TOCとは(制約条件理論:Theory of Constraints)
制約理論は、英語のTheory of Constraintsを訳したものです。これは、「もの」とか「サービス」の生産を行うシステムを、現在、主流となっている伝統 的な生産理論とは異なった観点から見る考え方で、欧米、特にアメリカや英語 圏の国々の製造業で、1980年代後半から広く使われるようになり、生産現場で 大きな成果を挙げている理論です。
制約理論は、あまり難しい理屈なしに、忙しい現場の責任者、監督者が現場で日常的に行う意思決定が、企業の全体目標(制約理論では「お金を儲ける」こ と)への貢献に直結することを目的にしています。
ここで、おそらく、いまだって生産工学や原価計算をべ一スとした判断の拠りどころがあるではないかという反論が出てきそうです。おいおい述べていき ますが、あまりにも長い間使われ、現場の責任者や監督者、経理の原価計算担当者が、揺るぐことのない、しっかりした根拠のある判断基準であると考えて いたものが、実は、問違っているのです。
このような判断基準に基づき、企業の各部分で日常的に行われている意思決定が、企業全体としての業績評価尺度である純利益、ROI、キャッシュフローの改善や 向上につながらないどころか、かえって、その足を引っ張ってしまっているのです。
この理論はイスラエル人の物理学者、エリヤフ・M・ゴールドラット博士 が1970年代に開発した生産現場でのスケジューリングを行うソフトウェア Eliyahu M. Goldratt 「OPT:Optimized Prodution Technology」が原典です。
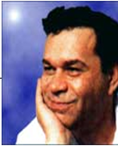
ゴールドラット博士
ゴールドラットは、1974年末に、このソフトウェアを親戚の依頼で開発し 設備や労力の追加なしに、生産を40-50%増加させることに成功しました。 まだ、ゴールドラットが学生だったころのことでした。
彼は中東戦争に参加した後、1978年に30歳で大学を卒業しその後、OPTの優れた点を認識していたCDC社の勧めで、Creative OutputInc.社を設立しました。アメリカでの最初のプロジェクトはGEの防衛システム事業部での仕事でしたが、そ こで彼は、スループットを30%増加させ、かつ、在庫を半減させることに成功しました。Creative OutputInc.社は高成長企業となりました。

The Goal
1984年、ゴールドラットは産業小説”The Goal”を出版し(1986年に改訂版を出版)、OPTの考え方を同書の中で明らかにしました。
この本は、中国語を含む十数ヵ国語に翻訳され、世界で200万部も売れたとい われているベストセラーになりました。
“The Goal”は、アレックス・ロゴという主人公が、白分の管下にある工場 の成績が改善されない限り、3ヵ月後には閉鎖すると予告され、奮闘する「産業 小説」です。アレックスは、ヨナというイスラエル人の物理学者の指導の下に、 5段階継続的改善プロセス、スループット、在庫、業務費用などのTOC概念を 学び、現場に適用することで、たった3ヵ月で業績を改善するというストーリー です。
ここで、強調しておきたいことがあります。それは、小説”The Goal”の主 人公アレックスが、白分の工場の業績を、たった、3ヵ月で改善し、工場の閉鎖 を免れたということです。
この本はたくさん売れましたが、ここでゴールドラットにとってショッキン グな問題が発生しました。この本を、たったの15ドルで買った企業が小説の中 の考え方を実行したところ、彼の高価なソフトウェァを購人して導入し、社員 を教育した企業よりも、よい成果を挙げてしまったのです。この本を買って、そこに述べられている考え方を実行した多くの企業で同様なことが起こりました。
つまり、制約理論は、あまり難しく考えず、その基本的な原理を理解し、 トップの支持の下で、要点を押えて展開して、生産システムの中に存在する制約資源を明確に意識し、それを徹底的に使うことを試行錯誤的に行うことから 開始できることを意味していると思います。
この時点で、彼は、現場のスケジューリングのコンピュータ・システムよりも、方針、業績測定、原価計算、経営風土、思考プロセスなどがより重要であるとはっきり認識し、生産組織運営の一般理論の展開に注力するため、1987 年、成長を続けていたCreative OutputInc.社を去り、アブラハムY.ゴール ドラット・インスティテュート(AGI)を設立しました。そこでの彼は、思考プロセスと教育に関心を移し、それ以降、今日、制約理論と呼ばれるものの開発に努め、一つのフレームワークとしてまとめることに注力しました。あとで説 明するように、制約理論は、ロジステイックス、業績システム、問題解決/思考 プロセスの三つの領域をカバーします。
Theory of Constraints=制約条件理論
鎖全体の強度は最も弱い輪(ボトルネック)の強度に等しい。
・ボトルネック(制約条件)の発見
・ボトルネックの最大活用
・スループットの極大化
・キャシュフォローの極大化
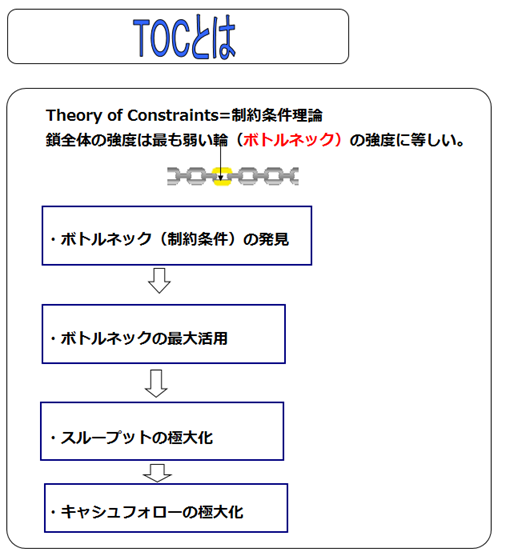
TOCとは
TOCと従来の考え方との根木的違い
(ボトルネックの最大活用)
■∑個別最適化≠全体最適
生産性向上に関しては、従来から多くの理論が存在したが、TOCがそれらの理論と根本的 に違う点は、ポトルネックの最大活用を通じて、全体最適をもたらすという考えだ。
従来の考え方では、個別最適の集積が全体最適をもたらす、つまり、 「Σ個別最適(個別最適の集積)=全体最適 という考え方にもとづいていた。個別のプロセスをそれぞれ最適化し、それぞれが アウトプットの最大化をはかれば、全体での最適化が生まれるという考え方だ。
しかし、TOCでは個別最適の集積が必ずしも全体最適にはならないと考える 。
∑個別最適化≠全体最適
むしろ、ボトルネック以外のプロセスの能力を極大化させない場合のほうが在 庫の減少などを通じてキャッシュフローが増加する場合もある。
つまり、ボトルネック以外のプロセスの極大化は「ムダな」中間のアウトプットを増大させ、在庫の増加やムダな働きをするだけで、全体としてのスループットの増加に寄与せず むしろ、キャッシュフローの減少をもたらすと考える。
そして、ボトルネックの最適化(最大活用)だけに焦点をあて、そのことだけに着目することが全体最適をもたらすという考え方をしている。
■ボトルネック以外のプロセスの動き
ボトルネック以外のプロセスはボトルネックに従属させる、つまり、ボトルネックの動きにそれ以外のプロセスを同調させることがスループット極大化、キャシュフォロー極大化に繋がると考える。
(”ドラム・バッファー・ロープ”という考え方)
この考え方は、例え話だが、あたかも①ボトルネックにドラム(太鼓)を打たせてそのリズムを他のプ ロセスに知らせ、②ポトルネックの動きが止まらないようにその直前プロセスでは少しバッファー
(余裕)を持たせ、さらに、③最先端のプロセスが勝手に先走らないように、そのプロセスとポトルネックとをロープでつなげることによりスピードを維持しようとする。それぞれが全力を出す のではなく、あくまでもポトルネックを最大活用することが全体最適をもたらすと考える。
従来の生産管理
個別最適の集合 = 全体の最適
個々が最適化するように独立して行動
結果:個々の努力の成果があまり全体に結びつかない
TOC
ボトルネックの最大活用 =全体の最適
によるスループットの極大化
ボトルネック以外はボトルネックに従属
“ドラム・バッファー・ロープ”
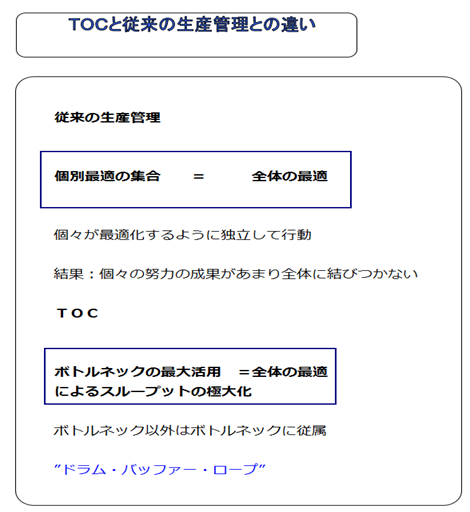
TOCと従来の考え方
『スループットの定義』
Through put =一定時間に処理する仕事量
TOCでは、売上高の構成を、図にあるように、利益、経費、資材費の三つに分解して考える。
そのうち、スループットとは、利益と経費を足したものを指す。
言い方を変えると、売上高から資材費を引いたものだ。
資材費は、原材料費などの変動費を表している。つまり、売上高の中から変動費である資材 費などを差し引いたものがスループットということである。
ここでいう経費は固定費的要素が強いものを指す。短期的には生産量の増減にかかわらずかかるものをいう。
したがって、スループットは、売上高の中から、変動費部分を除いたもので、経費が大きけれ ば損失が、経費がスループットよりも小さければ利益が発生する。
TOCでは、個別原価計算を行わない。企業にとって全体としてのスループット向上が重要 だからだ。固定費や間接費を一単位あたりの製品に、あるロジックで配分、賦課することは、 いかにも論理的であるように思えるが、結果として全体のスループットやキャッシュフローが 増大しなければ意昧がない。
企業は「現在から将来にわたって設け続けること」が必要だということをTOCは強調する個別あたりの利益は出ていててもこれまでの生産量をべースにした個別原価を用いるため、 生産量が従来より急減する場合には全体としての利益は出ていないことがある。また、在庫は資産計上されるため、それが販売されるまではコストとはならないが、実際には多額のキャッ シュフローがその在庫に注ぎこまれ、販売されてやっとキャッシュが戻ってくる。そのような 矛盾を解決するために、個別原価計算をしないスループットという考え方をTOCでは用いて いるのである。あくまでも全体最適を目的とするのだ。
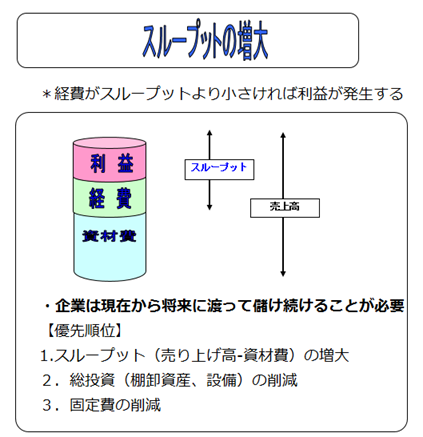
スループットの増大
従来の考え方では利益を上げる為、には原価を低く抑えることが重要になってきます。
原価の内訳は資材費、外注加工費、直接人件費、設備への投資など製品を作る際に直接的にかかった費用すべてを含んでいますので購買部門は資材費をいかに安く抑えるか、製造部門はいかに設備の稼働率を上げるか、生産性をいかに向上させる かを目標として活動します。
しかし、これらの目標を達成すればするほど、不要な在庫は増大し、リードタイムを 長期化させる大きな原因のひとつとなっています。
スループットの特徴は、 “配賦”を行わないことです。この”配賦”は企業に よって定められた配賦基準に従って計算されます。現実には一個の製品を作るのに かかった費用は求められるものではありませんが、複雑な計算式を用いて様々な 費用を一個あたりの原価として計上しています。そこでスループットでは配賦が 必要とされるような人件費、減価償却費などは業務費用として個別の原価には配賦せず、 利益を計算する際に一括して差し引くことになります。つまり一個あたりの原価 を求めないのです。TOCスループット指標を使うことで、スループット増大という目的が 明らかになり素早く、正しい意思決定を行うことが可能になります。
ただし、個別の製品の定価の設定や、財務諸表作成では従来の原価計算を継続しなければ いけないことも事実です。実際に企業内で利用していく場合にはこのTOCスループットと 財務会計における情報の整合性や手間を少なくするためのシステム構築も必要となってきます。
ボトルネックとは
3種類のボトルネック(bottle neck)
ボトルネックとは、ある事象が制約条件となりその事象を含むプロセス全体の生産性を 落としている事象をいう。ボトルネックが解消されれば、全体の生産性(スループット)が向上する。
TOCではボトルネック(制約条件)を3種類考える。「物理的制約」、「方針制約」、「市場制約」だ。
①物理的制約とは、製造工程などにおいて、ある工程の処理能力が低いため、システム全 体が生み出すスループットが制限されている工程をいう。
その工程の能力が向上すれば、全体のスループット量が増える。これは、製造工程だけでなく、事務処理などの業務についても当てはまることで、物理的制約(能力的制約)を
取り除くことにより、スループットの向上を図ることができる。
②方針制約とは、経営方針がボトルネックとなっていることを指す。具体的には組織や評 価制度などに問題がある結果、全体のスループットが制約を受けているような状態を指す。
③市場制約とは、物理的制約や方針制約とは違い、自社の生産能力(スループット能力) が市場の需要を上回っている状態をいう。この場合には、需要を喚起するマーケティン グ戦略などの変更が必要となる。物理的制約や方針制約がある場合には、市場の需要が あるにもかかわらず、それにたいして十分なスループットが出せない状態にある。
それに対し市場制約がある場合には自社製品の市場での需要が足りない状況であり、 それへの対応策として価格対策などを考えることとなる。
この場合にはTOC独自の考え方である固定費を考慮しない価格政策ことや「思考プロセス」を用いて新たなマーケテング戦略を考えることとなる。
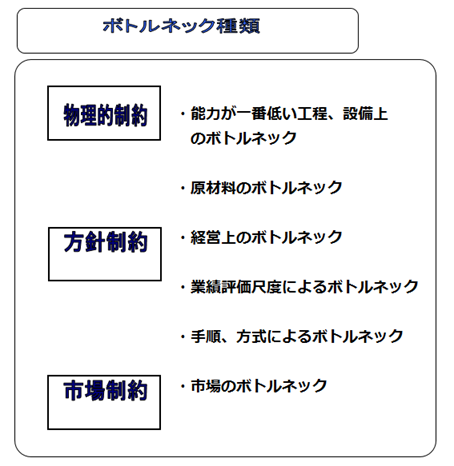
ボトルネックの種類
物理的制約
キャパシティ制約
下図は、単純な例だが生産資源(設備、人的資源)による物理制約の例である。
プロセス1からプロセス2、プロセス3を経て製品が完成する
それぞれのプロセスの下に1時間あたりの処理能力を示した。プロセス1では10個、 2では7個、3では15個だ。この場合、プロセス1で1時間あたり10個処理された中間製品は、プロセス2に持ちこまれるが、ここでは時間あたり7個の処理しかできない。そうなると、せっかく、プロセス1でそれ以上の処理(10個)ができていても、プロセス2がフル回転の状 態で、時間あたり3個の積み残しが出てくることとなる。
もし、プロセス1もフル回転で操業すれば、時間あたり3個の在庫を増加させつづけることとなる。 一方、プロセス3では、時間あたり15個の処理能力がありながら、プロセス2で7個の 製品しかアウトプットされないために、処理能力が時間あたり8個分余っている状態となる。
したがって、この製造工程全体の処理能力は、プロセス2の生産能力である時間あたり7個と いうことになる。つまり、プロセス2がポトルネック(物理的制約)である。 ここで重要なことは、上では単純な例を用いたが、工程全体が複雑になっても工程全体の生 産性はポトルネックの生産能力によって決められてしまうということだ。
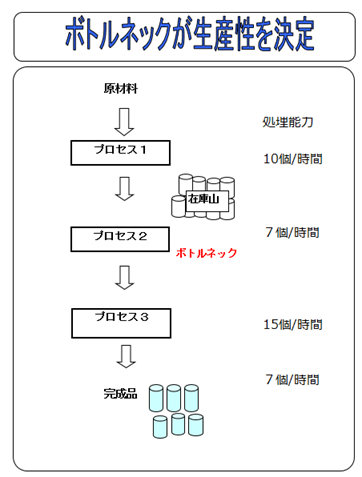
キャパシティ制約
原材料制約
JITシステムの最大の弱点である突発事後が発生した際の生じる原料不足による 原材料制約のことである。
方針制約
制約理論では、方針とは、ものの見方、業績評価尺度、方式(手順、各種の方式やテクニック)からなり、これらはすべて、スルー プットの増大を阻止してしまう制約となりうるものと考えます。広く組織風土 と呼ばれるものも、これに含まれるように思われます。「方針」は、経営の基礎
となるもので、本来、制約になってよいものではありませんが、現実には、多 くの会社で制約になっている場合があるのではないでしょうか。方針の制約の 特徴は、場合によっては、それが方針の制約とは異なる現れ方をすることのよ うです。スケジューリングの仕方や、段取に関する方針により、本来、利用可 能な資源キャパシティが使われなくなり、それが物理的な制約に見えたり、強い残業規制により人的資源が制約に見えたりすることです。このあたりの問題 の「真の原因」を突き止めるのに問題解決/患考プロセス分枝の技法が使われます。
ものの見方による制約
企業には、いわゆる企業それぞれの組織風土があります。ある企業は、そのよし悪しは別として、新しもの好きですぐに飛びつき、従来の方式を変えてい こうという傾向があり、ある企業は保守的であり、変化を好まなかったりします。また、新しい、本当に役に立つものが出てきても、問題意識がないので、 それにまったく関心を示さず、いままでの方式を踏襲するだけの企業もあるか もしれません。
企業の中のものの見方とか風土が、企業目標の達成に必要な方 針を決定し、その実行をモニターして評価する尺度を確立することを妨げ、スループットの増大を阻んでいるとすると、これらは制約です。この種類の制約 の例は、例えば、組織風土の一部として、管理者の頭の中に、どんなことが あっても(例えば、スループットが減っても)残業予算を守ろうとか、監督者や作業員が、機械は常時稼動すべきであるという価値観を持っていて、高い稼働率を誇りに思い、それが落ちると不安に感ずるとか、また、販売員が、売れば スループットを減らしてしまう製品でも、その販売数量が高い伸び率を示さな いと落ち着かなくなるというのは、ものの考え方の制約といえるでしょう。
業界評価尺度による制約
部門や個人の業績を評価する尺度自体も、企業目標の達成に不適当な行動を 提起したり、目標達成に不可欠な行動を妨げるとすれば、それらは制約です。
特定の設備の業績を評価するのに、前後の工程の作業に関わりなく、部分業績 尺度であるその設備だけの設備稼働率や直接労働の作業能率だけで、その設備 の責任者の業績を評価するなどはこの例です。
2-3:方式(手順や利用する各種の方式やテクニック)による制約
方式による制約には、日常的に各職場で行われている手順(業務プロセス)、 EOQのようなテクニックがスループットの増大を阻止しているなら、これらは 制約です。例えば、受注から、与信調査をして・販売を許可し、生産オーダーを出して生産し、倉庫に入れたものからピッキングして梱包し、輸送手段を手配して出荷するという、一連の業務プロセスで、実は制約が与信調査にあっ たというようなことも起こりえます。巡回セールスの販売員が注文を販売部に伝達する方式も制約になりえます。生産現場では・バッチサイズの決め方、 オーダーのまとめ方、生産の優先順位づけ方式も、リードタイム・納期遵守度 に影響するので、制約になるかもしれません。
市場制約
ここでいう市場の制約は・普通に考えるよりも意味を広くとります。通常、 市場が制約であるという場合、ある製品やサービスの市場が、その製品を生産 している企業群の生産キャパシティよりも小さく、したがって、供給過剰となり、このような意味で市場が制約であると考えると思います。しかし、制約理 論ではある特定の会社の製品やサービスにたいする需要が、その会社のその 製品の生産キャパシティよりも小さい場合(手余り状態)に、市場が制約である
といいます。また、その会社が複数の製品を販売しており、したがって、製品 間に、制約資源でのスループット・レート(単位時間あたりのスループット) に差があり、かつ、物理的制約でスループットが制限されている場合に、もし、 スループット・レートの最も高い製品の需要に制限がある場合も、市場に制約が あるといいます。
(市場占有率が100%でない限り)ある企業が、市場の一部しか販路として獲れない理由が、市場の求めるリードタイム、価格、納期遵守度、品質条件などの 競争条件にある場合、一見、市場に制約があるように見えます。また、手持の 生産資源の持つケイパビリティを十分に使いつくす戦略をとっていない場合も、市場に制約があるように見えたりします。
このように、制約理論では手持資源を使いきるだけの自社製品への需要が ない場合、市場が制約であるといいますが、実は、真の原因が、その企業のリードタイム、価格政策、納期遵守度、品質条件、市場のセグメント化の考え 方であったりする場合もありえます。したがって、市場の制約は、リードタイ ムを短縮し、価格政策を変更し、納期遵守度を向上させ、品質条件を改善し、市場をセグメント化してきめこまかい価格政策を採ったり、製品をリブランド して新しい市場を開拓し、さらに、新製品を開発したりして、打破すべきものと考えます。需要がないからしょうがないという発想の逆の発想です。
改善の5ステップ
TOCでは物理的制約を解消しスループットを極大化するまでには、五つのステップがある と考える。そのステップは、図表にあるように、①ボトルネックを発見する、②ボトルネック を徹底的に活用する、③ボトルネック以外をボトルネックに従属させる、④ボトルネックの能 力を向上させる、⑤惰性に注意しながら繰り返す、である。
ポトルネックを発見する:
ボトルネックの発見がボトルネック解消の第一歩となることはいうまでもない。 どこがボトルネックなのかが直感的に分かる場合もあるが、複雑なシステムでは生産性のデータを活用するなどしてボトルネックを特定する作業が必要となる。
ボトルネックを徹底的に活用する:
TOCでは、費用をかけずにボトルネックの解消をすることをまず第一義に考える。 そのためには、ボトルネックになっているプロセスをいかに徹底活用できるかと いうことを考える。
ボトルネックのプロセスを最大限に活用する為にはその稼働を100%にするために その前のプロセスにおいてボトルネックで使用する部品のバッファを持つことが必要 となる。
バッファーを考える際には図にように「安全領域」「警戒領域」「危険領域」に分け それぞれ決められた分量で前工程からボトルネック工程にバッファーとして蓄積されているかを確認する。
必要以上のバッファーは過剰在庫となりキャッシュフォローを減少させる。 さらのバッファーは出荷前の時点でも必要である。
顧客の要請に応じて直ぐに出荷できるように過去のデーターから適正な在庫を確保する 必要がある。
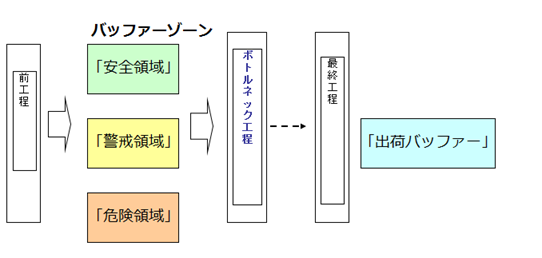
ボトルネックを活用する
■製造工程における具体的事例
1)工程中の仕掛在庫をスケジューリングに組み込む
2)段取り回数の削減、段取り時間の短縮
3)24時間稼働
4)他の設備による代替生産
5)ロット分割による負荷分散
ボトルネック以外をポトルネックに従属させる:
ボトルネック以外のプロセスがボトルネックと関係なく生産などの活動を行うと、 各プロセスでは十分能力を出しきっていても、結局はボトルネックのせいで、 全体のスループットが向上しないということになる。
さらに、その弊害はそれだけにとどまらず、ムダな在庫の増加やその在庫を作り出すた めのムダな労働コストがかかってしまう。したがって、「ドラム・バッファー・ロープ」 により、ボトルネック以外のプロセスをボトルネックに従属させなければならない。
■ドラム・バッファー・ロープとは
①ドラムの役目:
隊列の行進を行う場合、一番歩みの遅いボトルネックの人にドラムを打たせ、サインを 送ることにより他の人にボトルネックの人の速度を教えることができ歩調が合わせることが 可能となる。
②バッファーの役目:
ボトルネックの直前を行く人とボトルネックの人との間に適度な間隔を持たせることにより ポトルネックの人の進行が妨げられないようにする。ボトルネックの進行スピードが全体の 進行スピードを決定するため、ボトルネックの能力を最大限に出させるため。
③ロープの役目:
ボトルネックの人よりも前にいる人は、ボトルネックよりも歩くスピードが速いため放って おくとどんどん前に進んでしまう。しかし、そのことは全体の進行スピードを上げるものではなく、 むしろ余分なエネルギーを消費させたり、全体の隊列が長くなるため監督範囲を広げてしまう (管理コストの増加)。それを避けるためにボトルネックの人と先頭とをロープで結べば、先頭 が行きすぎることはなくなり、隊列の長さを管理することができる。
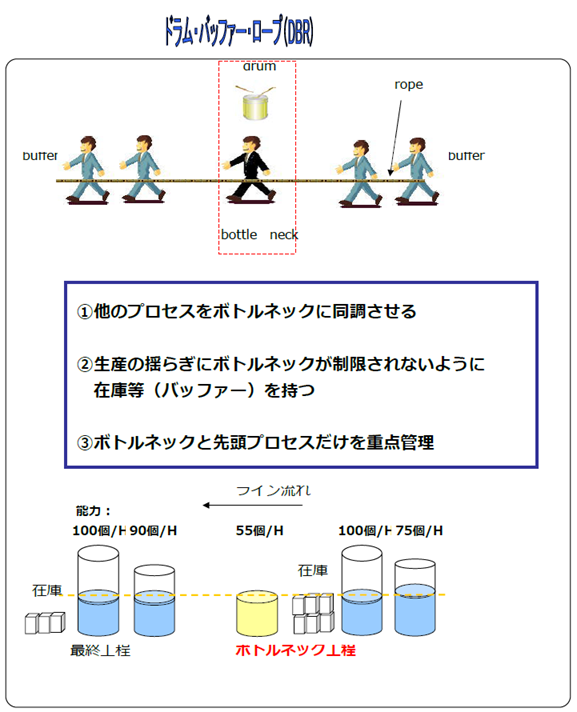
ドラム・バッファー・ロープとは
DBRの概念は、「ドラム」は他のプロセスをポトルネックに同調させる、「バッファー」は生産の ゆらぎなどにボトルネックが制限されないように適切な在庫等を持つ、「ロープ」はボトルネック
と先頭プロセスとの同調を特に管理することにより全体プロセスの管理範囲を限定する。
ということを表したものである。
全体最適を実現するためには、DBRを活用したボトルネックの最大活用が、まず最優先の取り組み となる。
ボトルネックの能力を向上させる:
①から③までを通じてスループットの極大化を図るが、それでもまだ十分なスループットを確保 できない場合には、ボトルネックの能力を向上させなければならない。 ポトルネックの能力向上は徹底活用よりもコストがかかる。
ボトルネックの能力を向上させる方法としては、工程改善、作業改善、設備投資などがある。
TOCにおいては、キャッシュフローの極大化が目的であるから、設備投資のように資本投入 を必要とするポトルネックの能力向上は、先に説明した①ボトルネックの徹底活用、②ボトル ネック以外をボトルネックに従属させること、に次ぐプライオリティー(優先順位)ということになる。
さらに、設備投資には、時間を要する場合も多い。
ポトルネックの能力を向上させるのに時問がかかる場合には、そのポトルネックの能力を向上 させている間に他の人がボトルネックになったり、その他の制約条件が新たに現れてきて、 従来のボトルネックの能力向上が大きな意味を持たなくなる。
製造工程で言えばボトルネックの他の工程がボトルネックになったり、環境変化為に市場制約が 物理制約より大きな制約になることも想定される。
能力向上のために投資を行う場合には、あくまでもポトルネックの能力向上に集中する必要 がある。ポトルネック以外の工程などに投資を行っても、結局ボトルネックが生産性を決定する。
さらにボトルネックの能力向上してもそれがスループットひいてはキャッシュフローの増加に つながらなければ意味がない。
繰り返すこと。
- から④までの過程を、惰性に注意しながら繰り返すことによりスループットを高める。
何度も繰り返すうちに惰性になりがちだが、それを排除することも重要だ。
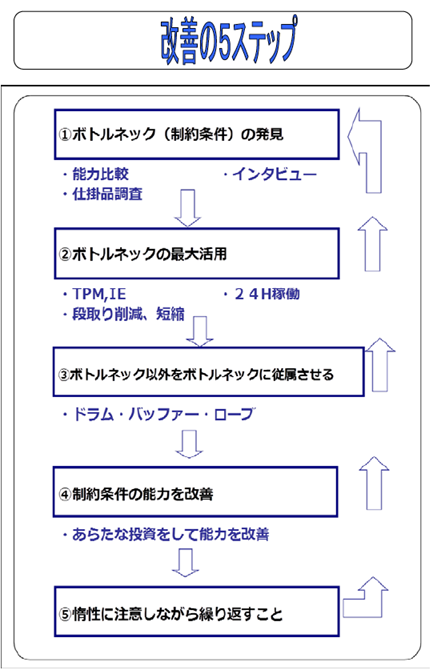
ボトルネックの改善
コメント