COPQ cost of poor quality 【イラスト図解】
英語:cost of poor quality 中国語:不良质量成本
COPQとは
不良品質コスト.シックスシグマにおける品質改善活動の経済的効果を斟酌 (しんしゃく)するための基本的スケールで,いわゆる品質コストにおける失敗コストと同義である.
すなわち,シックスシグマによってもたらされる成果を知る最も確実な方法は,作業のやり直しや非効率,顧客の不満,売上の喪失などによる損失を計算し,それを減らすことでどれだけ利益額が改善するかをつかむことである.また,品質改善活動の優先順位を決定するためにも,それが財務上どれだけの利益増につながるかを把握することは重要とされる.
事実,経営そのものプロセスや活動は無数に存在する.他方で,経営資源は有限であるため,改善すべきプロセスや活動の優先順位を決定しなければならない.そこで,各改善プロジェクトが財務上どれだけの利益増につながるかを予測するとともに,事後的にも実績を同様な視点から判定することが不可欠となる.COPQは,品質改善が利益業績に及ぼす効果を失敗コストの減少額としてダイレクトに表示することから,シックスシグマにとってまさに理想的なスケールであったといえる.
関連記事:シックスシグマーCOPQとは
わかりやすく COPQ
COPQとは『経営のやり方、プロセスが悪い為に発生するコスト』のことです したがってCOPQは金額で表示することになり数値化できるため、比較、共有化 が可能となります。下は「氷山」をイメージしています。 COPQの種類には、海面の上側にあるものと、下側にあるものに大別されます。
上側は、ほとんどの企業でこれまでも「コスト」として認識され、それが増えてしまうと削減対象になって いたようなものです。
それに対して下側は、少々分かりにくいCOPQです。
シックスシグマを導入している企業や個別企業の経営視点によっては、こうした項目のコストを「削減対象」としている場合もありますが、経理やその帳簿上には出てこないものが多く、事業実績に具体的に影響を与えているもの であったとしても、他の費目に含まれてしまっていることが少なくないのです。
これらは一般に「機会損失コスト」「失敗コスト」などとも呼ばれています。 各社によって若干数値が異なりますが、氷山の上側にあるCOPQは「売上の5-8%」相当、下側は 同「15-20%」相当、存在していると言われています。
つまり、私たちが普段から気にしているコストの3倍にも相当するCOPQが、内在している可能性が あるということです。 長らくコストダウン努力をしてきた日本企業にとっては、既に上側のCOPQ削減はほぼ完了しており、 これからターゲットとするのは「下側しかない」という大手製造業もあります。
こうしたCOPQが発生してしまう原因はいろいろあるわけですが、シックスシグマでの基本的考え方は「バラツキがCOPQを生む」ということです。 適切なプロセスがいつも安定して運営されていれば、最初に計画した以上のコスト(=COPQ)はかかりません。
しかし、例えば、そのプロセスを担当する人のやり方やスキルレベルによって、計画よりも時間がかかってしまったり、 欠陥(エラー、不良品)が発生すれば余計なコスト(=COPQ)が必要となってしまうのです。
シックスシグマの目的は、「COPQを発生させているプロセスのバラツキを減らすこと」です、「プロセスを変えずにコストを減らす」ことだけが目的であるとすれば、その手法としてシックスシグマを採用することは、 COPQを発生させるだけです。
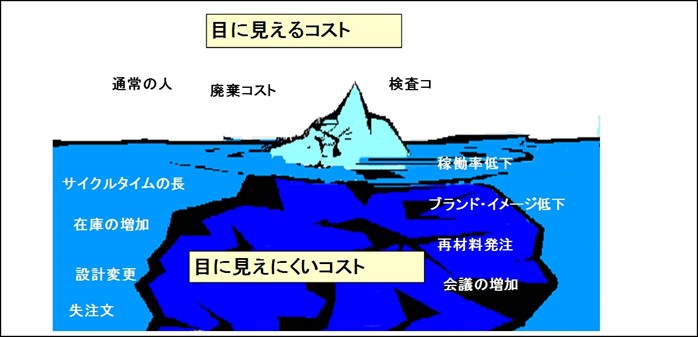
COPQの概念図 見えるコストと見えないコスト
COPQの計算 | 材料手配、工程配分、物流等
【事例】 M社にてお客様より連絡があり「不良品がひとつ入っていたので完成品Aが組み立てできないので出荷できない 至急、代替品を送れ!」との連絡があった。
在庫がない為に緊急に生産会議を招集して材料手配、工程配分、物流等について検討を行い、代替品をつくり、特別便で お客様に届けた。
上記の場合のCOPQは下記の表になる。
(1) 生産方式はすべて「標準品単品生産」
(2) 従業員の規定労務時間は部署にかかわらず「1日8時間」
(3) A社の製品1個当たり製造原価は5,000円 参考:類似している競合他社の製造原価は「4,500円」
(4) 生産計画部門で、今回の件に費やした工数は「1人X1日」(計画調整、資材発注などを含む)
(5) ライン変更のためのセットアップは、平均で「1人1時間」の対応/処理、生産1時間
(6) 製品1個当たりの検査「1人4時間」
(7) 通常、@500円の部材を今回は800円で調達(1個)
(8) 1日当たりローディングは、部門ごとに以下となっている
営業部: 8,000円、検査部:11,000円、生産部:9,000円、間接:12,000円
(9) 製品1個あたりの物流費用は200円
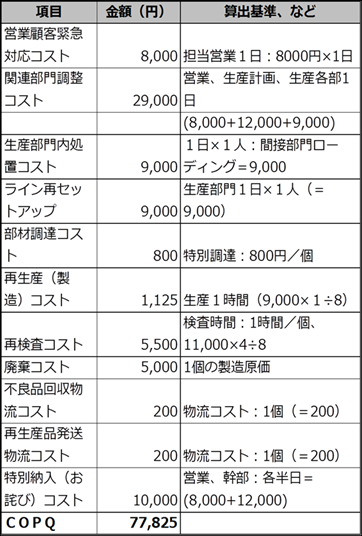
COPQの計算 | 材料手配、工程配分、物流等
つまり一個の不良品のために77、825円ものロス費用が余計に発生した