6σ(シックス・シグマ)とは?
シックスシグマとは、ビジネス・プロセスを極めてバラツキの小さい状態にすることを目的とした経営・品質管理手法のこと です。σ(シグマ)とは、統計学用語で標準偏差のことであり、平均からの「バラツキ」を示すものです。
具体的には、6σでは100万回に3、4件のエラーが起こる確率を表し、5σでは233件、4σでは6240件のエラーとなります。よって、シックスシグマとは、ビジネスにおけるあらゆるエラー・欠陥を100万分の3~4の確率以内に抑えるシステムプロセスを構築しようというものです。
統計的管理に使用されているXbar-R管理図は±3σ(0.3%の不良発生率)であることから比較するとそのよう発生確率は 非常に小さく具体例としては『小さな図書館にある本のうちの一冊の一箇所に誤植がある確率』です
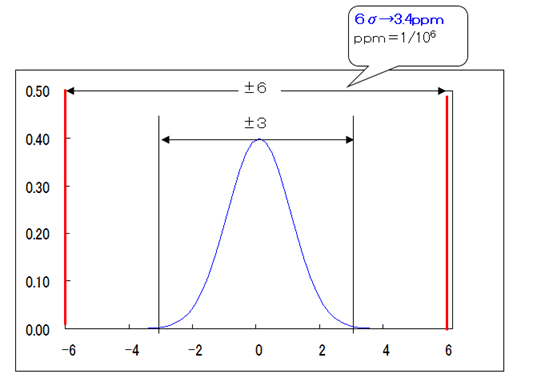
6シグマ – リーンシックスシグマの概念
*統計学上は6σの値の出現頻度は『100万分の3.4』でなく『10億分の1』である。
『100万分の3.4』の出現頻度は4.5σに相当するが6σの開発元であるモトローラに経験則に基づいている。
シックスシグマの歴史 | ゼネラル・エレクトリックでの誕生
シックスシグマの手法は1980年代初頭に日本のポケベル市場に参入しようとしたモトローラが、自社と日本メーカーの 不良品率を比べて自社の品質の低さに愕然とし、品質向上を目指したのが始まりだといわれている。
この時の活動の中心にあたったマイケル・ハリー(Mikel Harry)が同僚と共にシックスシグマを開発した。 この活動結果として栄えある第一回MB賞(マルコム・ポールドリッジ賞)を受賞した。
モトローラをはじめとし、テキサス・インスツルメンツ(TI)、アセア・ブラウン・ボベリ(ABB)、アライド・シグナルが 次々に導入し、さらにGEの導入により脚光を浴びた。
GEの総師・ジャック・ウェルチは1996年にシックス・シグマの活動を宣言し徹底して活動の推進を自ら図り 驚異的な成果を上げた。
生産志向の時代に「メイド・イン・ジャパン製品」で強さを発揮していた日本企業も、顧客志向の時代となった現在では、 これまで生産さえしていればよかった生産部門と他部門との連携が強く求められるようになっています。
そのため、欧米企業の動向にいち早く着目したソニーをはじめとし、東芝、日立マクセル、シマノなどが、品質管理 だけでなく、経営改革手法としてシックスシグマを取り入れている。
もともと、6σは日本の品質管理(SQC、TQC,TQM等)をベンチマーキングしてアメリカ流にアレンジしたベスト プラクティスです。その違いは改善活動の取り組みを精神論、経験、勘、根回し、度胸だけで行うのでなく科学的に 論理的に考えた手法に基いて活動を推進し経営に寄与しようするものです。
6σのToolはTQMと差はほとんどありません但しその改善への至るプロセスは注目に値します。 全ての事象を数値化し、共有化し、真の経営に寄与するものを優先的に人的資源、投資を行い集中的に 活動を取り組んでいます。
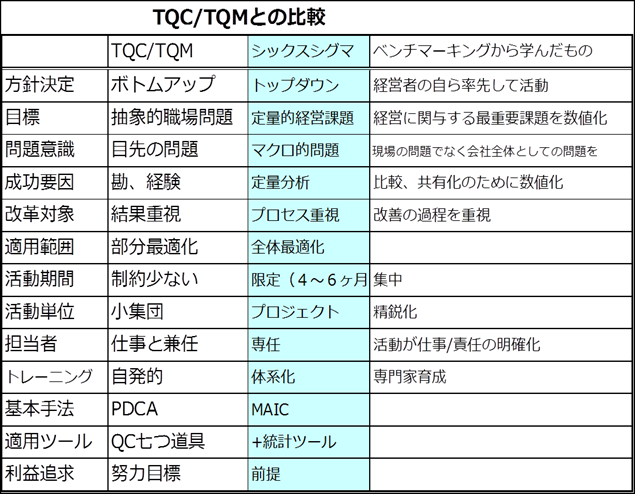
TQM/TQCとシックスシグマの比較
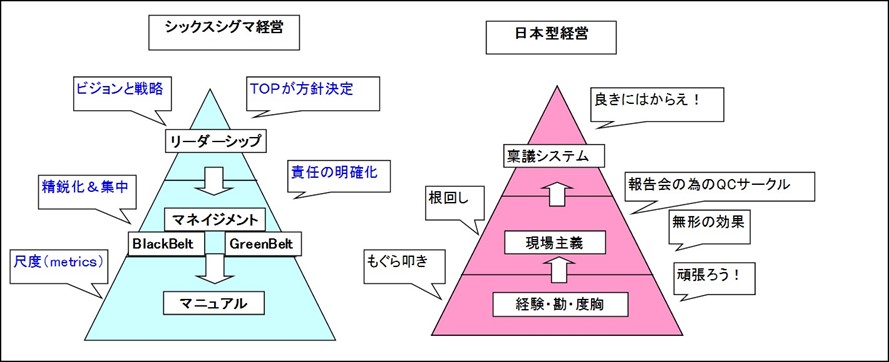
シックスシグマ経営と従来の日本型経営
CTQとは(Critical to Quality) | 経営成果に影響を与える重要な要因
CTQとは「経営成果に影響を与える重要な要因」のこと(Critical to:不可欠な)であり シックスシグマで対象にしているものは常にCTQです。
「CTQが明確に特定できれば、問題は解決されたものと同じだ」であり後はパッケージソフトにて分析し、改善すれば シックスシグマ活動は終了です。
さらに言い換えれば、CTQは、「経営上、重要な問題、要因に重点化して取り組んでいくこと」を示すコンセプトである と表現することができます。
TOC(Theory of Constraint:制約理論)での ボトルネックなども、根本的な趣旨はCTQと同様のものです。
CTQの具体例・・・・「ホテルでの食事」
恋人と優雅な休日を送る場合――のんびりとくつろぎ、豪華な内装や食器、用がない限りはテーブルにはウエイターや ウエイトレスは寄ってこない
全社をあげてのコンファレンス(Conference)の場合–食事が終わった瞬間にコーヒーはすぐに出てきて欲しい 食事、くつろぎは二の次、ビジネスが第一優先
「良いレストラン」は顧客の定義によって異なります。顧客ニーズの分析が重要となります。 あなたがこのレストランをマネジメントする立場であった時、自分たちにとって重要な顧客ニーズを厳密に把握して、 対応していく必要があるのです。シックスシグマは、こういった曖昧性を徹底的に分析、評価していきます。
CTQの検討/設定について注意すべきポイント整理したものが下図です。
「CTQ改革」の基本
全社視点の重視→全社最適化→スタッフの重視(現場偏重主義の脱皮) 顧客ニーズの事業化→理想を追求しない→尺度は競合との比較 目標設定の数値化
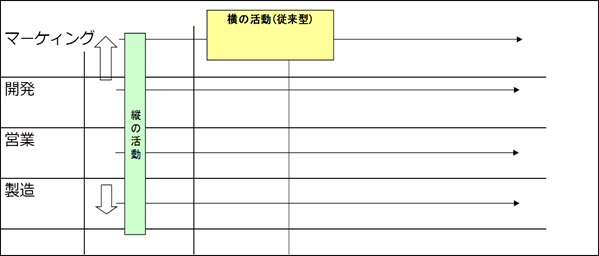
CTQとは
顧客に納期への希望を単に聞いてしまったら、即納を期待されることは、ほぼ間違いないでしょう 製品やサービスによっては、即納をするためにたくさんの在庫、工数が必要となる場合が多くあります。
勿論、顧客の即納ニーズに合わせ、経営システムを革新することは重要です。しかし、事業として考えれば
、あるべき姿は理想ではなく、競合他社との関係で検討/設定すべきでしょう、(=過剰品質/サービスによるCOPQ発生の排除)。「(競合と比較して)2日遅い」これこそがVOCとして捉えるものであり、CTQ設定の基準なのです。 さらに配慮すべきことですが、CTQ、つまり「経営に重要なインパクトを与える要因は、数多くあるはずがない」
ということです。数少ない経営に決定的なインパクトを与える要因を定義することが重要であり、その課題に経営資源を集中して成果を追求することが改革の効率も高めることになります。
シックスシグマでは、これを『バイタル・フュー』(Vaital few)と呼んでいます。これは極めて重要な概念であると 考えています。CTQがたくさんあるということは、まだ課題の定義が完了していないことと同意義です。
シックスシグマに限らず、改革プロジェクトを実行する前に、課題の関連づけ、優先順位設定を行いますが、 それが10、20とあがってくることがあります。こうした場合、私達は問題の因果関係分析(原因/結果相互関連図) を実施しますが、そうすると大抵の場合は3から5件程度に集約することができます。改革には資源が必要です。
そしてその資源には限りがあるはずです。改革を実行するのであれば、大きな根幹の問題を対象として、集中的に資源投下をすることが重要だということです。
COPQとは(Cost of Poor Quality) | プロセスが悪い為に発生するコスト
COPQとは『経営のやり方、プロセスが悪い為に発生するコスト』のことです したがってCOPQは金額で表示することになり数値化できるため、比較、共有化 が可能となります。下は「氷山」をイメージしています。 COPQの種類には、海面の上側にあるものと、下側にあるものに大別されます。
上側は、ほとんどの企業でこれまでも「コスト」として認識され、それが増えてしまうと削減対象になって いたようなものです。
それに対して下側は、少々分かりにくいCOPQです。
シックスシグマを導入している企業や個別企業の経営視点によっては、こうした項目のコストを「削減対象」としている場合もありますが、経理やその帳簿上には出てこないものが多く、事業実績に具体的に影響を与えているもの であったとしても、他の費目に含まれてしまっていることが少なくないのです。
これらは一般に「機会損失コスト」「失敗コスト」などとも呼ばれています。 各社によって若干数値が異なりますが、氷山の上側にあるCOPQは「売上の5-8%」相当、下側は 同「15-20%」相当、存在していると言われています。
つまり、私たちが普段から気にしているコストの3倍にも相当するCOPQが、内在している可能性が あるということです。 長らくコストダウン努力をしてきた日本企業にとっては、既に上側のCOPQ削減はほぼ完了しており、 これからターゲットとするのは「下側しかない」という大手製造業もあります。
こうしたCOPQが発生してしまう原因はいろいろあるわけですが、シックスシグマでの基本的考え方は「バラツキがCOPQを生む」ということです。 適切なプロセスがいつも安定して運営されていれば、最初に計画した以上のコスト(=COPQ)はかかりません。
しかし、例えば、そのプロセスを担当する人のやり方やスキルレベルによって、計画よりも時間がかかってしまったり、 欠陥(エラー、不良品)が発生すれば余計なコスト(=COPQ)が必要となってしまうのです。
シックスシグマの目的は、「COPQを発生させているプロセスのバラツキを減らすこと」です、「プロセスを変えずにコストを減らす」ことだけが目的であるとすれば、その手法としてシックスシグマを採用することは、 COPQを発生させるだけです。
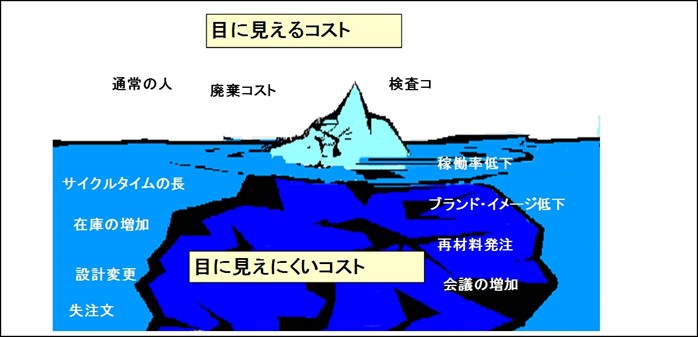
COPQの概念図 見えるコストと見えないコスト
COPQの計算 | 材料手配、工程配分、物流等
【事例】 M社にてお客様より連絡があり「不良品がひとつ入っていたので完成品Aが組み立てできないので出荷できない 至急、代替品を送れ!」との連絡があった。
在庫がない為に緊急に生産会議を招集して材料手配、工程配分、物流等について検討を行い、代替品をつくり、特別便で お客様に届けた。
上記の場合のCOPQは下記の表になる。
(1) 生産方式はすべて「標準品単品生産」
(2) 従業員の規定労務時間は部署にかかわらず「1日8時間」
(3) A社の製品1個当たり製造原価は5,000円 参考:類似している競合他社の製造原価は「4,500円」
(4) 生産計画部門で、今回の件に費やした工数は「1人X1日」(計画調整、資材発注などを含む)
(5) ライン変更のためのセットアップは、平均で「1人1時間」の対応/処理、生産1時間
(6) 製品1個当たりの検査「1人4時間」
(7) 通常、@500円の部材を今回は800円で調達(1個)
(8) 1日当たりローディングは、部門ごとに以下となっている
営業部: 8,000円、検査部:11,000円、生産部:9,000円、間接:12,000円
(9) 製品1個あたりの物流費用は200円
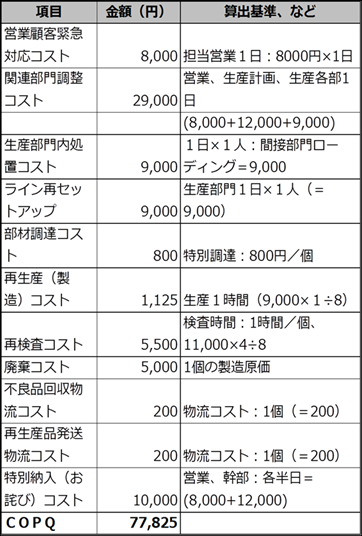
COPQの計算 | 材料手配、工程配分、物流等
つまり一個の不良品のために77、825円ものロス費用が余計に発生した
コメント