統計的品質管理SQC | 統計的分布の解析
統計的品質
たいていの工場では良品と不良品の両方を製造している.どうして良品と不良品が混じって作られるのであろうか.製品がどのようなものであろうと,またその製造方法がどのようなものであろうと,その原因は常に同じである。
バラツキ—これが不良の原因である。
もし,まったく同じ材料を用いて,まったく同じ機械装置により,まったく同じ作業のやり方で作られた製品に,まったく同じ検査を行ったとすればどうなるであろうか.製品が何個作られようとも,上の4つの「まったく同じ」という条件が満たされるかぎり,「まったく同じ」製品ができるはずで,全数良品になるか,全数不良品になるかのいずれかで,良品と不良品が混じって作られることはない。全数不良になるのは,用いた材料,機械装置,作業方法,検査のやり方のいずれかが不適切な場合で,確実に「まったく同じ」不良品が作り
出される.上の4つの条件が完全に満たされれば,作り出される製品は全部「同じ」良品になるはずである。
①材料のバラツキ
②機械・装置のバラツキ
③作業のやり方のバラツキ
④検査のバラツキ が不良の原因である
鉄板を曲げる作業について考えてみよう.鉄板1枚1枚はみな同じ厚さであるようにみえる.しかし,これらを精密に測れば全部厚さが異なる。また1枚の鉄板でもその1枚の中で厚いところと薄いところがある。さらにその結晶構造にまで立ち入って調べれぱ,鉄,炭素,その他の元素で作られている内部構造は各部分で少しずつ異なる。このような違いは当然品質特性に影響する.同じ方法でプレス作業を行っても,曲りの状態がばらつく。なかには亀裂が発生するものもでてくる。
機械加工作業について考乏てみよう。切削用の刃物は製品を何個か加工する問に切れ味が変わってくる.温度の変化により潤滑油の状態にも変化が起こる。
セットのやり方,位置ぎめの状態で製品の寸法は変化する。
熱処理作業について考えてみよう.電気炉であれば電圧の変動,温度測定の誤差,制御の遅れ,ガス炉であれぱガス圧の変動などで炉温は変化する。炉の入口付近,天井部,床部,炉壁部,中央部で温度は異なっている。炉に熱処理材料を装入するとき,材料間の相互の位置関係により受ける熱量はばらつく。
これは製品の品質特性,たとえば硬度に影響を与える。
作業者,これも品質のバラツキに大きな影響を持つ.大きな人,小さな人,器用な人,不器用な人,力の強い人,弱い人,右利き,左利き一まったく同じように作業をやっているつもりでも,人によりそのやり方は異なる。同じ人でもその日その日の気分,体調によって作業の内容は変わってくる。うっかりミスがでることもある。
検査においても見かけ上、品質にバラツキが発生する.測定器を使う検査であれば,測定器の誤差,使い方の違いによってデータはばらつく.目視検査のような官能検査においては,検査員の判断規準がばらついておれば,それが見かけの上で品質に変動を与える.検査のバラツキは製品の品質変動には直接関係しないが,良,不良の判定に影響するのである。
以上のべたように1つの製品を作るにあたって,その製品の品質特性に影響を与える要因は無数にあり,外見上同じような状態で作業が行われているようでも,われわれに見えないところで無数の要因で条件が異なっており,これが品質ヒンシツに影響する.要因のバラツキという観点から製造工程を眺めるとき,
「工程とはバラツキの要因の集まりである」
とすることができる.これらの原因により製品の品質特性は変動し,良品ができたり,不良品ができたりする.良,不良の区別は製品が品質規格に合っているか否かによって区別されるものであり、良品といえども規格の中でバラツイており,先にのべたような「まったく同じ良品」ではない.不良の原因はバラツキにある。このバラツキをなくせば不良はなくなる.これは製品の種類,製製造方法がどのようなものであっても常に成立する単純なしかも強力な原理である。
以上のべたように,まったく同じ条件で作ったつもりであっても細かく観察るとわずかずつ条件が異なっており,その結果として品質はばらつく。同時に作られた同じ製品の品質のバラツキがどのような状態にあるかによって,集団としての品質を考えることができる。同じと思われる条件で連続して作られた製品の集まり–これをロツトという–について,品質特性の統計的分布を考え,この分布全体が規準をどの程度満足しているかによってロットとしての品質の良し悪しが定められる。たとえば,図1.1においてロットAとロットBを比べるとロットAの方が全体として基準に近いのでロットBよりもロットAの方がよいとすることができる。
個々の製品ではロットBにおいても,基準を完全に満足しているものがあり,これについては,ロットAの製品より劣るとはいえないのであるが,全体としてみたときにはAの方がよいとされるのである。このような集団の品質を統計的品質という.統計的品質は製品の集団全体の品質の傾向を示すもので,集団の品質特性の統計的分布によって定められる。
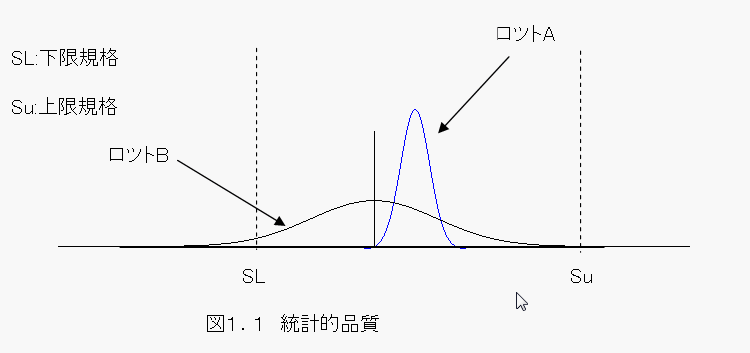
統計的品質管理の概念図 平均値とバラツキσの説明
統計的品質は,製品1個1個の品質ではなく,集団としての品質である.統計的品質の把握においては,製品の品質特性の測定値は,測定の対象となった製品の個々の評価のためというよりは,品質特性の分布の推測に用いられる。
品質特性が規格に対する適合,不適合で測定されるときは統計的品質は良品率または不良率で表される。
統計的品質は,材料や製造条件によって法則的に支配され,好ましい統計的品質を得るにはこれらの条件を適正に設定し,維持することが必要になる。
個々の製品の品質は検査によって獲得されるのに対し,統計的品質の獲得は材料,機械、装置,作業,計測の適正な管理によって得られる.製造工程が適切に設定され,その管理によって製品品質の統計的分布が満足すべき状態にあるとき,品質は工程で作り込まれているという.この場合は,不良品が発生しないため,個々の製品について合否の判定を目的とする検査は不要となる。
製品品質をばらつかせる原因は無数にあるとはいえ,その影響の大きさはみな同じというわけではない。品質に大きな影響を与えているものもあるし,技術的には重要と考えられるものでも,適切に管理が行われているため,現実の品質変動にはほとんど影響を及ぼしていないものもある。実際の品質変動に影響を与えている原因について,その寄与度を大きさの順に並べてグラフに書くと一般に下図のような図が得られる。
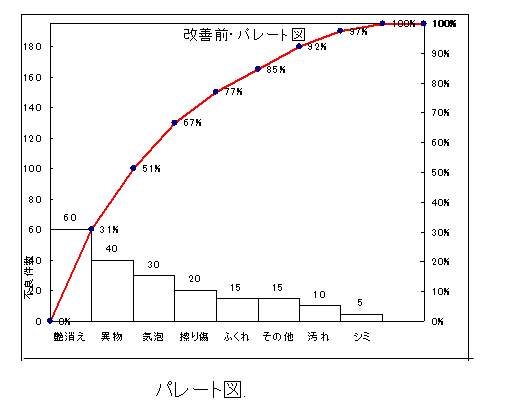
パレート図の具体的な説明図
この図をパレート図という.無数に考えられる原因は,多くの場合この図に示されるように,数は少ないが大きな影響を与えるもの(vital few)と,数は多いが小さな影響しか与えないもの(trivial many)の2つに大別することができる。大きな影響を与える数少ない原因を押えることにより,不良の大部分をなくすことができる。
イタリアの経済学者パレート(V.F.D.Pareto)は所得の分布にいて指数的法則を発表した、これは所得の大部分はごく少数の人で獲得れていることをのべたものである。
品質管理においてこの現象を不良の原因系に適用して,これをパレートの法則あるいはパレートの原理とよんでいる。
品質に大きな影響を与える原因をすべて除去し,多くの小さな影響しか持たない原因だけで品質が変動している状態を統計的管理状態という。このような状態は無数にある小さな原因がランダムに偶然的に発生する状態であり,確率論で知られている中心極限定理により,品質特性の分布は正規分布もしくは,それに近い分布になる。
統計的品質管理の創始者であるシューハートは品質変動を管理する立場から,品質に変動を与える原因を偶然原因(chance cause)と突止原因(assignable cause)の2つに分けた。偶然原因は技術的に同一条件で作業を実施しても結果にバラツキを与える原因で,これを抑えることが技術的,経済的に困難なもので,上にのべたtrival manyに対応する原因である。これらは避けられない原因、不可避的原因ともよばれる。突止原因とは技術標準,作業標準が守られなかったり,未設定であった場合に品質が異常になるなど,とくに大きなパラツキを与える原因である。これらは関係者が協力すれば技術的に除去しうる原因で異常原因ともよばれる。
通常の製造工程,実験,測定操作では操業条件の変化,装置や計測器の故障,あるいは使用ミスなどによりいろいろの異常原因が発生する.これらを着実に除去し,偶然原因だけによる管理状態を目指して改善をはかっていこうとするのが統計的品質管理の考え方である。
管理された状態からとられたデータは,正規分布あるいはそれに近い統計的分布に従い,異常が発生しなければ,あらかじめ定められた確率で入ると考えられる限界を設定することができる.この限界を統計的管理限界というが,これは規格,公差とは別の概念である。
規格,公差は品質を規定するものであり,個々の製品の良,不良の判定基準として用いる。
これに対し,管理限界はデータがこの限界を外れた場合,工程に異常があることを意味し,工程の正常,異常の判定基準として用いる.測定値が管理限界を外れた場合,処置をとる対象は製品ではなく,工程である。製品の合否を定めるのは製品規格であり,工程
が異常であったとしても,そこで作られた製品が規格に入っていれば,製品としては合格である。ただし,工程異常の場合は,品質にも何らかの影響があるはずであり,異常の状態で作られた製品は一般に検査を入念に行うことが必要である。
全社的品質管理 | 工場での不良低減
高度の工業製品においては,製品の品質基盤はその設計および製造に関わる固有の技術にある。この固有の技術なしでよい品質の製品が作れるものではない。また,よい品質の製品を作り出すのは優秀な技術者である.しかし,実際場面では①現有の技術は完全なものが少なく,改善すべき点が多くある.
・優れた技術者は常に不足している.
・たとえ優れた技術者がいても,チームワークが悪く,仕事の進め方が適切でないとうまくいかない。
のが普通で,このような場合には品質の改善がはかられなければならない。企業が計画的,組織的,継続的に改善を行うシステムを持つことはきわめて有効であり,これによって固有技術も進歩し,技術者の能力も向上する。
日本の品質管理は品質を管理するだけでなく「改善」することにも重点を置いている。改善を組織的,継続的に実施する活動が日本的品質管理である。
品質管理による改善は固有技術による改善と比べて,地味で目だたないものであるが,これには次のような特質がある。
(1)わずかな効果でも,それが本質的なものである場合には蓄積され,多くの改善カイゼンが累積してくるとその総合効果はきわめて大きなものとなる。
(2)現在の方法とまったく異なる新しい原理によるといった質的改善でなく,条件を変えるといった量的な改善が中心となるため,その方法には後でのべるように普遍性がある.ある業種で用いられる方法が技術基盤の異なる他の業種にも適用することができる.すなわち固有技術はその製品を中心とするかぎられた範囲で用いられるのに対し,品質改善のための技術はたとえば化粧品の製品から原子カプラントの建設まですべての業種で適用することが可能である。
(b)品質管理活動の拡大—全社的品質管理(Total Quality Management)
アメリカから導入された品質管理活動の中心は当初は工場の不良減らしにあったが,品質管理は現在では商品企画から設計,製造販売,アフターサービスにわたる品質改善のための体系的方法に発展してきている.製品の品質は工場で作られるものではなく,設計からアフターサービスにいたる各工程が完全に行われることによって始めて顧客の満足する品質を実現することができる。
これを達成するために,品質管理は企業のマネージメントの中のきわめて大きな部分を占シめ,この活動は全杜的品質管理(TQM)とよばれている。また,企業が各プロセスにおいて品質改善を組織的・継続的に行うシステムを持ち,実践することは企業経営にもきわめて有効であることが多くの企業において実証されている。
デミング賞 | デミング賞受賞企業
デミング(W.E..Deming)はアメリカの統計学者であるが,日本の品質管理の発展に深い関わりを持っている.彼は日本科学技術連盟の招きにより,1950年,51年,52年に来日し,品質管理,市場調査などのセミナーを行い,日本における統計的方法・品質管理の普及・発展に大きな役割をはたした。1951年にデミング賞が創設された.これはデミング博士から講義録の印税の寄付を受けた日本科学技術連盟が,これを基金として設立したものである。
デミング賞には,デミング賞本賞とデミング賞実施賞とがある.デミング賞本賞は統計的品質管理の理論ならびに応用の研究において卓越した業績をあげた人,またはこの方法の普及において功績顕著な人に与えられる.デミング賞実施賞は統計的品質管理の実施によって大きな業績をあげている企業に授与される。
デミング賞実施賞は日本における品質管理推進の大きな力の1つになっている。日本の代表的な企業の多くが実施賞を受賞することによって自社の品質管理のレベノレアップをはかっており,それが結果として目本の品質管理の水準を押し上げる結果とになっている。
先にものべたように日本の品質管理はアメリカから導入されたものであるが,日本において独自の発展を遂げた.これにはデミング賞がきわめて大きな役割を果たしている.それはデミング賞を通していろいろな品質経営手法が日本の企業で開発されたからである.1960年代以後において開発された手法を振り返ってみると表1.1に示したようなものがある.これらの手法は企業秘密にはならず,他の企業でも広く使われるところとなり,これが日本全体の品質管理のレベルを向上することにつながっているのである。
表1.1デミング賞受審時に発表された経営手法
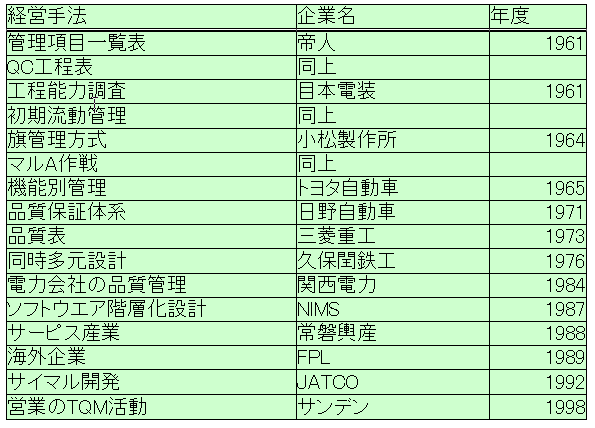
デミング賞の経営手法とデミング賞受賞企業
マルコム・ボールドリッジ賞 | アメリカでの設立
日本のデミング賞が品質改善に大きな役割を果たしていることがアメリカの人へたちにも理解されて,アメリカでもそういう賞をつくろうとする動きがアメリカの有力企業の経営者の問で起こり,議会への働きかけによって1987年にマルコム・ボールドリッジ賞(Malcolm Baldrige National Quality Award)の制度が設立された。
マルコム・ボールドリッジは元アメリカの商務長官でこの賞を設けるけることに努力を払っていたが,休暇中にロデオで落馬して不慮の死をとげた。
長官の生前の貢献を記念して,この賞にマルコム・ボールドリッジの名ナが冠せられることになったのである。
この賞は日本のデミング賞実施と同じように品質管理に大きな業績をあげた企業を表彰する制度であるが,デミング賞が民間の団体である日本科学技術連盟によって創設されたのに対して,ボールドリッジ賞は「Public Low 100-107」としてアメリカ合衆国の法律によって制定され,1987年から活動を開始した。
日本のデミング賞を下敷きとしているが,デミング賞よりもさらに充実したものになっている。
1992年にはヨ-ロッパおいてもヨーロッパ品質賞(European Quality Award)が設立されている。
IS09000規格による品質管理 | 品質審査登録制度
1.1節でのべたように,シューハートの開発した統計的品質管理の方法はアメリカ軍によって採用されたため,近代的品質管理は2つの方向に分れて発展した、1つは前節でのべたよいモノを作るための品質管理で,生産者において統計的方法を活用して製造の不良を低減する活動から始まり,全社的品質管理に至るものである。他の1つは購入者においてよいものを買うための品質管理で,品質システムを規格化し,これを購入者の生産者に対する要求事項とする形で発展してきている。現在,国際的に広く行われているIS09000規格による品質審査登録制度がこれである。
(a)品質管理要求事項とは
よいものを買カうための品質管理活動の出発点はまず検査である、製品が要求どおりのものになっているかどうかを検査し,検査に合格したものを購入する。
しかし,すべての品質が検査できるわけではない。検査で確認できない品質,たとえぱ製品の強度や寿命など,破壊検査でしか確認できない品質については,まず抜取検査でサンプルの品質確認を行い,さらにサンプル以外の他の製品がサンプルと同等の品質であることを確保するために,ロットを定義し,ロットに含まれる製品の品質の均一性を要求事項として定めるのである。
製品の均一性は原材料の管理と生産工程の標準化によって獲得されるが,それが確実に行われていることを確認するために購入者は供給者の工場に出かけていってその状況を調べる.これが工程監査である。
工程監査の結果が好ましいものであっも,継続的な購入においては,その状態が安定して常に確保されていることが必要である.このためには供給者の品質管理体制が適切なものになっいなければならない。そこで購入者は供給者の品質管理のやり方について要求事項を定めるのである。
.これが品質システム要求事項で,以下に述べるISO9000がこの要求事項の国際規格である。
(b)lS09000規格の誕生
1970年代において多くの欧米諸国で品質保証の要求事項に関連する規格が制定された。このような規格を各国がばらばらに持っていることは,国際的な通商活動の障害になる恐れがあり,これらの規格を統合して品質保証の国際規格をつくる動きが起こり,1979年にISO(国際標準化機構)において「品質保証の分野における標準化」を活動範囲とする技術委員会TC176が設置された。
ここで規格原案の検討が行われ,IS09000~9004の5つの規格が1SO規格として制定され,1987年3月にその初版が発行された。それ以後,引続き規格の改定が行われ,1994年に第1回改定,2000年に2回目の改定版が発行される。
2000年に発行されるIS09001およぴIS09004の内容を図示すると図1.3のようになっている。
品質管理要求事項がIS09000規格として制定され,これが多くの購入者に採用されると,購入者が供給者に求める品質管理システムは共通のものとなる。
そのような状況では購入者がそれぞれ別個に供給者の品質システムがIS09000規格に適合しているかどうかを監査することは,多くの購入者に製品を納入している供給者は同じ監査を何回も受けることになり,経済的ではない。
これを避けるために購入者に代って第三者が供給者の品質システムの適合性評価を一元的に行うことにすれば,監査の回数を減らすことができる.このような考え方にもとづいて第三者による品質システム審査登録制度がヨーロッパで始められたが,1990年に入ってこれが国際的に行われるようになった.この制度はわが国にも導入され,1994年に正式に発足した。
この制度は商取引や契約などに際して,供給者や購入者が任意に利用できるサ一ビスとして提供されるもので,強制的なものではない.あくまでも購入者と、供給者の間で取引の際に第三者による審査登録制度を利用するかどうかを両者の同意にもとづいて契約として定めるものである。
この制度の中核となるのは審査登録機関であるが,これはどのような組繊でもISOで定められている資格基準を満たし,審査能力があると認定されれば,それが国の組繊であろうと民間の組織であろうと審査登録機関になることができる.その組織がこの基準を満たしているかどうかの審査は認定機関によって行われる。
認定機関は各国で1機関が存在するが,認定機関を持たない国もある。わが国では(財)日本適合性認定協会がこの業務を行っており,ここで認定を受けた審査登録機関は現在約30機関ある。
この制度の運営には審査を行う審査員の教育訓練を行うことが必要で,これも審査登録機関と同様にあらかじめ定められた基準を満たす組織であればどのような組織であっても審査員の養成機関となることができる.現在わが国には約10の研修機関が認定されている。
この制度は国際機関であるIS09001にもとづいた制度であるため,供給者が審査登録を受けるとその結果は国内だけではなく国際的取引においても通用しうるものとなる。これにはお互いに他国の審査登録結果を認めることが必要である。これを相互承認というが,認定機関がお互いの審査能力を認めあって他国の認定機関で認定を受けた審査登録機関を自国で認定した審査登録機関と同等と見なす制度である。相互承認は審査登録機関どうしで行うこともある。
まとめ
世界の品質管理の歴史は、産業革命以降、統計的手法の導入、TQMの普及など、様々な段階を経て発展してきました。日本の品質管理は、世界の潮流を踏まえつつ、QCサークル活動など独自の取り組みを展開し、世界トップレベルの品質を達成しました。
今後の展望
近年では、Industry4.0、Web3.0、IoTやAIの活用など、新たな技術の導入により、品質管理はさらに進化しています。また、サプライチェーン全体の品質管理や、サービス産業における品質管理なども注目されています。
新しい時代の品質管理〜Industry4.0とWeb3.0〜
品質管理は産業革命とともに始まりました、大規模大生産の時代にその必要に駆られて品質管理は行われたことはその時期の手法・考え方の発展が物語っています。
その時期の産業革命をIndustry1.0とするならば、現代はIndustry4.0の時代で、ものづくり業界全体に革命がもたらされようとしています,自動車業界においても、CASEやMaasといった、新しい時代を省庁する標語が掲げられ、時代の変換期を迎えています。
時を同じくしてソフトウェア、Webサービス業界においては、これまでGAFAといわれる中央集権型のサービスがビッグデータを基に多方面にサービス展開を行うことで主権を得たWeb2.0時代の進化が緩やかになり、ブロックチェーンやメタバースといった新しい技術、考え方を基にWeb3.0が構築されようとしています。
いずれにおいても、従来型の大規模大生産を基に構築された品質管理の体系的な知識体系の全てが通用することはなく、新しい時代の品質管理が求められ始めています。より正確には品質管理自体が考えられている、というよりは新しい時代のテクノロジーが発展しているため、その後に新しい時代の品質管理が構築されるでしょう、という時代が近く訪れています。
関連キーワード: #品質管理、#TQC、#TQM、#QCサークル、#デミング賞、#メイド・イン・ジャパン、#IoT、#AI
おすすめ 品質管理 参考文献:
コメント