ヒューマンエラーの対策として有効なポカヨケについて仕組み、種類、事例を、掲載しました、工場、研究所でのヒューマンエラー 防止対策にお役に立ててください。
更に『お金のかからない安全衛生~ヒューマンエラーの改善』については下記の記事を参考願います、工場等での安全衛生事故に役に立ちます。
2024年版 トヨタ式ポカヨケ対策【音声解説】
トヨタ式ポカヨケ対策の解説動画です。
- 3分で分かる! AIでポカヨケ改善案を出だす!
- ポカヨケとはどういう意味? | 安全対策、事例、装置
- 心理的なヒューマンエラー | ポカミスの原因&対策
- ポカヨケの由来、語源
- ポカヨケの考え方
- トヨタ生産方式のポカヨケ
- フールプルーフ、フェイルセーフとポカヨケの違いは?
- ポカヨケと5Sの関係:相乗効果で品質向上を
- 検査の分類 ~ポカヨケシステムの歩み
- ポカヨケ装置の種類
- ポカヨケ装置 検知センサーの種類
- ポカヨケ装置の動画事例
- ポカヨケの分析手法
- ポカヨケ アプリ、ツール、システムとは
- 主なタイプ別一覧
- ポカヨケ対応アプリ POKAYOKE® Premiumとは
- ポカヨケとAIの活用:新たな品質管理の時代へ
- ポカヨケによる安全で高品質な社会の実現に向けて
- ポカヨケの教育と訓練:安全な職場環境を築くための第一歩
- ポカヨケ導入時の課題と対策
- ポカヨケの効果的な評価方法
- ポカヨケQ&A 上位10選【初心者向けにやさしく解説】
- まとめ
- ポカヨケ対策 Poka yoke 資料 無料 ダウンロード
3分で分かる! AIでポカヨケ改善案を出だす!
【現場改革】AIでポカヨケ改善案を出す方法と注意点
製造現場で長年使われてきた「ポカヨケ(ミス防止)」に、いま新たな風が吹いています。
それが「AI(人工知能)」との組み合わせです。
人間の思い込みや慣れによるヒューマンエラーを防ぐには、経験とカイゼンの積み重ねが不可欠でしたが、
AIの登場で“次の一手”が見えるようになってきたのです。
簡単に、AIでポカヨケの改善案を出す方法と、導入時の注意点について現場目線で解説します。
AIが得意なポカヨケ改善アプローチとは?
AIは「学習」と「予測」が得意です。これを現場に活かすことで、以下のようなポカヨケが可能になります。
カメラ×AIで動作ミスを検出
作業手順通りに動いているかをカメラでモニタリングし、
AIが「手順違反」や「パーツの取り忘れ」をリアルタイムで検知。
例:ネジ締め忘れをカメラで確認 → アラームで警告
作業ログからミス傾向を学習
「どんな作業者が」「いつ」「どんなミスをしやすいか」
過去データからAIが傾向を掴み、リスクの高い作業に注意喚起を提案。
例:新人が朝の時間帯に手順ミス多発 → チェックシート導入を提案
AIチャットで改善案をブレスト
ChatGPTのような生成AIに「現場の課題」を伝えると、斬新なポカヨケアイデアを会話形式で出してくれます。
例:「この装置で部品の向きがよく間違う」と入力 → 向き識別センサーや冶具の提案が返ってくる
導入時の注意点:過信は禁物!
AIは万能ではありません。導入時には以下の点に注意しましょう。
データの質が命
AIは“過去のデータ”から学習します。
誤ったデータや偏った情報では、正確な提案はできません。
✕ 作業ミスの記録がバラバラ → 提案があいまいに
◎ ミスの内容・原因・発生時刻を丁寧に記録 → 精度UP
2. 現場の納得感が必要
「AIがこう言ってるから変えよう」はNG。
現場の声とAIの提案を融合させるファシリテーションが重要です。
3. 継続的な検証が不可欠
AIの提案はあくまで“仮説”。現場で試して、結果を記録し、
さらにAIにフィードバックすることで、改善の質が高まります。
AIは「第二の目」として使おう
AIは、人間が見落としがちなパターンや予兆を見つける「もう一つの目」になります。
でも、最終的に改善を動かすのは現場の力。AIを“頼る”のではなく、“活かす”ことが成功のカギです。
ポカヨケ+AI=未来の現場力。
今日から一歩ずつ、導入を検討してみてはいかがでしょうか?
*具体的なポカヨケ改善提案 事例集については下記の記事を参照願いします。
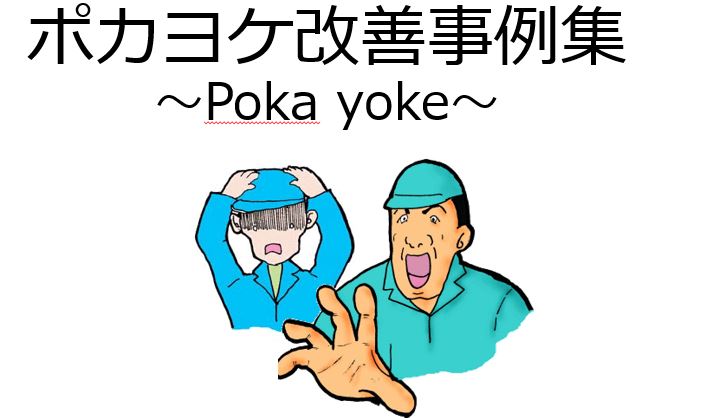
ポカヨケとはどういう意味? | 安全対策、事例、装置
「人間は間違いをおかす動物で、ポカミスを起こしやすい動物であるといわれ、ポカミス対策(ポカヨケ)が必要である。
「ポカヨケ(Poka-Yoke)」は、日本語の「ポカ(うっかりミス)」+「ヨケ(避ける)」を組み合わせた言葉で「人為的なミス(うっかりミス)を未然に防ぐ仕組み」を意味します。
海外でも「ポカヨケ(Poka-Yoke)」は、そのまま 「Poka-Yoke」 という日本語由来の言葉として使われています。特に英語圏の製造業や品質管理の分野では、以下のように理解・使用されています:
海外での「Poka-Yoke」の読み方・使われ方
項目 | 内容 |
---|---|
読み方(英語) | ポーカ・ヨーケ(/ˈpoʊ.kə ˈjoʊ.keɪ/) または単純に「ポカヨーク」に近い発音 |
意味の訳 | Error-proofing(エラープルーフィング) Mistake-proofing(ミステイクプルーフィング) |
用途 | トヨタ生産方式やリーン生産方式の一部として、製造業・医療・ソフトウェアなどでも広く使用 |
関連する表現(英語圏でよく使われる言い換え)
日本語 | 英語での対応語 | 備考 |
---|---|---|
ポカヨケ | Poka-Yoke | 専門用語としてそのまま使用されることが多い |
間違い防止 | Mistake-proofing | わかりやすい一般語。教育・研修などで多用 |
エラー防止 | Error-proofing | システム設計や医療現場などで使われる |
フェイルセーフ | Fail-safe | 大きな事故を防ぐ仕組み全般(やや広義) |
以下に、代表的な言語での表現をまとめました:
各言語における「ポカヨケ」の呼び方と訳語
言語 | 発音・カタカナ表記 | 一般的な訳語 | 説明補足 |
---|---|---|---|
🇨🇳 中国語(簡体) | ポーカー・ヨーク(波卡优可) | 防错装置 / 防错技术(fáng cuò jìshù) | 「ミス防止技術」などと訳されることが多い |
🇪🇸 スペイン語 | ポカ・ジョケ または ポカ・ヨーケ | A prueba de errores / Dispositivo a prueba de errores | 「エラー防止」「ミスの起きない装置」など |
🇰🇷 韓国語 | 포카요케(ポカヨケ) | 실수 방지 장치(シルス パンジ チャンチ) | 「ミス防止装置」などと意訳される |
🇮🇳 ヒンディー語 | पोका-योके(ポーカーヨーケ) | गलती रोकने की तकनीक(galti rokne ki takneek) | 「間違いを防ぐ技術」 |
🇸🇦 アラビア語 | بوكا-يوكي(ブーカ・ユーキ) | تقنية منع الأخطاء (taqniat mani al’akhta’) | 「ミス防止の技術」 |
🇷🇺 ロシア語 | Пока-йоке(ポカ・ヨーケ) | Защита от ошибок / Устройство против ошибок | 「ミス防止」「エラー防止装置」など |
ポカヨケ対策の目的
製造業においてポカヨケ対策をする目的は下記の3点です。
生産性の向上:不良品を低減して生産量を増やす。
製造工程の品質の向上:製品製造工程からできるだけ早く不良品を取り除き流通を防止。
安全確保:現場の作業員の安全を守り、労災を防ぐ
ポカヨケ対策は、次の2点を達成する為に優先にして設計されます。
- 不良品が発生しないこと
- 不良品が流失しないこと
心理的なヒューマンエラー | ポカミスの原因&対策
心理的なヒューマンエラーとは、人間の心理状態や認知機能が原因となって起こるミスや判断の誤りです。物理的な要因(機械の故障など)ではなく、人間の心の中にある要因がミスを引き起こす点が特徴です。
心理的なヒューマンエラーを引き起こす主な要因
- ストレス:
- 仕事の負荷、人間関係のトラブルなど、ストレスは集中力の低下や判断力の誤りを引き起こします。
- 疲労:
- 長時間労働や睡眠不足は、注意力や反応速度を低下させ、ミスを誘発します。
- 飽き:
- 同じ作業の繰り返しは、注意が散漫になり、ミスにつながりやすくなります。
- 焦り:
- 納期が迫ったり、周囲から急かされたりすると、冷静さを失い、安易な判断をしてしまうことがあります。
- プレッシャー:
- 評価される場面や責任が伴う状況では、緊張してミスをしやすくなります。
- 感情:
- 怒り、悲しみ、喜びなどの感情は、判断に影響を与え、ミスを引き起こす可能性があります。
心理的なヒューマンエラーの影響
- 品質低下:
- 製品やサービスの品質が低下し、顧客からのクレームや信頼の失墜につながります。
- 生産性低下:
- ミスの修正や再作業が必要となり、生産性が低下します。
- 事故発生:
- 重大な事故につながる可能性もあります。
- 例えば、医療現場での誤投薬、建設現場での墜落事故など。
- コスト増:
- 不良品発生による廃棄コスト、再作業コスト、顧客への補償コストなどが発生し、経済的な損失につながります。
- 組織への悪影響:
- 組織全体の士気低下、顧客からの信頼喪失、法的責任問題など、組織全体に大きな影響を与える可能性があります。
心理的なヒューマンエラーを防ぐために
- 労働環境の改善:
- 適切な休憩時間の設定、照明の調整、騒音の軽減など、快適な作業環境を整える。
- 作業負荷の軽減:
- 作業手順の簡素化、人員配置の最適化など、作業負荷を軽減する。
- 教育・訓練:
- 安全に関する教育、マニュアルの徹底など、従業員のスキルアップを図る。
- 心理的なサポート:
- カウンセリングやストレスマネジメントの研修など、従業員の心の健康をサポートする。
- ポカヨケの導入:
- ヒューマンエラーが起こりやすい作業工程に、ポカヨケ(ミス防止対策)を導入する。
ヒューマンエラーの種類【ポカミスはなぜ起こる?】
ポカヨケ対策を考える上で、「なぜヒューマンエラーが発生したのか」原因を追求することが再発防止に役立ちます。
まずヒューマンエラーの発生は次のように分類できます。
ミステイク:Mistake
見間違い、聞き違い、勘違いなどのミスは人間の認知システムの特性によって不可避的に発生する。しかし、それは認知システムに欠陥があるためではない。人間の認知システムはコンピュータのように入力情報を処理して、認識、決定というアウトプットを出力する。目や耳はセンサーである。
コンピューターとの大きな違いは、情報が不完全でもあいまいでも、前例や状況、文脈を手がかりにしてとりあえずのアウトプットを出してくれることだ。そうでなければ、人類は生存競争を生き延びられなかった。
ミステイクは人間の素晴らしい証知能力の副作用である。
スリップ(錯誤):Slip
スリップ:意図した動作は正しかったのに、意図しない動作のミスをおかしてしまうのがスリップである。慣れた動作は体が記憶している。何かしようと意図が形成されるとその意図を実現するのに適当な動作のパターン(心理学では行為のスキーマと呼ぶ)が活性化し動作を開始するきっかけ(「トリガー」=外からの刺激、前の動作の終了)とともに行為スキーマが実行される。
この過程の中で、いつも動作のトリガーとなっている刺激か来ると意図がないのに動作してしまったり(例=もっと上の階に行こうとしていたのに自分のオフィスかある階でエレベータのドアが開くと降りてしまう)
意図の形成から後の動作はほとんど無意識に遂行されるために、十分に意識しないで体を動かす(あるいは動いてしまう)からミスを起こすのである。しかし、意識しながら動作をすると動きが遅くなるしスムーズにつながらない。あらゆる熟練作業は意図だけを意識すれば後は勝手に体が動く。そうでなければ仕事にならない。
つまり、行為のスリップも行為の熟練に伴う副作用なのである。
ラプス(失念):Lapse
記憶には覚える段階、覚えた情報を保持する段階。そして、覚えている情報を取り出す(思い出す)ステップがある。
覚えられない。覚えたのに忘れてしまった。思い出そうとしても思い出せないという失敗はそれほど問題ではない。
事故に結びつきやすいのは思い出すことを忘れてしまうというラプス「失念」である。行うべき行為の予定をいったん記憶し、それを忘れたわけではないのに適切なタイミングで思いだせないのが失念である。
連絡のし忘れ、引き継ぎ事項の漏れ、最後の手順のやり忘れなどは重大事故につながっている。
しかし、必要な時に自発的に全てことを思い出す為にはメモやタイマー、チェックリストなどで頭の外側に記憶をとどめておく工夫が必要である。
工場におけるヒューマンエラー対策とは
工場では次のようなヒューマンエラー対策として様々な取り組みをしています。
- 業務の単純化・平準化:覚えやすく忘れにくいシンプルな業務にし、属人的にしない
- 作業環境の整備:工場内を集中力を保ちやすい温度・湿度、確認しやすい明るさを保つ
- 作業者のスキル向上:教育・訓練を実施して従業員のスキルを上げる
- 確認の習慣づけ:熟練者でも手順を守り確認を徹底する
- コミュニケーションの強化:ルール違反をしにくい風土を作る
ポカヨケの由来、語源
ポカヨケはトヨタ生産方式の基本概念の一つであり、ポカヨケの基本コンセプトは新郷重夫氏が創案しており、新郷氏の著書により日本国外でもポカヨケは広まり、結果Poka-yokeとして製造業の分野では国外でも通じる言葉となった。
当初は「バカヨケ」と呼ばれたが、当時の女性のオペレータが「私はそんなにバカですか!」と泣き泣き訴えたそうで、すぐに「ポカヨケ」に言い換えたのとの事です。
「ポカ」とは、うっかりミスやぼんやりミス、さらには早合点、ミスなどを自働的に「ヨケル」という意味のことばで元々は囲碁・将棋の世界で、通常は考えられない悪手を指すことを「ポカ」と呼ぶんでいのが由来です。
“Poka-Yoke(ポカヨケ)”とは、日本語で「うっかりミスの防止」を意味する言葉で、1960年代に自動車製造業界で使われはじめました。ポカヨケというコンセプトは、品質工学の技術者である新郷重夫氏によって構築されたものです。
新郷氏は当時、コンサルをしており、名古屋の山田電機でプッシュボタン作業の組み立てる際にバネを入れ忘れるといったミスの問題を検討していました。解決策は、スイッチ組み立ての作業工程を改善し、2つのステップで成り立つようにするというものでした。
1. 2つのバネをバネホルダーに置くことでそれらのバネを入れる準備を行う。
2. その2つのバネをバネホルダーから取り出し、スイッチに入れる。
改善後、スイッチを組み立てる工程は長くなるが製造中のミスをなくすことが可能となり、結果としてより質の高い製品を生産することができるようになった。
ポカヨケは、現在でもソフトウェアインターフェースにおいて使われています。
例えば無料のホームページ作成ソフト「WordPress(ワードプレス)」には、間違って記事を削除してしまうことを防ぐ機能が用意されています。
ポカヨケの目的は、エラーをすぐに検出して修正できるようにプロセスを設計し、ヒュマンエラーを排除することです。
ポカヨケの考え方
しかしどんなにマニュアルを整備し、環境を整えたところで、ヒューマンエラーをゼロにするのは不可能です。
製造業では、物理的にミスが発生しない仕組み、ミスを発見しやすい仕組み、ミスの影響を最小限にする仕組みづくりを追求をしています。
ポカヨケの基本的な考え方
- 人がミスしないようにする
- 人がミスしたらすぐ発見されるようにする
- 人がミスしたらときに、影響範囲をできる限り少なくする
トヨタ生産方式のポカヨケ
トヨタ生産方式のポカヨケの定義は下記の内容あり、『発生防止のポカヨケ』と『流出防止のポカヨケ』の2種類があります。
ポカヨケとは工程内に設置されて、作業者のウッカリミス(ポカ)を避けて(ヨケ)くれる仕組みのことです。作業者は 標準作業通りの一連の作業をするだけでいいのです。このポカヨケにより工数を一切かけずに全数検査が可能になったため、価格競争力を減ずることなく、品質を格段に向上させることに成功したのです。
ポカヨケには、「不良自体を発生させないポカヨケ(発生防止のポカヨケ)」と「不良は1つ作ってしまうが、それを発見しそれ以上の不良を発生させないポカヨケ(流出防止のポカヨケ)」の2種類に大別されます。
またもう1つの分類としては、電気を使用するものとしないものに分けることができます。電気を使用するものは、毎日始業時にポカヨケの機能が有効に動くかどうかチェックしなければなりません。しかし電気を使用しないものはその必要がないので、まったく工数がかかりません。もちろん電気を使用しないポカヨケの方が優れているのは言うまでもありません。引用先:トヨタの生産方式に関して
参考資料:全図解トヨタ生産工場ポカヨケのすべて
フールプルーフ、フェイルセーフとポカヨケの違いは?
フールプルーフは、人間の操作ミスを防ぐための機能のことを指します。
ポカヨケもヒューマンエラーを防止する機能です。
欧米では、Fool Proof(フールプルーフ)と呼ばれていたので、日本では直訳して「バカヨケ」と呼んでいましたが表現方法が悪いのでポカミスを避ける意味の『ポカヨケ』に変更になりました。
一方、フェイルセーフは、何らかの故障が発生しても、システムが正常に機能し続け、安全に停止できるように設計された機能のことを指します。 つまり、故障が発生した場合でも、システムが安全に動作し続けるようにすることが目的です。
ポカヨケと5Sの関係:相乗効果で品質向上を
ポカヨケと5Sは、ともに製造現場の品質向上に不可欠な要素であり、密接な関係があります。それぞれが独立して効果を発揮するだけでなく、両者を組み合わせることで、より高いレベルの品質管理を実現することができます。
ポカヨケと5Sのそれぞれの役割
- ポカヨケ:
- 人間のミスを未然に防ぐための仕組みや装置のことです。
- ミスの原因を根本から取り除き、不良品発生を防止します。
- 5S:
- 整理、整頓、清掃、清潔、躾の5つの要素からなる職場環境改善活動です。
- 作業環境を整備し、効率的な作業を可能にします。
ポカヨケと5Sの連携による効果
- ポカヨケの有効性の向上:
- 5Sによって整理された清潔な環境は、ポカヨケ装置の機能を最大限に引き出し、誤動作や見落としを防止します。
- 例えば、工具の定位置化により、必要な工具をすぐに取り出せるようになり、間違った工具の使用を防ぎます。
- ポカヨケの発見を促進:
- 5S活動を通じて、現場の改善点や潜在的な問題点が可視化されます。
- これにより、新たなポカヨケの導入や既存のポカヨケの改善につながります。
- 品質意識の向上:
- 5S活動は、従業員の意識改革を促し、全員が品質向上に貢献するという共通の目標を持つことにつながります。
- このような意識改革は、ポカヨケの有効性を高め、品質意識の定着を促します。
- 作業効率の向上:
- 5Sによって作業環境が改善され、探し物をする時間や移動時間が削減されます。
- 作業効率の向上は、ひいては品質向上にもつながります。
ポカヨケと5Sの連携を成功させるポイント
- 両者の関係性を理解する:
- ポカヨケと5Sは、それぞれが独立した活動ではなく、相互に補完し合う関係であることを理解することが重要です。
- 5Sを徹底的に実施する:
- ポカヨケの効果を最大限に引き出すためには、5Sが徹底されていることが前提となります。
- 現場の意見を反映する:
- ポカヨケの導入や5Sの改善は、現場の意見を積極的に取り入れることで、より効果的なものになります。
- PDCAサイクルを回す:
- ポカヨケと5Sは、一度導入すれば終わりではなく、継続的な改善活動が必要です。PDCAサイクルを回すことで、常に最適な状態を維持することができます。
*ポカヨケと5Sは、それぞれが強力なツールであり、両者を組み合わせることで、より高いレベルの品質管理を実現することができます。5Sによって整備された清潔な環境で、ポカヨケが効果を発揮し、結果として製品の品質向上、生産性向上、コスト削減につながります。
検査の分類 ~ポカヨケシステムの歩み
新郷重夫氏は不良率を下げて品質を向上させる品質管理の検査方法として昔からある選別するだけの「分別検査」、“不良情報をフィードバックして再発防止する” 「情報検査」、そして“ミスが発生した時点で対策し不良を造らない“ポカヨケを用いた「源流検査」があるとした。
【検査の分類】
①分別検査:不良を見つける検査(Judgment Inspection System)
②情報検査:不良を減らす検査(Informative Inspection System)
③源流検査:不良を造らぬ検査(Source Inspection System)
分別検査:不良を見つける検査
英語:Informative Inspection System
過去そして現在でも多くの向上で用いられている検査、目的は「加工の終わった製品を“良品と不良品”に区別する検査」全数検査、抜き取り検査もこの方式。
この検査は「次工程、お客様に不良を送らない」という意味では有効な方法であるが如何に正確に検査しても「工場自体の不良率を下げる」ことには寄与しません。
抜き取り検査方式の欠点:
抜き取り検査方式の場合も「検査工数を低減する」には有効であるが同じく「工場自体の不良率を下げる」には寄与しません。
最終検査の欠点:
工場では製品の全数検査を最終工程で行っていますが時間軸で考えるとアクションが遅れます、その工程で検査した方が素早いアクションが出来ます。
AI検査の欠点:
最近は画像認識技術が飛躍的に進歩しAIを活用すれば精度の高い検査は可能であり漏れ不良ゼロを容易に達成することはコストを無視すれば可能ですが同じく「工場自体の不良率を下げる」には寄与しません。
情報検査:不良を減らす検査
英語:Judgment Inspection System
情報検査とは「不良が発生したら、その情報を発生した工程にフィード・バックし、アクションを行い改善することにより、再発防止をする検査」のことである。
この検査を用いれば徐々に不良率が低減できる。
この検査には三つの方式がある。
①管理図方式(SQC方式) Static Quality Control System
②順次点検方式(SuC方式)Successive Check System
③自主点検方式(SeC方式) Self Check System
管理図方式(SQC方式)
SQC方式とは「推定統計学に基づいた管理図を使用して管理限界外に異常が発生したらその情報を発生工程にフィードバックしてアクションを行い改善し、事前に不良の発生を防止する」。
規格限界線:製品の機能を要求許容限界線、規格値±許容値で表現される。
管理限界線:統計量の値がかなり高い確率で存在する範囲を締める限界、通常は2σ管理限界線が用いられる。
【68–95–99.7 ルール】
正規分布において、平均値を中心とした標準偏差の2倍、4倍、6倍の幅に入るデータの割合の簡略表現である、不良率を推定するときに活用される。
正規分布の場合、
1σ 区間におさまる確率→ 約 68.27%
2σ 区間におさまる確率→ 約 95.45%
3σ 区間におさまる確率→ 約 99.73%
であることが知られています。
管理図の欠点:
「不良率を減らすためには,まず,品質の現状を知り,これにアクションを加えなければ,効果は発揮されない」
しかし“管理図法”では「異常のチェックは抜き取りで行われる。よって異常を抽出できる確率は,“全数抽出”に比べて,はるかに低い。
しかも,一般に行われている“管理図方式”では「異常の抽出から,アクションの実施までの“時間的な距離”は,相当間隔があるのであるから,改善されるまでに相当,長い時間が必要となり、その間に,かなりの“不良現象の発生”が起こる。
又、現場に利用される管理図として“不良率の管理図”いわゆる“P管理図”というものがある、これは「従来,発生している不良率から異常値を除去して普通の状態での不良率の数値”を推測統計学に基づいてサンプルを抜き取って管理限界を設定する管理方法である。
このような方策を採用すれば,
・従来以上の不良率の発生を防止することができる。
しかし、逆説的に言うと不良があっての管理図であり、「不良率をゼロにする」という積極的な考え方ではなく消極的な方法である。
順次点検方式(Su CS :Succssive Check System)
新郷氏はSQC方式の欠点をカバーする点検方式として次工程の作業者が検査し、不良が発生時は即時、前工程に連絡し、対策改善できるようなシステム「順次点検方式」を考えポカヨケを用い松下電器のテレビ工場で実施、絶大なる効果を上げることに成功した。
順次点検方式の方法は下記のとおり。
①全数検査 実施
②不良品 判定は第三者が行う。
③不良発生時、ただちに発生工程に連絡、アクションを実施。
ポイントは「検査は客観的でなければならない!」
自主点検方式(Self Check System)
不良のフードバックとアクションを早める為には加工者が全数検査すれば良いが“検査は客観的に判断する”原則に反しており、ポカミスの発生する恐れがある。
しかし、新郷氏は”ポカヨケ”を用いて自主点検すれば自工程で不良が検知でき、即座にフードバックできると考えてコンサル先の向上に導入して効果を上げた。
この検査のポイントは「不良を自工程で発見し、確認できること」
源流検査:不良を造らない検査
英語:Source Inspection System
新郷氏は源流検査というのは「“不良を発生した結果”によって,フィード・バックとアクションを行うのではなく,“不良を発生させる原因の条件のミズを発見して,その“ミスの段階で,フィード・バックとアクションを行い“ミスは発生しても”,それを“不良には転化させない”ようにするという考え方に基づく検査方式」と説明してあり
“源流検査”と全数検査”および“フィード・バックとアクションの即時対応性”とを結合することによって不良ゼロが可能としています。
そして具体的手段としでポカヨケを利用することがきわめて効果的でありと力説しています。
源流検査の優位性~ヒューマンエラー対策
不良の原因は5M+1Eであり、材料(Material)、機械(Machine)、作業者(Man)作業方法(Method)測定(Measurement)そして環境(Environment)と言われています。
しかし、現在のモノづくり技術の進歩のお陰で良い材料が開発され、マシンは高信頼性になり、作業方法も標準化され、測定の精度も向上し、環境の制御も容易になり、どの業種の製品においても以前と比較して製品の品質は向上し、不良率は低下してきていますが不良ゼロには達成できていません。
残る不良の多くの要因は作業者(Man)によるヒューマンエラーです。
ヒューマンエラーには規則性がなく、いつ発生するかわからないので推計統計学の“抜く取り方式”ではなかなか、補足する事は困難です。
作業者(Man)によるヒューマンエラーを対策するには源流検査の具体的
手段である“ポカヨケ”による全数検査が有効です。
源流検査の優位性~フードバックとアクションスピード化
源流検査では
ミスが発生⇒不良に転化しない内に原因の段階で“フィードバック”
⇒ただちに“アクション”
が可能になり、スピードが早いという利点があります。
従来の管理方式では
ミスが発生⇒“結果”として不良が発生⇒不良発生情報をフィードバック⇒アクションを開始
といった流れで処理されるのでどうしても時間が遅れてその間に不良が発生するといった事があった。
源流検査の優位性~予防保全への活用
源流検査の考え方と共通するのが予防保全(TPM)です。
設備の故障を発生する前に事前に不具合の予兆を検知してアクションをする保全の方法で”故障ゼロのマシン”にすることが可能です。
例えば軸受部に“サーミスター”を取り付けて温度が規定以上になったら自動的にマシンを停止させる。
又、スマートホンの異常高温時の“起動停止機能”も同じ発想です。
ポカヨケ装置の種類
ポカヨケ装置の種類は分類ごとに下記のような種類に区分される。
(1)検知方法別:
①識別式・・色分け、ICタグ、画像検査機
②アラーム式・・警報機、カウンター
③治具式・・ポカヨケ・ガイドピン
④接触式・・製品の形状の違いにより異常を検知する方式。
⑤定数式・・規定の回数でない時、異常と判断し検知する方式。
⑥動作ステップ式・・動作ミスを異常と判断し検知する方式。
(2)目的別:
①規制式・・異常が発生した場合、機械を停止。
②注意式・・異常が発生時、作業者の“注意を喚起する”方式。
(3)時系列別:
①事前・・ミスを発生する前に対策
②発生時・・ミスが発生時にポカヨケ
③事後・・ ミスが発生後にポカヨケ
検知方法別 ポカヨケ装置の種類
ポカミス対策のポカヨケを仕組み別に分類すると下記のようなモノがある。
識別、選別して検知
識別には、たとえば色分けやICタグ、置き場の設定がある。色分けは、良品と不良品を区別するために、ケースに色がついたものを使用する。たとえば、赤であれば不良品とする。
また最近ではICタグが用いられるようになってきた。ICタグは双方向の通信が可能なので、瞬時に情報を入力、出力できる。製品や部品の加工履歴など簡単にメモリーすることができるため、トレーサービリティの把握には、効果を発揮する。
又、選別検査も画像検査機にて精度の高い選別が現在では可能。
アラームで検知
異常が発生した場合、アラームで作業者に知らせることが大切である、センサによる警報やカウンターによる生産量の把握などがある。
治具で検知
ポカミス防止で簡単なのは、専用治具である。(ポカヨケガイドピン)
たとえば、部品をセットするに治具を使用すれば簡単に取り付けられ、段取りミスを防止できる。
接触で検知
製品の形状の違い、寸法差によって異常を検知する方式。
定数で検知
一定の回数の動作を繰り返す作業の場合、規定の回数行わなかった場合、異常と判断し検知する方式。
動作ステップで検知
一定のステップで作業を行わなければならない時、動作ミスを異常と判断し検知する方式。
ポカヨケ装置の目的別 分類
ポカヨケ装置の目的別の分類として規制式と注意式がある。
規制式
異常が発生した場合、機械を停止するとか、ロックが解除されない等の次の作業に進行をストップさせて連続して不良の発生を防止する方法。
*強い強制力があるので不良をゼロにする為には有効な手段である。
注意式
異常が発生した場合、その情報を
・ブザー警告音
・光の点滅、点灯
で作業者の“注意を喚起する”方式である。
注意式は作業者がその情報に気が付かないと異常の発生が継続してしまう欠点があるので光の点滅、点灯させる場所、位置に配慮し、警告音の場合は周囲の環境音も考慮しなければならない。
ポカヨケ装置の時系列別方式、分類
ポカヨケには時系列的に分類すると下記の3種の方式があります。
①事後対策:
製造した内容を後工程で検査し、不具合があれば、その混入を防止する方式。
②発生時対策:
不良検出センサーに相当する装置、治具を取り付けて不良発生時点でアラームを鳴らしたり、不良混入を防ぐ方式。
③事前対策:
製品製造の源流を逆上り、製造技術上の原理的対策を図って不良発生を防ぐ方式です。フールプルーフ設計がこれに該当します。
事後 ポカヨケ対策
製造した内容を後工程で検査し不具合があれば、その混入を防止する方式。
ポカヨケ事例:空の缶詰はマグネット棒に吸引されて、出荷を防止。
缶詰の充填ミス対策として空の缶は排除できるようにした。
*画像をクリックする関連動画が再生します。
Please click an image, and can pay the movie .
発生時 ポカヨケ対策
不良検出センサーに相当する装置、治具を取り付けて不良発生時点でアラームを鳴らしたり、不良混入を防ぐ方式。
ポカヨケ事例:切削加工時の異物による樹脂製品の浮き上がり検知を「エアマイクロセンサ」で検知、加工機を停止。
*画像をクリックする関連動画が再生します。
Please click an image, and can pay the movie .
ポカヨケ装置 検知センサーの種類
ポカヨケの異常を検知するセンサーとしは色々なモノがあり、大きく分けると接触式と非接触式があります。
接触式 リミットスイッチ
下記は接触式検知センサーの代表であるリミットスイッチの種類一覧表です。
リミットスイッチとは内蔵マイクロスイッチを外力、水、油、ガス、塵埃などから保護する目的で封入ケースに組み込んだものであり、特に機械的強度や耐環境性を要求されるところに適用できるように作られたスイッチをいいます。形状は横形、縦形、マルチプル形に大別されます。
【リミットスイッチの種類一覧表】
非接触式 ポカヨケ検知センサー
下記は非接触式検知センサーの代表である光電センサーの種類一覧表です。
光電センサとは、可視光線、赤外線などの“光”を、投光部から発射し、検出物体によって反射する光や、遮光される光量の変化を受光部で検出し出力信号を得るものです。
【光電センサーの検出方式の種類一覧表】
その他 ポカヨケ検知センサー
その他のポカヨケ検知センサーとしては変位センサー、金属通過センサー、液面センサ等があります。
【その他 ポカヨケ検知センサー 種類一覧表】
ポカヨケ装置の動画事例
工場安全 ポカヨケ装置
機械回転物の中に手を入れないように、安全カバーでガードし、また安全カバーを開けると自動的に回転物が停止し、手を巻き込まれない仕組み。
セーフティレーザスキャナを使用した事例。
物流ピッキング ポカヨケ装置
ピッキングシステムでは部品の取り出しを毎回チェックでき、部品の取り間違いを警告できますので、製造不良を低減でき生産性の向上が図れます、又、ピッキングシステムを導入することで、慣れていない作業者でもピッキング表示灯の点灯順に従い段取りよく組み立て作業が行なえます。
ポカヨケ装置 トルクレンチ
ポカヨケトルクレンチは締付け回数管理で締め忘れを防止できる。
ポカヨケ装置 システム 組立作業
ポカヨケシステムを導入することで、慣れていない作業者でも表示灯の点灯順に従い段取りよく組み立て作業が行なえます。
棚から部品を取り出すとき、バーコードを読み取りした電気信号で、ランプを点滅させ、誰でも間違いなくピックアップ。
【日東工器】ねじ締め忘れ・ポカよけ
電動ドライバーを使用してのネジ締め忘れを防止するためのポカヨケ装置。
下図は車載機器や電装機器などのネジ締めの信頼性を要求される製品
の組み立てに最適の「ねじ締めカウンタ」です。
ポカヨケ装置 シャッター oneA
棚や作業台に取付ける事で、ピッキングする場所をランプ指示とシャッターの開閉により作業者に知らせます。
ポカヨケ シャッター 事例:
必要な棚以外はシャッターが開かないため、間違えたところからは取ることもなくポカミスをシャットアウトします。
バーコード・二次元コード・RFタグのポカヨケ装置の導入
バーコードや二次元コード、またはRFタグを製品・部品に取り付けることで、より正確な識別や更新作業が可能となる。
例としてRFタグを読み取ることで金型管理をシステム化できれば、金型のメンテナンス時期を把握できます。
これによりサビや汚れの発生・付着を防げるため、不良品の発生を抑えられます。
また生産管理システムと連携し、作業漏れがあった場合にも後工程に通知される仕組みにすることで、重大なミスの発生を防ぐこともできます。
ポカヨケの分析手法
ヒューマンエラーの真の原因を把握しないでポカヨケ対策すると必ず
ヒューマンエラーが再発しますので「根本原因分析」RCA(Root Cause Analysis)する事が重要です。
RCAの手法には下記のような方法はあります。
①FTA(Fault Tree Analysis) 故障の木の解析
製品の故障、およびそれにより発生した事故の原因を分析する手法。
②VTA(Variation Tree Analysis) 変化の木の解析
事故発生におけるヒューマンファクターを解明するために考案された手法。
③なぜなぜ分析
⑤連関図分析
⑥特性列挙法
ポカヨケ アプリ、ツール、システムとは
「ポカヨケ」の考え方は、現代のデジタル技術・ITシステム・アプリケーションにも応用されています。ここでは、ポカヨケを実現するアプリ・ツール・システムの例やその特徴を分かりやすく紹介します。
主なタイプ別一覧
分類 | ツール/システム名 | 内容 | ポカヨケ機能 |
---|---|---|---|
作業手順支援系 | 作業指示アプリ(例:tebiki、KAIZEN NAVI) | スマホやタブレットで作業手順を画像や動画で指示 | 手順飛ばしを防止、チェックボックスで記録管理 |
IoT/センサ系 | PLC連携システム、RFID、画像認識 | 工場の装置と連動し、部品や動作を自動監視 | 部品間違い・組付け忘れのリアルタイム検出 |
チェックリスト系 | デジタル点検アプリ(例:SmartCheck、Asana) | スマホ・タブレットで点検や確認をデジタル化 | 抜け漏れをアラート通知で防止 |
工程管理系 | MES(製造実行システム) | 作業工程をリアルタイムで記録・制御 | 工程の順番違いや不具合の即時警告 |
ソフトウェア開発 | フォーム制御、入力バリデーション | Webフォームやアプリでの入力ミス防止 | 入力漏れ・誤記・不適切値の入力不可にする |
✅ RPA/自動化系 | UiPath、Power Automate | 手作業の繰り返し業務を自動処理 | ミスの起きやすい転記・集計作業を自動化 |
ポカヨケ アプリ、ツール、システム 導入のメリット
効果 | 説明 |
---|---|
✅ ミスの削減 | 人の注意力に頼らない仕組み化が可能 |
✅ 作業の標準化 | 誰でも同じ手順で実施できるように |
✅ 教育の簡易化 | 新人でも安心して作業可能 |
✅ トラブル予防 | 異常や逸脱をリアルタイムに検出・記録 |
現場導入の例
-
製造現場で「部品が正しい位置にないと次の工程に進まない」
-
医療現場で「患者情報の入力ミス防止アラート」
-
サービス業で「接客マニュアルに従わないと次に進めないレジ操作」
ポカヨケ対応アプリ・ツール一覧
1. POKAYOKE® Premium(マーズコンピュータ)
Android対応の現場向けアプリで、ピッキングミスや棚卸ミス、出荷ロット管理などをバーコードスキャンで防止します。複数のパッケージモデルが用意されており、物流・製造・通販業などで活用されています
-
詳細・導入モデル一覧: https://www.pokayoke-premium.com
2. POKAYOKE plus(ヘルツ電子)
Windows対応の生産工程支援ソフトウェアです。ポカヨケ対応工具やセンサーと連携し、作業実績や安全装備の着用状況をリアルタイムで記録・管理します。トレーサビリティの確保にも有効です。
3. ポカヨケシステム(東朋テクノロジー)
30年以上の実績を持つポカヨケシステムで、ハード・ソフト両面からのトータル提案が可能です。ピッキングシステムや作業指示システムなど、多様な現場ニーズに対応しています。
4. TULIP(T Project)
プログラミング不要で業務アプリを作成できるプラットフォームです。製造現場での作業手順のデジタル化や自動チェック機能により、ヒューマンエラーを防止します。
5. Asana
プロジェクト管理ツールで、タスクの可視化や進捗管理を通じて、作業の抜け漏れを防止します。チームでの協働作業に適しています。
-
サイト: https://asana.com
6. UiPath
RPA(ロボティック・プロセス・オートメーション)ツールで、定型業務の自動化により、手作業によるミスを削減します。業務プロセスの効率化に寄与します。
-
サイト: https://uipath.com
これらのツールは、業種や業務内容に応じて適切なものを選定することで、ヒューマンエラーの防止や業務効率の向上に貢献します。導入を検討される際は、各製品の詳細を確認し、現場のニーズに合ったものを選択してください。
ポカヨケ対応アプリ POKAYOKE® Premiumとは
POKAYOKE® Premiumは、マーズコンピュータ株式会社が提供するAndroid対応のポカヨケ対策アプリケーションです。物流・製造・倉庫などの現場で発生しやすい「うっかりミス」や「作業ミス」を防止し、業務の正確性と効率性を向上させることを目的としています。
🔧 主な機能と特徴
-
バーコード照合機能:商品のバーコードをスキャンし、事前に登録されたデータと照合することで、誤出荷や誤ピッキングを防止します
-
1対1チェック:伝票と現物のバーコードをそれぞれスキャンし、一致しているかを確認します。
-
1対nチェック:複数のバーコードリストと照合し、対象商品の有無を確認します。
-
データ連携機能:作業履歴やチェックリストをCSV形式で出力・入力可能で、他システムとの連携が容易です。
-
ルールチェック機能:バーコードの桁数や特定の文字列パターンを設定し、照合時にルール違反を検出します。
パッケージモデル
POKAYOKE® Premiumは、以下のような用途に応じたパッケージモデルが用意されています:
-
ピッキング間違い防止モデル:商品の取り間違いを防止するためのモデルで、一覧形式や1対1形式があります
-
実地棚卸モデル:棚卸作業を効率化し、入力ミスを防止します。棚卸数入力タイプと在庫台帳タイプがあります。
-
出荷ロット記録・トレースモデル:出荷された商品のロット番号を記録し、トレーサビリティを確保します。
-
荷物お預かりモデル:複数の荷物を預かり、返却時に間違いなく全て返却できるよう管理します。
導入のメリット
-
ヒューマンエラーの削減:作業ミスを未然に防止し、品質向上に貢献します。
-
作業効率の向上:バーコードスキャンによる迅速な照合で、作業時間を短縮します。
-
教育コストの削減:操作が直感的で簡単なため、新人教育の負担を軽減します。
-
初期費用のみで導入可能:ランニングコストが不要で、導入しやすい価格設定です。
公式サイト
詳細な情報や導入のご相談は、公式サイトをご覧ください:
ポカヨケとAIの活用:新たな品質管理の時代へ
近年、製造業を中心に、ポカヨケにAIが導入されるケースが増えています。従来の人間の経験や勘に頼っていたポカヨケが、AIの力を借りることで、より高度化し、効果的なものへと進化しています。
なぜAIがポカヨケに注目されるのか?
- 人間の限界を超える検出能力: AIは、画像認識、音声認識などの技術を用いて、人間の目では見つけられない微細な不良や、複雑なパターンを検出することができます。
- リアルタイムでの異常検知: AIは大量のデータを高速に処理できるため、生産ラインでの異常をリアルタイムで検知し、迅速な対応が可能になります。
- 学習機能による精度向上: AIは、過去のデータから学習し、精度を向上させることができます。そのため、新たな種類の不良が発生した場合でも、迅速に対応することができます。
- 客観的な判断: AIは、感情や主観に左右されることなく、客観的な判断を行うことができます。
AIを活用したポカヨケの対策事例
画像認識による外観検査:
- 製品表面の傷、ひび割れ、汚れなどを、高精度なカメラとAIの画像認識技術を用いて自動検出します。
- 人間の目視検査に比べて、より迅速かつ正確な検査が可能になります。
精密機器部品の製造工場Aでは下記の2つの課題ありました。
- 欠陥分類に時間がかかる
- 欠陥分類の目視が困難
精密機器部品に生じる欠陥は微細な大きさのものも多く、欠陥の種類も多種多様であることから発見が困難で、分類に非常に時間がかかるという問題がありました。そこで同社は画像認識AIシステムを導入しました。
システム導入後は、従来に比べて欠陥分類の精度を大幅に引き上げることに成功、欠陥分類に要する時間が短縮されて検査効率が向上するとともに、欠陥分類の精度が高まったことから、製造工程も大きく改善しています。
撮影された画像の欠陥分類の正解率は96.47%と非常に高く、これまでは難しかった製造工程改善への適切なフィードバックも可能となった。
- 音声認識による作業指示の確認:
- 作業指示を音声で確認し、作業者が誤った手順で作業を行っていないかを確認します。
- 複数の作業者がいる現場でも、個々の作業状況を把握できます。
- センサーデータ分析による異常検知:
- 機械の振動、温度、圧力などのセンサーデータをAIで分析し、異常を早期に検知します。
- 設備の故障を事前に予測し、生産停止を防ぐことができます。
AI導入によるメリット
- 品質向上:
- 人間の目視検査では見つけられない不良を検出し、製品の品質を向上させます。
- 生産性向上:
- 自動化による検査時間の短縮、不良品発生の抑制により、生産性を向上させます。
- コスト削減:
- 人件費の削減、不良品発生による損失の減少など、コスト削減に貢献します。
- 作業環境の改善:
- 危険な作業や単調な作業をAIに任せることで、作業者の負担を軽減し、作業環境を改善します。
AI導入の課題と対策
- 初期投資:
- AIシステムの導入には、高額な初期投資が必要となる場合があります。
- データの質:
- AIの学習には、大量の高品質なデータが必要となります。
- 人材育成:
- AIシステムを運用するためには、専門知識を持った人材の育成が必要です。
*AIとポカヨケの組み合わせは、製造業の品質管理を革新的に変える可能性を秘めています。しかし、AI導入には、初期投資や人材育成など、克服すべき課題も存在します。企業は、自社の状況に合わせて、AI導入のメリットとデメリットを慎重に検討し、最適な導入計画を立てる必要があります。
ポカヨケによる安全で高品質な社会の実現に向けて
ポカヨケは、製造業に限らず、様々な分野で導入され、その社会的意義は非常に大きいです。
ポカヨケの社会的意義
- 製品の品質向上と安全性の確保: ポカヨケは、ヒューマンエラーを未然に防ぎ、製品の品質向上に大きく貢献します。食品や医薬品など、人々の健康に関わる製品においては、その重要性が特に高いです。また、機械の誤動作や製品の欠陥による事故を防ぎ、人々の安全を守ります。
- 生産性の向上とコスト削減: ポカヨケによって不良品が減少し、再作業や廃棄が削減されることで、生産効率が向上し、コスト削減につながります。これは、企業の競争力強化に不可欠な要素です。
- 労働環境の改善: ポカヨケは、作業者の負担を軽減し、ミスによるストレスを減らすことで、労働環境の改善に貢献します。
- 社会全体の信頼性向上: 高品質な製品やサービスを提供することで、企業に対する信頼感が高まり、ひいては社会全体の信頼性向上につながります。
ポカヨケが社会に与える具体的な影響
- リコール問題の防止: 自動車や家電製品などのリコール問題は、企業のイメージダウンだけでなく、消費者の安全を脅かす深刻な問題です。ポカヨケは、このような問題の発生を未然に防ぎ、消費者の安心・安全を守ります。
- 医療分野での貢献: 医療現場では、誤投薬や手術ミスなどが起こる可能性があります。ポカヨケは、このような医療ミスを防ぎ、患者の安全を確保する上で重要な役割を果たします。
- サービス業における品質向上: サービス業においても、ポカヨケの考え方は応用できます。例えば、飲食店での注文ミスや、小売店でのレジ打ち間違いなどを防ぐことで、顧客満足度を高めることができます。
ポカヨケの今後の展望
近年では、AIやIoTなどの技術の進展により、ポカヨケの仕組みはますます高度化しています。例えば、画像認識技術を用いて製品の外観検査を行うなど、より精度の高い検査が可能になっています。
また、ポカヨケは、製造業だけでなく、サービス業や医療など、様々な分野で導入が進んでいます。今後も、ポカヨケは、社会の様々な問題解決に貢献していくことが期待されます。
安全性の向上と労災リスクの低減
ポカヨケを導入することで、以下の効果が期待できます。
- ヒューマンエラーの防止:
- 作業手順の誤り、部品の取り違え、締め忘れなど、人の手によるミスを物理的に防ぎます。
- 例えば、ある部品を特定の場所にしか取り付けられないような形状にする、工具のサイズを限定するなどが挙げられます。
- 危険な作業の排除:
- 危険を伴う作業を自動化したり、安全装置を設けたりすることで、労働災害のリスクを大幅に低減します。
- 作業者の負担軽減:
- 重労働や反復作業を機械に任せることで、作業者の負担を軽減し、疲労によるミスを防ぎます。
- 安全意識の向上:
- ポカヨケの導入によって、安全に対する意識が向上し、安全な作業習慣が定着します。
ポカヨケの教育と訓練:安全な職場環境を築くための第一歩
ポカヨケは、ヒューマンエラーを防止し、安全な職場環境を実現するための重要な取り組みです。しかし、ポカヨケの仕組みを導入するだけでは十分ではありません。作業者への適切な教育と訓練が、ポカヨケを効果的に機能させるために不可欠です。
なぜ教育と訓練が必要なのか?
- ポカヨケの目的と意義の理解: ポカヨケがなぜ必要なのか、どのような効果があるのかを理解することで、作業者は主体的にポカヨケに取り組むことができます。
- ポカヨケ手法の習得: さまざまなポカヨケ手法を習得し、それぞれの状況に応じた適切な手法を選択できるようになります。
- 標準作業手順の習得: 標準作業手順を熟知し、常に手順に従って作業を行う習慣を身につけます。
- 問題発見能力の向上: ポカヨケが機能していない場合や、新たなポカが発生した場合に、自ら問題を発見し、改善提案を行う能力を養います。
効果的な教育と訓練の方法
- OJT(On-the-Job Training): 経験豊富なベテラン社員が、実際の作業現場で新人社員に指導を行います。
- OFF-JT(Off-the-Job Training): 研修施設や会議室など、実際の作業現場から離れた場所で、座学や実習を行います。
- シミュレーション: 実際の作業を模擬的に体験できるシミュレーターを用いて、安全な環境下で訓練を行います。
- グループワーク: グループでディスカッションを行い、互いに意見交換することで、より深い理解を促します。
教育と訓練で意識すべき点
- 多様な学習スタイルへの対応: 視覚、聴覚、触覚など、それぞれの学習スタイルに合わせた多様な教材や手法を用いることが重要です。
- 反復練習: 繰り返し練習することで、習得した知識やスキルを定着させます。
- 評価とフィードバック: 定期的に評価を行い、フィードバックを与えることで、改善点を明確にし、モチベーションを維持します。
- 現場へのフィードバック: 訓練で得られた意見や改善点を、実際の現場にフィードバックし、改善に活かします。
ポカヨケ教育と訓練の重要性
ポカヨケの教育と訓練は、単に作業手順を教えるだけでなく、安全意識の向上、問題解決能力の育成、組織全体の活性化にもつながります。
- 安全意識の向上: ポカヨケの重要性を認識し、安全第一の意識を醸成します。
- 問題解決能力の育成: 問題を発見し、改善策を提案できる人材を育成します。
- 組織全体の活性化: 従業員が主体的に改善活動に参加し、組織全体の活性化を図ります。
ポカヨケ導入時の課題と対策
ポカヨケの導入は、企業の品質向上や安全性の確保に大きく貢献しますが、その導入には様々な課題が伴います。ここでは、ポカヨケ導入時に起こりうる課題と、それらの対策について詳しく解説
現場の抵抗感:
新しい仕組みへの抵抗感や、従来のやり方への固執。
対策:
導入の目的やメリットを丁寧に説明し、理解を得る。
現場の意見を聞きながら、一緒に改善していく姿勢を示す。
パイロット導入を行い、効果を実感してもらう。
コスト:
治具やシステムの導入、教育訓練など、多額の費用がかかる場合がある。
対策:
コスト削減につながるポカヨケ方法を検討する。
長期的な視点で費用対効果を評価する。
段階的な導入を検討する。
時間:
システム構築や教育訓練に時間がかかる。
対策:
導入スケジュールを明確にし、進捗状況を定期的に報告する。
シンプルなポカヨケから導入し、徐々に複雑なものを導入していく。
標準化の難しさ:
多様な作業工程において、一律の標準化が難しい場合がある。
対策:
工程ごとに最適なポカヨケ方法を検討する。
標準作業手順書を分かりやすく作成し、周知徹底する。
効果測定の難しさ:
ポカヨケの効果を定量的に評価するのが難しい場合がある。
対策:
導入前後のデータ比較を行う。
定期的なヒアリングを行い、現場の声を聞く。
*ポカヨケの導入は、一朝一夕にできるものではありません。現場の状況や企業の規模によって、最適な導入方法や対策は異なります。現場の意見を聞きながら、段階的に導入を進め、継続的な改善を心掛けることが重要です。
ポカヨケの効果的な評価方法
ポカヨケの効果を評価することは、改善活動の継続的な推進に不可欠です。導入前と導入後の比較、定量的なデータの収集、そして多角的な視点からの分析が重要となります。
効果評価のポイント
- 定量的なデータの収集:
- ポカミス発生件数、不良品発生率、生産性、納期遵守率などの数値化可能な指標を設定し、導入前後の変化を比較します。
- KPI (Key Performance Indicator) を設定し、定期的に測定することで、効果を可視化します。
- 多角的な視点からの分析:
- ポカヨケ導入による直接的な効果だけでなく、作業者の満足度、作業環境の改善、コスト削減効果なども評価対象に含めます。
- 現場の声を聞き、定性的な評価も併せて行うことで、より深い理解を得ることができます。
- 長期的な視点:
- 短期的な効果だけでなく、長期的な効果も考慮します。
- ポカヨケが定着し、組織全体の品質意識が向上しているかなどを評価します。
評価方法の具体例
- Before-After比較:
- ポカヨケ導入前と導入後のデータを比較し、改善効果を定量的に評価します。
- 例:不良品発生率が30%から10%に減少したなど。
- KPIの追跡:
- 事前に設定したKPIを定期的に測定し、目標達成状況を把握します。
- 例:生産性が15%向上したなど。
- アンケート調査:
- 現場の作業者にアンケートを実施し、ポカヨケ導入による作業の効率化、満足度などを評価します。
- 例:作業の負担が軽減された、ミスが減って安心して作業できるなど。
- コスト削減効果の算出:
- 不良品発生による損失、再作業コストなどの削減額を算出し、経済的な効果を評価します。
- PDCAサイクルの活用:
効果的な評価のための注意点
- 評価指標の明確化:
- 評価したい効果に合わせて、適切な指標を設定します。
- データの正確性:
- データ収集方法を標準化し、正確なデータを収集します。
- 客観的な評価:
- 主観的な判断ではなく、客観的なデータに基づいて評価を行います。
- 現場との連携:
- 現場の意見を聞きながら、評価方法を改善していきます。
*ポカヨケの効果評価は、単に数値目標の達成だけでなく、組織全体の品質向上につながる重要な活動です。多角的な視点から評価を行い、改善活動を継続することで、より効果的なポカヨケを実現することができます。
ポカヨケQ&A 上位10選【初心者向けにやさしく解説】
ポカヨケとは?
「ポカ(うっかりミス)」+「ヨケ(避ける)」という意味で、製造現場などで人為的ミスを未然に防ぐための仕組みです。
1. ポカヨケの目的は?
ヒューマンエラーを防ぎ、不良品の発生や安全事故を未然に防ぐことが主な目的です。
2. ポカヨケの起源は?
トヨタの新郷重雄氏が1960年代に体系化しました。もともとは「バカヨケ(馬鹿でもできる)」という言葉から来ていますが、差別的な表現を避け「ポカヨケ」となりました。
3. ポカヨケの主な種類は?
- 接触型:物理的形状や寸法で不良を検知
- 定数型:数量や回数によるミス防止
- 動作型:順番や手順の違いを監視して異常を検知
4. いつ導入するべき?
ミスが頻発する工程、または一度のミスが大きな損失につながる工程に導入するのが効果的です。
5. ポカヨケ導入のステップは?
- 問題点の洗い出し
- 原因の分析(例:なぜなぜ分析)
- 仕組みの設計(センサー、ガイドなど)
- 試行・検証
- 本格導入と継続的改善
6. 活用事例には何がある?
- 箱詰め作業での「説明書入れ忘れ」防止カウンター
- 組立工程での「部品の向き間違い」防止治具
- 検査工程での「高さセンサー+警報ランプ」設置
参考:トヨタ生産方式におけるポカヨケ改善事例集【イラスト図解】
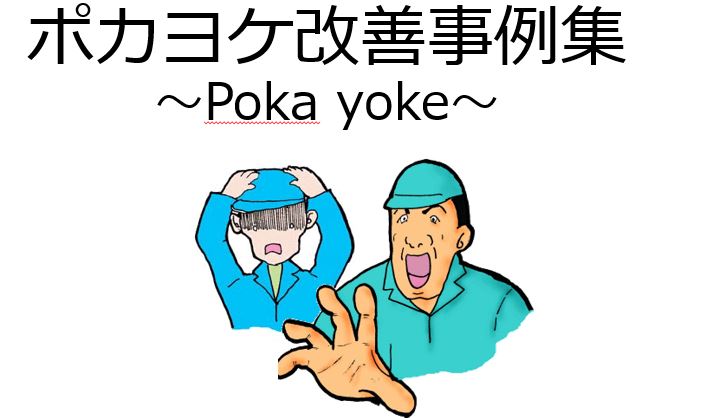
7. メリットは?
- 不良品の減少
- 品質の安定と向上
- 作業効率アップ
- 作業者の心理的負担の軽減
8. 導入時の注意点は?
警報が鳴っても気づかない配置では効果が薄れます。人の動線や視認性に配慮した設計が必要です。また、工程全体の整合性も大切です。
9. 対応できる業種は?
製造業に限らず、梱包、検品、事務処理、ITシステムなど、ヒューマンエラーが発生しうるあらゆる業務に応用可能です。
10. ポカヨケは一過性の対策ですか?
いいえ。ポカヨケは継続的改善(カイゼン)の一部です。定期的な見直しや現場の声を反映して育てていくことが大切です。
まとめ
トヨタ生産方式の基本概念のひとつとして有名なのは『ポカヨケ』です。
「ミスを発生させない、不良品を流さない」という思想は工程の自動化が進んだ現在でも変わらず重要なものです。
従来は「ミスをおかさないための工夫」が主に行われていましたが、現在では「自動化・機械化によって人の手をかけない」考え方へとシフトしています。
IoTやRFIDといった技術は、この思想をさらに発展させる手段としてさらなる活用が期待されてますがどんなツールを作成しても元々は人間が設計、開発、製造したモノなので確率は低いですが必ずヒューマンエラーが潜んでいます。
工場での具体的なポカヨケ事例をnoteに投稿しています、ご参考 願いします。
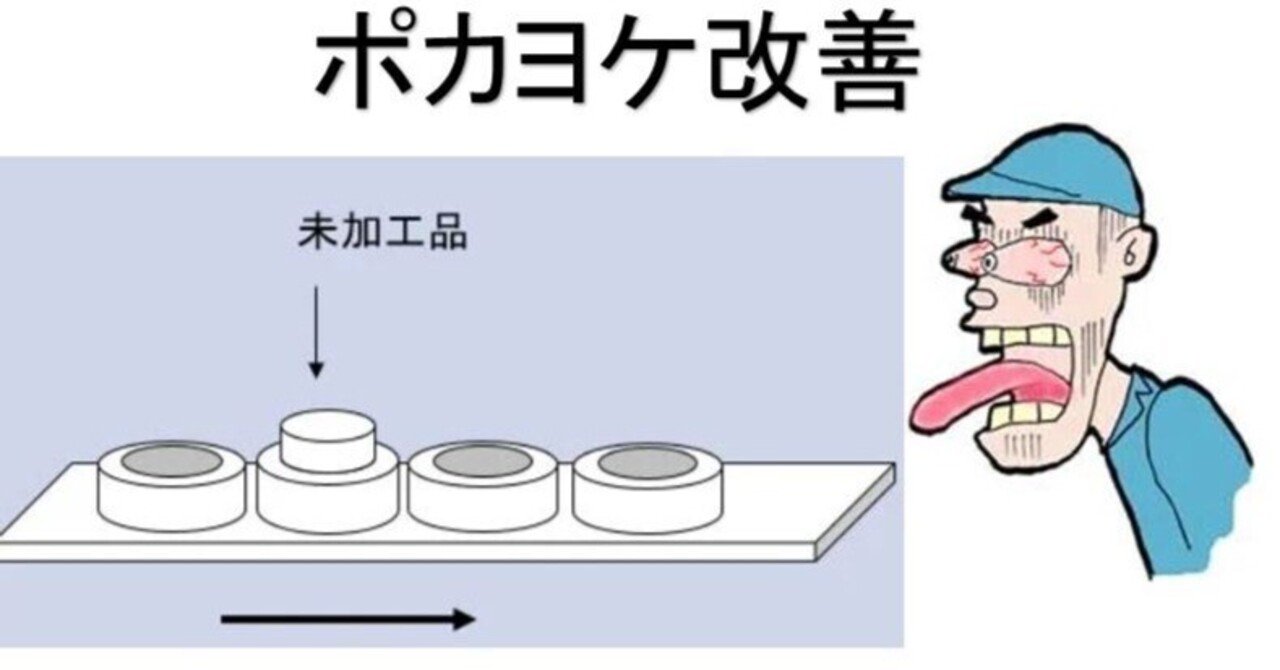
ポカヨケとは、「人の失敗を責めるのではなく、仕組みで支える」ための知恵です。
「智慧ある者は、つまずきより学び、道を正す」──仏教の教えより
失敗から学び、再発を防ぐ工夫こそ、真の現場改善の第一歩です。
関連キーワード:
フールプルーフ フェールセーフ ポカヨケ ヒューマンエラー KAIZEN
ポカヨケ対策 Poka yoke 資料 無料 ダウンロード
ポカヨケ対策のパワポ資料が無料でダウンロードできます。
自己学習、講座開催時にお役に立ててください。
グーグルスライド版 トヨタ式のポカヨケの基礎知識と導入のメリットを紹介
スライドシェアー版 ポカヨケ対策 Poka yoke 資料
スライドシェアー(Slideshare)から資料が無料でダウンロードできます。
参考文献:
1.源流検査とポカヨケ・システム―不良=0への挑戦 新郷 重夫 (著)
2.ポケット図解 ポカヨケの基本がわかる本
3.ナットク現場改善シリーズ よくわかる「ポカヨケ」の本
4.全図解トヨタ生産工場ポカヨケのすべて
コメント
[…] 匠の知恵 ポカヨケ対策 Poka yoke【図解】 | 日本のものづくり~品質管理、生産管理、設備…https://takuminotie.com/blog/2019/11/15/post-18830/ポカヨケとは 「人間は間違いをおかす動物で、ポカミ […]
[…] 程时,就考虑到人为失误,把过程设计成不容易出错的过程。比如,在设计机器时,为了防止机器切到手,设置成需要用手去按在另外一个地方的按钮。https://takuminotie.com/blog/2019/11/15/post-18830/ […]