- 目で見る管理 【イラスト図解】
目で見る管理 【イラスト図解】
英語:visual management 中国語:目视管理
目で見る管理とは
管理・監督者が、生産活動の状態が正常か異常かを目で見て即時に判断できる現場管理の形態をいう。
誰が見てもひと目でわかる管理を目的とし、「管理の標準化」ともいい換えられる。計数による机上の管理はともすれば管理者だけがわかるものになりがちで、問題が潜在化し改革の糸口が見えにくい。
そこで生産活動における物の流し方、情報の流し方、作業のやり方、管理の仕方等すべてについて、正常と異常の状態区分を明確にし、問題が発生した場合”すぐに誰でも”認識できる、つまり問題を顕在化する仕組みを作る。これが「目で見る管理」で次のようなものがある。
①赤札
②看板
③白線表示
④赤ライン
⑤アンドン
⑥かんばん
⑦生産管理板
⑧標準作業票
⑨さらし首
⑩ミス防止板
わかりやすく 目で見る管理
見える化
現場で目にした状態が正しいのか、正しくないのか、説明を聞かなくても見た目でわかるようにすることである。
このままの状態で放置しておいてもよいのか?
何か問題はないのか? がわからず、現場が管理されてない状態では困るのである。
そのために、基準や標準をつくり、それを現場に表示して、基準や標準に従っているかそうでないか、わかるようにする。
たとえば、部品がシユーター上に置いてある。何の表示もされていなければ、その量で良いのか悪いのかが判断出来ない。そこで、シユーター上に部品の最小と最大を表示すれば、誰の目にも正常か異常かがわかる。
物を置く場所についてもこのことが言える。 5S活動で、物の置く場所を決め、区画をしておくと、その区問線の外やまったく異なる所に物が置いてある時に、それは異常だと、誰もが判断できるのである。
現場全体をこのように“見える化”すれば、誰でも正しいか正しくないかが判断でき、全員が正しい方法に持っていこうと努力する。
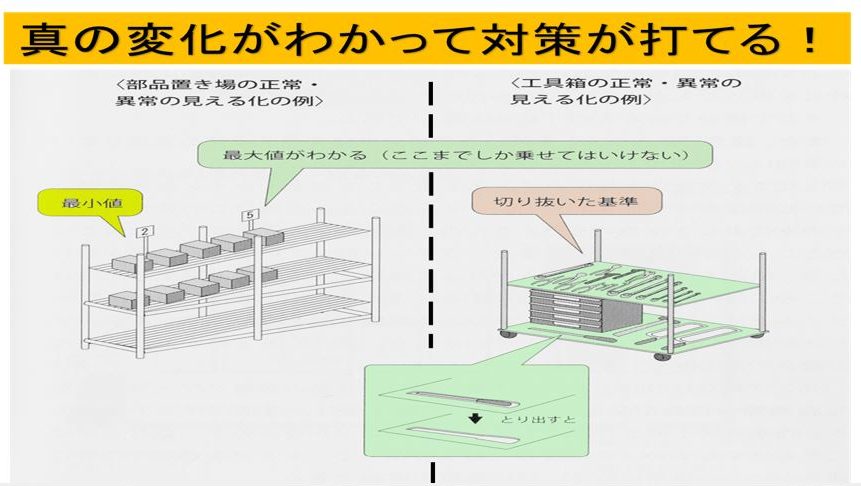
画像出典先:『すぐに使えるトヨタ生産方式 導入・実践ノウハウ集』(著者:竹内鉦造)
トヨタはさまざまな作業において、「目で見る管理」が工夫されています。目で見れば誰もが容易に状況が分かり、共通の認識ができるため、作業にムダやミスがなくなります。
ところで、トヨタでは問題が発生したら現地へ行き、問題の生じたモノを見て、問題発生状況をよく観察しなさいという思想、すなわち、三現主義が根づいています。
このことは、古くから言い伝えられている「百聞は一見にしかず」を実践のなかで企業体質として、つくりあげてきたものです。
しかし、三現主義が重要だと頭の中で分かっていても、体にしみこませるのは容易なことではあリません。現場で観察するには、現場でのモノの見方、考え方、体力、気力が必要になってきます。
実際に企業で問題が生じたとき、現場に出向き、問題発生状況を観察してもらうようなとき、問題解決の方向が見えない人は多いものです。現場でのモノの見方、考え方を話し、再度、現場観察に行つてもらおうとすると、デスクワークに逃げてしまう人も出てきます。
トヨタ生産方式の代名詞のように言われている「かんばん」も、簡単に運用できるものではあリません。
たとえば、特急品や割込み品があった場合、現在生産中のものとの関係はどうなるのか、きめの細かい対応が必要になってきます。ラインストップも問題を発見しやすくした例といえます。
下の表は、トヨタにおける目で見る管理の一例です。いずれの場合も、目的を明確にして企業体質に合つたものを導人していかないとかえって混乱を生じるので注意が必要です。
No | 項目 | 具体例と説明 |
1 | 現場主義(三現主義) | 現地、現物、現実 |
2 | かんばんのバラツキ | 進捗状況の管理、適切なかんばんの活用 |
3 | 異常警報装置 | アンドン、ブザー、呼び出し灯 |
4 | 5S | 所番地管理、通路の区画線、危険マーク、治工具形合わせ板、目に訴えるための意識づけに有効 |
5 | 進捗状況 | 現場の何を見ると進捗状況が分かるのかを認識、各工程のかんばんと現物量、手持ちの状況、生産管理板、ガントチャート(日程計画表) |
6 | 生産管理板 | 進捗状況、生産計画と実績とその差異、品種、 特急品、割り込み品への対応状況、機械設備 の稼働状況 |
7 | 生産指標 | 生産高、歩留り、生産性、稼働率、可動率、段取 り替え時間、不良率、良品率、不良件数、手直し 不良率、チョコ停 |
8 | 問題点とその対策 | カイゼン提案報告書(問題点、現状分析、原因の状況究明、カイゼン案)、現場の人たちの関心を高める、参加意識の向上に有効 |
9 | 標準作業の遅れ | 標準作業どおりに作業を進められなくなったと き、ベルトコンベヤ上に引いた線の間隔てモノ が来ないとき |
異常発生時の設備・ライン の自動停止 |
ポカヨヶ、検知器、タクトタィムオーバー時の ラィン自動停止、定位置停止 |
|
製品の識別 | 検査前、検査中、良品、不適合品(赤箱) | |
バラツキの吸収 | バラツキの吸収 | |
目で見る管理の代表例
「目で見る管理」とは、工程で発生した問題(異常と正常の差)を迅速に把握し、だれもが容易にカイゼンし、管理することです。主な方法を以下に説明します。
生産管理板
生産の状況が計画に対して進んでいるのか遅れているのか、目で見て分かるようにすることです。生産計画数量(生産時間帯の時間をタクトタイムで割ったもの)、生産実績との差異などで表示します。
アンドン
エ程でどのような異常が起きているかを管理・監督者に分かるよう知らせるものです。呼び出しアンドン、異常アンドン、稼動アンドン等があリます。
(下図参照)
定位置停止方式と即時停止方式
定位置停止方式とは、作業者が異常を感じたときに連絡し、ラインがいつも同じ位置で停止するようにしたものです。停止するまで時間があり、監督者の援助などで、ラインを止めなくてよい場合もあります。
即時停止方式とは、原則はできるだけ止めないようにするが、問題が発生したらすぐラインが止まるようにしたものです。
指定席と自由席
指定席とは、塗装工程などでハンガーなどに目印をつけ、ハンガーの指定箇所に製品をかけていく方法のことです。
自由席とは、生産にバラツキが発生し、バラツキを吸収するため、なにをかけてもよいようにしたものです。
目で見る管理の詳細は下記の関連記事に記載しています。
関連記事:目で見る管理
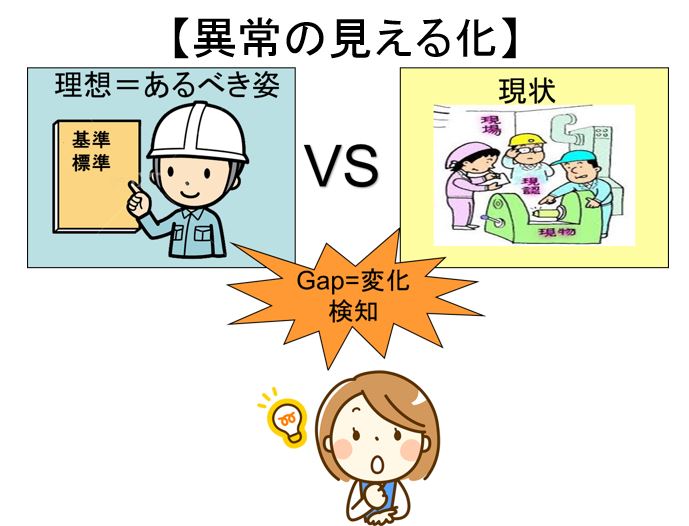