故障を優先して対策し低減させる
・分類・層別方法・・・ライン/発生箇所/故障モード/原因別等
故障解析
・設備に加わるストレス→機械、電気ストレス+温度・湿度・振動・粉塵
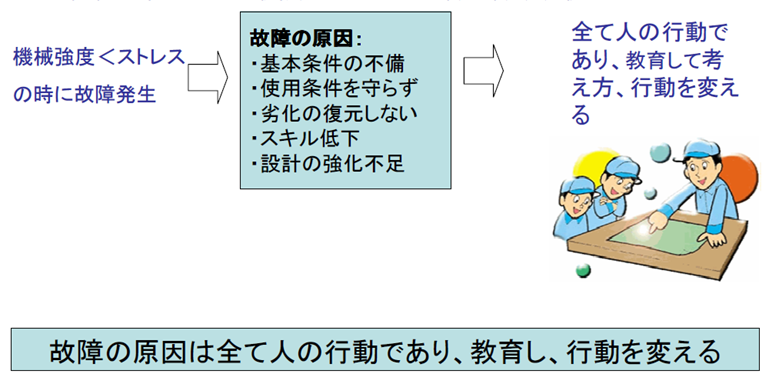
設備故障解析の教育
故障解析の進め方
故障解析は、TPM活動において非常に重要なプロセスです。故障を繰り返さないためには、根本原因を特定し、効果的な対策を講じることが不可欠です。
故障解析の一般的な手順
- 故障情報の収集:
- いつ、どこで、どのような故障が発生したか
- 故障前の兆候はあったか
- 故障時の状況
- 修理内容
- 過去の故障履歴
故障解析のポイント
- 現場主義: 現場で実際に発生した状況を把握し、関係者全員で議論することが重要です。
- データに基づいた分析: 故障データや設備の履歴データを活用し、客観的な分析を行うことが重要です。
- 多角的な視点: 故障の原因は、人、物、方法、環境など、様々な要因が複雑に絡み合っている場合が多いので、多角的な視点で分析することが重要です。
- チームワーク: 故障解析は、現場のオペレーター、保全担当者、エンジニアなど、様々な立場の人々が協力して行うことが重要です。
故障解析のツール
- 5Why分析: なぜ?を繰り返すことで、根本原因を特定する
- 魚骨図: 原因と結果の関係を図で表し、多角的に分析する
- パレート図: 故障の原因を頻度順に並べ、主要な原因を特定する
- 故障履歴データベース: 過去の故障データを蓄積し、分析に活用する
故障解析の事例
- モーターの焼きつき: 負荷がかかりすぎている、冷却ファンが故障している、潤滑油不足など、様々な原因が考えられます。
- センサーの誤動作: 配線が断線している、センサーが汚れている、ノイズの影響を受けているなど、様々な原因が考えられます。
- 配管の破損: 配管の経年劣化、振動による疲労、異物混入など、様々な原因が考えられます。
TPM 基本条件の整備
基本条件とは設備の清掃、給油、増す締めの三要素を言う、基本条件を整えることは設備の劣化を防ぐ活動であり、故障の原因を作らない為のもっとも重要な活動である。
なぜ基本条件の整備が重要なのか?
- 設備の寿命延長: 定期的な清掃、給油、増締めを行うことで、設備の摩耗や劣化を遅らせ、寿命を延ばすことができます。
- 故障の防止: 汚れや異物による故障、緩みによる故障などを未然に防ぎ、生産ラインの停止を減らします。
- 品質の安定化: 清潔な状態で設備を維持することで、製品への異物混入や品質低下を防ぎます。
- 安全性の向上: 設備の異常を早期に発見し、安全な作業環境を確保します。
- 従業員の意識向上: 基本条件の整備を通して、従業員の設備に対する意識を高め、自主保全の意識を醸成します。
基本条件の整備の内容
- 清掃: 設備の表面、内部、周辺を清掃し、汚れや異物を除去します。
- 給油: 摺動部や回転部に潤滑油を供給し、摩耗を防止します。
- 増締め: 緩んでいるボルトやナットを締め直し、振動やガタつきを防ぎます。
基本条件の整備を行う上でのポイント
- 標準化: 清掃、給油、増締めの手順を標準化し、誰でも同じように作業できるようにします。
- 定期化: 定期的に実施することで、設備の状態を常に良好に保ちます。
- 全員参加: 全員が責任を持って、基本条件の整備を行うことが重要です。
- 目視による点検: 清掃や給油を行う際に、目視で設備の状態を確認し、異常を発見します。
- 記録: 実施内容や異常を発見した場合は、記録を残し、改善に繋げます。
*PMにおける基本条件の整備は、設備の寿命を延ばし、故障を防止するための最も基礎的な活動です。清掃、給油、増締めといったシンプルな作業を継続的に行うことで、生産性の向上、品質の安定化、安全性の確保に貢献します。
TPM 使用条件の遵守
TPM(Total Productive Maintenance)において、使用条件の遵守は、設備の寿命を延ばし、故障を防止するために非常に重要な要素です。設備は、設計された範囲内で使用されることで、その性能を最大限に発揮し、長寿命化が期待できます。
なぜ使用条件の遵守が重要なのか?
- 設備の寿命延長: 設計された範囲内で使用することで、設備の摩耗や劣化を遅らせ、寿命を延ばすことができます。
- 故障の防止: 過負荷、過熱、異物混入など、設計外の条件下での使用は、故障の原因となります。
- 品質の安定化: 設計された条件下で使用することで、製品の品質を安定化させることができます。
- 安全性の向上: 設計外の使用方法による事故を防止し、安全な作業環境を確保します。
使用条件の遵守の具体例
- 速度: 設備の設計速度を超えて運転しない。
- 負荷: 設備の設計負荷を超えて使用しない。
- 温度: 設備の許容温度範囲内で使用する。
- 湿度: 設備の許容湿度範囲内で使用する。
- 振動: 過度の振動を与えない。
- 異物混入: 異物が混入しないように注意する。
劣化の復元
TPM(Total Productive Maintenance)において、劣化の復元は、設備の性能を維持し、寿命を延ばすために非常に重要な活動です。設備は、時間の経過とともに摩耗や劣化が進行するため、定期的な復元作業が必要となります。
なぜ劣化の復元が重要なのか?
- 性能の維持: 劣化部分を復元することで、設備の本来の性能を維持することができます。
- 故障の防止: 劣化が進行すると、故障のリスクが高まります。復元することで、故障を未然に防ぐことができます。
- 寿命の延長: 定期的な復元を行うことで、設備の寿命を延ばすことができます。
- コスト削減: 故障による生産停止や修理費用を削減することができます。
劣化の復元の方法
- 清掃: 汚れや異物を除去し、設備の機能を回復させます。
- 給油: 潤滑油を供給し、摩耗を防止します。
- 増締め: 緩んだボルトやナットを締め直し、振動やガタつきを防ぎます。
- 部品交換: 摩耗が激しい部品や破損した部品を交換します。
- 調整: 設備の精度を調整します。
劣化の復元を行う上でのポイント
- 標準化: 復元作業の手順を標準化し、誰でも同じように作業できるようにします。
- 定期化: 定期的に復元作業を行うことで、設備の状態を常に良好に保ちます。
- 目視による点検: 復元作業を行う際に、目視で設備の状態を確認し、異常を発見します。
- 記録: 実施内容や異常を発見した場合は、記録を残し、改善に繋げます。
設計上の弱点改善
TPM(Total Productive Maintenance)における設計上の弱点改善は、設備の根本的な問題点を解決し、長期的な安定稼働を実現するための重要な活動です。設備の設計段階で考慮されていない要因や、運用を通じて明らかになった問題点を改善することで、故障の頻度を減らし、生産性を向上させることができます。
設計上の弱点とは?
設計上の弱点とは、設備の設計段階で検討漏れがあったり、想定外の状況に対応できていなかったりといった、故障やトラブルの原因となる潜在的な問題点のことです。
- 強度不足: 負荷が集中する部分の強度が不足している。
- 材料の選定ミス: 使用環境に適さない材料が使用されている。
- 構造的な問題: 配管の配置が不適切、アクセス性が悪いなど。
- メンテナンス性の不足: 部品交換や調整が難しい構造になっている。
設計上の弱点改善の重要性
- 故障の根本原因の解決: 設計上の問題を改善することで、繰り返される故障を根本的に解決することができます。
- 設備寿命の延長: 設計上の問題を改善することで、設備の寿命を延ばすことができます。
- 生産性の向上: 故障が減ることで、生産性が向上します。
- コスト削減: 故障による修理費用や生産停止による損失を削減することができます。
設計上の弱点改善の手順
- 弱点の洗い出し:
- 過去の故障履歴を分析し、共通する原因を特定する。
- 現場の意見を聞き、潜在的な問題点を洗い出す。
- 3Dモデルやシミュレーションを用いて、設計上の問題点を可視化する。
- 改善策の検討:
- 問題点に対して、複数の改善策を検討する。
- コスト、効果、実現可能性などを考慮して、最適な改善策を選ぶ。
- 改善の実施:
- 設計変更、部品交換、構造の変更など、必要な対策を実施する。
- 効果検証:
- 改善策の実施後、効果を検証し、問題が解決されていることを確認する。
設計上の弱点改善の具体例
- モーターの過負荷: モーターの容量を上げる、冷却ファンを増設する。
- 配管の振動: 支持点を増やす、振動吸収材を使用する。
- センサーの誤動作: 耐環境性の高いセンサーに交換する、ノイズ対策を行う。
オペレーション、保全の技能向上
TPM(Total Productive Maintenance)において、オペレーターと保全員の技能向上は、設備の安定稼働と生産性の向上に不可欠です。両者の連携を強化し、それぞれのスキルを向上させることで、設備の寿命を延ばし、故障を減らし、品質の安定化を実現することができます。
オペレーターの技能向上
オペレーターは、設備を安全かつ効率的に運転するための知識とスキルを習得する必要があります。
- 設備の仕組みの理解: 設備の構造、各部品の役割、運転原理を深く理解することで、異常を早期に発見し、適切な対応を行うことができます。
- 運転操作の習熟: 正しい運転操作手順を習得し、安全な運転を行うことができます。
- 異常時の対応: 異常が発生した場合の対応手順を習得し、迅速かつ適切な対応を行うことができます。
- 品質管理: 製品品質に影響を与える要因を理解し、品質管理に貢献することができます。
保全員の技能向上
保全員は、設備の点検、整備、修理を行うための知識とスキルを習得する必要があります。
- 保全技術の習得: 機械加工、電気工事、溶接など、必要な保全技術を習得します。
- 故障診断能力: 故障の原因を正確に診断し、適切な修理を行う能力を養います。
- 予防保全の知識: 故障を未然に防ぐための予防保全の知識を習得します。
- 改善提案能力: 設備の改善点を見つけ、改善提案を行う能力を養います。
オペレーターと保全員の連携強化
オペレーターと保全員が連携することで、より効果的な設備管理が可能になります。
- 共同での点検: 運転員と保全員が共同で設備の点検を行うことで、異常を早期に発見し、故障を防止することができます。
- 情報共有: 運転員が発見した異常や改善点、保全員が実施した作業内容などを共有することで、相互理解を深め、連携を強化することができます。
- 共同での改善活動: 運転員と保全員が共同で改善活動を行うことで、より効果的な改善を実現することができます。
製造工場での段取り改善のための具体的な手法
製造工場での段取り改善は、生産効率を向上させるために非常に重要です。以下に課題と具体的な改善手法をいくつか紹介します:
段取り替えの一般的課題
- 作業手順の標準化不足:
- 作業手順が標準化されていないため、作業者ごとに異なる方法で段取り替えが行われ、効率が低下します。
- 工具や機器の精度問題:
- 使用する工具や機器の精度が低い場合、段取り替えに時間がかかり、不良品が発生しやすくなります。
- 作業者のスキル不足:
- 作業者のスキルや経験が不足していると、段取り替えに時間がかかり、ミスが増える可能性があります。
- 設備のメンテナンス不足:
- 設備のメンテナンスが不十分だと、段取り替え時にトラブルが発生しやすくなります。
- 段取り替え時間の把握不足:
- 段取り替えにかかる時間を正確に把握していないと、計画通りに生産が進まず、生産性が低下します。
これらの課題を解決するためには、作業手順の標準化や作業者の教育、設備のメンテナンスの徹底が重要です。また、段取り替え時間を定量的に把握し、改善点を見つけることも必要です
段取り替えの改善
段取り替えの改善は、生産効率を向上させるために重要です。以下にいくつかの具体的な改善手法を紹介します:
- 内段取りと外段取りの区別:
- 内段取りは機械を停止しないと行えない作業で、外段取りは機械を動かしながら行える作業です。内段取りを外段取りに変えることで、機械の停止時間を減らすことができます。
- 段取り時間の短縮:
- 作業手順を見直し、必要な工具や材料を事前に準備することで、段取り時間を短縮できます。また、段取り作業を標準化し、全員が同じ手順で作業できるようにすることも重要です。
- 5S活動の徹底:
- 整理、整頓、清掃、清潔、しつけの5S活動を徹底することで、作業環境を整え、無駄な動きを減らすことができます。
- 自動化の導入:
- 段取り作業を自動化することで、時間短縮と精度向上が期待できます。例えば、工具交換を自動化する装置を導入することが考えられます。
- 作業者の教育と訓練:
- 作業者に対する教育と訓練を行い、段取り作業のスキルを向上させることが重要です。これにより、作業の効率と品質が向上します。
これらの手法を組み合わせて実施することで、段取り替えの効率を大幅に改善することができます。
段取り改善の着眼点
段取りの着眼点には、以下のようなポイントがあります:
- 作業手順の標準化:
- 作業手順を標準化することで、誰が行っても同じ品質と効率で段取り替えができるようになります。
- 内段取りと外段取りの区別:
- 内段取り(機械を停止して行う作業)と外段取り(機械を動かしながら行う作業)を明確に区別し、可能な限り内段取りを外段取りに変えることで、生産停止時間を減らします。
- 工具や材料の事前準備:
- 必要な工具や材料を事前に準備しておくことで、段取り替えの時間を短縮できます。
- 5S活動の徹底:
- 整理、整頓、清掃、清潔、しつけの5S活動を徹底することで、作業環境を整え、無駄な動きを減らします。
- 作業者の教育と訓練:
- 作業者に対する教育と訓練を行い、段取り作業のスキルを向上させることが重要です。
- 段取り替えの時間計測と分析:
- 段取り替えにかかる時間を計測し、データを分析することで、改善点を見つけ出し、効率化を図ります。
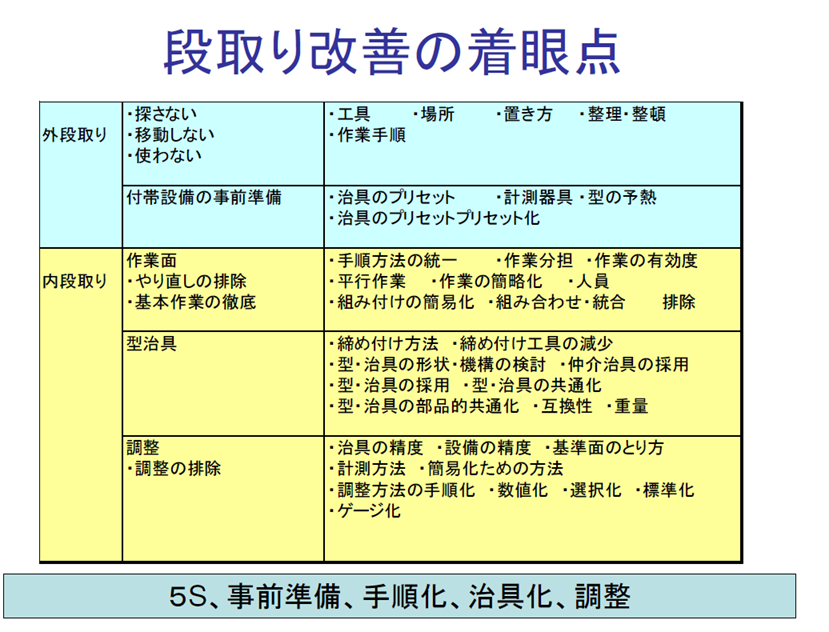
5S、事前準備、手順化、治具化、調整
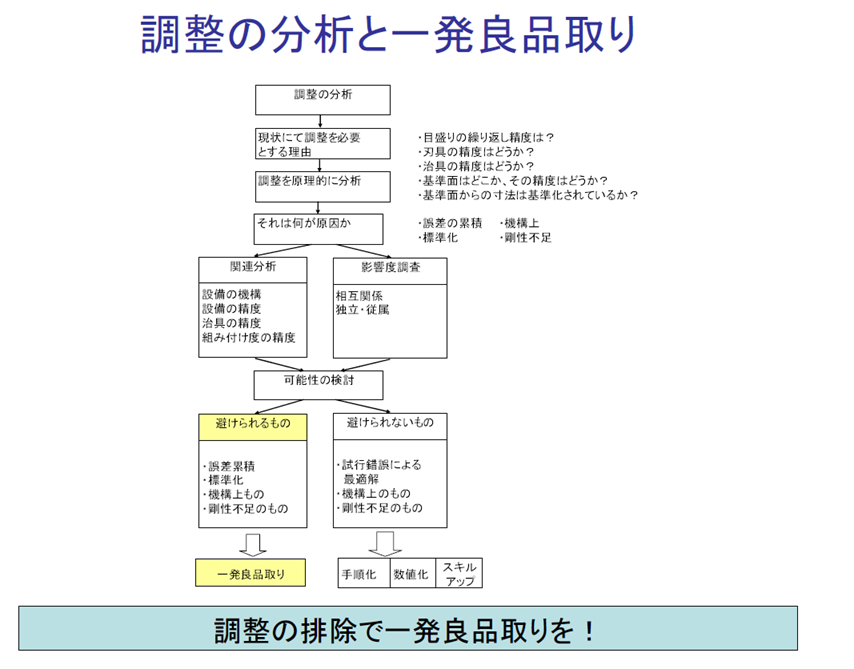
調整分析と一発良品段取り – 調整の排除で一発良品取りを!
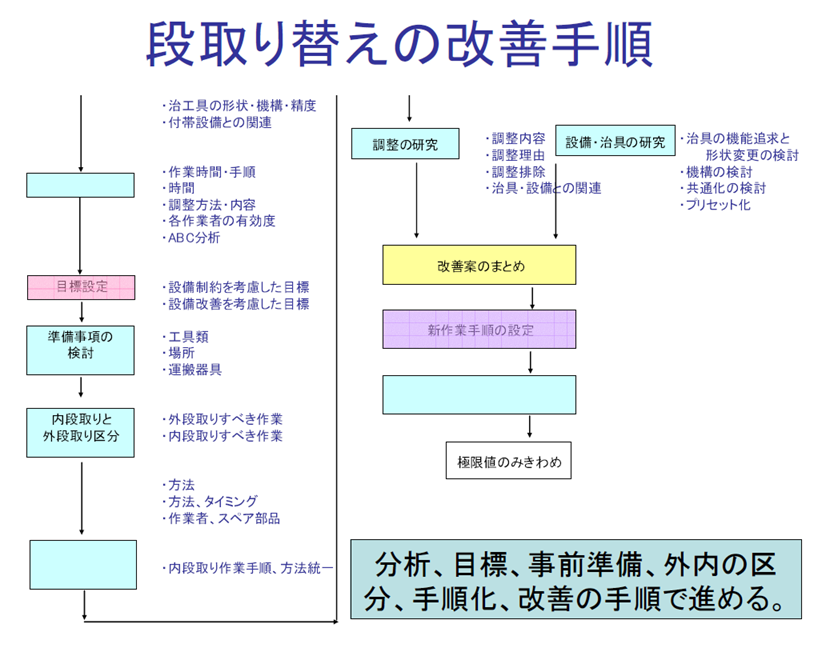
段取り替えの改善手順 – 分析、目標、事前準備、外内の区分、手順化、改善の手順で進める。
更に詳細の内容は下記の記事を参照願いします。
関連記事:段取りの改善
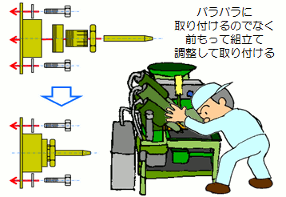
刃具ロス削減による生産性向上の改善手法
刃具ロスを削減することで生産性を向上させるための手法には、以下のようなものがあります:
- 刃具の寿命管理:
- 刃具の寿命を正確に把握し、適切なタイミングで交換することで、刃具の摩耗や破損によるロスを防ぎます。
- 定期的なメンテナンス:
- 刃具の定期的なメンテナンスを行い、刃先の状態を常に良好に保つことで、加工精度を維持し、ロスを減少させます。
- 自動化の導入:
- 刃具交換の自動化を導入することで、交換作業の時間を短縮し、作業者の負担を軽減します。
- 作業者の教育と訓練:
- 作業者に対する教育と訓練を行い、刃具の取り扱いや交換方法を徹底させることで、ミスを減らし、ロスを防ぎます。
- 刃具の品質管理:
- 使用する刃具の品質を管理し、信頼性の高い刃具を使用することで、予期せぬトラブルを防ぎます。
刃具寿命延長の進め方
刃具の寿命を延ばすための進め方には、いくつかの重要なポイントがあります:
- 適切な切削条件の設定:
- 切削速度、送り速度、切り込み深さなどの切削条件を最適化することで、刃具の摩耗を減らし、寿命を延ばすことができます。
- 冷却と潤滑:
- 切削中の温度を制御するために、適切な冷却剤や潤滑剤を使用することが重要です。これにより、刃具の過熱を防ぎ、摩耗を減少させます。
- 刃具の材質選定:
- 切削対象の材質に適した刃具を選定することで、刃具の寿命を延ばすことができます。例えば、耐熱性の高い材質を使用するなど。
- 定期的なメンテナンスと再研磨:
- 刃具の定期的なメンテナンスや再研磨を行うことで、切削性能を維持し、寿命を延ばすことができます。
- 工具の管理とモニタリング:
- 刃具の使用状況をモニタリングし、寿命が近づいた刃具を早めに交換することで、予期せぬトラブルを防ぎます。
これらの手法を組み合わせて実施することで、刃具の寿命を効果的に延ばし、生産効率を向上させることができます。
刃具平均寿命アップのポイント
1.一般的に刃具寿命は切削熱に伴う熱摩擦によるものと考えられてきた。すなわち、切削スピードが遅いほ ど、寿命は長くなり、早いほど短くなると。しかし、刃具は熱磨耗の影響だけでなくワークを含めた主軸系 のアンバランスのよる振動、刃具、ホルダー系の振動の共振による機械的な振動が刃具の磨耗に大きな ウェイトを占めているのである。
2.刃具寿命は観点を変えて振動解析の面から刃具寿命の延長を図ることが必要である。すなわち、刃具の 切削点の振動を測定し、現状の加工条件が最適かを検討する。
3.振動が最小となる切削スピード等の条件を見つければ刃具寿命が2倍以上延長される場合が多い。
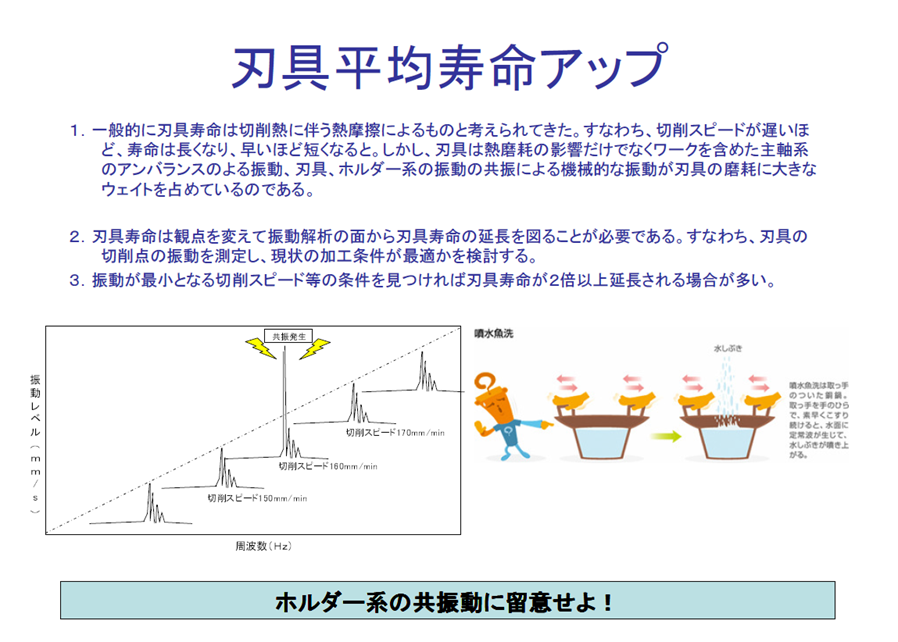
刃具寿命向上の方法 – ホルダー系の共振動に留意せよ!
刃具寿命・検知パラメータ
刃具の寿命を延ばし、適切なタイミングで交換するためには、いくつかの検知パラメータが重要です。以下に主要なパラメータを紹介します:
- 切削力:
- 切削中の力をモニタリングすることで、刃具の摩耗や破損を検知できます。異常な力が検出された場合、刃具の交換が必要です。
- 振動:
- 切削中の振動を測定することで、刃具の状態を把握できます。振動が増加すると、刃具の摩耗が進んでいる可能性があります。
- 温度:
- 切削中の温度を監視することで、刃具の摩耗や破損を予測できます。温度が異常に高くなると、刃具の寿命が短くなる可能性があります。
- 切削音:
- 切削中の音を分析することで、刃具の状態を評価できます。異常な音が発生した場合、刃具の交換が必要です。
- 切削速度と送り速度:
- 切削速度と送り速度を適切に設定し、モニタリングすることで、刃具の寿命を延ばすことができます。
これらのパラメータをモニタリングし、データを分析することで、刃具の寿命を効果的に管理し、適切なタイミングで交換することが可能です。
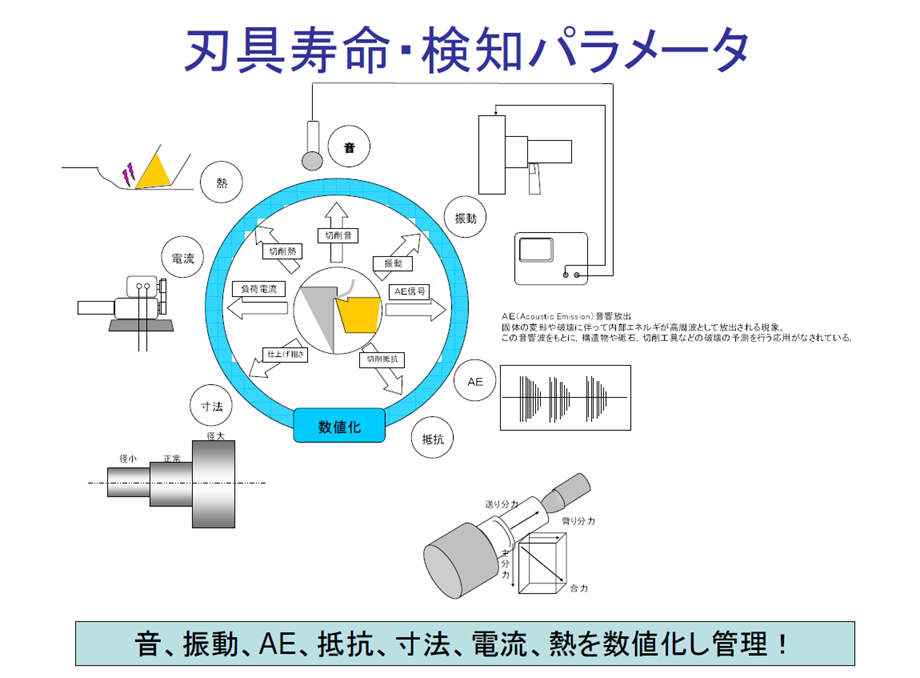
刃具寿命 検知 – 音、振動、AE、抵抗、寸法、電流、熱を数値化し管理!
効率的な生産を実現する立ち上がりロス対策
立ち上がりロスの一般的な課題
効率的な生産を実現するための立ち上がりロス対策には、以下のような手法があります:
- 定期的なメンテナンス:
- 設備の定期的なメンテナンスを行うことで、立ち上がり時のトラブルを防ぎ、スムーズな稼働を実現します。
- 作業手順の標準化:
- 作業手順を標準化し、誰でも同じ手順で作業できるようにすることで、立ち上がり時のミスを減らします。
- 設備の予熱:
- 設備を予熱することで、立ち上がり時の温度差によるトラブルを防ぎます。特に冬場や長期停止後には効果的です。
理論的研究不足:
立ち上がりの現象・・・寸法バラツキのため調整を繰り返す、機械の異常動作による刃具損傷
*熱変位・・設備の稼動に伴う熱変化により、設備の構成部品の一部が膨張・収縮 して、XYZのいずれかの方向に伸縮する現象によりワークと加工点(刃具等)の相対 位置が変わることである。
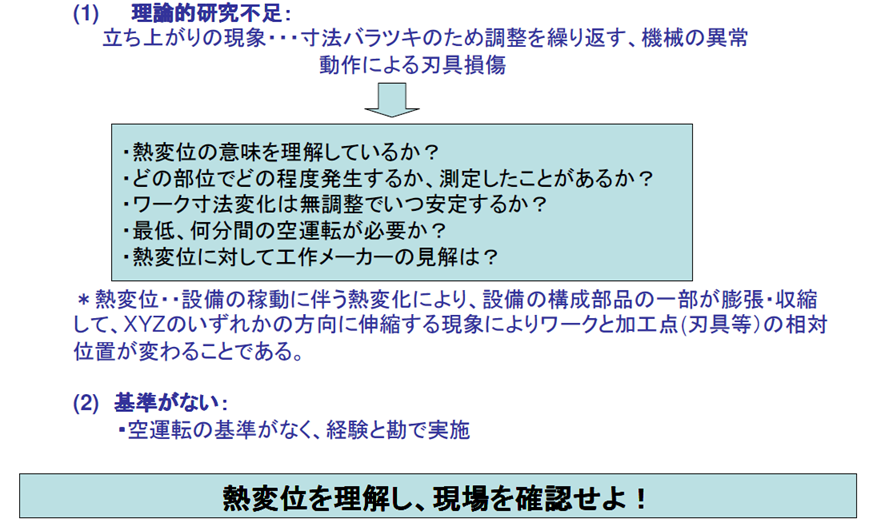
立ち上がりロス改善
生産現場での立ち上がりロスを効率的に改善する方法
測定:
設備の長時間停止から稼動を開始して品質が安定するまでの主軸、 テーブル等の温度変化を測定する。
材質検討:
・熱変位を最小にするための材質を工作メーカーに相談して検討する。
発生部を冷却
・冷却ファン等で熱を冷却する
自動補正
・変位量をあらかじめ見込んで自動補正する
設備の予熱:
- 設備を予熱することで、立ち上がり時の温度差によるトラブルを防ぎます。特に冬場や長期停止後には効果的です。
チョコ停(小停止)の改善の成功事例を徹底分析する方法
チョコ停(小停止)は、製造現場で短時間の生産停止を指します。具体的には、数分から数十分程度の停止を意味し、以下のような分類があります:
チョコ停(小停止)の一般的な課題
- 機械的なトラブル:
- 部品の摩耗や破損、機械の故障などが原因で発生する停止。
- 材料の供給不足:
- 生産ラインに必要な材料が一時的に不足することで発生する停止。
- 作業者のミス:
- 作業者の操作ミスや段取り替えの不備などが原因で発生する停止。
- 品質問題:
- 生産中に品質問題が発生し、調整や修正が必要となる停止。
- 外部要因:
- 電力供給の問題や外部からの影響で発生する停止。
チョコ停(小停止)は短時間の停止であるため、見過ごされがちですが、頻繁に発生すると生産効率に大きな影響を与える可能性があります。
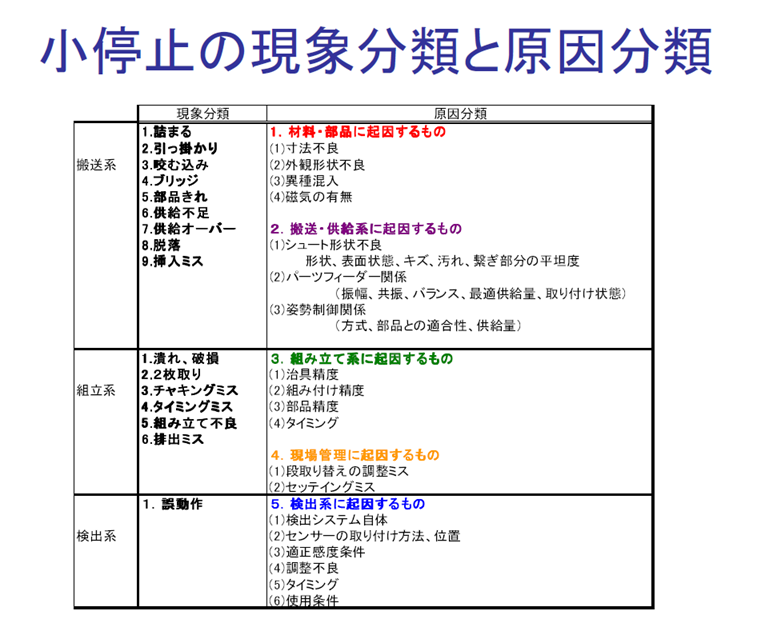
チョコ停(小停止)現象分類と原因分類
チョコ停(小停止)改善の対象
1.微欠陥の是正:
外観的 (キズ、磨耗)
寸法的 (必要な寸法精度、クリアランス)
作動 (ガタ、芯ずれ)
2.現場の基本原則の徹底
清掃 (汚れ、ガタ)の徹底
給油 (汚れ、磨耗)
増締め (ゆるみ)
3.基本作業の徹底
正しい操作
段取り作業 (調整の仕方、セッテイング)
設備の見方 (異常の見つけ方)
4.最適条件の検討
取り付け条件 (角度、位置、共振、エアー圧、真空度、振幅)
加工条件 (最適供給量)
5.あるべき姿の検討
要求される精度(部品精度、組み付け精度)の限界
使用条件(適正使用範囲)
6.弱点研究
1.部品形状にマッチした設計(形状変更)
2.部品選択(材質・機能から変更)
3.機構、システムの検討
チョコ停(小停止)減少の改善の方法
チョコ停(小停止)を減少させるための改善方法には、以下のような手法があります
リアルタイムモニタリング:
- IoT技術を活用して設備の稼働状況をリアルタイムでモニタリングし、異常を早期に検知して対策を講じます。
又、現場を正しく観察するためにはビデオを利用し、小停止の現象を正しく観察し発生メカニズ ムを検討、その際、ワーク挙動(動き、姿勢、角度、浮き、振動)を良く観察する。
微欠陥の是正:
製品の接触面の関する各部品、治具の微欠陥を発見し、是正することである。 発見する方法としては外観形状的に微小なものを見つけ出す観察、分析の精度アップが必要である。
基本条件の徹底:
清掃、給油、増締めの十分に行う。
基本作業の徹底:
正しい操作、段取り、調整を行う。
最適条件の検討:
部品、ユニットの取り付け条件、加工条件の見直しとその最適化を検討
弱点研究:
設備、部品、治具、検出システム等の設計上の問題点を検討
工場の生産性向上に役立つ速度低下ロス対策
速度低下ロスの一般的な課題
1)設備の仕様があいまい :
設備の速度限界がわからないで稼動し不良、故障を発生
(2)仕様スピードに達成していない:
過去のトラブルで速度低下した状態のまま、稼動している
(3)速度アップに対する問題点が顕在化されてない 速度アップにより潜在していた問題を発見しその原因を追及する
(4)エアカットタイム、アイドルタイムの見方が甘い:
エアーカット・タイム→加工が完了しても空運転している時間
アイドル・タイム →ひとつの作業から次の作業に移行する際に生じる空き時間
*1秒以下まで測定できる測定器にて小さな空き時間をDATAとしてまとめ、問題点を顕在化する。
(5)動作、回転速度に対する見方があまい:
動作が遅い、動作がスムーズでないのにそのまま放置している。
(6)理論的なアプローチが弱い: 理論値から現在のスピード限界を求め、比較しさらに設計改善の参考とする。
速度低下改善の方法
TPM(Total Productive Maintenance)における速度低下の改善方法には、以下のような手法があります
(1)トラブルの真の原因を把握
実験的に速度をアップする。
①Cpの変化?
②従来にない不良項目は?
③刃具の寿命は?
④小停止の発生件数は?
⑤不良の発生比率は?
*悪化した要因を調査し対策を打つ。
(2)動作の有効性をチェクする
①エアーカットタイムの短縮
②アイドルタイムの短縮
③動作時間の短縮
④平行作業による時間短縮
*設備機構、部品構成、タイミング、サイクル線図もとに改善を行う。
TPM活動による不良ロス改善とその重要性を解説
TPM活動は、不良ロス改善に非常に有効な手法です。予防保全、自主保全、改善活動の継続という3つの側面から、不良ロスを減らし、生産性向上、品質向上、コスト削減を実現することができます。
慢性不良の一般的な課題
1)対策をしているが良化しない為、放置
①アプローチの仕方が間違っている
慢性不良の原因は数多くあり、そのつど原因が変化するのでその中の幾つかだけを対策しても 効果が少ない場合が多い、”理屈で考えてあやしいもの”について全て対策を打つことが必要で ある
②技術者の犯すミス 技術者は自分の専門領域でしか物事を考えないためにミスを起こしやすい
*技術者は現場を見る目(作業、調整、段取り、設備)を養い、変動要素がどこにあるかを見 抜く力が必要である
2)要因捉え方及び究明の仕方に問題がある
①慢性不良の要因のアプローチが間違っている 現象の見極め方、解析不十分のため、真の要因を見逃している
②要因究明の仕方が間違っている 欠陥を欠陥として取り上げず欠陥が現象に影響しないと判断ミスしている
慢性不良低減の方法
(1)変動要因の固定化
要因とは?:現象に論理的に影響を与えられると考えるもの
原因とは?:現象に直接、間接的に影響を与えたと証明されるもの
【要因の分類】
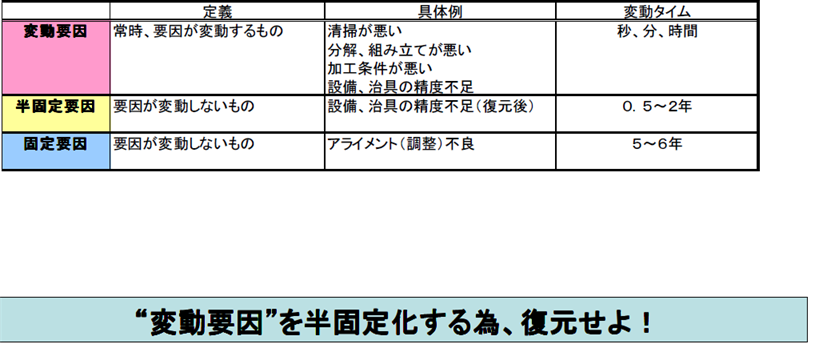
慢性不良低減の考え方
(2)比較研究
良品と不良品との違いがどこに、どのように、どの程度あり、それは何故かを十分に 追求し、有意差を定量的、定性的に研究することである。
①結果からの比較(製品比較) 製品面から形状、寸法、機能面での比較又は発生部位、時間的変動を比較検討
②プロセス比較 設備、治工具、金型についての比較研究で形状的、寸法的、表面粗さなどの違いを検討 特に数値化してないものは測定方法の研究が急務である
③部品交換による比較 組み立て品の場合、不良に関係すると考えられる部品を相互に交換し、結果を比較 研究するものである。また、設備の場合は部分的な交換による比較研究も考えられる
*ポイント
分析の精度アップ—-微妙な違いをどう発見するか?
・具体例:顕微鏡、ルーペ使用 、測定方法の研究
・具体例:表面粗さ計、ビジグラフ
不良低減の進め方
不良低減の進め方には、以下のような手法があります:
- 原因分析:
- 不良品の発生原因を特定するために、データを収集し、分析します。例えば、5Why分析や魚骨図(Ishikawa図)を使用して根本原因を追求します。
- 標準化:
- 作業手順やプロセスを標準化し、全員が同じ方法で作業を行うことで、ばらつきを減らし、不良品の発生を防ぎます。
- 教育と訓練:
- 作業者に対する教育と訓練を行い、品質管理の重要性を理解させるとともに、適切な作業手順を徹底させます。
- 設備のメンテナンス:
- 設備の定期的なメンテナンスを行い、故障やトラブルを未然に防ぐことで、不良品の発生を減少させます。
- 品質管理ツールの活用:
- SPC(統計的プロセス制御)やFMEA(故障モード影響解析)などの品質管理ツールを活用し、プロセスの安定性を確保します。
- 改善活動の推進:
- 継続的な改善活動(Kaizen)を推進し、現場の問題点を常に見直し、改善を行います。
これらの手法を組み合わせて実施することで、不良品の発生を効果的に減少させることができます。
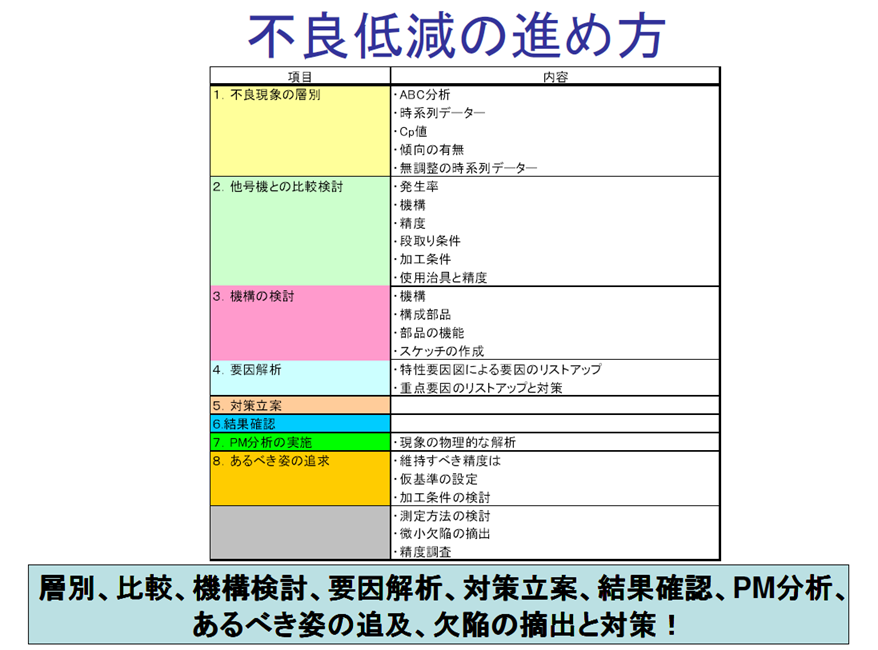
不良低減の進め方 層別、比較、機構検討、要因解析、対策立案、結果確認、PM分析、あるべき姿の追及、欠陥の摘出と対策!
ECRSの原則を活用した業務改善の方法
ECRSは、業務改善の4原則を指し、不要な業務を排除し、業務を効率化するための強力なツールです。
ECRSの4原則
ECRSは、以下の4つの原則から構成されています。
- Eliminate(排除): 不要な業務を徹底的に排除します。
- Combine(結合): 類似の業務をまとめ、効率化を図ります。
- Rearrange(再配置): 業務の順序や場所を改善し、流れをスムーズにします。
- Simplify(簡素化): 業務の手順をシンプルにし、複雑さを解消します。
ECRSを活用した業務改善の手順
- 現状分析:
- 業務の流れを可視化し、ボトルネックや無駄な工程を特定します。
- 各業務の目的や必要性を明確にします。
- ECRSの適用:
- Eliminate:
- 業務の目的を達成するために、本当に必要な業務かを見直します。
- 不要な書類作成、会議、報告などを洗い出します。
- 自動化できる業務がないか検討します。
- Combine:
- 類似の業務を統合し、一つの業務にまとめます。
- 複数の部署で行っている同じような作業を一つに集約します。
- Rearrange:
- 業務の順序を入れ替え、より効率的な流れを作ります。
- 作業者の動線を考慮し、無駄な移動を減らします。
- Simplify:
- 業務の手順を簡素化し、複雑な作業を分解します。
- 標準作業手順書を作成し、誰でも同じように作業できるようにします。
- Eliminate:
- 改善の実施:
- 分析結果に基づき、具体的な改善策を立案し、実施します。
- 小さな改善から始め、徐々に範囲を広げていきます。
- 効果検証:
- 改善後の効果を定量的に評価します。
- 改善前との比較を行い、改善効果を数値化します。
- 標準化:
- 改善効果が確認できた場合は、標準化し、定着させます。
- 標準作業手順書を更新し、全従業員に周知徹底します。
ECRS導入のメリット
- 生産性向上:
- 不要な業務の排除により、作業時間が短縮されます。
- 業務の流れがスムーズになり、生産性が向上します。
- コスト削減:
- 人件費、材料費、設備投資費などのコスト削減に繋がります。
- 品質向上:
- 標準作業手順書の作成により、品質の安定化が期待できます。
- ミスの発生率が減少します。
- 従業員のモチベーション向上:
- 改善活動への参加により、従業員の主体性や帰属意識が高まります。
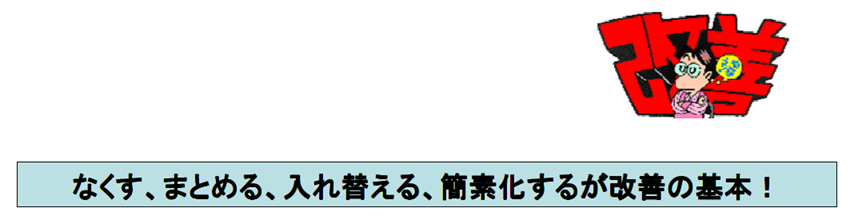
改善の原則
従来の改善とゼロにする為の改善
従来の改善とゼロにするための改善には、アプローチの違いがあります。以下にそれぞれの特徴を説明します:
従来の改善
従来の改善は、既存のプロセスやシステムを少しずつ改善していくアプローチです。以下のような特徴があります:
- 漸進的な改善:
- 小さな変更を積み重ねて、徐々に効率や品質を向上させます。
- 現状の維持:
- 現在のシステムやプロセスをベースに改善を行うため、大きな変革は伴いません。
- 低リスク:
- 小さな変更を行うため、リスクが低く、失敗しても影響が少ないです。
ゼロにするための改善
ゼロにするための改善は、根本的な問題解決を目指し、徹底的に不良やロスを排除するアプローチです。以下のような特徴があります:
- 根本原因の追求:
- 問題の根本原因を特定し、それを完全に排除することを目指します。
- 大きな変革:
- 現在のシステムやプロセスを大幅に変更することが多く、革新的なアプローチが求められます。
- 高リスク・高リターン:
- 大きな変革を伴うため、リスクも高いですが、成功すれば大きな成果が得られます。
具体的な手法
- 従来の改善:
- PDCAサイクル(Plan-Do-Check-Act)を活用し、継続的な改善を行います。
- 5S活動(整理、整頓、清掃、清潔、しつけ)を徹底し、作業環境を整えます。
- ゼロにするための改善:
- TPM(Total Productive Maintenance)を導入し、設備の総合的な効率を最大化します。
“ゼロ”にする考え方の適用—PM分析の適用
- TPM(Total Productive Maintenance)を導入し、設備の総合的な効率を最大化します。
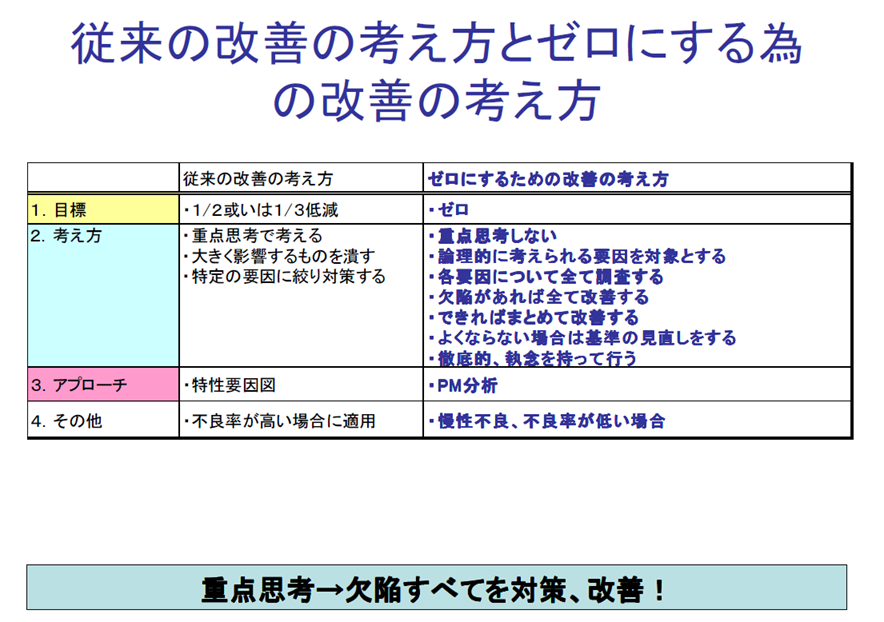
従来の改善の考え方とゼロにする為 の改善の考え方
まとめ
TPM(Total Productive Maintenance)において、個別改善は、設備の潜在能力を最大限に引き出し、生産性を向上させる上で極めて重要な要素です。
個別改善のテーマは、設備の故障、不良品の発生、作業の効率化など、多岐にわたります。
個別改善活動は、現場の状況に合わせて、柔軟に実施することが重要です。
個別改善活動を通じて、従業員のスキルアップやモチベーション向上にも繋がります。
関連キーワード:
OEE 5S なぜなぜ分析 TPM 予防保全 5S活動
無料での資料『TPMにおける生産効率化の個別改善』
Googleスライド 『TPMにおける生産効率化の個別改善』無料ダウンロード
Googleスライドから無料で『TPMにおける生産効率化の個別改善』の資料がダウンロードできます。
slideshare ダウンロード資料
パワーポイントで作成した資料です。
引用文献:
今日からモノ知りシリーズ トコトンやさしいTPMの本
現場力を高める実践的TPM入門【改訂版】
わかる!使える!TPM入門 〈基礎知識〉〈段取り〉〈実践活動〉/日本プラントメンテナンス協会
わかる!使える!TPM入門 〈基礎知識〉〈段取り〉〈実践活動〉/日本プラントメンテナンス協会
コメント