TPM活動とは?基本を学ぼう
TPM(Total Productive Maintenance)は、製造現場における設備の寿命を延ばし、生産性を向上させるための活動です。全従業員が主体的に保全活動に参加し、設備のトラブルを未然に防ぎ、生産性を最大限に引き出すことを目指します。
TPMの考え方、哲学
TPM(Total Productive Maintenance)は、単なる保全活動ではなく、企業全体の生産性を向上させるための総合的な取り組みです。
TPMの哲学を理解し、具体的な活動に取り組むことで、企業はより高いレベルの生産性と品質を実現することができます。
QC活動
ロスを減らす活動でありロス発生後に活動→ゼロにならない。
待ちの改善活動・・・不良が発生しから分析、対策、改善。
TPM活動
ロスを未然に予防する活動、ロス前の活動→ゼロにできる。
攻めの改善活動・・・不良が発生する前に分析、対策、改善。
TPMの核心、本質
TPMの核心は、「生産システムにおけるあらゆるロスをゼロにする」という点にあります。このロスには、機械の故障だけでなく、人材、時間、材料など、あらゆる資源の無駄が含まれます。
ロスをゼロにする為には要因、プロセスの管理が必要ですが利益が出ない工場、儲からない会社は結果の管理に没頭しています。
TPMの誕生と歴史
1950年代から60年代にかけて米国から導入したPM(予防保全をもとにして日本独特のTPMを作り上げたのが1971年であった。
以来、1971年代から80年代にかけてTPMはその画期的な成果が認められて次第に発展しTPMによるPM賞受賞事業場数の急増あらゆる業種への広がり生産部門のTPMから全TPMへ、世界各国へのTPMの展開など、全社、全業種、全世界へと限りなく広がりをみせている。
日本電装で生まれたTPM
日本でTPMが初めて誕生したのは自動車部品の総合メーカーとして有名な日本電装である。
同社が生産保全を導入したのが1961年のことだったがその後トランスファー化などのオートメーションの進展に対応して、1969年から”全員参加のPM(略称TPM)を旗印にして素晴らしい成果を上げ、1971年度PM優秀事業賞(略称PM賞)を受賞した。
1964年から続けられている、このPM賞の審査表彰の中で日本電装のTPMが抜群であるとして、審査委員の全員から絶賛された。
この日本電装のTPM展開にあたっては、現在の社会法人日本プラントメンテナンス協会(略称 JIPの前身である当時の日本プラントエンジニア協会(略称 JIPE)が前面協力したのであるが、このTPMこそこれからのオートメーション時代、人間尊重時代にふさわしいものいであるとの認識にもとづき、以来、TPMの普及推進に全力をあげてきた。
生産部門のTPMから全社的なTPMへ
TPMでは生産部門における活動が中心であり、現在もそうであるが最近ではこれが生産部門以外の部門広がりをみせている。
たとえば事務部門のTMP、技術部門のTPM、営業部門のTMPなどがそれであり、TPMはいまや全社各部門へとその活動を拡大している。
TPMがその活動を生産部門にとどめているより、これが全社に展開されれば、もちろん巨大な社内パワーの結集と なり、それだけおおきな成果をあげることができる。
こうなると文字とおり、トップマネジメントから第一線の従業員、事務員、技術員全体が含まれた、全員参加活動となる。
TPMの定義
製造現場における設備の寿命を延ばし、生産性を最大限に引き出すための活動です。全従業員が主体的に保全活動に参加し、設備のトラブルを未然に防ぎ、生産性を最大限に引き出すことを目指します。
日本電装が初めて実施したTPMを産業界に普及していくために,JIPE(JIPMの前身)が1971年に定めたTPMの定義を表1・3に示す。当時は,生産部門を対象としたTPMであったから,この定義は生産部門のTPMの定義”だということができる。
ところが,TPMの普及発展とともに,生産システム効率化の極限追求のためには,生産部門のみでは不十分であることがわかり,開発,営業,管理などのあらゆる部門にわたってTPMを全社展開するようになってきた。つまり,今日すでに全社的なTPMが展開されており,この実態を表した定義を,新たに定めることが必要になった。
そこで1989年になって定めた新定義,すなわぢ全社的TPMの定義”が表1・4である。
最初の定義,つまり”生産部門のTPMの定義”と,新定義(全社的TPM)が比較対照しやすいように,新定義も5項目で定義づけられてる。
表1・3 TPMの定義(生産部門のTPM)
TPMの定義(生産部門のTPM)表1・4 TPMの新定義(全社的TPM)
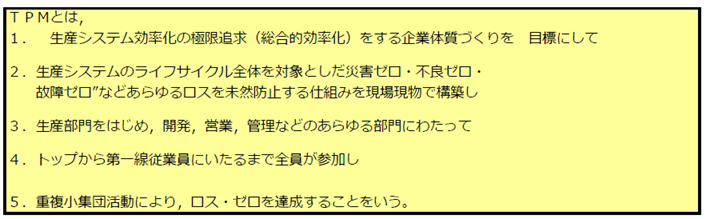
TPMの新定義(全社的TPM)
TPMの目的
TPMの目的は、以下の通りです。
- 設備の寿命延長: 計画的な保全活動により、設備の寿命を延ばし、交換や買い替えにかかるコストを削減します。
- 生産性の向上: 設備の故障やトラブルを減らし、生産の安定化を図ることで、生産性を向上させます。
- 品質の向上: 不良品発生を減らし、製品品質の安定化を図ります。
- コストの削減: 設備の故障による修理費や不良品発生による損失を削減します。
- 安全な作業環境の確保: 設備の安全な運用を確保することで、労働災害を防止します。
- 従業員のモチベーション向上: 全員参加型の活動であるため、従業員のモチベーション向上に繋がり、企業全体の活性化を図ります。
TPMの特徴
- 全員参加: 全員が主体的に保全活動に参加します。
- 自主管理: 各従業員が自分の担当する設備の状態を把握し、自主的に保全活動を行います。
- 計画的な保全: 設備の寿命を延ばすために、計画的な保全活動を実施します。
- ロス削減: 設備の故障や不良品発生など、さまざまなロスを削減し、生産性を向上させます。
TPM ”オペレーターの自主保全”
設備管理は設備の健康管理である。人間の身体の健康管理は予防医学によって非常によくなり寿命が伸びたが、予防保全は設備の予防医学であり設備の健康管理の基本だといえる。
身体の健康管理は身体を使う本人が病気にかからないように日頃から病気を予防することが第一である。さらに専門の医者が定期健康診断をして 異常を早期発見し、早期治療をすることによって健康が維持できる。
同様にオペレーターが自分の使う設備を自分で守る—これを自主保全という。故障や不良が出るのは設備の病気であり、設備が病気にかからないように日常の保全(清掃・給油・増締め・点検など)をしっかりやる。 さらにこれに加えて設備の専門の医者である保全マンが定期検査(診断)を行い、早期修理する。
米国では専門分業化が進んでおり、オペレーターは生産(運転)に専念し、保全は保全マンの仕事になっている。日常保全も保全マンの仕事であり、オペレーターの 仕事だとは思ってない。 このような米国流の分業は自動化・FA化の進展とともに見直しが必要だというのがTPMの主張である。
つまりものを作るのは自動化設備であり、その自動化設備の健康管理のための日常保全をオペレーターが担当するようにオペレーターと保全マンの分業の分かれ目を変えようというのである。
TPMは全員参加の小集団活動
日本的マネジメントは現在、小集団を抜きにしては考えられない。日本の小集団活動を大別すると、職制主導型とボランタリー型に分けられる。
TPMの小集団活動は職制主導型である。ボランタリー型の代表例はQCサークル活動である。ボランタリー型というのはやりたい人がやる—つまり、QCサークル活動はやりたい人が自分の時間で自由にやるのが原則だといわれる。
これに対してTPMの小集団活動は職制と一体となって、仕事そのものを従業員が自律的に行う活動なのである。前項で述べた自主保全を小集団活動によって行う。 自主保全、すなわち清掃、給油、増締め、点検などの日常保全をオペレーターが自分で行うがこのような自主保全はオペレーターの仕事そのものである。
やりたい人がやるボランタリー型とは全然違うのである。TPMでは職制と一体の小集団活動を行うがこれを”重複小集団活動“と呼んでいる。各階層ごとに、たとえば工場長をリーダーに各課長をメンバーをメンバーとする管理者層の小集団、課長をリーダーに係長、班長などの監督者層をメンバーとする小集団、係長、班長などの監督者層をリーダーに係員、班員など第一線従業員をメンバーとする第一線の小集団がそれぞれテーマや目標を決めて小集団活動を行う。このような、とくに職制主導型の重複小集団活動はTPMの大きな特色であり、これに対して伝統的な米国流PMではこのような活動はこれまで行われていない。
TPMは生産効率の総合的な極限を目標とする。
生産システムの多くはマン-マシン・システムであるが、自動化が進むに従い生産システムの設備依存度が高まり、生産効率は設備の作り方 、使い方、保全の仕方の良否に左右されることはいうまでもない。
TPMでは設備の作り方、使い方、保全の仕方を改善することによって、故障や段取り調整による停止ロス、チョコ停や速度低下による速度ロス、工程不良や立ち上がり、歩留まり低下による不良ロスなどをなくし、生産システムの効率を総合的に極限まで高めようというのが目標である。
これに対して伝統的な米国流PMでは設備の専門家中心のアプローチであるため設備の作り方、保全の仕方の改善による設備効率の極限追求をしても、設備の使い方まで踏み込んだ生産効率の総合的な極限追求はなされていない。
TPMとPM、TQC、JITの違い
PMという言葉は最初に米国から日本に入ってきた1950年頃には、予防保全(Preventive Maintenance)の意味で使われていた。
1950年代から60年代にかけてこの予防保全に続いて
生産保全(PM:Productive Maintenance)
改良保全(CM:Corrective Maintenance)
保全予防(MP:Maintenance Prevention)
信頼性工学(Reliability Engineering)
保全工学(Maintenability Engineering)
など数多くのことを米国から学んできた。そしてPMといえば設備管理の代名詞に思えるほど、米国流PMが日本に普及した。
このような米国流のPMに対して 日本流に工夫を加えて、日本式PMに仕立て直したのが TPM(Total Productive Maintenance)だということができる。
TPMは日本で生み出した日本独特の全社的設備管理方式であるがもちろん、米国から学んだPMの技術手法がベースになっていることはいうまでもない。それでは伝統的な米国流PMと日本で生み出したTPMとはいったいどこが違うのか。
以下にTPMの特色をあげながら、米国流PMとの相違点を 明らかにしてみたい。(表1・1 参照)
表1・1 TPMの特色と米国流PMとの相違点
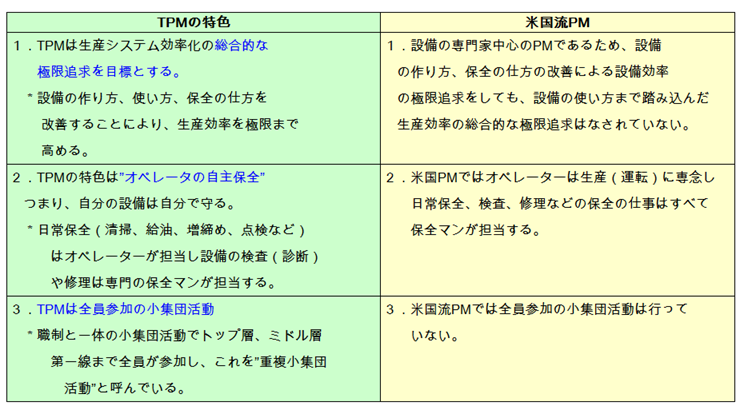
TPMと米国流PMとの相違点
JITとTPMに共通した基本理念
JITとTPMは密接不可分の関係にある。自動化・FA化の進んだ今日,『必要なものを,必要なときに,必要なだけ』生産するという,いわゆるJIT生産を実施するためには,突発故障やチョコ停や不良をゼロにし,また多品種少量生産のための段取り調整時間を極小化しなければならない。それらを可能にするのがTPMであり,JITの完全実施を支えるのがTPMであるといえる。
これをTPMの例からみるとJIT生産をしている工場ほどTPMによる成果が大きく上がるのである、ここでさらに強調しておきたいことはJITとTPMには共通した基本理念があるということである。
表1・5に示すとおり,JITとTPMに共通した基本理念として
1) 経営に直結する全社的な製造技術
2)徹底したムグの排除
3)未然防止
4) 現場(または現地)現物主義
5)参画経営・人間尊重
の5項目をあげることができるJITの基本理念は,大野耐一等(トヨタ生産方式)による。
表1・5 JITとTPMに共通した基本理念
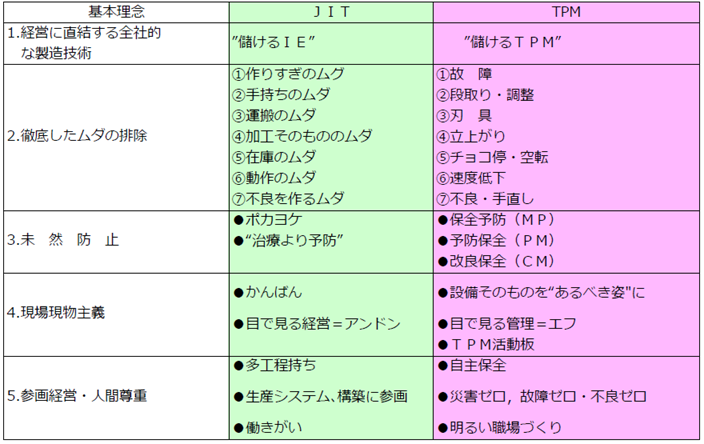
JITとTPMに共通した基本理念
T Q C とTPMの特色比較
TPMが全社的な展開になるに従い既に産業界に広く普及しているTQCといったいどこが違うのかという質問がよく出る。
表1.6は,TQCとTPMの特色比較をしたものである。TQCとTPMに共通しているのは,その目的が「企業の体質改善(業績向上と明るい職場づくり)」にあるという点である。ところが,この目的を達成するための手段・方法に,両者それぞれの特色がある。
表 1・6 T Q C とTPMの特色比較
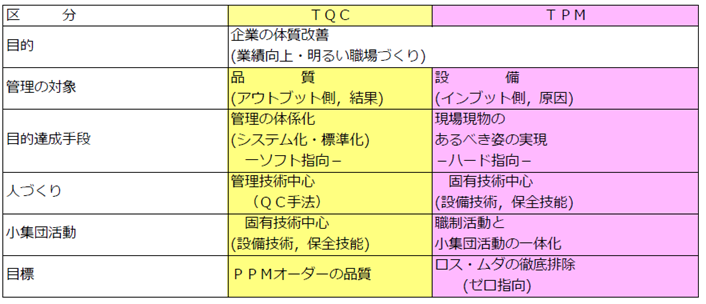
T Q C とTPMの特色比較
まず管理の対象であるが, TQCは「品質(アウトブット側,結果)」を対象とするのに対して, TPMは「設備(インブット側,原因)」を対象とすることが特色である。
次に目的達成の手段として, TQCは「管理の体系化(システム化・標準化)」で強調されるが, TPMでは「現場現物のあるべき姿の実現」に重点を置く。
つまり,クリーンな職場づくり,”災害ゼロ,不良ゼロ,故障ゼロ”の設備そこものを実現することである。
人づくりでは, TQCが管理技術(QC手法)中心であるのに対して, TPMでは固有技術(設備技術,保全技能)が中心で,”設備に強い人づくり”を行う。
小集団活動では, TOCが「ボランタリー型のサークル活動」であるのに対して, TPMでは「職制活動と小集団活動のー体化」,換言すればトッブから 第一線までが全員参加して,仕事として行う職制主導型の重複小集団活動なのである。 目標については, TQCで「PPMオーダーの品質(100万個あたりの不良個数)」などといわれるが, TPMではロス・ムダの徹底排除,すなわちゼロ指向である。
TPM展開プログラムの12ステップとは
TPM展開プログラムの12ステップを,最初に発表したのは1983年のことであった。
以来,TPMを展開するときにはこのステップが採用される。
一方, 1980年代の中頃からTPMの全社展開をする企業が出はじめTPMの定義も全社的TPMに合わせた新定義が定められた。
そこでTPMの全社展開に対応して TPM展開プログラム12ステップを新しくしたものが表1・8である。
表1・8に示すとおりTPM展開の段階を
(1) 導入準備段階……第1~5ステップ
(2)導入開始……第6ステッブ
(3) 導入実施段階……第7~11ステッブ
(4) 定着段階……第12ステップ
の4つに分けた。
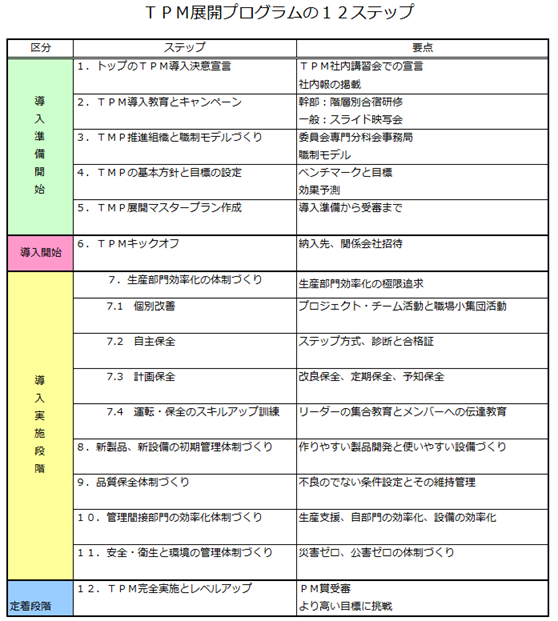
TPM展開プログラムの12ステップ
導入準備段階で十分に準備を整えたうえで導入開始,すなわちTPMのキックオフをするべきである。
事業場の大きさによって差はあるが,第1ステップの「トップのTPM導入決意宣言」から第5ステップまでの準備段階を終えるのに,一般に3~6ヵ月かかる。
TPMのキックオフをしたならば,ただちに導入実施段階に入る。そして,定着段階すなわち第12ステップ「TPM完全実施とレベルアップ」の段階にきてPM賞を受審する。
TPMのキックオフからPM賞受審までが,一般に2年半から3年かかる。従業員数の多い大規模な事業場では,3年以上から5年もかかるケースがある。
1983年に発表した「TPM展開プログラムの12ステップ」と,表1・8に示した12ステップの相違点は,導入実施段階である。前者は「生産部門のTPM」であるのに対して,後者は「全社展開のTPM」に対応して,ステップ展開したものである。
生産部門のTPMにおける導入実施段階では,
① 設備効率化の個別改善
② 自主保全体制づくり
③ 保全部門の計画保全体制づくり
④ 運転・保全のスキルアップ訓練
⑤ 設備初期管理体制づくり
5項目を, TPM展開の5本柱と称して実施してきた。
新ステップでは,全社展開のTPMに対応して,生産部門におけるTPM展開の5本柱を若干手直しするとともに,さらに3本の柱を加えて8本柱とすることにした。
まず,生産部門のTPM展開5本柱のうちのはじめの4本をまとめて,『生産部門効率化の体制づくり』とした。
そして,5本目の柱を設備だけでなく製品開発にまでさかのぼって,「新製 ・新設備の初期管理体制づくり」とした。
新たに加えた3本の柱とは,
⑥品質保全体制づくり
⑦管理間接部門の効率化体制づくり
⑧安全・衛生と環境の管理体制づくり
3つであり、下記のように構成された。
TPM展開8本柱
最終的にTPM活動は、大きく分けて下記のように8つの柱で構成される。
① 設備効率化の個別改善
② 自主保全体制づくり
③ 保全部門の計画保全体制づくり
④ 運転・保全のスキルアップ訓練
⑤ 設備初期管理体制づくり
⑥品質保全体制づくり
⑦管理間接部門の効率化体制づくり
⓼安全・衛生と環境の管理体制づくり
現在,すでにTPM展開中の事業場では,上述した8本柱を実施しているケースがほとんどである。
しかしながら,第1類・第2類のPM賞受審段階では,生産部門効率化の体制づくりにウエイトが置かれている。それでも十分に受賞レベルの有形効果を上げ゙ていれば表彰されるので,生産部門効率化の体制づくり以外の柱の中には,受賞後の課題となるものがある。
幸い,PM賞を受審することによって,全社展開の8本柱のうちさらに改善を必要とする弱点が,トップから第一線までの全員によく見えるようになる。そして,PM賞受賞までをパートI,受賞後のレベルアップと弱点改善で,文字どおり「全社展開のTPM」へのチャレンジをパートIIと称して,”特別賞”を目指す企業が多くなってきた。

TPM展開8本柱
TPM導入の準備体制から定着段階までの概要
TPMの驚異的な成果が知られるようになるとともに, TPMのキックオフを急ぐ企業があるが,あまりあわてて始めないでほしい。
キックオフというのは,サッカーやラグビーの試合開始と同じで, TPMの実際の活動を開始することをいう。すなわちキックオフは,”設備効率化の個別改善”や”オペレーターの自主保全”の活動を実行に移すことを意味する。
個別改善や自主保全を,誰が何を担当してどのように進めるのかもわからずにキックオフすると,ちょうどルールも知らず,練習もせずにサッカーやラグビーのキックオフをするようなもので,試合の行いようがない。
TPM導入の準備体制づくりとは,キックオフするまでに全従業員が, TPMとは何か,そしてゴール(目標)や進め方についても十分理解し,キックオフと同時に全員がTPM活動を実施できるようにすることである。以下, TPM導入準備段階の5つのステップについて,その要点を述べる。
ステップ1:トップのTPM導入決意宣言
TPMの成否は,トップの決意と熱意次第である。全社のトップは社長,事業場のトップは所長や工場長であることはいうまでもない。
トップみずから他社のPM賞受賞事業場のトップの話を聞き現場を見て,TPMの効果を確かめたうえでTPM導入の決意をしてほしい。 TPMの実施には人手もかかるし,費用もかかる。しかし,かけた費用の3~10倍の効果(コストダウン)が得られるのであるから,人手と費用をかけてもTPMを実施しようと腹を決めるのが,導入決意の意味である。自分で決めておいて,実行段階で熱意をもたないトップはいないはずである。
そして,導人決意宣言というのは,幹部や従業員の集まりの席上で,トップみずからTPM導入を決意したことを宣言する。また,社内報にトップの決意宣言を掲載する。
ステップ2 : TPMの導入教育とキャンペーン
TPM導入教育のために,階層別のTPMカレッジ・コースが設けられている
TPMカレッジ・コースには,
(1) TPM経営幹部コース
(2) TPM管理者コース
(3) TPMインストラクター養成コース
(4) TPM現場リーダー養成コースの4つがある。
この4コースは,いずれも社内コースと公開コースとがある。
TPMインストラクター養成コースは,TPM管理者コースの終了者が参加資格を持ち,このコース終了者は, JIPMからTPMカレッジ・コースの社内インストラクククーの資格を与えられる。
TPM導入のキャンペーンには,横断幕やたれ幕,立看板,ポスター・標語などが使われる。
ステップ3:TPM推進組織と職制モデルづくり
TPMは重複小集団組織で推進していく。図1・3は,重複小集団組織のモデルを示したものである。
また,全社TPM推進委員会や,部門別・工場別推進委員会の事務局を設ける,この事務局は TPM推進室またはTPM事務局と呼ばれることが多い。
事務局には専任担当者を置いてほしい。
さらに,必要に応じてTPMの主要な活動,たとえば8本柱のそれぞれにワーキング・グループを設ける。このワーキング・グループは,専門分科会あるいは部会と呼ばれている。図1・4は, TPM推進組織の例である。
組織づくりができたならば,工場長,部課長,スタッフ,役付者が一緒になってモデル設備を選んで,自主保全・個別改善をみずから行い,設備をあるべき姿にしてロスゼロの成果を上げてみせる。これを職制モデルづくりと呼んでいる。
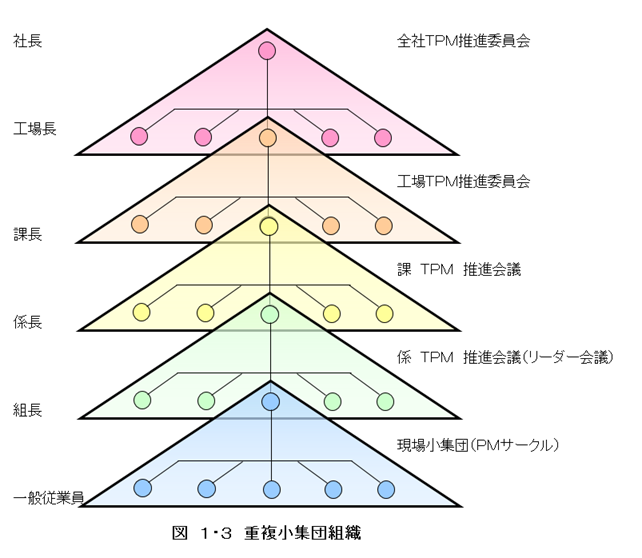
TPM推進組織と職制モデルづくり
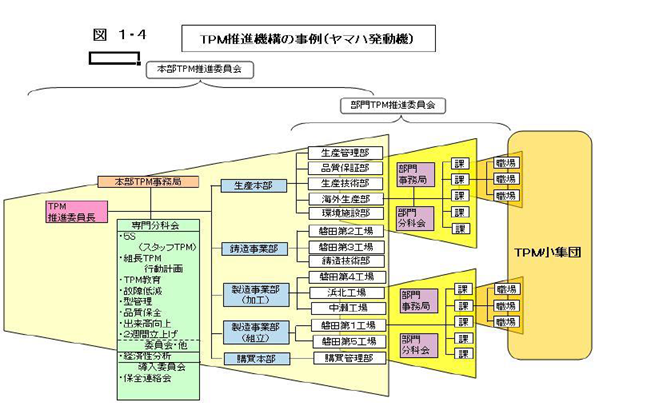
TPM推進組織と職制モデルづくりの具体的事例
ステップ4:TPMの基本方針と目標の設定
TPMは,それを実施することが目標ではない。企業のニーズ,方針,目標を達成するための手段として,TPMを実施するのである。 TPMの基本方針や目標の設置に際しては,このことを十分念頭におくべきである。
逆に,企業の方針や目標を設定するときには,その達成の手段としてTPMを実施することを明文化し,企業活動におけるTPMの位置づけを明らかにするべきである。
目標設定にあたっては,まずPM賞を何年度に受審するかを決め,その時点までに達成すべき目標項目ごとの目標値を決める。目標値は,故障半減,工程不良半減などの中途半端な値ではなく,PM賞受賞事業場の効果事例を参考にして突発故障件数1/100以下,工程不良 /10以下など,思い切った極限追求を目指すものにしていただきたい。
設備総合効率,故障件数,チョコ停回数などの現状のデータがとられていない場合には,最少限3ヵ月間のデータをとり,これをベンチマークにして目標設定をするとよい。図 1・5 は, TPMの基本方針と目標の設定事例である。
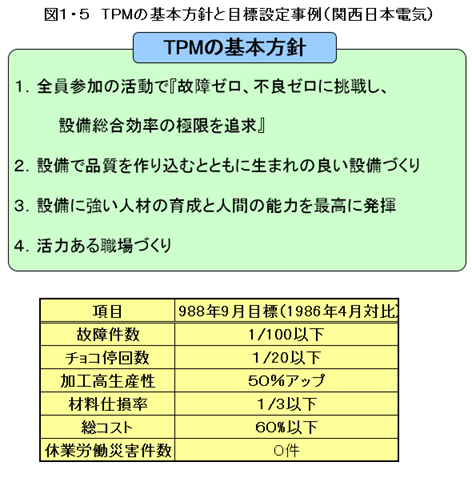
TPMの基本方針と目標の設定
ステップ5:TPM展開のマスタープランの作成
TPMの導入準備段階から定着段階にいたり,PM賞の受審をするまでの日程計画を「TPM展開のマスタープラン」と呼んでいる, TPMの主要な活動ごと,たとえば8本柱のそれぞれの活動について,さらに細目をあげ,着手と完了の時期を示す。
また,自主保全のステップについては,ステップごとの着手・完了予定を示す。
図1・6は, TPM展開マスタープランの事例である。
最近はモデル先行方式と称して,前述のとおり個別改善と自主保全のためのモデルの設備または生産ラインを選び, TPM導入準備期間中にこれらのモデルについて個別改善と自主保全を行い TPMをやれば効果が出ることをモデルで示す方法が採用されるようになった。
そして,モデルによる効果例はキックオフ大会で発表されるが,このようなモデル先行方式をとると,トップをはじめ全従業員がキックオフの時点で,TPMの効果に確信をもって取り組むことができる,
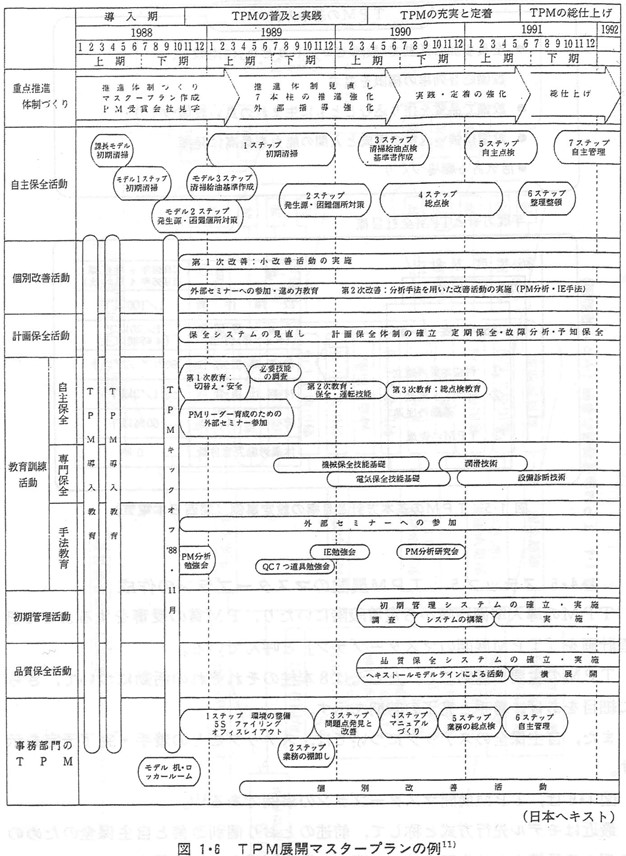
TPM展開のマスタープランの作成
画像出典先:TPM展開プログラム,組立加工編
ステップ6 : TPMのキックオフ(導入開始)
導入準備段階ではトッブ層,ミドル層か中心になって準備体制づくりを行い,一般従業員は導入教育を受けたり,モデルによる個別改善や自主保全を見聞する程度である。
導入開始すなわちキックオフの日は,いよいよ全員参加でTPMを開始する記念すべき日なのである。体育館や食堂などの広い会場に,できるだけ多くの従業員が集まり,「TPMキックオフ大会」あるいは「TPMキックオフ式」称する盛大なイベントが催される。
当日のブログラムの例をあげると,次のとおりである。
(1)トップの挨拶(TPM導入決意をあらためて宣言)
(2) TPM推進組織, TPMの基本方針と目標,TPMのマスタープランの発表(TPM推進委員長またはTPM推進室長)
(3)組合委員長または従業員代表によるTPM活動開始の決意宣言
(4)来賓祝辞
(5)準備期間中の職制モデルによる個別改善・自主保全の成果発表
(6)ポスター・標語・作文などの入選作品の表彰
ステップ7:生産部門効率化の体制づくり
まず,現在使用中の設備の総合効率を極限まで高める活動から開始する。この活動を次の4つに分ける。
ステップ7・1 :個別改善
生産システム効率化の個別改善は,職制のプロジェクトチームによる活動と,職場小集団による活動とがある。
まず,職制のブロジェクトチームによる活動から始める。管理者,監督者,スタッフがモデル設備で故障ゼロ,チョコ停ゼロ,不良ゼロなどの改善をして手本を示す。職場小集団は,当面は自主保全活動に全力投球し,設備総合効率が向上して余裕が出始めてがら個別改善に取り組む。
ステップ7・2 :自主保全
オペレーターの自主保全はステッブ方式がよい,ステップの事例として,①初期清掃(清掃・点検),②発生源・困難個所対策,③自主保全仮基準の作成,④総点検,⑤自主点検,⑥標準化,⑦自主管理の徹底—-の7ステップが普及 している。
これらのステップは機械加工向きであり,組立工程や職種・工程に合わせて工夫されている。
各ステップごとに不具合個所を発見してエフ(絵符)をつけ,その対策が終わるとエフを取る方法が普及しており,これを”エフづけ・エフ取り作戦“と呼んでいる。
また,各ステッブごとに管理者・スタッフが診断員となって合否を判定し,合格すると魅力的な合格証を職場小集団に交付し,次のステップに進む。このステップごとの達成感が,やる気を高める。
自主保全活動のために,活動板,ワンポイント・レッスン,ミーティング場などが使われる。
ステップ7・3 :計画保全
専門保全の行う計画保全が,オペレーターの自主保全と一体となってロスを排除し,効率を高める。
キックオフ当初は自主保全の支援,とくにエフ取りや発生源・困難個所対策で多忙をきわめるが,まずは設備の強制劣化を排除し,寿命のバラツキをなくすことが先決である。
次いで,設備の設計上の弱点対策(改良保全)を行い, MTBF(平均故障間隔)を延長し,それからTBM(Time Based Maintenance) つまり定期保全の体制を見直す。
そのうえで,設備診断技術を活用した予知保全。つまりCBM (Condition Based Maintenance)へと進む。このほか,予備品管理,図面管理,工具管理,保全費管理など保全作業の効率化を進め,さらに保全管理や診断の自動化,コンピュータ化を行う。
ステップ7・4 :運転・保全のスキルアップ訓練
前述した個別改善,自主保全,計画保全を支えるものが運転・保全の技術・技能である。運転ミス,修理ミスをなくし,設備に強い人づくりをするため,技能研修所を設けて継続的にスキルアップを図る。 国家資格の取得,とくに機械保全技能士の資格取得を奨励してほしい。
ステップ8:新製品・新設備の初期管理体制づくり
現存設備に対する個別改善,自主保全,計画保全などの活動から出てきた設備改善,作業改善,発生源・困難個所対策,改良保全などのさまざまな改善情報を新製品・新設備の開発段階にフィードバックして,作りやすい製品開発,使いやすい設備づくりをする。
ステップ9:品質保全体制づくり
不良の出ない設備の条件を設定し,その条件を維持管理することによって,不良をゼロにすることを”品質保全”と呼んでいる。
たとえば,円筒研削盤でワークの真円度が規格外れになる場合,規格外れの出ない設備の条件を振動値の大きさで設定し,その振動値の傾向管理をするここにより規格外れ,すなわち不良ゼロが続けられる。 ワークの品質特性を測定,管理するよりも,その品質特性を生み出す原因系の設備の条件設定と維持,すなわち品質保全こそ,これからの新しい品質保証のあり方である。
ステップ10 : 管理間接部門の効率化体制づくり
開発部門,営業部門,管理部門などのTPM活動は,生産効率化の支援活動,自部門の効率化,所管設備の効率化の3つに分けられる。
営業の受注の仕方,資材の発注の仕方などが,生産効率を大きく左右することはいうまで’もない。 自部門の効率化では,生産部門と歩調を合わせて,たとえば自主保全,個別保全で書類の整理,スペース創出,OA化による省人などが行われている。
設備とは,有形固定資産の総称であり,土地・建物・構築物・機械および装置・車両運搬具・船舶、工具・器具・備品で,固定資産に計上されるものがすべて設備である。管理間接部門で所管する設備の効率化をしてほしい。
ステップ11 :安全・衛生と環境の管理体制づくり
TPMでは,3K(汚い,きつい,危険)を追放し,クリーンで明るい,安全な職場づくりを目指している。 災害ゼロ,公害ゼロはPM賞受賞の絶対条件としている。オペレーターが自主保全をするために災害が起きるなどといわれないように,安全第一を厳守してほしい。
幸い,運転・保全のスキルアップ訓練により”設備に強い人づくり”ができ,設備の構造・機能に習熟することにより災害ゼロが達成されている。 このステッブでは,安全・衛生と環境の管理を設備の切り口から見直しをしてほしい。
ステップ12 : TPM完全実施とレベルアップ(定着段階)
導入実施段階で”人と設備の体質改善による企業の体質改善”が実現するが,TPMの目標とする”生産システム効率化の極限追求”が終わったわけではない。極限追求の企業体質を維持し,さらにより高い目標に挑戦していこうというのが,このステップである。
この段階に到達してPM賞を受審するが,最近では,受賞した事業場が,さらにより高い目標に挑戦するための活動をパートIIと称し, TPM活動を続けるケースが多くなった。第2類から第1類へ,第1類から特別賞へとチャレンジし,それによって企業体質はいっそう改善強化されていく。
TPM活動の効果と成果
TPM活動は、企業の生産性向上や品質改善に多大な貢献を果たします。具体的にどのような効果や成果が期待できるのか、詳しく見ていきましょう。
TPM活動による効果
- 生産性の向上
- 設備の故障やトラブルが減少し、生産ラインの稼働率が向上します。
- 計画的な保全により、生産計画の安定化が図られ、納期遅延の減少につながります。
- 品質の向上
- 設備の異常を早期に発見し、不良品発生を防止できます。
- 製品品質の安定化により、顧客満足度が向上し、リピートにつながります。
- コストの削減
- 設備の故障による修理費、不良品発生による廃棄コスト、再作業コストなどが削減されます。
- エネルギー消費量の削減にもつながり、環境負荷の軽減にも貢献します。
- 安全な作業環境の確保
- 設備の安全な運用を確保することで、労働災害を防止し、安全な職場環境を実現します。
- 従業員のモチベーション向上
- 全員参加型の活動であるため、従業員のモチベーション向上に繋がり、企業全体の活性化を図ります。
- 企業イメージの向上
- 品質の高い製品を提供し、環境に配慮した企業として、企業イメージが向上します。
TPM活動の成果指標
TPM活動の効果を定量的に評価するために、様々な指標が用いられます。代表的な指標としては、以下のものが挙げられます。
- 設備総合効率(OEE): 設備の稼働率、性能率、品質率の3つの要素から算出される指標で、設備の有効活用度を示します。
- 故障件数: 設備の故障件数を減らすことで、生産性の向上を図ります。
- 不良品発生率: 不良品発生率を減らすことで、製品品質の向上を図ります。
- 修理コスト: 設備の修理に要するコストを削減することで、コスト削減効果を測ります。
- 従業員の満足度: アンケート調査などを通じて、従業員の満足度を測定します。
TPM活動の成功事例
TPM活動は、多くの企業で導入されており、様々な成功事例があります。例えば、
- 製造業: 設備の寿命を延ばし、生産性を大幅に向上させた。
- サービス業: 設備の故障によるサービスの中断を減らし、顧客満足度を向上させた。
など、業種を問わず、TPM活動は企業の競争力強化に貢献しています。
TPMの効果事例
TPMを導入してから,PM賞を受賞するまで3年以上はかかる。したがって,このような効果が出るまでには,やはり3年以上かかるということである。
まず,有形の効果であるが,生産システムのアウトプットとして生産性(P : Productivity),品質ぐQ : Quality),コスト(C : Cost),納期(D:Delivery),安全・衛生・環境(S : Safetyで代表させる),作業意欲(M:Morale)の6つを取り上げる。
そして, TPM導入時点をベンチマークとしてそれらがどんなに良くなったかをを相対的に評価してみると,表1・7に示すとおり,付加価値生産性1.5~2倍、工程不良率1/10,製造原価30%減,製品・仕掛り品在庫半減などのほか,災害ゼロ,公害ゼロ,改善提案件数5~10倍といった画期的な効果が出ている。
表1・7 TPMの効果事例
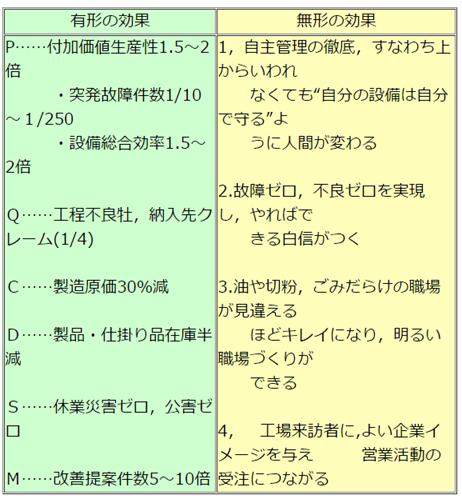
TPMの効果事例
TPM活動の課題と注意点
- 初期投資: TPM活動の導入には初期投資が必要となる場合があります。
- 全従業員の意識改革: 全員が活動に参加するためには、意識改革が不可欠です。
- 継続的な取り組み: TPM活動は一過性の活動ではなく、継続的な取り組みが必要です。
TPM 自主保全のメリットとデメリット
自主保全は、TPM活動の中核を担う重要な要素です。現場の従業員が主体的に設備の保全を行うことで、生産性の向上やコスト削減に大きく貢献します。しかし、一方でデメリットも存在します。
メリット
- 生産性の向上: 設備のトラブルが減少し、稼働率が向上することで、生産性が大幅に向上します。
- 品質の安定化: 設備の異常を早期に発見し、対応することで、製品の品質が安定します。
- コスト削減: 設備の寿命が延び、修理費用が削減されることで、コストが大幅に削減できます。
- 従業員のスキルアップ: 保全作業を通じて、従業員のスキルが向上し、多能工化が促進されます。
- 従業員のモチベーション向上: 自らで設備を管理し、改善することで、従業員の仕事への満足度やモチベーションが向上します。
- 迅速な対応: 現場で問題が発生した場合、すぐに対応できるため、復旧までの時間が短縮されます。
デメリット
- 作業ミスによるトラブル: 経験不足や知識不足により、作業ミスが発生し、かえって設備を損傷させる可能性があります。
- 時間的な制約: 生産活動と並行して保全作業を行うため、時間が不足しがちです。
- 専門的な知識が必要: 複雑な設備の保全には、専門的な知識や技術が必要となります。
- 従業員の負担増: 保全作業が従業員の負担となり、モチベーション低下につながる可能性があります。
- 初期投資: 自主保全を始めるためには、工具や備品などの初期投資が必要となる場合があります。
デメリットを克服するために
自主保全のデメリットを克服するためには、以下の対策が有効です。
- 教育・研修の徹底: 従業員に対して、保全に関する知識や技術を徹底的に教育・研修します。
- 標準作業手順書の作成: 作業手順を明確にすることで、ミスを防止し、作業効率を向上させます。
- 定期的な点検・評価: 保全活動の効果を定期的に点検・評価し、改善点を明確にします。
- 専門家のサポート: 複雑な設備の保全については、専門家のサポートを受けることも検討します。
- 従業員の負担軽減: 保全作業の負担を軽減するために、作業の効率化を図ったり、人員配置を工夫したりします。
自主保全は、メリットとデメリットを理解し、適切な対策を行うことで、効果を発揮する活動です。
TPM 自主保全を成功させるためのポイント
- 経営層のコミットメント: 経営層が自主保全の重要性を認識し、積極的に支援することが不可欠です。
- 全従業員の参加: 全員が主体的に活動に参加できるような雰囲気作りが重要です。
- スモールスタート: 全ての設備を対象とするのではなく、一部の設備から始めて徐々に範囲を広げていくことが効果的です。
- 目標設定: 定量的な目標を設定し、達成状況を定期的に評価することで、モチベーションを維持します。
TPM活動による生産性向上実績について
TPM活動(Total Productive Maintenance)は、企業の生産性を向上させるための非常に効果的な手法として広く知られています。多くの企業がTPM活動に取り組むことで、目覚ましい成果を上げています。
TPM活動による具体的な生産性向上効果
TPM活動によって得られる生産性向上効果は多岐にわたりますが、代表的なものとして以下が挙げられます。
- 設備稼働率の向上:
- 故障やトラブルの減少により、設備が長時間稼働できるようになり、生産性が向上します。
- 不良品率の低下:
- 品質管理の徹底により、不良品が減少し、製品の品質が向上します。これにより、再加工や廃棄によるロスが削減され、生産性が向上します。
- 生産リードタイムの短縮:
- 生産工程の改善やムダの削減により、製品の製造期間が短縮され、顧客への納期が早まります。
- コスト削減:
- 設備の寿命延長、エネルギー消費量の削減、不良品による損失の減少など、様々な要因によりコストが削減されます。
- 従業員のモチベーション向上:
- 従業員が主体的に活動に参加し、改善に貢献することで、仕事への満足度やモチベーションが向上します。
TPM活動の成功事例
数多くの企業がTPM活動に取り組んでいますが、特に顕著な成果を上げている企業の事例としては、以下のようなものが挙げられます。
- 自動車メーカー: 生産ラインの自動化、不良品率の低減、生産リードタイムの短縮など、多岐にわたる改善を実現し、世界的な競争力を獲得しています。
- 電機メーカー: 高度な技術を要する製品の製造において、TPM活動を通じて品質の安定化と生産性の向上を両立させています。
- 食品メーカー: 食品衛生の確保と同時に、生産効率の向上を実現し、高品質な製品を安定的に供給しています。
TPM活動の課題と今後の展望
TPM活動は、多くのメリットをもたらしますが、同時に課題も存在します。例えば、従業員の負担増、専門知識の不足、時間的な制約などが挙げられます。これらの課題を克服するためには、ITツールの活用や外部専門家の支援など、様々な工夫が必要となります。
今後、TPM活動は、IoTやAIなどの新たな技術との融合が進み、より高度化していくことが期待されます。また、サプライチェーン全体でのTPM活動の展開も注目されています。
TPM活動の課題
- 人材育成の難しさ:
- 全員参加型の活動であるため、多様なバックグラウンドを持つ従業員に対して、必要な知識やスキルを習得させることが容易ではありません。
- 熟練者の退職に伴い、ノウハウの継承が困難になるケースも少なくありません。
- 変化への対応:
- 技術革新や市場の変化が激しい現代において、TPM活動も柔軟に対応していく必要があります。
- 新しい技術や設備の導入にともない、既存の活動を見直し、新たな取り組みを始めることが求められます。
- 従業員のモチベーション維持:
- 長期にわたってTPM活動を継続するためには、従業員のモチベーションを維持することが重要です。
- 成果がなかなか見えない場合や、業務が忙しく、TPM活動に十分な時間が割けない場合など、モチベーションが低下する要因は様々です。
- デジタル化への対応:
- IoTやAIなどのデジタル技術の進展により、TPM活動もデジタル化が求められています。
- しかし、全ての企業がデジタル化に対応できるわけではなく、導入コストやスキル不足が課題となる場合があります。
TPM活動の今後の展望
- デジタル化による変革:
- IoTセンサーを活用した予知保全、AIによるデータ分析、AR/VRを用いた教育訓練など、デジタル技術を駆使することで、TPM活動の効率化と高度化が期待できます。
- 人材育成の強化:
- OJTだけでなく、eラーニングやシミュレーションを活用した多様な学習機会を提供することで、従業員のスキルアップを支援します。
- 若手社員の育成にも力を入れることで、人材の育成と継承を両立させます。
- 外部機関との連携による人材育成プログラムの導入も有効です。
- 組織文化の醸成:
- TPM活動は、単なる改善活動ではなく、企業文化の一部として根付かせることが重要です。
- トップのコミットメント、従業員の主体的な参加、部門間の連携を促進することで、持続可能なTPM活動を構築します。
- サプライチェーン全体の最適化:
- 自社だけでなく、サプライヤーや顧客も含めたサプライチェーン全体でTPM活動を展開することで、より大きな効果が期待できます。
- SDGsとの連携:
- 環境問題への関心の高まりを受け、TPM活動とSDGsを連携させることで、環境負荷の低減と生産性向上を両立させます。
まとめ
TPM活動(Total Productive Maintenance)は、企業の生産性向上に不可欠な活動です。多くの企業がTPM活動に取り組むことで、具体的な成果を上げています。TPM活動の成功には、経営層のコミットメント、従業員の意識改革、段階的な導入、効果測定などが重要です。
*次のTMP活動を進めるステップである『全社で進めるTPMを活用した生産効率の考え方【図解】』は下記を参照願いします。

関連キーワード:
自主保全 計画保全 初期管理 品質保全 改善 標準化
5S QC7つ道具 PDCAサイクル
ものづくりドットコムへの記事掲載
『TPM、総合生産的な保全とは』を2014年5月13日 ものづくりドットコムに記事を掲載しました。
無料でTPM活動の資料がダウンロード
Googleスライド TPM活動 無料ダウンロード
Googleスライドから無料でTPM活動の資料がダウンロードできます。
slideshare ダウンロード資料(PDF)
パワーポイントで作成した資料です。
引用文献:
今日からモノ知りシリーズ トコトンやさしいTPMの本
現場力を高める実践的TPM入門【改訂版】
わかる!使える!TPM入門 〈基礎知識〉〈段取り〉〈実践活動〉/日本プラントメンテナンス協会
コメント
[…] 概要: TPMとは(Total Productive Maintenance 総合 生産的な保全 ) すなわち小集団活動によりPMを推進することをいう。 全部門が協力して生産効率を上げる。 関連記事: TPM 設備保全の概要 | 機械保全 | TPMとは? […]