生産効率を高めるために必要なステップと注意点
生産の効率化とは,生産を行うのに必要な投入量(インプット–材料・人・設備・エネルギーなど)を最少にして,最大の産出量(アウトプット)を得ることであり,付加価値をいかに上げ,製造原価をいかに低減させるかである。
そのためには,次の活動が必要となろう。
量的な拡大を図る活動 | 単位時間当たりの出来高 | 人の効率
①設備の効率化を高める活動:
設備の効率をいかに高めるか,また,単位時間当たりの出来高をいかに高めるか。
②人の効率を高める活動:
設備の安定化の推進により,1人当たりの持ち台数をいかに増加させるか, また作業改善・自動化の推進により省人化をいかに高めるか
③管理効率を高める活動:
生産が円滑にできるための計画の立て方,または部品欠品を発生させないための部品調達をどうするか,また物流ロスをいかに最少にするか
質的な拡大を図る活動 |品質の向上 | 無人化運転
①品質の向上を高める活動:
不良・手直しをいかに減少させるか,また品質のバラツキをいかに少なくするか,品質のレベルをいかに上げるかの活動を通じて,出来高増と品質のレベルアップを図る
②無人化を推進する活動:
無人運転をするための条件を追求し,それを具現化して無人化の推進を行い,出来高増を図る。
量的拡大を図る活動は,設備の不稼動時間をいかに減少させるか,また単位時間当たりの出来高増をいかに図るかであり,さらに工数面の改善を図ること、による,1人当たりの出来高生産性の向上を図るものである。
質的な拡大を図る活動は,品質改善による不良品の減少と品質のレベルアップを図るものであり、また無人化のための必要条件,十分条件は何かを検討することにより,技術面でのレベルを高めるとともに,生産性の向上を図る活動である。
生産効率化の最終的なねらいは,設備の固有能力を十分に発揮,維持しているかどうか,そのために人の能力を最高に発揮,維持することが必要であり,マンーマシン・システムの最高状態,極限状態を維持することである。
また,その結果として,付加価値生産性の増大,製造原価の低減などを操業度に影響なく,それぞれ達成することである。生産が増加している場合は,生産量を増加する対策を行うことと,より原価低減を図り,生産が減産する場合は,減産しても原価高にならないように,人員減少,副資材の原単位コストを削減し,全体の加工費を低減する活動を行う必要がある。
TPM活動で効率化を阻害する16大ロス
生産効率化を阻害するロスとして,次の16大ロスがある(図2・1参照)。
設備効率を阻害する7大ロス
①故障ロス
②段取り・調整ロス
③刃具ロス
④立上がりロス
⑤チョコ停・空転ロス
⑥速度低下ロス
⑦不良・手直しロス
設備操業度を阻害するロス
⑧SD(シャットダウン)ロス
人の効率化を阻害する5大ロス
⑨管理ロス
⑩動作ロス
⑪編成ロス
⑫自動化置換ロス
⑬測定調整ロス
原単位の効率化を阻害する3大ロス
⑭歩留りロス
⑮エネルギーロス
⑯型・治工具ロス
以下,それぞれのロスについて解説していく。
図2・1 生産活動におけるロス構造(16大ロス)
設備効率を阻害する8大ロス
故障ロス
突発的・慢性的に発生している故障によるロスで,時間的なロス(出来高減),物量ロス(不良発生)を伴うものである。
故障に関する一般的な問題は,“故障”の定義が不明確なことである。そのため, TPM活動当初は故障件数が増加する傾向が見受けられるが,それは故障件数が増加するのではなく,定義がはっきりしておらず,いままで故障としてカウントしなかったものを含めたためである。
そこで,故障の定義を以下のよう定める。
●機能の停止あるいは低下を伴うもの(当然,生産停止あるいは生産量減を伴う)
●機能の回復に部品交換ヽ修理を伴うもの
●修理に要する時間が5~10分以上のもの
突発的なものは,わりに目につきやすく,またそれなりに対策が打ちやすいが,頻繁に起きる慢性的なものは,いろいろ対策を打ってもなかなか直らないために放置されるケースが多い。また,ロス,の中で一番大きなウエイトを占めるため,どこの工場でも重点的に行っているが,なかなか達成できないのが実状のようである。
故障ロスに対しては,設備の信頼度をいかに高めるかの研究と,故障が発生してから回復するまでの時間を,いかに最小にするかの保全性の研究が必要である。いずれにしても故障の発生を”ゼロ”にすることである,そして,それは投資をあまりしないでも(一時的にはする)達成は可能である。そのためには,まず従来のBM (Breakdown Maintenance)の誤った認識–故障の発生はやむを得ないもので,発生するものという考え方—~を改める必要がある。
段取り・調整ロス
段取り・調整ロスとは,現製品の生産終了時点から次の製品の切替え・調整を行い,完全な良品ができるまでの時間的なロスをいう。 ここで段取替えとは,生産終了時の治工具類の取外し,後片づけ,掃除,次の製品に必要な治工具類・金具類の準備→取付け→調整→試加工→調整→測定→生産と一連の作業を行い,完全な良品ができるまでの時間である。
最近は各社でも段取替えの研究が進んでいるが(シングル段取り),一般的にはまだ解決すべき課題が多く残されている。IE的アブローチによる内段取りとタト段取りの区分,外段取り,内段取りの時間短縮の研究により,時間短縮の傾向は各社にかなり見受けられるが,調整の問題がいぜんとして残されている。
調整とは,以下のことをいう。
●ある目的に向かって最適解・最適値を追求するために行う処置で,たとえば,品質をねらい値に収めるための処置,その他のトラブルを防止するための処置など
●試行錯誤の繰返しにより達成するもの
調整はまったく扱いにくい問題であり,一般的には突込みが不足しており,食わず嫌いの傾向があるが,避けられるものと避けらないものとに区分することが先決である。
避けられないものには剛性不足によるもの,機構的なものがあり,避けられるものには誤差の累積によるもの(精度不足に起因する),標準化不備によるものがある。
アプローチとしては,まず調整のメカニズムを検討し,時間短縮を図ることが課題である,
そしてその目標は”極小化”にある。
また,段取り・調整ロスの最終的な課題は“一発良品段取り”の実現にある。最近では調整をゼロにすることにより,”一発良品段取り”がかなり普及するようになってきた。 一発良品段取りとは,治具交換後に試し加工をせずに,最初から良品を作り出す方法である。従来は,治具交換後に試し加工し,寸法測定しながら調整して所期の寸法に追い込むという方法で,試し加工に3~4個のワークを使用しているのが普通である。
一発良品段取りを実現するためには,調整をゼロにすることが必須の条件である。段取替えの時間短縮には,さまざまな検討が行われているが,調整や試し加工をゼロにする考え方,アプローチは一部の会社でしか行われていない。
刃具ロス
刃具ロスとは,刃具の定期的交換,切損による一時的な交換に伴う時間的なロスと,交換の前後に発生する物量ロス(不良・手直し)である。
たとえば,チップの交換・砥石の交換・交換後のワーク計測時間,またチップ破損の場合に発生する手直し品とその手直し時間,廃品不良あるいは交換後の品質が安定するまでの時間などである。
刃具ロスは,刃具の寿命延長のための材質・形状変更などの研究により少なくなりつつあるが,まだまだ研究を要する課題である。 刃具に一定の交換基準(定数管理)が設定されているが,定数まで使用しないうちに折損・チッピングを起こして不良を発生させ,やむを得ず交換したり,またそれを防止するために定数を短くして使用している場合が多い。
定数の設定にしても,設備的精度,刃物ホルダーの精度などに十分気をつけていないために,それを修正さえすれば定数が延びるのに,短く設定している場合など,その決め方に問題がある。 いずれにしても,刃具寿命については一部の生産技術者・刃物専門家が定数刀設定を行うが,実際にはそれが守れる基準でないために,現場まかせになっているのが一般的である。
刃具ロスは他のロス(故障・不良手直し・段取り・その他)に比較して,口スとして顕在化されにくい面があった。それは刃具そのもののコストが,わりに安価であるためと,他の不良ロスの方が多いために,刃具ロスに対する認識があまかったからだと考える。
しかし,故障・段取り・不良などのロスが減少した段階では,刃具ロスが設備総合効率を阻害する一番大きな要因であると考えている。とくにトランスファーマシンなどは,設備台数が多いわりに人員が少ないために,刃具に伴う口スが総合効率の阻害要因として10~12%に相当する場合もある。
刃具ロスをとくに重要視するのは,以下のためである。
●夜間無人運転の実施のため
●設備総合効率の向上のため
●刃具費の低減のため
機械工場で夜間無人化を阻害している要因として,刃具の寿命が短く一直分(夜間)もたないことがあるが(その他チョコ停・自動計測などの問題もあるが),刃具寿命の延長は夜間無人運転を実施するための必須の条件である。
刃具ロスを減少するためには,固有技術の領域の面(材質変更・形状変更その他)からとソフト面(振動測定と最適切削条件の追求)からの検討が必要である。また,目標は刃具寿命の”極大化”にある。
立上がりロス
立上がりロスの定義は,以下のとおりである。
●定修後のスタートアップ時
●休止後(長時間停止)のスタートアップ時
●休日後のスタートアップ時
●昼休み後のスタートアップ時
などに,規定のサイクルタイムで運転しても,機械的なトラブル(チョコ停・小トラブル・刃具破損など)がなく,品質が安定し良品を生産できるまでの時間的ロスと,その間に発生する物量ロス(不良・手直し)である。
機械工場では,朝の生産立上がり時に寸法バラツキが発生するために,調整頻度が多,い,調整に失敗し手直しが発生する,刃具を破損するなどのロスがあり,これを防止するために朝早くからウォーミングアップを行いながら空運転を行っている。
これを月曜病といい,寒冷地や高精度の製品を作る設備に多く見受けられる現象であり,朝の立上がり時に0.5~1.0時間も要する場合がある。 これはある程度やむを得ない面もあるが,”どうにもならない””この設備では避けられない”などの理由で,放置されているのが現状である。
これらのロスが発生する基本的な原因は,機械的な膨張・収縮による熱変位である,熱変位がどの部位に発生するのか,それは十方向なのか,一方向なのか,ワークに対する影響度はどうなのか,また時間経過(空運転の時間)とともにそれがどのように変化するのか,平衡状態になるのは何分後なのか,などが検討されていない。
立上がりロスを減少させるには,熱変位の発生部位とその時間的な変化,ワークの寸法変動に時間的変化を調査することから始める必要がある。熱変位については,改善できるものと現状の技術レベルでは解決できないものがあるが,改善できるものはできるだけ改善し,空運転に伴うエネルギーロス,出来高減ロスを減少すべきである。そして目標ぱ極小化”にある。
チョコ停・空転ロス
チョコ停・空転ロスの定義は,以下のとおりである。
●一時的な機能の停止を伴うもの
●機能の回復は簡単な処置(異常なワークの除去とリセット)でできるもの
●部品交換,修理は伴わないもの
●回復時間は2~3秒から5分未満のもの
このように故障とは異なり,一時的なトラブルのために設備が停止,または空転している状態をいう。 たとえば,ワークがシュート上で詰まって空転したり,品質不良のためにセンサーが作動して一時的に停止する場合である。これらは,ワークの除去,リセットさえすれば機械は正常に作動するものであり,設備の故障とは性格的に異なる。
しかし一般には,この小さなトラブルにより設備の効率化が非常に阻害される場合が多く,とくに自動機,自動組立機,搬送設備に多くみられる現象である。 一般に,チョコ停(空転)は処置が簡単なために見逃される傾向がある。
また,顕在化しにくい面が多く,顕在化していても定量化が困難なため,効率化にどの程度妨げになっているか,はっきりしない場合が多い。チョコ停を減少させるためには,現象をよく分析することと,微欠陥を徹底的に排除することが重要であり,その目標ぱゼロ”である。無人運転を実施するうえで,”チョコ停ゼロ”は必須の条件である。
速度低下ロス
速度低下ロスとは,設備のスピードが遅いために発生するロスで,以下のように定義する。
●設計時点のスピード(あるいは品種ごとの基準スピード)
に対する,実際のスピードの差によるロス
●設計時点のスピードが,現状の技術水準またはあるべき姿に比べて低い場合のロス
前者の例として,1サイクルの時間が60秒で基準設定しているが,実際には65秒で稼動している場合,5秒が速度ロスとなる。後者の例として,1サイクjレ時間が60秒で設定されているが,現状のレベルで改善すれば50秒まで下げられる場合,10秒が速度ロスとなる。
設計スピードで稼動した場合,品質的トラブル,メカ的トラブルの発生のためにスピードダウンせざるを得ない場合もある。また,過去にトラブルが発生にしたとか,設備の寿命が短くなるとかの理由で,スピードが出せるのに出していない場合もある。
また,設備の仕様スピードがわからないままに稼動してぃる場合もある。 一般的には,これらの速度低下ロスを明確にしないままで稼動するケースが多い。しかし,この速度低下ロスは7大ロスの中でも,もっとも効率に寄与する割合が高いので,十分に検討する必要がある。
スピードアップを図ることが,問題の顕在化,技術レペルアップに寄与するものであり,その目標は,設計スピードと実際スピードの差を”ゼロ”にもっていくことにある。
不良・手直しロス
不良・手直しロスの定義は以下のとおりとする。すなわち,不良・手直しによる物量的ロス(廃棄不良)と,修正して良品とするための時間的ロスである。 一般的に,突発不良は対策が立てやすく,放置されることはまずないが,慢性不良はなかなか原因がわからず,対策を講じてはみるが良い結果が得られず,放置される場合が多い。また,手直し品も修理品も修正工数が必要であるため,慢性不良と考えるべきである。
慢性不良を低減するには,慢性故障と同様に,従来と同じような対策を実施してもなかなか解決が困難であり,発想の転換が必要である。不良現象を基本的に見直し,その発生メカニズムを再検討し,不良ぱゼロ”を達成することを目標に,管理ポイントを再検討する必要がある。
SD(シャットダウン:Shutdown)ロス・・設備操業度を阻害するロス
SDロスの定義は,設備の計画的な保全を行うために設備を停止する時間的なロスと,その立上がりのために発生する物量ロスである、このSDロスは,設備の特性上やむを得ないものであり,品質上・安全上・信頼性の維持の面から,設備による時間の長短はあるが発生するものである。シャットダウン時に行われる作業は,清掃・点検・部品交換・オーバーホール・精度チェックなどを伴うものである。
たとえば,半導体工場の真空設備では,高真空下(10-7程度)でガスを注入し,物理的・化学的な反応を行うために設備内部が汚れるので,定期的なクリーニングや部品交換をする必要がある。また,真空ポンプ(ロータリー,拡散ポンプ)などの定期的な整備(オイル交換,フィルターや部品交換など)を行っている。これらの作業は,品質や設備の信頼|生を維持するうえで,欠くことのできないものである。
しかし,このシャットダウンに伴う作業は設備操業度に大きく影響するものであり,これをロスとしてとらえ,1回当たりの作業時間短縮,周期の延長を図ることが必要である。シャットダウンに関して,一般的な問題点として,以下のようなものがある。
① 過去の延長で作業が行われている
●部分的に余計な作業を行っている
●部品寿命がまだあるのに交換している
●作業の方法,基準が十分整備されていない
②作業全体のクリティカルパス(全体の時間を規制する作業)がはっきり していない
③周期の設定に論理的な裏付けがない
④周期延長の改善活動が不十分である
⑤時間短縮の研究がなされていない
これらの問題点を1つずつ解決することが,シャットダウン時間の短縮,周期の延長につながるのである。
人の効率化を阻害する5大ロス
人の効率化を阻害している5大ロスを総称して工数ロスともいう。工数ロスとは配置されている作業者の動作,作業方法,レイアウトなどのまずさに起因して発生する時間的ロスと,本来の作業以外に行っている作業(非定常作業)の時間的ロスである。
工数ロスは動作そのものにムダがある,物の置き方が悪いためにムダな動作が発生している,レイアウトがまずいために歩行が多いなどの定常作業の中でのロスと,刃具が定数になる前にチッピングを起こすため,その処理に追われるなどのの非定常作業のために発生するロスがある。
従来からからIE手法などの研究で工数ロス低減の試みは活発に行われ,原価低減に大きな貢献をしてきたが,まだ改善の余地が数多く残されている。また工数が低減されたといっても,設備上のチョコ停・調整などのトラブルが多発すると、稼動率の低下を招くために余分な人員配置をしたり,また作業動作をみても、 まだムダな動作が多い。
工数ロスを低減するには,トラブルの発生による非定常作業を減少することが先決であり,それから定常作業について作業のやり方,レイアウトの変更,動作の改善を行うべきである。以下に,人の効率化を阻害する5つのロスについて述べる。
管理ロス
管理ロスとは,材料待ち,指示待ち,故障修理待ちなどの管理上発生する手待ちロスをいう。
動作ロス
動作ロスとは,動作経済の原則に反する動作ロス,スキルの差によって発生するロス,レイアウトのまずさに起因する歩行ロスなどである。
編成ロス
編成ロスとは,多工程持ち・多台持ちにおける手待ちロス,コンペヤ作業のラインバランス・ロスなどである。
自動化置換ロス
自動化置換ロスとは,自動化に置き換えることにより省人化できるのに,それを行わないために生じる人的ロスである。
たとえば,部品のローディング・アンローディングの自動化を行うことにより,省人化が図れるのにやらない場合などである。また,部品や製品の供給・払出し・運搬などの物流に関わる自動化を行わないために生じる物流ロスも,自動化置換ロスの範疇に入る。
測定調整ロス
測定調整ロスとは,品質不良の発生・流出防止のため,測定・調整を頻繁に実施するために生じるロスエ数である。
原単位の効率化を阻害する3大ロス
歩留りロス
歩留りロスとは,素材重量と製品重量の差,または素材投入総重量と製品重量の差による物量ロスである。
前者は,鋳物素材の鋳造欠陥(砂かみ,表面欠陥)の発生を防止したり,造型作業の型の精度不良をカバーするために,必要以上に肉厚を厚くする場合の材料ロスで,そのため機械切削時間が多くかかったり,刃具寿命を短くしている場合もある。
後者は,湯口重量・バリ発生量と製品重量との差であり,造型の型合わせ精度不良によりバリの発生量が多くなり,歩留りを悪化させている材料ロスである。
アルミ鋳造ではランナーの重量とバリの重量が該当する。 たとえば,自動車エンジンのシリンダーブロックの工程では,砂型の部分的な弱さと,砂型・中子型の型合わせ不良(ズレ)によるバリが発生し,バリ取りにかなりの人員を要している場合が多い。このバリをいかに減少させるか,歩留まり,エネルギー,工数ロスの面から大きな課題である。
エネルギーロス
エネルギーロスとは,電力,燃料,蒸気,エア,水(排水処理を含む)などのエネルギーのロスである。
電力,燃料,ユーティリティ費用は,原価の中で占める割合も高いため,各社削減に努力している。エネルギーロスのうち,大きなものは改善されているが,細かなロスはまだ数多く残されており改善の余地がある。たとえば油圧装置の場合,
●圧力設定はどうか
●保持時間はどうか
●油圧ポンプの形式はどうか(可変容量型か)
●油圧回路は適切か
などを検討すれば,種々の問題が摘出されるはずであり,これらを1つずつ改善する必要がある。細かなエネルギーロスを数多く発掘し,改善することが大きな成果になる。
型・治工具ロス(副資材ロスを含む)
型・治工具ロスとは,製品を作るために必要な型・治工具ロスの製作・補修に伴って発生する,金銭的ロスである。 企型の新規製作,寿命による更新,摩耗に対する補修,破損による更新,金型部品の製作・補修,治工具の製作・補修に伴って発生する費用である。補修回数が多ければ,当然費用は高くなる。
また生産に必要な副資材ロスとして,切削油,消耗交換部品,その他薬品・ガスなどの費用も型・治工具ロスに含める。この型・治工具ロスは,原単位に換算して管理する必要がある。一般的な問題点として,これらのロスかどの程度発生しているのかが顕在化されていないことにある。製造原価を低減するためには,金型補修のMTBFをいかに延長するか,破損をいかに防止するか,交換部品の寿命をいかに延長するかが課題である。
TPM 設備ロスを明らかにするための7つの項目
TPM 7大ロスの定義と設備総合効率との関係
前述したロスを時間的側面から検討すると,図2・2のように表される。ここで,時間と効率化に関する指標の定義づけをしておく。
操業時間
操業時間とは,1日または月間を通じて設備が稼動しうる時間である。
負荷時間
負荷時間とは,1日または月間を通じて設備が稼動しなくてはならない時間である。すなわち,生産計画上の休止時間,保全のための休止時間,日常管理上に必要な朝礼,その他の休止時間などを操業可能な時間から差し引いた時間である。
稼動時間
稼動時間とは,負荷時間から故障,段取り,刃具交換,その他の停止時間を差し引いたもので,実際に設備が稼動した時間である。
正味稼動時間
正味稼動時間とは,稼動時間に対し,一定スピードで正味稼動した時間チョコ停による停止,スピード低下によるロスを差し引いたものである。
価値稼動時間
価値稼動時間とは,正味稼動時間から不良品,手直し品に相当する時間を差し引いた時間である。実際に製品(良品)を作り出した時間である。
時間稼動率
時間稼動率は,負荷時間に対し,設備の停止を除外した正味時間の時間的比率を算出したものである。
性能稼動率
性能稼動率は,速度稼動率と正味稼動率から成り立っている。速度稼動率はスピード差を意味し,設備の固有能力,設計能力に対し,実際に稼動している
スピードの比率である。これは,スピード差を浮彫りにするものである。本来は設計スピードを用いるが,品質によりスピードを変える必要がある場合(設計時点で考慮できなかった要素により,所期のスピードを出した場合,品質・設備トラブルを起こし,スピードを変えざるを得ない)は,品種ごとの基準スピードを用いる、したがって,設備のおかれている状態により,次のいずれかによって算出する。
●設計仕様に決められたサイクルタイム
●現在の理想状態で考えられるサイクルタイム(品種別サイクルタイム)
●現在までの最高のサイクルタイム,類似設備から判断される目標としてのサイクルタイム
正味稼動率は,一定スピードの持続性を意味するもので,単位時間内において一定スピードで稼動しているかどうかを浮彫りにするものである。
設計,基準スピードに対して早い・遅いではなく,たとえスピードを落として稼動する場合でも,そのスピードで長時間安定稼動しているかどうかであり,チョコ停によるロス,日報上に現れない小トラブル・調整ロスを算出するものである。
総合効率
総合効率は,時間稼動率,性能稼動率,良品率の相乗積であり,それは現状設備が時間的・速度的にどうか,良品率はどうかを総合化して,付加価値を生み出す時間にどれだけ貢献しているかを示す尺度である。
1.時間稼動率=(負荷時間-停止時間)/負荷時間
2.性能稼働率=(出来高×実際サイクルタイム)/(負荷時間-停止時間)×(基準サイクルタイム/実際サイクルタイム)
3.良品率=良品数/投入数量
良品数=投入数量-(立上がり不良数量十工程不良数十手直し数)
4.設備総合効率=時間稼動率×性能稼動率×良品率
総合効率算出事例
1日の操業時間 60分×8時間=480分
1日の負荷時間 460分
1日の稼動時間 400分
1日の出来高 400個
時間稼動率=400/460×100=87%
基準サイクルクイム 0.5分/個
実際サイクルクイム 0.8分/個
【停止内訳】
段取り 20分
故障 20分
調整 20分
不良 2%
正味稼動率=(400個×0.8)/400分×100=80%
(1-正味稼動率)がチョコ停によるロスである。
性能稼動率= 0.625×0.800×100=50%
良品率 98%
総合効率= 0.87×0.5×0.98×100=42.6%
人の効率化阻害の5大ロスの構造
5大ロスを時間的側面から検討すると,図2・4のように表される。時間と効率化に関する指標の定義は以下のとおりである。
就業工数
会社が賃金を支払う対象となる時間,いわゆる拘束時間であり,1日8時間,月間で8時間×24日である。
負荷工数
就業工数から除外工数(他部門応援),休憩時間,朝礼時間などを引いたもので,実際に生産計画を達成するために,設備が稼動しなければならない時間ある。
正味作業工数
実際に作業に投入した時間(工数)である。負荷工数から故障,段取り,刃具、立上がりなどの設備に関連するロスによって機械を停止する時間と,部品を取りに行くムダな動作や探す動作,刃具を調整するなど人に起因するロスの両方を引いたものである。
有効工数
正味作業工数のうち,実際に作業している工数である。すなわち,正味作業工数から,人員配置のまずさに伴うアンバランスロス,非定常作業の発生に伴う処理工数,自動化が不十分なために発生しているロスなどを引いたものである。
価値工数(出来高工数)
有効工数から,不良・手直しにかかった工数,品質が不安定なために頻繁に測定を行う工数を引いたもので,出来高に結びついた工数である。
設備総合効率に対する人の工数との関係
設備総合効率の向上には,設備の7大ロスが影響することはもちろん人であるが,それ以外に人の作業のやり方,作業の遅れ,スキル不足,レイアウトのまずさなどに起因する人のロスが影響し,それは性能稼動率に現れる。
半自動機の場合
故障停止が1日に60分,段取替えが60分かかり,負荷時間が1日460分とすれば,時間稼動率は
460-(60+60)÷460×100≒74%
一方,速度低下ロスがゼロで(基準サイクルタイムどおり運転されている),チョコ停・空転ロスが1日120回発生し,その処置に1分/回かかったとすれば,120分のロスタイムが発生しているとき,基準サイクルタイムを0.5分/個,出来高を500とすると,性能稼動率は,
基準サイクル・タイム×出来高)÷(負荷時間-停止時間)=(0.5×500)÷(460-120)×100≒73.5%
となる。これは人がムダな動作がなく作業した場合である。
しかし実際には,人の動作遅れ,作業遅れ,レイアウトのまずさなどによって作業ロスが発生し,出来高も450くらいの場合が多い。このようなとき,人の動作ロス,をみるには,能率の指標を用いる。すなわち,
(0.5×450)÷460-(60+60)×100≒66%
したがって,性能稼動率73.5%から66%を引いた7.5%が,人の動作ロスに起因しているということになる。
自動化ラインの場合
この場合は,以下の2つでとらえる。
●設計人員に対する実際人員の差
●無人運転率の向上
前者は,新ラインを設計する場合に,あらかじめ何人と設定するが,実際にはチョコ停,刃具ロス,品質ロスなどでトラブルが多く,設計時の見積り人員より多くかかる。したがって,これらのトラブルを減少させ,設計人員で運転することを考えていく必要がある。
後者は,昼休み無人運転あるいは直間の2時間の無人運転を行うためにトラブルの解消を図る。さらに夜間無人運転まで行うようにする。 いずれにしても,設備の7大ロスについては時間的な把握はできるが,人の動作ロスは時間的にとらえるのはむずかしい。
原単位の効率化阻害の3大ロスの算出法
歩留りロスについては向上率,エネルギーロス,型・治工具ロスについては削減率で表す。
●歩留まり向上率=(1 -改善後の投入材料の総重量/現状の投入材料の総重量)×100
●エネルギー削減率=(1 – 改善後の投入エネルギー/現状の投入エネルギー)×100
●型・治工具ロスの削減率=(1-改善後の投入金額/現状の投入金額)×100
生産効率化の進め方のステップ
生産効率化の最終的なねらいは,製造原価をいかに低減させるかにある。そのためには,時間当たりの出来高増,1人当たりの労働生産性の向上,材料仕損費の低減などが必要となる。
生産効率化を進めるにあたっては,表2・2の手順で行うのが一般的である。
第1ステップ:設備7大ロスの低減
生産効率化の第1ステップは,7大ロスを定量的に測定し,その改善を図ることに全力投球することにある。
7大ロスは,すべての設備に発生しているものではなく,設備の特性,製品特性,設備管理のレベルなどにより発生状態は異なってくる。故障,チョコ停が頻発し,稼動率を悪化させている場合もあり,段取替え時間が長くかつ回数が多くて稼動率を悪化させている場合もある。したがって,7大ロスが発生しているのか,どの程度発生しているのかの測定を実施することが必要である。
一般的に,7大ロスについての問題点として,
●7大ロスのそれぞれの定義が不明確
●測定の仕組みができていない
●測定の仕組みはできているが
基礎データの精度が悪い
データをまとめていない
ロスの構造が把握されていない
●解決すべき課題と,それの寄与率の優先順位がはっきりしていない
●ネックエ程がはっきりしていない
などがあり,ロスの構造がどうなっているか,その大きさを認識することから始めることが必要である。
また,第1ステップでは,設備の固有能力を阻害している7大ロスを定量的に顕在化することであり,その寄与率はどの程度なのか,対策するときの優先順位は何かを明確にするべきである。
また,各工程の能力バランスはどうかを検討し,第1,第2,第3のネック工程を明確にし,ネックエ程を左右するのは何かも,合わせて検討するべきである。
各ロス項目の不稼動要因を明確にし,それを減少するためには,現時点で考えられるテーマをすべてリストアップすることが必要である。各テーマごとに
●寄与率–設備総合効率への寄与率
●難易度–原因・対策のわかっているテーマ
簡単な取り組みやすいテーマ
多工程に関連する大きなテーマ
原因がわからない慢性的なテーマ
●優先順位–各テーマの改善する順位
●分担–各階層別(課長・係長・班長・リーダー)で改善するもの,スタッフが改善するものの分担を決める。
などを検討し,効果の大きいもの,取り組みやすいものから改善を実施することが望ましい。表2・3は,テーマの難易度を考慮し,各職制・スタッフ別に割りつけた例である。
また7大ロスが時系列的にどう変化しているか,改善効果が寄与しているか,別の問題が発生していないかなどをフォローする必要がある。
表2・3 個別改善のテーマと階層別担当
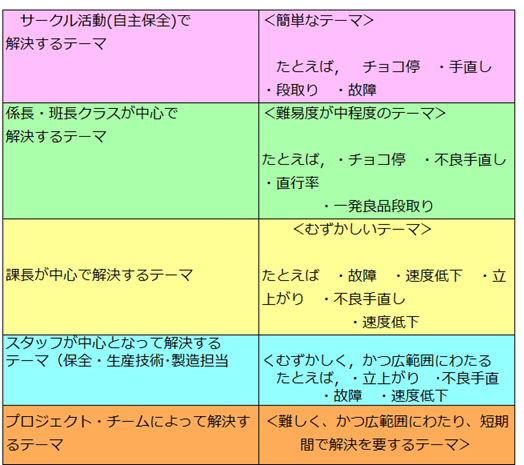
個別改善のテーマと階層別担当
第2ステップ:設備総合効率の向上
一般的に,7大ロスを減少させることが,すぐに設備総合効率の向上につながる場合が多いため,7大ロスの改善を徹底的に行うことが得策である。そして,7大ロスのうち改善を行ったロス項目について,
●改善の成果が出ているか
●それが設備総合効率にどれだけ寄与したか,寄与していないとすればその理由は何か
●7大ロスの構造は変化したか
●従来から発生している慢性的なもの以外に,突発的なものはあるのか,ないのか
●今後,重点的に解決するべきロスと課題は何かなどをフォローし,効果を上げることが必要である。
ロスの構造は,一定の傾向はあるが各月により変動し,その内容を見て的確な対策をとる必要があるため,ロス構造の時系列なデータの推移をチェックする必要がある。
しかし,7大ロスが減少しても,必ずしも設備総合効率が向上しない場合がある。それは,次のようなケースである。
●前工程からの物の流れが悪く,手待ちロスが多く発生するケース
●段取り回数の増加によるケース
前者は,7大ロスが減少し効率が上がった分,前工程からの物の流れが悪いために,余計に手待ちが発生する場合である。
これは,もともとその傾向があったにもかかわらず,7大ロスが発生しているときは,その傾向が顕在化されなかったにすぎないことによる。
しかし,7大ロスが減少した分,効率が上がり稼動時間が少なくてすむようになったために,手待ちが大きく顕在化するようになったのである。
その原因が外注の能力不足,管理上のミス,生産計画上のミスにあろうと,それらの原因を追求し,総合効率を上げる対策を行う必要がある。
後者は,段取り回数が増加することにより総合効率が上がらないケースである。
どの企業でもロットが小さくなることは避けられないため,どうしても段取り回数が増加する傾向にある。
段取り時間の短縮を行っても,その効果よりも回数、増加によるロスが上回るために,総合効率が上がらないのである。
したがって,1回当たりの段取り時間の短縮をさらに進める必要がある。
いずれにしても,設備総合効率が向上しなくては意味がない,7大ロスを徹底的に低減するとともに手待ちロスを解消し,効果を上げることである。
第3ステップ:労働生産性の向上
7大ロスが減少し,設備総合効率が向上した段階で,次に行うことは労働生産性をいかに向上させるかである。
一般的に設備総合効率が向上すると,出来高生産性(出来高/時間)は当然向上するものである。
しかし,労働生産性(出来高/人・時間)は必ずしも向上しない場合がある。
ここで労働生産性とは,1人(当たり)の時間当たり出来高を表す指標である。
最終的には,この労働生産性が向上して初めて効果が出るものであり,これが向上しないとあまり意味がない。設備総合効率が向上しても労働生産性が向上しないのは,配置人員をそのままにしているからにほかならない。
現状の配置人,員が,設計時点の見積り人員に対して多く必要となるのは,チョコ停・調整頻度が多い,手直し品が多い,刃具交換の頻度が多いなどのトラブル処理のために,配置せざるを得ないという場合が多い。したがって,設備総合効率が向上した段階では,
●1人当たりの持ち台数は増加できないか
●人員の削減はできないか
●レイアウト変更により,さらに人員を削減できないか
●ワークの供給,払出しのズトッカー量を改善し,さらに人員は削減できないか
●簡単な自動化(あまり費用をかけない)を行うことにより,人員の削減はできないか
などを検討する必要がある。
労働生産性を向上させるためには,上記の観点から検討するとともに,それを推進するうえでの阻害要因はあるのか,それを解決するにはどうするかなどを検討し,生産性を上げることが重要である。
第4ステップ:昼休み無人運転の推進
労働生産性をさらに向上させるためには,昼休み,シフト間の無人運転を指向するべきである。昼休みの1時間をフルに稼動すれば,約10%の生産性向上につながり,効果も大きいものである。昼休み無人運転を行うねらいは,次の点にある。
●生産性の向上
●問題点の顕在化
●上記問題点を解決するための技能のレベルアップ
無人運転を推進することによって,次のようなことが顕在化される。
●従来からの問題点がさらに明確になる
●チョコ停の発生間隔が意外に短く,また多発している(これは,チョコ停の回数把握精度が悪かったためである)
●誤動作による停止がときどきある
●予期しない問題点が顕在化される
●設備の調整を行わないために(無人運転のために),手直しが一部発生する
●センサーの異常による停止が発生する
●ワーク拠送系の姿勢が悪く,過負荷で停止するには,オペレーターが監視している場合はライン停止を伴わないため,無雑作にそれを修正するために問題点として顕在化されない) このように,無人運転を行うとさまざまな問題点がクローズアップされるが,それぞれに対して技術的な改善を加えることが必要である。
設備に対し,寸法調整,条件変更,ワークの姿勢を修正する,チョコ停を改善するなどでタッチするユニットや部品,回数を調査し,それをノータッチ化することがポイントである。
そして, MTBFを1~2時間からさらに改善し,いかに5~6時間に延長するかが課題である。
第5ステップ:原価低減の推進
TPM活動の最終的な成果は,原価がどれだけ減少したかという,原価面に反映するものでなければならない。原価低減が達成できないようでは, TPM活動が成功したとはいえない。設備総合効率が向上し労働生産性が向上すれば,当然、製造原価は減少するはずである。これらの向上分が,原価にどう反映したかを検討する必要がある。検討項目としては,以下のようなものがある。
●目標原価は達成したか
●期待した原価低減はできたか,もしできていないとすれば,その理由は何か
●解決すべき課題は何か,それを解決した場合の寄与率はどうか
●変動費率は減少したか,費目別に変化はないか
●標準原価の場合,原価差額,材料費差額,加工費差額はどうか
●工場全体の収益改善に,どの程度貢献しているか
設備総合効率・労働生産性の向上が,原価低減にどれだけ貢献したか,していない場合はその他のコストアッブ要因があるためであり,それらを追求し解消すことが必要である。
図2・5にTPMの成果指標の体系化の例を示す。
原価低減を図る場合,操業度の高低により低減のねらいどころを変える必要がある。
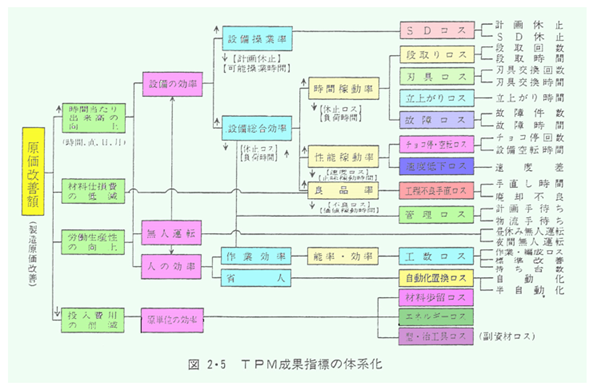
TPMの成果指標の体系化
① 操業度が高い場合
出来高の増産によるメリットと,それを達成するため7大ロスの低減を中心に進め,とくにサイクルの短縮,手直し品の低減などを図る。
② 操業度が低い場合
原単位ロスの低減と労働生産性向上による原価低減を図るため,とくに以下のようなことに重点をおいて進める。
●持ち台数による省人化を図る
●自動化(ローディング・アンローディング)の推進と省人化を図る
●昼休み,シフト間の無人運転の推進
●型・治工具の修理費の低減を図る
●1台当たり(製品)の刃具費およびエネルギー費の低減を図る
●歩留り向上による原単位ロスの低減を図る
第6ステップ:夜間無人化の推進
TPMを実施した場合の究極の目標は夜間無人化ライン”の確立にあるといえよう。無人化の考えは従来から指向され,昼休み無人運転・夜間の無人運転などは部分的には実施されているが,完全な夜間無人運転のケースは少ない。
FAライン・FMSラインの名のもとに宣伝はされているが,無人化ではなく省人化の域を脱していない(一部のマシニングセンターでは行われている)。
無人化がなかなか進まない理由は,
●故障の対策が不十分である
●刃具寿命が一直分もたない
●ワークの自動計測システムが確立されていない
●搬送系のチョコ停の対策が不十分である
●オペレーターによる調整作業が多い
●寸法維持のための調整 ・チョコ停のための調整
●不良の出ない条件(良品条件)が確立されていない
●不良の出ない条件を維持している時間が短い
などの研究が不足しているためである。
刃具の寿命延長については,振動解析(後述)によってどこまで延長が可能かということにかかってくる。もしー直分延長できない場合には,工程を分割する方法も考えられよう。また搬送系のチョコ停については,類似設備でその発生メカニズムを解明することは可能であり,対策は立てられよう。
ここで一番問題になるのは,不良の出ない設備–QA設備-をどう作り上げるかある。品質を保証する設備-QA設備-とは,製品の品質特性値を確実に維持でき,Cp値も1.67を維持できるものである, そのためには,不良の出ない条件を研究することが必要であり,次のステップを実施することがポイントである。
●現状ラインでの不良現象の層別
●おのおのの現象についてPM分析の実施
●各要因について維持すべき精度の範囲を設定
●品質特性と設備部位の関係を品質保全マトリックスに整備
●維持すべき精度の測定方法を決め,容易に測定できること
夜間無人運転の効果はいうまでもなく大きいものであり,無人化のための阻害要因を整理し,それらを解決することが技術のレベルアップにつながるものであり, TPM活動の総仕上げをするということである。今後検討すべき大きな課題である。
PM分析を活用して慢性ロスを解決する方法
慢性不良や慢性故障のような慢性化した不具合を原理・原則に従って物理的に解析し不具合の現象のメカニズムを明らかにしそれらに影響すると考えられる要因を設備上の構造上、人、材料、方法の面からすべてリストアップする方法。
PM分析のPMとは予防保全、生産保全の意味ではなくPにはPhenomenon(現象)、physical(物理的)という意味がありMにはmechanism(メカニズム)machine(設備) man (人)material(材料) method(方法)の意味がある。
PM分析表の活用法と具体例を解説
PM分析とは、製品やサービスの不良や故障といった問題の原因を、物理的な視点から深く掘り下げて分析し、そのメカニズムを解明するための手法です。そして、その分析結果をまとめたものがPM分析表です。
PM分析の目的
- 問題の根本原因の特定: 表面的な症状だけでなく、問題の本質的な原因を突き止める
- 再発防止策の策定: 根本原因に基づいた効果的な対策を立てる
- 品質向上: 製品やサービスの品質を安定的に高める
PM分析の考え方
PM分析では、問題の原因を以下の4つの要素(4M)から分析します。
- Machine(機械): 機械の構造、摩耗、不良など
- Man(人): 操作ミス、技能不足、メンテナンス不足など
- Material(材料):材料の品質、異物混入、劣化など
- Method(方法):作業手順、工程管理、検査方法など
これらの要素を一つ一つ丁寧に分析し、問題発生のメカニズムを明らかにすることで、効果的な改善策を導き出すことができます。
PM分析表の構成(例)
PM分析表の構成は、分析する問題や企業によって異なりますが、一般的には以下の項目が含まれます。
- 問題点: 具体的にどのような問題が発生しているのか
- 現象: 問題がどのように現れているのか
- 原因仮説: 考えられる原因を複数列挙
- 検証方法: 各原因仮説を検証する方法
- 結果: 検証結果に基づいた結論
- 対策: 改善策
PM分析のメリット
- 問題解決の効率化: 根本原因に焦点を当てることで、無駄な対策を減らす
- 品質向上: 製品やサービスの品質が安定し、顧客満足度向上につながる
- コスト削減: 不良品発生の減少や、生産効率の向上によるコスト削減
- 従業員のスキルアップ: 問題解決能力の向上
PM分析表の例
故障の原因を部品レベル迄、分析する
具体的PM分析表の実例
加工図を描き、原理を理解する
慢性ロスと突発ロスの比較
慢性とは常時,同一の現象が,あるバラツキの範囲で発生するものをいい,突発とは,慢性的に発生する現象が,あるバラツキの水準から突発的にとび出したものをいう。同一現象が量的に多くなる場合と,異質の現象が現れる場合がある。
突発的なものは復元的問題であり,何かの条件変動(治工具,作業方法,設備の状態)が起きたときに発生するもので,元の水準に戻すための復元的対策が必要である(図2・6参照)。
慢性的なものはやっかいな問題であり,種々の対策を打ってもなかなか解決されない問題であり,対策としては従来とは異なった革新的な対策,すなわち見方を変えた管理ポイントを新たに設定し,管理することが必要である。
ジュラン博士は,”現代品質経営”の中で次のように表現している。
「突発的なものは,状況の変化によって起きるものであり,その変動要因を復元しさえすれば,元の状態に戻る。慢性的なものは,持続性の好ましくないものであり、従来の管理ポイントを全面的に見直す必要がある。現状打破(Break Through)の考え方が必要である」
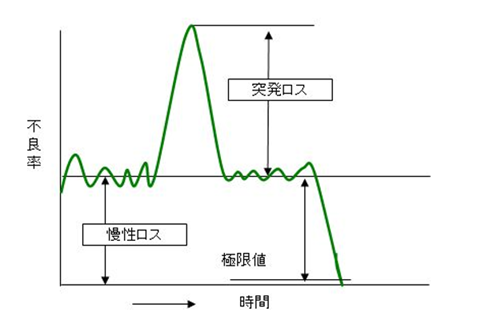
慢性ロスと突発ロス
慢性と突発の比較
(1) 発生状態による比較
発生状況による比較であり,2・5・1項のとおりである。
(2) 潜在化の程度による比較(表2・4参照)
突発的なものは,現状水準との比較によってロスとして顕在化されやすいが,慢性的なものは潜在化してしまい,顕在化されにくい傾向がある。
それは,気づかない,見逃している,思い込み,あきらめ,効果測定の問題などに起因する。
したがって,慢性的ロスを顕在化させるには,極限値または技術的なレペルとの比較によってはじめて明確になる場合が多い。
たとえば,チョコ停がかなりの回数発生している場合,それによるロスが定量的に把握されていないと, どの程度のロス,が発生しているかわからない。
これは極限値・理論値(正味稼動時間を1サイクルの時間で割った値)と比較すれば,簡単にロスが浮き彫りになってくる。
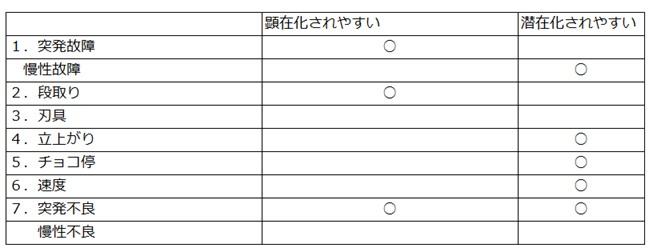
潜在化の程度による比較
(3) 原因系による比較
突発的なものは,比較的簡単に原因-結果の関係がつきとめられやすいが,慢性的なものは原因―結果の関係が不明確な場合が多く,単一原因の場合は少なく複合的原因である場合が多い。
(4) 対策系による比較
突発的なものは,前述のように原因系がわかりやすいために対策が打ちやすいが,慢性的なものは複合原因によるため,種々の対策をとってもなかなか解決できない。
(5)経済性による比較
突発的なものは,1回発生するとその損失は大きいのに比べ,慢性的なものは1回の損失は少ないが,常時発生しているため,その累積値は大きくなり,その損失額も大きくなる傾向がある。 以上のように突発的なものは顕在化しやすく,原因系がはっきりしやすいため,的確な対策が打ちやすいが,慢性的なものは潜在化しやすく,ロスがロスして顕在化しにくい性質がある。
したがって,潜在化しているものをいかに顕在化させるか,そのために極限値との比較あるいは技術レペルとの比較を行い,的確な対策を打つことが必要である。
一般的に,突発的なものに対しては十分とはいえないまでも手を打っているが,慢性的なものには手つかずの状況といえる。以下,慢性ロスを中心に説明を加える。
慢性ロスの特徴
まず「慢性ロスの考え方」について説明していく。慢性ロスを改善する場合に重要なことは,まず「慢性ロスの特徴を十分に把握する」ということである。
慢性ロスの特徴を整理すると,次の2点にしぼられる(図2・7)。
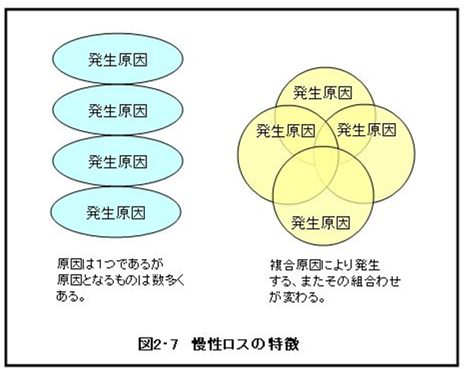
慢性ロスの特徴
(1) 原因は1つであるが,原因となるものは数多くあり,それがそのつど変わる
たとえば,原因となるものがAからJの10が考えられるとすれば,Aが原因となる場合もあり,CやDがなる場合もあり,毎回コロコロ変わるということ
である。しだかって特定のもの,たとえばAだけを重点的に対策を打っても,効果はあまり期待できない。 具体的に説明すると,ベアリングの外・内輪のボール軌道面のホーニング仕上げ面は,品質に大きな影響を与えるものである。
たとえば,仕上げ面の不良として粗目残りがあり,1~2%発生している場合を考えてみる。
粗目残りの要因として,ホーニング砥石の形状,砥石の取付け方法,ドレス不良砥石の目詰まり,砥石ホルダーのガタ,ワークスピンドルのガタ,研磨工程の曲率不良加工条件,その他10数項目が考えられる。
前工程の曲率不良が原因の場合もあり,砥石の取付け方法が原因の場合もあり,また10数項目がそれぞれ原因となる場合もある。したがって,原因となるものは毎回変わると考えなくてはならない。
このようなことから,対策としては,原因と考えられるものすべてについて対策して,正しい状態に維持し,変動させないようにしなければ,問題は解決しない。原因を見きわめることができれば問題はないが,見きわめることはなかなか困難なために,このような考え方が必要になるのである。
(2) 複合原因により発生し,その要因の組合わせがそのつど変わる
このケースは前項の場合と違って,いろいろな要因が重なり合って,それが複合された状態で現象を発生させる--つまり複合原因によって発生する場合である。さらに始末の悪いことは,その要因の組合わせが変わることも考えられることである。
すなわち, ABCの要因が重なって現象を発生させる場合,ACGHの要因が重なる場合というように,その組合わせがそのつど変わる場合である。 たとえば,内面研削盤で部品の仕上げ研磨する工程で,真円度不良が出る場合を考えてみる。
材料寸法にバラツキがあるうえに,ワーク取付け基準板が摩耗していたり,さらに砥石スピンドルの振れ,タイルの剛性が弱いなどの要因が重なって,ときどき不良を発生させる場合がある。これらは,それぞれの要因が重なって複合され,それが原因となって真円度不良を起こしているのである。
したがって,原因と考えられるものすべてに対して,1つずつ対策を打たなければ解決しない。原因はこれこれである,といった決めつけ,絞り込みをすることが一番よくないのである。 さて,多くの現場でみられることは,このような慢性ロスの特徴を理解しないままに対策を打っているために,故障や不良が減少しないことである。
その典型的な例は,前述のように「現象を十分に解析しないまま原因を決めつける,絞りすぎる」ことなのである。原因はこれとこれだと決めつけて,それに対してのみ対策を打ち,それ以外は全然考えもしないし,対策もしない。
対策そのものは的を射たものであり,そのものには効果的であっても,他の原因のものについて対策をしていないために,一時的には良くなるが,長続きしないため結果として良くならない場合が多い。このように,慢性ロスの特性を十分理解していないことが一番大きな問題なのである。
TPM 改善の考え方
慢性ロスはなぜ発生し,なぜ減少しないのだろうか。それをひと言でいえば,設備の信頼度が低いからにほかならない。信頼度とは,設備・機器・システムが与えられた条件で規定の期間中,要求された機能を果たす確率である。
-定期間内にトラブル(不良・故障)を起こさない確率であるといえる。信頼度が低いから故障や不良の発生を伴い,その発生サイクルが短いから慢性化するのである。
信頼度は,固有信頼度と使用信頼度から成り立っている。固有信頼度とは設計に起因する信頼度で,設計,製作の段階で決まってしまうものである。使用信頼度とは,使用する側に起因する信頼度であり,使用条件・方法のまずさに起因するものである。また,固有信頼度と使用信頼度は次のように細分化され,全体の信頼度は,それぞれの相乗積となる。

固有信頼度と使用信頼度
設計信頼度
設計信頼度とは,設計上に起因する信頼度である。設計自体に問題があり卜ラブルが発生する場合で,次の項目がある。
●部品形状にマッチしない治工具
●機構自体に問題
●部品の選択に問題
●検出システムに問題
●部品寿命が短い
製作信頼度
製作信頼度とは,部品の製作・組立上のまずさに起因する信頼度であり,部品の製作・組付けに問題かおりトラブルが発生するもので,次のような項目がある。
●部品の寸法精度に問題
●部品の形状に問題
●組付けに問題
据付け信頼度
据付け信頼度とは,設備の据付け上のまずさに起因する信頼度であり,据付け上に問題がありトラブルが発生するもので,次の項目がある。
●据付けの不備による振動の発生
●水平度不良
●据付けの不備による配管・配線の不備
運転操作信頼度
運転操作信頼度とは,運転操作のまずさに起因する信頼度であり,操作上に問題かありトラブルが発生するもので,次の項目がある。
●操作ミス
●段取調整ミス
●基本条件の不徹底
●使用条件のミス
保全信頼度
保全信頼度とは,保全品質のまずさに起因する信頼度である。保全上に問題がありトラブルを発生するもので,次の項目がある。
●部品の交換ミス
●組付け精度不良
一般的には使用信頼度の不備に起因するものが多く,設計信頼度に起因するものは少ないといえる。
故障・不良などのトラブルが発生した場合,それらの原因がどの信頼度に起因するかを検討することが必要である。信頼度が低いのは,設備の使い方の研究が不足しているからと考えられる。設備の使い方とは,設備を使うノウハウの研究であり,設備を使い切る技術と設備を使いこなす技術から成り立っている(図2・8,9参照)。
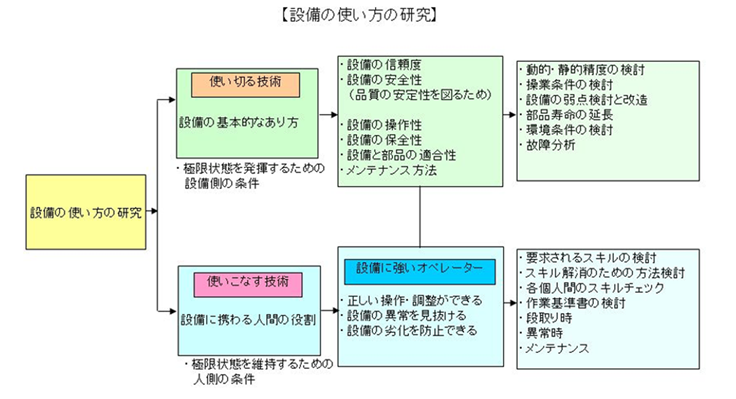
設備の使い方
設備を使い切る技術とは,部品特性を考えて,より良い品質を作るために設備が具備すべき条件,より稼動率(時間・速度)を高めるために具備すべき条件,より操作性・保全性を容易にするための条件などの研究を行い,設備の最高状態を発揮させるための設備本体,周辺機器に関する基本的なあり方を研究することである。
設備を使いこなす研究とは,設備を常に最高状態に維持するための操作・調整・異常発見・異常処置などの,設備に携わる人の役割は何かを研究することである。 設備を使い切る技術が先行していてもそれを使う人の腕が遅れていて,やるべきことを十分にやらなければトラブルの発生につながる。
逆に人の腕が良くて,やるべきことを十分やったとしても,設備自体に問題があればトラブルの発生は避けられない,この両者のうち,どちらかでも研究不足であれば効果が半減するため,両者が車の両輪のように同一のレペルになることが必要であり,そうなって初めてマンーマシン系の総合効率化が可能になる。
設備はいつでも購入できるが,設備を使い切るノウハウは購入することはできない。このノウハウは自社で開発育成する以外にない。これが十分でないために,せっかくの設備がホコリをかぶったり,トラブル多発のために稼動が不十分であったりする例は非常に多い。旧設備の使い方の研究を十分にしないで,性能・大型化の設備導入を行っても,基礎ができていなから使い切るには時がかかり,同一の失敗を繰り返す可能性が大きい。
図2・9 設備の使い方の研究と改善の基本的考え方の関係
復元の考え方
復元とは,元の正しい状態に戻すことである。あらゆる設備は,時間の経過ともに少しずつ変化するものであり,その変化の度合いを検知し,度合いの度により元の正しい状態に戻すことが復元である。設備・構成部品の特性により,変化の状態が一定時間後に急激に現れたり,また一定時間後から漸増傾向を示したりの違いはあるにしろ,必ず発生するものである(図2・10参照)。
故障劣化の進行状態
一般的にこのような変化は,知らず知らずのうちに発生している場合が多く,またこれらの変化は,そうとう大きくならなければ確認できないため,小さな変化は見落としがちである。
大きな変化は,復元のための修理をせずに放置すると突発故障につながったりするので,そのまま放置しておくことは少ないが,小さな変化も放置しておくと,時間経過とともに突発故障につながるか,そこまでいかない場合でも慢性ロスの原因となる場合が多い。
この変化の度合いを劣化という。
劣化には,自然劣化と強制劣化の2種類かある。
自然劣化とは,正しい使い方をしていても物理的に劣化が進行するものをいい,強制劣化とは,人為的に劣化を促進させるもので,自然劣化の時間より当然短くなる,強制劣化とは,給油をしなければならない場所に給油をしない,掃除すべき場所を掃除しない。
など,当然やるべきことをしないために劣化を促進させることであり,劣化を見逃しているためにそれが強制劣化につながる場合もある。”生産現場は強制劣化の塊である”といっても過言ではない。いずれにしても劣化を放置しておくと,時間経過に従って劣化が大きくなり,他の部位に影響を及ぼし,劣化が劣化を誘発する場合もある。これを”ガクがガタを呼ぶ”ガタの連鎖反応”と表現している。
1本のボトルのゆるみが振動を発生させ,その振動がだんだん大きくなり,他の部位の振動を呼び起こし,”ガタがガクを呼ぶ”ことは日常頻繁に見られる現象である。したがって,劣化の状態を見きわめて,早目早目に復元をすることが望ましい。
設備の初期清掃
劣化を復元するといっても,
●元の正しい状態がわからない
●劣化を検知する方法が決められていない
●判断方法・基準がない
●復元のための方法がわからない
場合が多い。このようなことがないように,基準を設定する必要がある。
設備の劣化をチェックする手段として,清掃が非常に有効である。われわれま,この考え方で”清掃は点検なり”を各社に普及させるようにつとめている
このねらいは
●清掃することにより,各部位に接触する
●接触する動作を通じ,各部位の不具合点(発熱・振動・ガタ・異音)を発見することが可能である
●清掃をすること(ゴミ・汚れ・廃油などの一掃)により,強制劣化の進行を防止する
ことにあり,清掃をすることが設備の不具合を発見する有効な手段であるといえる。清掃をすることは,この他にも部品の寿命の延長,設備精度の維持,品質基準の維持などのためにも欠かせない条件であると言える。
車が汚れた場合に洗車する例で考えてみよう,自動洗車機で洗う場合と自分の手で洗うことの違いは何か。車をきれいにする,汚れを一掃するなどの心理的効果は同じであるが,自分で洗うことにより点検する(タイヤの摩耗,釘,亀裂,ボディのキズ,錆などの不具合の発見)ことの物理的効果を見逃すことはできない。これと同様に,設備も自分の手を汚しながら清掃をし,その過程を通じて不具合点を見つけ出すことが大切である。
TPMの初期清掃
予知保全の研究が最近各社で行われているが,これは設備・ユニットの劣化の進行状況を物理的,化学的な特性値で測定し,正常な状態と比較しながら劣化の状態をチェックする方法である。進行状況がある限度以上になれば、オーバーホール、部品の交換などの事前処置を行い、故障を未然に防止する方法で
●劣化の測定を何で行うか。
●異常の兆候をどう検知するか
●正常な状態とは何か
●異常の限度はどうかが設定せれていなければならない。
たとえば、高速回転の軸受けの劣化測定に振動、その他の変化を追跡する方法が一般に採用されているが、これも正常な振動に対し、時系列的に変動があるかなかをチェックし、その交換時期を推定する方法である。
したがって、予知保全のためには劣化の測定、検知方法が不可欠である。設備の故障が短いサイクルで発生する場合、機構の変更、部品の形状変更、材質変更などの対策を行うケースが見受けられる。しかし、このような対策を行っても結果はいっこうに良くならず、失敗するケースが多い。
これは機構、部品形状、材質などの問題でなく、部品磨耗、仕上がり精度、組み付け方法、組み付け精度に原因があるので、これを正しい状態に復元することにより故障が発生しない状態になる。したがって、機構、部品の変更の前に復元を行い、その結果を確認し、良くならなければはじめて改善を行うことが望ましい。
設備というものはそれを構成する部品、ユニット間の強度や精度のバランスがとれていて、はじめてその機能をまっとうできるものであり、復元とは設備全体としての強度、精度のバランスを取り直すことでなければならない。したがって、故障部位だけを復元したり、改造したりしても、強度、精度のバランスが復元されないかぎり再びロスが発生することになる。
あるべき姿の考え方
あるべき姿とは、設備の機能・性能を最高に発揮・維持するために具備すべき条件である。設備を構成しているユニット、構成部品が工学的な原理・原則からみて、望ましい姿に維持されてはじめて性能・機能が100%、長時間にわたり発揮・維持されるものである。また、あるべき姿とは工学的原則、原理からの望ましい姿、あるいは機能中心に考えた場合、理想的な状態で考えたときの望ましい姿である。
TPM 保全のスキル:生産性を高めるための多岐にわたる能力
TPM(Total Productive Maintenance:全生産保全)は、設備の寿命を延ばし、生産性を向上させるための活動です。TPMの成功には、多岐にわたるスキルが求められます。
TPM保全に必要なスキル
1. 技術的なスキル
- 設備の知識: 担当する設備の構造、機能、原理を深く理解していること。
- 保全作業スキル: 点検、清掃、部品交換など、保全作業を安全かつ効率的に行うスキル。
- トラブルシューティング能力: 設備が故障した際に、原因を迅速かつ正確に特定し、復旧できる能力。
- 改善提案能力: 設備の性能向上や作業効率化のための改善策を提案できる能力。
2. 知識・経験
- TPMの知識: TPMの考え方、8本の柱、16大ロスなど、TPMに関する基礎知識を習得していること。
- 品質管理の知識: 品質管理の考え方、手法を理解し、品質向上に貢献できること。
- 安全管理の知識: 安全に関する法規、規定を遵守し、安全な作業環境を維持できること。
- 統計的な知識: データに基づいて問題分析を行い、改善策を立案できること。
3. コミュニケーション能力
- チームワーク: 他のメンバーと協力し、目標達成に向けて取り組むことができること。
- 報告・連絡・相談: 上司や関係部署に適切に報告・連絡・相談できること。
- 問題解決能力: 発生した問題に対して、関係者と協力して解決策を導き出すことができること。
4. 問題解決能力
- ロジカルシンキング: 論理的に考え、問題の本質を捉えることができること。
- 創造性: 新しいアイデアを出し、問題解決に繋げることができること。
TPM保全のスキルを習得する方法
- OJT (On-the-Job Training): 経験豊富な先輩社員から直接指導を受ける。
- OFF-JT (Off-the-Job Training): 外部研修や社内研修に参加し、体系的に学ぶ。
- 資格取得: 関連資格を取得することで、スキルアップを図る。
- 自己学習: 専門書を読んだり、インターネットで情報を収集したりする。
TPM保全のスキルが重要である理由
TPM保全のスキルを習得することで、以下のような効果が期待できます。
- 設備の寿命延長: 定期的な点検・保全により、設備の故障を防止し、寿命を延ばすことができます。
- 生産性の向上: 設備の稼働率を高め、生産性を向上させることができます。
- 品質の安定化: 品質不良の原因を早期に発見し、品質の安定化を図ることができます。
- コスト削減: 設備の故障による損失を減らし、コスト削減に貢献することができます。
- 従業員のモチベーション向上: TPM活動を通して、従業員の主体性や問題解決能力を高めることができます。
TPM保全は、企業の競争力強化に不可欠な活動です。従業員一人ひとりがスキルアップを図り、TPM活動に積極的に参加することで、企業全体のレベルアップにつながります。
まとめ
生産効率の向上という観点から、TPMでは以下の考え方で改善を進めます。
全従業員の参加、損失の最小化、予防保全、継続的な改善
又、TPMの成功には、多岐にわたるスキルが求められます。
*TMP活動の基本である『初心者向けTPM活動の基本と自主保全の重要性【図解】』については下記を参照願いします。
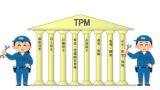
関連キーワード:
自主保全 計画保全 初期管理 品質保全 改善 標準化
5S QC7つ道具 PDCAサイクル
ものづくりドットコムへの記事掲載
『TPM、総合生産的な保全とは』を2014年5月13日 ものづくりドットコムに記事を掲載しました。
無料でTPMの資料がダウンロード
Googleスライド でTPM資料を無料ダウンロード
Googleスライドから無料でTPMの資料がダウンロードできます。
slideshare ダウンロード資料(PDF)
パワーポイントで作成した資料です。
引用文献:
今日からモノ知りシリーズ トコトンやさしいTPMの本
現場力を高める実践的TPM入門【改訂版】
わかる!使える!TPM入門 〈基礎知識〉〈段取り〉〈実践活動〉/日本プラントメンテナンス協会
わかる!使える!TPM入門 〈基礎知識〉〈段取り〉〈実践活動〉/日本プラントメンテナンス協会
コメント