シューハート管理図の作り方について下記の点をポイントに図解入れで解説しています。
・管理図 エクセル
・管理図 種類
・管理図 書き方
・管理図 異常
・R管理図とS管理図の違い
モノづくりの参考になれば幸いです。(*^_^*)
*現在、シューハート管理図の作成はAIで簡単に作成できる時代になりました。
下記が『AIによる管理図作成、分析』の参考記事です。
youtube シューハート管理図の作成 音声解説
管理図の種類の説明をしている動画の紹介、これでXbar、c、u、p、npの違いが分かる!
3分で分かる! シューハート管理図とは 概要解説
シューハート管理図とは、統計的品質管理において、プロセスが安定している状態かどうかを判断するために用いられるグラフの一種です。アメリカのベル研究所のウォルター・シューハート博士によって考案されたことから、この名が付いています。
シューハート管理図の目的
異常な変動の検出: プロセスに異常な原因(例えば、機械の故障、原材料の品質低下など)が発生した場合、データに異常な変動が現れます。シューハート管理図は、この異常な変動を早期に検出し、問題の原因究明と対策に繋げることを目的としています。
プロセスの安定性の維持: プロセスが安定している状態を継続することで、製品の品質を安定させ、顧客満足度を高めることができます。シューハート管理図は、この安定状態を維持するための重要なツールです。
シューハート管理図の仕組み
シューハート管理図は、時間経過とともに測定されたデータをグラフ上にプロットし、中心線と上下の管理限界線と呼ばれる線を引きます。この管理限界線は、過去のデータに基づいて計算され、プロセスが正常に稼働している範囲を示します。
中心線: データの平均値を表します。
管理上限線: 上限の管理限界線を超えるデータは、異常な変動を示す可能性が高いと判断されます。
管理下限線: 下限の管理限界線を超えるデータも、異常な変動を示す可能性が高いと判断されます。
シューハート管理図の種類
シューハート管理図には、測定するデータの種類によって様々な種類があります。代表的なものとしては、以下のものが挙げられます。
個票管理図: 各製品の測定値をそのままプロットする管理図です。
平均と範囲管理図: 一定個数の製品をグループ化し、各グループの平均値と範囲をプロットする管理図です。
メディアンと範囲管理図: 一定個数の製品をグループ化し、各グループの中央値と範囲をプロットする管理図です。
シューハート管理図の活用
シューハート管理図は、製造業だけでなく、サービス業やIT業界など、様々な分野で活用されています。
品質管理: 製品やサービスの品質を安定させる
工程管理: 生産工程の異常を早期に検出し、対策を講じる
改善活動: プロセスの改善点を特定し、改善活動に繋げる
シューハート管理図のメリット
視覚的に異常を検出できる: グラフを見ることで、異常な変動を直感的に把握できます。
早期に問題を発見できる: 異常な変動を早期に発見することで、問題の拡大を防ぎ、コスト削減に繋がります。
客観的な判断ができる: 統計的な手法に基づいて判断するため、主観的な判断を排除できます。
シューハート管理図とは
管理図は、工程が管理された安定な状態になっているかを調べるため、または工程を管理し、安定な状態を維持するために用いられる、管理線の入った折れ線グラフです。
その構造は下記のグラフのように一本の中心線(CL)とその上下に一対の管理限界線(UCL、LCL)から構成されている。
英語: control chart
中国語:控制图
工程の状態を表す特性値をプロットした時に管理限界線の中にあり点の並びにクセがなければ工程は管理状態にあると判断します。
管理線には中心線(CL)および上方管理限界線(UCL)と下方管理限界線(LCL)があり、両管理限界線は一般的に標準偏差の三倍の3σを用います。
管理限界から外れる確率は3/1000(0.3%)つまり1000台生産して3個である。
3σ法 中心線 CL(CenterLine) =平均値
上方管理限界線 UCL(Uper Cntrorl limt) =平均値+3×標準偏差(σ)
下方管理限界線 LCL(Lper Cntrorl limt) =平均値-3×標準偏差(σ)
シューハート管理図 具体的事例
・管理限界線から外れている。工程が異常である
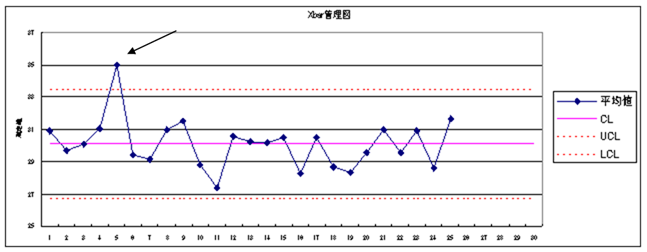
x管理図の管理限界線から外れている
また、点の並び方が連続して並んでいる場合も工程が異常と判断される。
下記の図が具体的事例である。
・連続して同じ方向に点が並んでいる、工程が異常である。
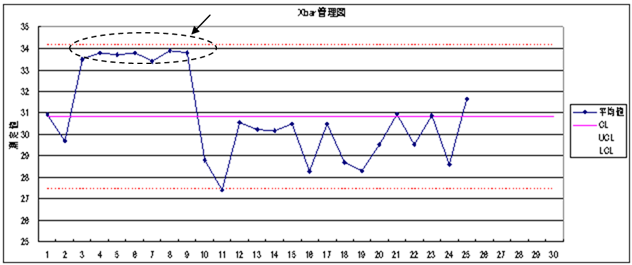
x管理図の点が連続
シューハート管理図の種類
管理図には大別して計量値管理図と計数値管理図に大別されます。
計量値管理図には、Xバー-R管理図、XーRs管理図、 Xメジアン-R管理図がありま
す。
また、計数値管理図には、P管理図とPn管理図、C管理図、U管理図があります。
シューハート管理限界線を計算するための係数表
管理図の管理限界値は総平均の±3σであり、これは平均値の中心極限定理と正規分布の性質を利用しています。
管理限界値を算出する方法には3×標準偏差と係数による推定の2つが存在しますがどちらも同じような値を示しますががコンピューターが手軽に使用きる現在は標準偏差から計算する方法の方が簡単であり、わざわざ 係数表からA2.D4を求めて計算する必要はありません、不要です。
何故、管理限界線を計算するためを係数表するのか?
管理図を作ったシューハート博士は20世紀前半には手軽に使えるコンピューターがない時代であり、計算尺を使用した手計算でもかなり手間がかかります。
つまり、各値を平均から引いて、それぞれ二乗して、全て足し合わせて、自由度で割って、平方根をとる、時間がかかり、計算ミスも発生しやすいです。
そこで、係数を使ったこの方法であれば、算出するのは平均と範囲(最大-最小)だけになるので、現場でも簡単に計算、計算出来ます。
つまりコンピューターがない時代には管理限界線を計算するためを係数表が必要でした。
Xbar-R 管理図 作り方
代表的なXbar-R管理図のつくり方は、次のようになっています。
データーサンプリング
ある品質特性について、同じ工程の生産ロットの検査データを20群以上集
めます。
並べ替え&平均値Xbarと範囲R算出
集めたデータを生産順ごとに並べ、群ごとの平均値Xbarと範囲Rを計算します。
中心線 CL 算出
データの総平均Xbarを計算します。
この総平均Xbarが、Xbar管理図の中心線(CL)となります。次に、範囲Rの
平均値Rbarを計算します。この平均値RbarがR管理図の中心線となります。
なお、 A²はロットごとの抜取検査数で決まる係数です。
Xbar-R管理図の上方管理限界線と下方管理限界線を計算
Xbar-R管理図の上方管理限界線と下方管理限界線を計算します。
UCL=Xbar+A²×Rbar
LCL=Xbar-A²XRbar
R管理図の上方管理限界線と下方管理限界線
⑤R管理図の上方管理限界線と下方管理限界線を計算します。
UCL=D4一Rbar
LCL=D3×Rbar
なお、D4,D3はロットごとの抜取検査数で決まる係数ですが、ロットの抜
取検査数が6個以下の場合は、D3の値はほぼゼロに近いため考慮しません。
シューハート管理図の目的 | 解析用と管理用
管理図の目的は工程内で異常が発生した場合に早期に工程の異常を検知するための図でありヒストグラム、散布図では困難な時間的変化を簡単な方法で知ることができる。
管理図は使用目的別に解析用と管理用がある。
解析用・・ 工程の状態が把握できていない場合それを調査する為にする。
管理用・・ 工程が安定状態になり品質の維持継続を目的として使用。
X-Rs管理図とは
サンプル1個だけのデータで,管理図を作成するのがX-Rs管理図です。
作り方は,Xbar-R管理図と同じですがデータが1個しかないので平均値も範囲も計算する必要がありません。
その代わり平均値としてはサンプル1個のデータ,範囲の代わりとしては一つ前のデーターとの差分Rs(移動範囲)を使います。データが少ないので感度は低いが,サンプリングにかかる手間が省略できます。
下記のような場合に用いられます。
・ 決められた工程から,1 個の測定値しか得られない。
・決められた工程の内部は均一であって,多くの測定値をとっても意味がない。
・測定値を得るのに時間や経費がかかり,現実には 1 個の測定値しか得られない。
X-Rs管理図の作り方
データ並べ替え
少なくとも 20~25 群からそれぞれ一つずつのサンプルをとり測定、データを時間順に並べ替える。
差分Rs(移動範囲)を計算する。
移動範囲 Rs の計算:
互いに相隣る二つの測定値の差(絶対値)を移動範囲 Rs という.
すなわち
Rs=|(第i番目の測定値)|ー|((第i +1)番の目測定値))|
Xの平均とRsの平均
Xの平均とRsの平均を計算します。
ここに,ΣX:測定値の総和
k:測定値の数
有効けた数:測定値のけたより 2 けた下まで求める.
ここに,ΣRs:移動範囲の総和
K-1:移動範囲の数
有効けた数:測定値のけたより 2 けた下まで求める.
管理限界を求める
X 管理図の管理限界は次式によって計算する.
有効けた数:平均値Xのけたより 1 けた下まで求める.
R管理図の管理限界は次式によって計算する.
有効けた数:Rsのけたより 1 けた下まで求める.
管理図用紙に記入
1)管理図用紙の縦軸に X と Rs を目盛り,横軸に測定値の番号を目盛る.
2)X,Rs を上下に対応させてプロットする.第 1 番目のプロットは X だけで Rs はなく,Rs のプロットは第 2 番目から始まる.
3)管理線を記入する.
・中心線 X は実線とし,数値を付記する.
・UCL,LCL は解析用は破線とし,管理用は一点鎖線とし,数値を付記する.
pn管理図とは?
工程を不良個数によって管理する場合で,サンプルの大きさが一定の場合に用いる。またこの場合,良品個数とか,2級品個数などでも適用できる。
pはロットの不良率,nは検査台数です、因ってpnは不良の個数です。
サップルの大きさが一定でない場合はp管理図を用いる。
pn管理図の作り方
pn管理図 データー収集
データのとり方はだいたい平均としてサンプル中に1~5個位の不良個数が含まれるような大きさのサンプルを少くとも約20~25群をとり測定検査して不良個数pnを調べる。
サンプルの大きさの見当をつけるには,不良率pを予想して,サンプル中に1~5個の不良が含まれるようにする。すなわち,
pn=1~5 n=1/p~5/p
たとえば,不良百分率がだいたい5%位と予想されるなら
n=1/0.05~5/0.05=20~100とする。
中心線 管理限界線 算出
ここに
pn:各群の不良個数
∑pn :不良個数の総和
k:群の数
管理限界を次式によって計算する。
計算のけた数は小数点以下1けたまで求めておけばよい
X,すなわち工程平均不良率は次式によって求める。
pn管理図事例
ある部品のショットブラストエ程で 部品120個ずつ表面処理加工を行っているが,この工程を管理するために外観検査による120個ずつの表面仕上り不良の数をしらべた。このデータおよび管理図は表3.4および図3.4のとおりである。
この管理図では限界線からとび出す点はなく,また並び方にくせもないので,この工程は管理状態にあることがわかる。
Pn管理図 とnp管理図 違い
色々な文献、サイトでPn管理図とnp管理図が記載されているがPn管理図とnp管理図は同じ管理図です、正式にはnp管理図。
JISハンドブック「品質管理」では不適合品数を用いて工程を評価するための管理図、群の大きさが一定の場合に用いると記載されている。
英語では“n”umber of nonconforming items chart
英語版のwikipediaの管理図の説明ではnp-chartと記載されている。
関連用語:np管理図
p管理図とは
p管理図は工程を不良率pによって管理する場合に用いる。サンプルの大きさは必ずしも一定でなくてよい。作り方はpn管理図とほぽ同様であるが,ただ管理限界の計算式が若干異なりサンプルの大きさが異なるときはnによって限界の幅が変る。
p管理図 作り方
データのとり方
だいたい平均としてサンプル中に1~5個位の不良個数が含まれるような大きさのサンプルを少くとも約20~25群とり測定検査して不良個数をしらべる。
pの計算
各群ごとの不良率pを計算する。これを一般式で表わすと
p=pn/n
ここに pn:サンプル中の不良個数
n:一群のサンプルの大きさ
備考: 管理図は,不良率をパーセントで表わしても,あるいは小数のまま用い
ても,いずれでもよい。
p管理線の計算
管理図に記入したデータについて,管理線を計算する。
中心線 pbar=∑pn/∑n
ここに∑pn:不良個数の総和
∑n:検査個数の総和
備考:ここで求める中心線は,各群の不良率の算術平均ではない。
管理限界は,次の公式によって計算する。
一般に不良率pのけたよりも1けた下まで求めておく。
p管理図用紙に記入
p管理図用紙を用意し,もとめたpの値を打点記入する。
さらに管理線を記入する。中心線βの値を実線で,UCLとLCLを破線で記入し数値を付記する。
サンプルの人きさが群ごとに違う場合は,記人した限界線は中心線に対して凸凹となる。
p管理状態 確認
p管理図の状態に問題がないか確認し、異常があった場合、すぐに原因を究明する。
pn管理図事例
表3.4のデータでp管理図を作ると下図のようになる。
c管理図とは
欠点を発生する可能性のあるひろがり(空間的,時間的)が一定の製品中の欠点数,たとえば一定の大きさの鉄板のきずの数,一定の大きさの織物の織むら,一定の長さの電線の表面きずなどで工程を管理する場合に用いる。
品物1個中の欠点数が少ない場合には,一定個数の品物の中の欠点数を用いてもよい、一定期間中に発生した故障件数,事故件数などを管理する場合にも応用できる。
c管理図の作り方
データのとり方
一定の大きさのサンプルを少くとも約20~25群とり,各群中の欠点数Cを調べる。サンプルの大きさは,だいたい平均としてサンプル中1~5個位の欠点数が含まれるようにする。
c管理図 管理線の計算
管理図に記入したデータについて管理線を計算する。
中心線 cbar=∑c/k
ここに ∑c:欠点数の総和
k=群の数
管理限界線は次の公式で計算する。
計算のけた数は小数点以下1けたまで求めておく。
備考:LCLは計算の結果負になることがあるが,この場合にはLCLは考えない。
c管理図 CL,UCLとLCLを記入
管理図用紙を用意し,求めたcの値を打点記入する。
さらに管理線を記入する。中心線の値を実線で,UCLとLCLの値を破線で記入し数値を付記する。
管理状態 確認
c管理図の状態に問題がないか確認し、異常があった場合、すぐに原因を究明する。
c管理図 事例
建材としての規格サイズで,大きさ一定のパネル板の欠点数をとりあげて,この工程を管理するための管理図を作成した。データ および管理図は表3.7,図3.7のとおりである。
管理限界からとび出している点があり,この工程は管理状態にあるとはいえない。
u管理図とは
製品の欠点を発生する可能性のあるひろがりが,いろいろ変化する場合に製品の一定単位を定めて,その一単位あたりの欠点数,たとえば一定面積あたりの織物の織むら,一定長さのあたりのエナメル線のピンホールなどで工程を管理する場合に用いる。
u管理図の作り方
データのとり方
少くとも約20~25群のサンプルをとり,サンプルの大きさ(長さ,面積,時間など)と,サンプル中の欠点数をしらべる。
サンプルの大きさは,だいたい平均としてサンプル中に1~5個の欠点数が含まれるようにする。
uの計算
各群ごとの単位あたりの欠点数uを求める。
これを一般式で表わすと
u=c/n ここに
c:サンプル中の欠点数
n :サンプルの大きさ
たとえば1500 m のエナメル線を検査し,ピンホールが5個あったとする。1000 mを単位とすれば,1500 m は1.5単位であるので単位あたりの欠点数は次のように計算される。
n=1500/1000=15 u=5/15=3.33
備考: 500 m を単位とすれば,単位あたりの欠点数はつぎのようになる。
n=1500/500=3.0
u=5/3.0=1.67
管理線の計算
管理図に記入したデータについて管理線を計算する。
中心線 ubar=∑c/∑n
ここに ∑c :欠点数の総和
∑n:サンプルの人きさの総和
管理限界は次の公式によって計算する。
備考:LCLは計算の結果負になることがあるがこの場合にはLCLは考えない。
管理図に記入
管理図用紙を用意し,手順2で求めたuの値を打点記入する。
さらに管理線を記入する。中心線u平均の値を実線で,UCLとICLの値を
破線で記入し数値を付記する。
管理状態 確認
u管理図の状態に問題がないか確認し、異常があった場合、すぐに原因を究明する。
u管理図 事例
表装紙のプリントエ程を管理するため,プリント不良個所の数をしらべる。サンプルの幅は一定であるが長さが種々変わるので,単位長さあたりのプリント不良個所の数を用いる。
この場合,nは最小1.0から最大2.0まで変動しているが,nbar=1.39に対し±50%(0.7~2.1)以内におさまっているので,簡便法を用いて,管理限界は
UCL=Ubar+3√(Ubar/n)=6.61
LCL=-
となる。
No121の点は,nによる管理限界で判定すると,わずかながら限界から点がとび出している。しかし、精密計算した限界を適用すると管理限界内におさまっている。
したがってこの工程は管理状態にあると判断できる。
データを表3.8に,管理図を図3.8に示す。
R管理図とS管理図の違い
工程の安定性を評価するときに使われる「管理図」ですが代表的な管理図としてR管理図とS管理図がります。
これらは、Xbar-R管理図やXbar-S管理図に使われるますが具体的に何がちがうのかを解説します。
R管理図とS管理図のグラフ比較
左がR管理図、右がS管理図となります。
しかし、R管理図かS管理図かはグラフの結果だけを見ても判断できません。
R管理図とS管理図の違いはR管理図は「サンプル範囲」S管理図は「サンプル標準偏差」です。
R管理図とは、R = Range(範囲)の頭文字です。
S管理図とは、S = standard deviation(標準偏差)の頭文字です。
エクセル Xbar-R管理図 フリー テンプレート
下記にエクセルで作成したXbar-R管理図があります、ご自由にダウンロードしてご使用ください。
エクセル Xbar-R管理図管理図の作成
上記の エクセルファイル Xbar-R管理図を基に説明します。
DATA入力
入力DATAシートに群ごとのデーターを入力。
Xbar管理限界線 R管理限界線 自動計算
Xbar管理限界線及びR管理限界線のUCL LCLが自動で計算されます。
Xbar-R管理図管理図の折れ線グラフ 作成
各群のデーターのプロット、折れ線およびCL、UCL、LCLが自動で表示される。
記録項目に記入
日付、データー群数、項目等を記入する。
エクセル pn管理図 フリー テンプレート
下記にエクセルで作成したpn管理図があります、ご自由にダウンロードしてご使用ください。
エクセル pn管理図管理図の作成
上記の エクセルファイル pn管理図を基に説明します。
DATA入力
入力DATAシートに不良個数データーを入力。
pn管理図 限界線 R管理限界線 自動計算
Xbar管理限界線及びR管理限界線のUCL LCLが自動で計算されます。
pn管理図管理図の折れ線グラフ 作成
管理図の見方、活用の仕方
管理図を有効に活用するには、管理図に打点した点の動きから、工程が安定状態にあるかどうかを判定し、異常と判断した場合には、異常が発生した原因をつかみ、是正処置を取ることが大切です。
工程の判定基準
管理図から見る、工程の判定基準工程が安定状態にあるかどうかについてですが、次のような場合を工程に異常があると判定します。
点が管理限界線の外側にある場合
点が管理限界線の内側にあっても、以下のように点の並び方にクセがある場合
中心線に対して、一方の側に連続して7点が並んでいる
連続する7点が、上昇または下降している
一定間隔で周期性を持っている
連続する3点中2点が、限界線近くにある。
限界線の近くとは、中心線と限界線を3等分して、そのいちばん外側の領域にあること
連続する多くの点が、中心線に接近している。
中心線に接近しているとは、中心線と限界線を3等分して、そのいちばん内側の領域にあることなお、判定基準は図面規格値ではなく、管理限界線を用います。図面規格値と管理限界線とを混同しないようにしてください。
管理図の活用|異常があればすぐ対応
データを溜めておいて、一括して管理図にデータを記載している例を見受けます。しかしこれでは、工程を管理するための管理図ではなく、見せるための管理図になっているといわざるを得ません。
真に工程を管理するためには、ロットごとにデータを取ったらすぐに管理図に打点し、工程に異常があると判定したら即座に異常を取り除くアクションを取り、工程を安定した状態に維持していくことが大切です。
あわてものの誤りとぼんやりものの誤り
管理限界線と規格値線を混同しないこと。
管理限界線は工程が管理、安定状態にあるのかどうかを判定するためのもの。
個々の製品の合格、不合格を判定するためのものではありません。
規格値は合格、不合格を判定するためのもので工程の管理状態を把握するものではありません
管理図における判断の誤り
統計を用いて管理を行う場合、常に次の2つの誤りを犯す危険があることを理解して管理図
を使用しなければならない。
第一種の誤り(あわてものの誤り)
異常が発生していないのに異常が発生したと判断する誤り。
第二種の誤り(ぼんやりものの誤り)
異常が発生しているのにそれを見過ごす誤り。
管理図においては一般的に管理限界線は管理特性の分布の標準偏差の3倍のところに設定している。
これは特性値が正規分布に従うとき限界から外れる確率が0.3%になるということである。
すなわち第一種の誤りを犯す確率が0.003あるということである。
Xbar-R管理図による工程解析|数理
管理図で集められた全データーのヒストグラムと各群(ロット)のヒストグラムの関係は下記の図のようになっており、全データーのヒストグラムのバラツキは群内バラツキと群間バラツキとで構成されている。
群内バラツキ: 各群(ロット)内のばらつき、測定誤差等が含まれる
群間バラツキ: 各群(ロット)間のバラツキ、日々サンプルを抜き取り管理している場合は日々ごとのバラツキを表す。
ロットをある条件でロット分けした場合はバラツキは大きくなるがランダムにロット分けした際はバラツキが小さくなる。
Xbar管理図 (群内変動と群間変動)
Xbar管理図は図のように各群の平均値のバラツキをグラフ化したものあり群間バラツキから工程の異常を検知するためのものであり、その管理限界線は群内のバラツキを基に計算されており群内バラツキを網の大ききとしてその網目に引っかかったロットが異常と判断する。
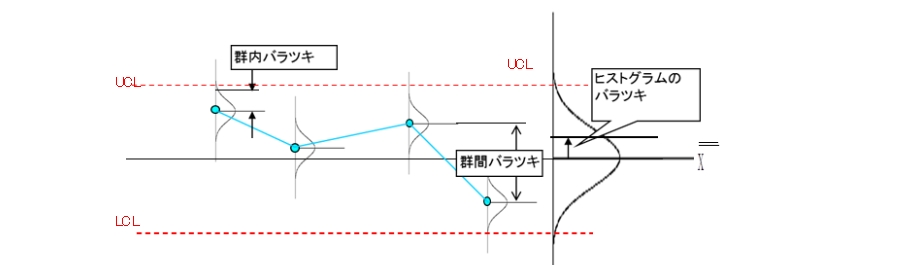
Xbar管理図
R管理図は群内のバラツキになんらかの原因で異常な群内バラツキが発生した場合に異常を検知する為の管理図である、すなわち全体の群が均一であるかどうかを管理するために用いる。
群内バラツキは下記の式より計算される。
管理図 事例1:
ある部品が20ロットあり各ロットn=5のサンプルを抜き取り測定を行い管理図をかいたところ下記にデーターが得られた。
ロット内バラツキσw: R管理図より下記の式で求まる。
管理図 事例2:
下記のような工程があり金属棒を4台の機械にてカットしてある部品を生産していた。
ある長さをn=4のサンプリンングで測定して管理図を描いたところ下記の管理図となった
Xbar、R管理図とも管理状態にあるので安定しておりそのばらつきは次のようなものに分けられる。
機械バラツキ(機械毎の設定、条件の違い):σk
素材のバラツキ(素材が変わることによるバラツキ):σb
ロット内バラツキ(一本の素材から作った製品間のバラツキ):σw
このうちどの要因が一番大きく影響しているかを計算してみるとR管理図より下記の式が導かれる
R管理図より
次にσk、σb、σwを求めるためにサンプルのとり方を下図のように機械ごとに1ロットn=5でサンプリングして測定をおこなう。
いずれの機械についてものどうような状態であったので機械No1のみの管理図のみを記載した。
R管理図は管理状態を示していることからロット内のバラツキは(一本の素材から作られるもののバラツキ)は素材が変わってもあまり変化しない。
しかしXbar管理図は限界外の点が多く群間のバラツキが大きいと判断される。
この場合同一機械のバラツキなので群間のバラツキは素材間のバラツキということのなる。
すなわち素材がかわると寸法が大きく変わることがわかる。
また、今回の管理図では
群間のバラツキ:σb=素材間(ロット間)のバラツキ
群内バラツキ:σw=一本の素材から作った製品間のバラツキ
となっている。そこでこれらの大きさを求めると
全データーを基にヒストグラムを作成してσを求めると
σ=27.0
よって全データーの分散σh2=ロット内バラツキσw2+ロット間バラツキσb2から
σb2=σh2-σw2≒(27)2-(10.7)2=24.82
また、機械のばらつきが含まれた前のR管理図(n=4サンプル)より
このようにしてすべてのバラツキが分解して推定することができた。
この結果から製品のばらつきには素材間のバラツキが大きく影響していることがわかるので
製品のバラツキを減少させるためには素材間の差をなくすことが一番の解決策である。
シューハート管理図の注意点とよくある誤り
シューハート管理図は、品質管理において非常に重要なツールですが、正しく理解し、運用しないと誤った判断をしてしまう可能性があります。ここでは、シューハート管理図の注意点とよくある誤りについて解説します。
注意点
- データの正確性: 管理図にプロットするデータは、正確で一貫性のあるものである必要があります。誤ったデータや外れ値は、誤った判断につながる可能性があります。
- サンプルサイズ: サンプルサイズは、管理図の精度に影響を与えます。一般的に、サンプルサイズが大きいほど、管理図の精度が高くなります。
- 管理限界線の設定: 管理限界線は、工程の安定性を評価するための基準となります。適切な管理限界線を設定しないと、誤った信号を出してしまう可能性があります。
- 異常信号の解釈: 管理図に異常信号が出た場合、必ずしも工程に異常が発生しているとは限りません。他の要因(測定誤差など)が原因である可能性も考えられます。
- 管理図の種類の選択: 測定データの種類(計量値、計数値)や工程の特性に応じて、適切な管理図の種類を選択する必要があります。
- 管理図の運用: 管理図は、単に作成するだけでなく、定期的に見直し、必要に応じて修正することが重要です。
よくある誤り
- 異常信号が出たらすぐに工程を停止する: 異常信号が出た場合、必ずしも工程を停止する必要はありません。まずは、異常の原因を特定し、必要な対策を講じる必要があります。
- 管理図だけで工程を判断する: 管理図は、工程の状態を評価するためのツールの一つです。他の情報(ヒストグラム、散布図など)も合わせて分析し、総合的に判断する必要があります。
- 管理限界線を頻繁に変更する: 管理限界線を頻繁に変更すると、管理図の信頼性が低下します。特別な理由がない限り、管理限界線は安定して維持することが望ましいです。
- 管理図の作成が目的化する: 管理図を作成することが目的になり、改善活動につながらないことがあります。管理図は、改善活動のためのツールであることを忘れてはいけません。
その他
- 第一種の誤り、第二種の誤り: 管理図の運用においては、第一種の誤り(正常な工程を異常と判断してしまう)と、第二種の誤り(異常な工程を正常と判断してしまう)のバランスを考慮する必要があります。
- 管理図の種類: X-R管理図、I-MR管理図、u管理図、np管理図など、様々な種類の管理図があります。それぞれの管理図の特徴を理解し、適切な管理図を選択することが重要です。
シューハート管理図の品質管理における具体的な活用
シューハート管理図は、製造業をはじめとする様々な分野で、製品やサービスの品質を安定的に維持するために広く活用されています。ここでは、シューハート管理図の実際の導入事例をいくつかご紹介します。
導入事例
製造業
- 自動車部品製造:
- 各工程での製品寸法や表面粗さのデータを取得し、管理図を作成。
- 管理限界線を越える異常なデータが出現した場合、原因を究明し、工程改善を実施。
- 結果として、製品不良率が大幅に減少し、品質が安定。
- 食品製造:
- 製品の重量や成分含有量を測定し、管理図を作成。
- 食中毒発生のリスクを低減するため、細菌数や温度を監視。
- 顧客からのクレーム件数が減少。
- 電子部品製造:
- 半導体製品の不良率を監視し、管理図を作成。
- 異常パターンを早期に検知することで、製造工程の停止時間を短縮。
- 製品品質の向上と生産性向上に貢献。
サービス業
- コールセンター:
- 顧客対応時間や解決率を測定し、管理図を作成。
- 顧客満足度向上のため、対応品質の安定化を図る。
- オペレーターの教育プログラムの改善に役立てる。
- 病院:
- 患者の待ち時間や検査結果の報告時間などを測定し、管理図を作成。
- 医療サービスの品質向上と患者満足度向上に繋げる。
導入による効果
- 品質の安定化:
- 偶然変動と異常変動を明確に分けることで、品質のばらつきを抑制。
- 製品不良率や顧客クレームの減少に繋がる。
- 問題の早期発見:
- 異常なデータを早期に検知することで、問題の原因を迅速に特定し、対策を講じることができる。
- 生産性向上:
- 工程の安定化により、無駄な作業や再作業を削減し、生産性を向上させる。
- コスト削減:
- 品質不良による損失を減らし、コスト削減に貢献。
導入のポイント
- 適切なデータの収集:
- 管理図を作成するために、必要なデータを正確に収集することが重要。
- 管理限界線の設定:
- データの特性に合わせて、適切な管理限界線を設定する。
- 定期的な見直し:
- プロセスが変化した場合や、新しいデータが得られた場合は、管理図を定期的に見直し、必要に応じて修正する。
- 全従業員の意識改革:
- 管理図を活用して、全従業員が品質意識を高めることが重要。
管理図 統計ソフト
Xbar管理図、R管理図等が簡単に作成できる統計ソフトの紹介です。
エクセル統計
長さや重さなどの計量値が1回の検査で複数得られる場合に用います。毎回の検査群ごとに平均値(Xbar)と範囲(Range)を求め、Xbar管理図とR管理図を同時に作成します。
検査のデータは、検査回数(行)×各回の検査データの個数(列)にまとめられている必要があります。
関連サイト:エクセル統計 Xbar-R管理図 : Xbar-R Chart
まとめ
管理図を活用できれば,規格外れが起きる前に異常を発見し, 早期に手を打つことができます。
生データをプロットするだけのグラフを使っている場合,統計量を使った管理図を作って事前に異常を発見し対策し、早期に工程の安定化に努めてください。
シューハート管理図は、プロセス管理において非常に重要なツールです。このグラフを活用することで、製品の品質向上やコスト削減に貢献することができます。
関連キーワード:
シューハート管理図 統計的品質管理 SPC 管理図 品質管理 工程能力指数
slideshare スライドシェア 無料ダウンロード資料(PDF)
パワーポイントで作成したスライドシェア資料です。
コメント