3分でわかる 自主保全とは? 自主保全の基礎知識
自主保全とは、一言で言うと、現場の従業員が自ら設備の管理を行い、その状態を良好に保つ活動のことです。
なぜ自主保全が重要なのか?
- 生産性の向上: 設備のトラブルを未然に防ぎ、生産の安定化に繋がります。
- 品質の向上: 設備の不良による製品不良を減らし、品質の安定化に繋がります。
- コスト削減: 設備の寿命を延ばし、修理費用を削減できます。
- 従業員のモチベーション向上: 自ら設備に関わることで、仕事への満足度が高まります。
- 安全な職場環境の構築: 設備の異常を早期に発見し、事故防止に繋がります。
自主保全の具体的な活動
- 日常点検: 毎日、設備の状態を点検し、異常があればすぐに対応します。
- 清掃: 設備を清潔に保ち、異常の早期発見を促します。
- 潤滑: 設備の動きをスムーズにするために、定期的に潤滑を行います。
- 部品交換: 摩耗した部品を交換し、設備の性能を維持します。
- 改善活動: 設備の改善案を出し、より良い状態を目指します。
自主保全の7つのステップ
自主保全は、以下の7つのステップで進められます。
- 初期清掃: 設備を徹底的に清掃し、現状を把握します。
- 発生源・困難個所対策: ゴミや汚れの発生源を特定し、対策を講じます。
- 基本点検: 設備の点検項目を明確にし、定期的に点検を行います。
- 異常発生時の対応: 異常が発生した場合の対応手順を明確にします。
- 自主保全の標準化: 自主保全活動を標準化し、全従業員に周知徹底します。
- 教育訓練: 自主保全に必要な知識やスキルを習得するための教育を行います。
- 自主管理: 従業員が主体的に自主保全活動に取り組み、改善を継続します。
自主保全のメリット
- 設備の寿命延長: 定期的な点検や清掃により、設備の寿命を延ばすことができます。
- 生産性の向上: 設備のトラブルを減らし、生産性を向上させることができます。
- 品質の安定化: 設備の不良による製品不良を減らし、品質の安定化に繋がります。
- コスト削減: 設備の修理費用を削減し、コスト削減に繋がります。
- 従業員のスキルアップ: 自主保全活動を通じて、従業員のスキルアップが図れます。
自主保全を成功させるポイント
- トップマネジメントのコミットメント: トップが自主保全の重要性を理解し、積極的に支援することが重要です。
- 全従業員の参加: 全員が自主保全活動に参加し、意見交換を行うことが重要です。
- 継続的な改善: 一度改善を行った後も、常に現状を見直し、改善を続けることが大切です。
- 小さな改善の積み重ね: 大きな改善だけでなく、小さな改善を積み重ねることも重要です。
自主保全は、TPM活動の根幹をなす重要な活動です。現場の従業員が主体的に設備に関わることで、企業全体の生産性向上に繋がります。
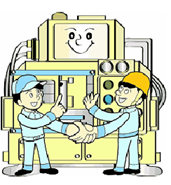
自主保全
自分の設備は自分で守る 〜 自主保全 のススメ〜
「自分の設備は自分で守る」という考え方は、TPM活動の基本理念の一つです。これは、作業者自身が設備の状態を常に把握し、日常的なメンテナンスや点検を行うことで、設備の故障を未然に防ぎ、生産効率を向上させることを目指しています。
日常点検
作業者が毎日設備の点検を行い、異常がないか確認します。これにより、早期に問題を発見し、対策を講じることができます。
清掃
- 定期的な清掃:設備や作業環境を定期的に清掃することで、異物の混入や故障を防ぎます。
- 清掃チェックリスト:清掃箇所や頻度を明確にしたチェックリストを作成し、計画的に清掃を実施します。
- 清掃教育:作業者に対して清掃の重要性を教育し、適切な清掃方法を指導します。
給油
- 適切な給油:設備の稼働状況に応じて、適切なタイミングで給油を行います。過剰な給油や不足は設備の故障を引き起こす可能性があります。
- 給油ポイントの確認:給油が必要な箇所を明確にし、定期的に確認します。
- 給油記録の管理:給油の履歴を記録し、適切な管理を行います。
増締め
- 定期的な増締め:設備の振動や使用によって緩んだボルトやナットを定期的に増締めすることで、設備の安定性を保ちます。
- 増締めトルクの管理:適切なトルクで増締めを行うために、トルクレンチを使用し、過剰な締め付けや不足を防ぎます。
- 増締め箇所の確認:増締めが必要な箇所をリスト化し、計画的に実施します。
教育と訓練
作業者に対する教育と訓練を行い、設備の操作方法やメンテナンスの重要性を理解させます。
記録と分析
点検やメンテナンスの記録を残し、データを分析することで、設備の状態を常に把握し、改善点を見つけ出します。
これらの取り組みを通じて、作業者自身が設備の管理に積極的に関与し、設備の故障を未然に防ぐことができます。
わかりやすい自主保全の7ステップ
自主保全の7ステップは、設備の効率的な運用と長寿命化を目指すための段階的なアプローチです。
自主保全は7つのステップですがその基本構成は3つのエリアに分けられます。
【第1エリア】劣化を防ぐ活動
第1~第3までのステップで、設備の清掃・点検を中心とする活動を通じて、設備の基本条件を徹底的に整備し、その維持体制をつくりあげる段階です。
“手を汚し・工夫し・苦労する”を徹底する重要なステップで、なかでも基本条件の整備である清掃・給油・増締めの3要素は、劣化を防ぐための最低必要条件であり、すべての活動のベースとなるものです。
【第2エリア】劣化を測る活動
第4~第5までのステップで、設備総点検技能教育と点検の実施により、劣化を防ぐ活動から劣化を測る活動へと発展させ、五感から理屈に裏付けられた日常点検ができる『設備に強いオペレーター』を目指す段階です。
成果が出て人が変わり、不良・故障は現場の恥であるという雰囲気がつくり出され、真の自主管理体制づくりに踏み出す重要なステップとなります。
【第3エリア】標準化と自主管理の活動
第6~第7ステップは、標準化と自主管理の仕上げの段階です。オペレーター自身が必要な保全技能の完成を図ることで、オペレーターと現場が大きく変わり、自主管理の職場となります。
以下に、各ステップの具体的な内容を説明します。
初期清掃:
-
- 設備の徹底的な清掃を行い、異常箇所を発見します。これにより、設備の基本的な状態を把握し、改善の基礎を築きます。
- 治工具、設備に付着したゴミ、汚れを除去することにより 設備の潜在欠陥を顕微化させ発見する。
発生源・困難箇所対策:
-
- ゴミや汚れの発生源を特定し、対策を講じます。また、清掃や点検が困難な箇所を改善します。
- ゴミ汚れの発生源を断ち、飛散防止、清掃・給油の困難箇所を改善し与えられた 目標時間内で清掃・給油ができるように する。
自主保全基準の作成:
-
- 清掃、給油、増締め、点検の基準を作成し、日常的に実施できるようにします
- 第1ステップで汚れを清掃したレベル及び第2ステップ で対策した設備状態を維持継続するために清掃仮基準 の作成と給油仮基準を作成する。
- 不具合・給油困難箇所の復元と改善
- 清掃・給油・点検仮基準の作成
- 清掃基準と給油基準を併せ清掃・給油・点検の効率を考慮して仮基準の作成を作成する。
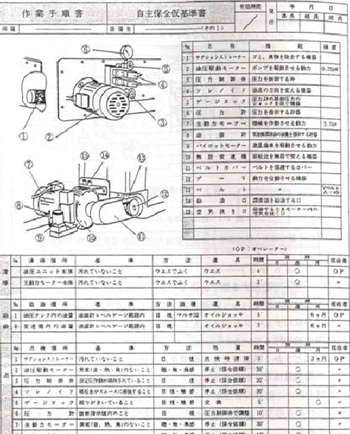
TPM 自主保全仮基準の作成
総点検:
-
- 設備の総点検を行い、微細な欠陥を発見し、修正します。これにより、設備の信頼性を向上させます。
- 五感による感覚的な不具合の検出から担当設備の機構・機 能を理解し、設備に関する知識を身につけ、論理に裏づけ された日常点検を行い、自主保全能力を高めていく。
- 総点検進め方:①設備の基礎教育を受ける(リーダークラス)設備構造、調整、正しい操作方法、ポイントを学びインスト ラクターを育成。②オペレーターに教える メンバーに伝達教育し、理解度を評価。
③学んだことを実践し不具合を発見する
④目で見る管理を推進する。
自主保全:
-
- 作業者が自主的に点検を行い、設備の状態を常に把握します。これにより、早期に異常を発見し、対策を講じることができます。
- いままで作成した清掃基準、給油基準、総点検基準、設備品質点検基準を見直し、点検の効率化、点検ミスのない状態に作り上げる。
- 設備保全 自主保全・・・設備本体、設備品質の管理項目を明確にして点検を行い、故障ゼロ、不良ゼロを目指す活動の総仕上げをする。
標準化:
-
- 各種の現場管理項目を標準化し、維持管理の完全システム化を推進します。
- 設備維持管理を確実にしてオペレーターの役割を 広め、徹底したロスの低減を図る
- 管理対象の明確化:・現場物流管理 ・標準作業基準 ・データー標準化 ・治工具、測定器管理基準 ・補修部品 管理基準 ・工程品質保証基準
- オペレーター自身の作業を観察しムリ、ムダ、 ムラを排除し改善と標準化を進める
自主管理の徹底:
-
- 会社方針や目標の展開と改善定着化により、無駄の排除・コストダウンを推進し、保全記録の確実実施と解析による設備改善を進めます。
- 活動の全てを集約し、設備を変え、人を変え、職場を変えて成果を出した実績に自信を持ちさらにチャレンジを続ける
- 活動の進め方:
①崩壊しないマネンジネント領域の整備②オペレーター自身の主体的行動力の養成
・リーダーのOJT教育
・テーマーを与える
これらのステップを順に実施することで、設備の効率的な運用と長寿命化が実現します。
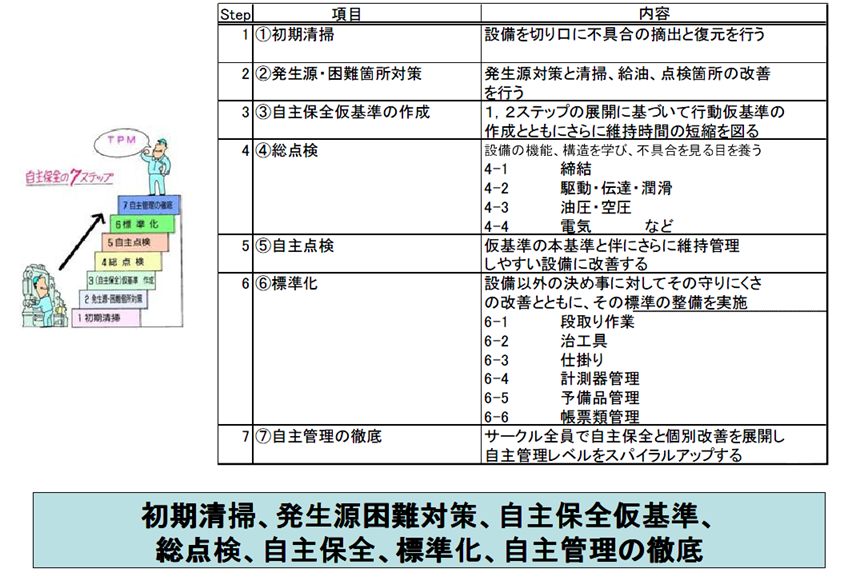
自主保全の7ステップ
自主保全 三種の神器
自主保全を円滑に推進していくためには、サークル活動の活性化が必要です、そのためには、やる気・やる腕・やる場の3つの条件を整えることが重要でこの3つの条件を整えるためのツールの代表的なものが、「ワンポイントレッスン」「活動板」「ミーティング」で、これらをまとめて『自主保全 三種の神器』と呼んでいます。
ワンポイントレッスン
自主保全のワンポイントレッスンは、短時間で効果的に学べる教育ツールです。通常、5分程度で重要なポイントを教えることを目的としています。これにより、作業者が日常的な保全活動を効率的に行えるようになります。
ワンポイントレッスンの目的
- 基礎知識の習得:
- 日常の生産活動やTPM(Total Productive Maintenance)を展開する上で必要な基礎知識を学びます。
- トラブル事例の共有:
- 実際に発生した不良や故障の事例をもとに、再発防止の観点から日常的に何をすべきかを学びます。
- 改善事例の共有:
- 現場での改善活動から生まれた事例を共有し、改善の考え方や対策、効果について学びます。
ワンポイントレッスンの実施方法
- 簡潔な資料作成:
- 学んだ内容を1件1枚にまとめ、ポイントを絞って作成します。
- 短時間の教育:
- 5〜10分程度の短い時間でメンバーに教育を行います。
- 伝達教育:
- 教育を受けた人が講師となり、他のメンバーにその知識を伝えることで、理解を深めます。
ワンポイントレッスンを活用することで、作業者全員のレベルアップが図れます。
関連用語:ワンポイントレッスン
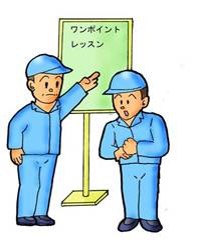
TPM活動板
TPM活動板は、TPM活動の進捗や目標、課題を「見える化」するためのツールです。これにより、チーム全体が現在の状況や今後の計画を共有しやすくなります。以下に、TPM活動板の具体的な内容を紹介します:
- 目標と目的:
- TPM活動の目標や目的を明確に掲示します。これにより、全員が共通の目標に向かって取り組むことができます。
- 進捗状況:
- 各活動の進捗状況を視覚的に表示します。例えば、ガントチャートや進捗バーを使用して、現在の進行度を示します。
- 課題と対策:
- 現在直面している課題や問題点を掲示し、それに対する対策やアクションプランを明示します。
- 成果と評価:
- 達成した成果や改善点を掲示し、評価を行います。これにより、成功事例を共有し、モチベーションを高めます。
TPM活動 ミーティング
TPM活動におけるミーティングは、チーム全体のコミュニケーションを円滑にし、活動の進捗や課題を共有するために重要です。
- 定期的な開催:
- TPMミーティングは定期的に開催し、活動の進捗状況や課題を共有します。週次や月次での開催が一般的です。
- アジェンダの設定:
- ミーティングのアジェンダを事前に設定し、参加者に共有します。これにより、効率的な議論が可能になります。
- 進捗報告:
- 各チームや担当者が活動の進捗状況を報告します。成功事例や課題を共有し、全員が現状を把握できるようにします。
- 課題の共有と対策の検討:
- 現在直面している課題を共有し、対策を検討します。全員で意見を出し合い、最適な解決策を見つけます。
- 次回の計画:
- 次回のミーティングまでに行うべき活動や目標を設定します。具体的なアクションプランを立て、責任者を明確にします。
- フィードバックの収集:
- ミーティングの最後に、参加者からフィードバックを収集し、次回のミーティングに反映させます。
これらの手法を取り入れることで、TPMミーティングが効果的に進行し、活動の成果を最大化することができます。
TPM活動の「エフ」(絵符)とは
TPM活動における「エフ」(絵符)は、設備や作業の不具合を視覚的に管理するためのツールです。エフは、どこにどのような不具合があるかを明確に示し、対策を講じるために使用されます。
エフの具体的な使用方法
- 不具合の発見:
- 設備や作業中に不具合を発見した場合、その場所にエフを付けます。エフには、日付や発見者の名前、不具合の内容を記入します。
- 不具合の見える化:
- エフを付けることで、不具合の場所や内容が一目でわかるようになります。これにより、迅速な対応が可能になります。
- エフの種類:
- エフには、白エフと赤エフの2種類があります。白エフは自分たちで処理できる不具合に使用し、赤エフは専門の保全部門に依頼する不具合に使用します。
- エフの取り外し:
- 不具合が解消されたら、エフを取り外します。これにより、問題が解決されたことを確認できます。
エフは、不具合の見える化と教育のツールとして非常に有効です。
*設備不具合箇所には不具合内容を示す 札を取り付けどんな不具合を誰が何時発見したかわ かるようにする。
まとめ
TPM(Total Productive Maintenance)において、個別改善は、設備の潜在能力を最大限に引き出し、生産性を向上させる上で極めて重要な要素です。
個別改善のテーマは、設備の故障、不良品の発生、作業の効率化など、多岐にわたります。
個別改善活動は、現場の状況に合わせて、柔軟に実施することが重要です。
個別改善活動を通じて、従業員のスキルアップやモチベーション向上にも繋がります。
関連キーワード:
OEE 5S なぜなぜ分析 TPM 予防保全 5S活動
無料ダウンロード 資料『TPMの自主保全とは?』
Googleスライド 『TPMの自主保全とは?』無料ダウンロード
Googleスライドから無料で『TPMにおける生産効率化の個別改善』の資料がダウンロードできます。
slideshare ダウンロード資料(PDF)
パワーポイントで作成した資料です。
引用文献:
今日からモノ知りシリーズ トコトンやさしいTPMの本
現場力を高める実践的TPM入門【改訂版】
わかる!使える!TPM入門 〈基礎知識〉〈段取り〉〈実践活動〉/日本プラントメンテナンス協会
わかる!使える!TPM入門 〈基礎知識〉〈段取り〉〈実践活動〉/日本プラントメンテナンス協会
コメント