問題解決型手法 QCストーリーについて下記の点をポイントに図解入れで解説しています。
・問題解決手法 QCストーリーとは
・問題解決の為のプロセス思考
・QCテーマの選定
・QCストーリー 8ステップ
モノづくりの参考になれば幸いです。(*^_^*)
動画 2024年版 分かり易い 問題解決型手法 QCストーリーとは 【音声解説付き】
品質改善の問題解決型手法 QCストーリーの概要、説明 動画です。
3分で分かる! 問題解決型手法 QCストーリーの概要解説
QCストーリーとは、品質管理(QC)における問題解決のプロセスをまとめたもので、企業や組織における改善活動の定番手法の一つです。
QCストーリーの目的
問題の明確化: 現場で発生している問題や課題を具体的に特定します。
原因の究明: 問題の原因をデータに基づいて科学的に分析し、根本的な原因を特定します。
対策の立案と実行: 問題解決のための効果的な対策を立案し、実際に実行します。
効果の検証: 実施した対策が効果をもたらしたかを検証し、改善効果を定量的に評価します。
標準化: 効果が確認された対策を標準化し、再発防止につなげます。
QCストーリーの構成
QCストーリーは、一般的に以下の構成でまとめられます。
テーマ: 解決したい問題を明確に記述します。
現状の把握: 問題の現状をデータや図を用いて具体的に示します。
目標の設定: 改善活動によって達成したい目標を数値化して設定します。
原因分析: 問題の原因を究明するための分析を行います。
対策の立案: 問題解決のための具体的な対策を複数案検討し、最適な対策を選択します。
対策の実施: 立案した対策を実行します。
効果の確認: 対策実施後の効果を定量的に評価します。
標準化: 効果が確認された対策を標準化し、マニュアル化などを行います。
今後の課題: 今後の改善活動に向けた課題を明確にします。
QCストーリーのメリット
問題解決能力の向上: 論理的な思考力や問題解決能力を養うことができます。
チームワークの強化: チームで協力して問題解決に取り組むことで、チームワークが強化されます。
品質向上: 製品やサービスの品質向上に繋がり、顧客満足度の向上にも貢献します。
コスト削減: 不良品発生の減少や効率化により、コスト削減につながる可能性があります。
QCストーリーの活用例
製造業: 製品不良の減少、生産性の向上
サービス業: 顧客満足度の向上、クレームの減少
事務部門: 業務効率化、ミス防止
QCストーリーを作成する際のポイント
データに基づいて分析する: 主観ではなく、データに基づいて客観的に分析することが重要です。
PDCAサイクルを回す: Plan(計画)、Do(実行)、Check(評価)、Act(改善)のPDCAサイクルを回しながら、継続的に改善活動を進めることが大切です。
チームで協力する: さまざまな立場の人々が協力して問題解決に取り組むことで、より効果的な改善が期待できます。
QCストーリーは、単なる問題解決の手法にとどまらず、組織全体の改善文化を醸成するための重要なツールです。
問題解決手法 QCストーリー
1.問題とは?
あるべき姿と現状とのギャップを問題と言います。現状は目の前に見える今の姿ですからすでにわかっており、あるべき姿を明らかにすれば、現状とのギャップとして問題が見えてきます。
たとえば、現状100個に3個が不良品という良品率97%のラインの場合、このラインの過去の最高値である良品率98%をあるべき姿に設定すれば、ギャップは1%となり、これが「問題」となります。
課題とは?
問題と課題はしばしば混同されますが意味が違います。
問題は現状の姿に着目し『設定している目標値』と現状の差であり、これに対して課題は将来の目指す姿に着目し『将来にあるべき姿の目標値』と現状との差です、問題は『解決する』であり課題は『達成する』です。
問題を『達成する』とは言いません。
QCストリーのタイプ、種類
問題解決法で原因に迫って対策を講じるタイプを「問題解決型」、設計的なアプローチを「課題達成型」、原因や対策が見えている場合を「施策実行型」と呼んでいる。
QCストリー 3つの型 活動の内容
種類 | 課題達成型 | 問題解決型 | 施策実行型 |
問題内容 | あるべき姿に近づけるため | ありたい姿にちかづけるため | 対策優先 |
活動内容 | 課題追求、良さを追求する | 原因追求、悪さを追及する活動 | 対策がみえているなら、まず対策を |
問題解決の為のプロセス思考
問題解決には考え方の定石としていくつかの基本的は考え方があります。
例えば、製品に傷がついていた、異物が混入していた、といったクレームが顧客からよせられ、何らかの対策を検討します。
顧客クレームだからすぐに対応しなくてはなりませんが傷、異物といった結果を表面的に見るのではなく、どのような経過(プロセス:process)で不良が発生し、発見できずに流出したか、プロセスを見る必要があります。結果は、プロセスによって導かれたものであってプロセスがなければ結果もないという考え方に基づいています。
事実を把握
問題解決は事実をとらえるところから始まります。改善活動の現場でよく「事実をとらえて、データで説明せよ」と言います。事実とは、今現実に起きていること、また刻々と変化する最新の状況のことです。
事実をとらえることは、現場で現物をよく見ることから始まります。問題は現場で起きています。たとえば、機械で製品をつくる工程なら不良品は機械でつくられていることになりますし、手作業職場ならその作業の中で不良品がつくられます。決して、現場から離れた会議室やスタッフの席不良がくられるわけではありません。ですから、現場で現物を見て現象(現実)を確認せよ、と言われているのです。こうした考え方を三現主義と言います。
また、データを示すことも必要です。過去の経験から不良品は機械の立ち上がり直後に多いと思っていたら、データを取ったらまったく違った、といったことがよく起こりす。事実をとらえる対極にある考え方が経験、カン、度胸でローマ字の値文字を取って[KKDの管理]などと呼ばれ、事実にも基づかない問題解決活動を戒める教訓となっています。
QCストーリーとは|TQC活動の課題解決型手法
QCストリーとは?
QCストーリーは、問題解決のプロセスや手順の筋道です。
QCストーリーは、もともと改善した内容を報告書にまとめたり、発表したりするときに使われていました。
その後このプロセスが、実際に改善活動を進める際にも有効だ、と認識されるようになり、QCストーリーとして普及していきました。もともと他人に理解してもらうための手順でしたが、自分自身で問題解決するための手順になった、というわけです。
QCストーリーは問題解決の定石で、これを使えば初心者でもある程度の問題を解決できます。 QCストーリーには、問題解決型QCストーリーや課題達成型QCストーリーなどがあり、また、QCストーリーの考え方を応用したいろいろなロス改善手順(たとえば、段取り調整ロス改善のプログラム、チョコ停ロス改善のプログラムなど)があります。
QCストーリーは英語、中国語では下記のように呼びます。
英語:QC Story
中国語:问题解决流程
QCストリーの考え方
QCストーリーに基づいていない問題解決はとにかくやってみて、うまくいけばハッピー、ダメならやり直す、という試行錯誤の繰り返しです。これでは前述のKKDです。
豊富な経験は時に役に立つこともありますが、経験のない問題は解決できない、以前に取り組んだものの結果が出なかったので始める前にあきらめる、カンがはずれると効果が出ない、といった弊害があり非効率的です。
QCストーリーの8つのステップを説明しましたが、これを簡単に表現すれば『真の原因を探し出して対策を打つ』ということです。真の原因を探し出すために現状把握や要因解析があり、対策の効果を維持するために歯止めがあります。
QC活動、小集団活動の課題達成型手法
さまざまな場所でさまざまな問題の解決が図られているがこれらの問題解決の筋道を分解すると多くの場合そこの共通のパターンが存在する。この共通パーターンはQCストーリーと呼ばれる。品質改善活動における問題解決の手順はひとつの物語あるいはドラマであるとみなしてQCストーリーと呼ぶのである。これは問題解決の一般的手順あるいは定石といってもよい。
QC活動、小集団活動、TPM活動はQCストーリーを使用しての現場の作業者によるQCテーマ、小集団活動テーマ、TPM活動の施策実行型、課題達成型の改善活動である。
実践的な小集団活動およびQCサークルの進め方は下記の記事を参照してください。
関連記事:小集団活動|QCサークル
以下にQCストーリーによって問題がどのように取り上げられ,分析され,解決に導かれるかをのべる。
QC問題とは何か
QCストーリーにおいて,問題は以下のように定義される、問題とは,目的を持った活動の望ましくない結果である。
問題の解決とは,望ましくない結果をもたらすプロセスを満足のいく結果がれるように改善することである。問題を引き起こした原因を事実にもとづいて調査し,想像や机上の理論にもとづく判断は避け,原因と結果との関係をデータを用いて解析する。
以下の8つのステップで問題の解決をはかる。
改善活動を論理的に一貫したものにし,その成果を着実に蓄積するために,活動をこの8つのステップに従って実施する,この手順は問題解決の方法としは遠回りに思えることもあるが,着実な道であり,結局は最短になる。QCストーリーの各ステップにはいくつかの「活動」がある、その内容を「解説」部分でのべる。
QCテーマの選定
職場のロスを把握し、難易度に応じてテーマを階層別に役割分担します。
問題を明確にし、QCテーマを選定をする。
①取り上げようとする問題がほかの問題よりも重要であることを確認する。
②問題の背景,今までの経過がどのようであったかを理解する。
③活動の望ましくない状態を具体的な言葉で表現する.何が損失であるか,それはどの程度改善されるべきであるかを具体的に示す。
④テーマと目標値を決定する。もし必要であればサブテーマも決める。
⑤組織活動では改善活動を担当する者は正式の任命を受ける、チームで取り組む場合にはメンバーとリーダが任命を受ける。
⑥改善活動の計画,予算の見積もりを策定する。
⑦活動のスケジュールを立てる。
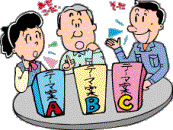
QCテーマ―の選定
QCサークル活動のテーマ―選定方法
1)われわれのまわりには,大小数え切れないほど多くの問題があるが, 時問,予算にかぎりがあるので,取り組む問題は優先順位をつけて選択しなければならない。利用できるデータを活用してもっとも重要と思われる問題を引き出す、問題の選出にあたっては,その選択の理由を明確にしておかなければならない。
2)問題の選定に理由づけをすることは,問題の解決に直接関係するものではない。しかし,関係する人々が問題の重要性の理解を共有しているときは,問題解決の可能性を高める問題の重要性が関係者に十分に理解されていなときは,解決できる問題であっても担当者の取り組みが徹底せず,活動を途中で止めてしまうことすらあり,改善は実現しない。できるだけ多くの人が問題に関して共通の認識が持てるようにこのステップを踏まなければならない。
3)改善の目標値が設定された根拠を示すことは重要である。不合理な目標値は人々の意欲を喪失させる、不良率0%を目標値としても,多くの場合このような目標を達成することは非常に難しい。もし達成されたとしても目標を成する過程でいろいろな弊害をもたらすおそれがある。合理的な目標値は,経済上の効果と技術的な可能性を考慮して決めなければならない。
4)問題に多くの種類の要素が内在している場合には,問題を効率的に扱うためにいくつかのサブテーマに分ける.全体が同種の問題からなっている場には全体の中から典型的な部分を選び出して改善し,全体に展開するための礎とするのがよい.代表的な部分を抜き出しメインテーマとし,ほかの部分をサブテーマとして計画をたてる。
5)問題を解決する期限を明示する。
必要性が十分理解されていれば,いつまでに問題点が解決されなければならないかもはっきりするだろう。
テーマ―選定のプロセス
手順① 職場内のロス把握
このプロセスは管理者が行います。管理者は、まず、自職場のロスの全体像を把握します。ロスの把握とは、たとえば、設備の効率化を阻害するロスについて、故障ロス、段取り調整ロス、立ち上がりロス、刃具交換口ス、速度ロス、チョコ停空転ロス、不良ロスといったロス別にロス時間を把握し、金額換算することを言います。ロスの全体像を把握し、ロス削減の中期計画や年間計画を考えるのが、この手順①です。
手順② テーマ候補のリスト化
次にロス削減計画に基づいてテーマ候補をリスト化し、優先順位を決めます。この手順②も管理者の役割であり、改善チームやサークルの仕事ではありません。具体的には、職場全体のロスのパレート図を作成、さらにその中でロスの大きな項目を細分化してテーマリストを作成してください。10テーマや20テーマはすぐリストにあがるはずです。
手順③ テーマを決める
最後に誰が、いつ、どのテーマを行うか決めます。管理者、監督者、第一線のオペレーターサークルなど各階層にはそれぞれ役割があり、取り組むテーマも各階層によって異なります。改善テーマもそれぞれの階層にふさわしいテーマを選定します、たとえば、慢性不良など困難なテーマはプロジェクトチー厶、比較的簡単なテーマはオペレーターサークル、というように適切に役割分担します。
テーマ―設定のポイント
ポイント 『木を見て森を見ず!』
全体を見渡し、次に細部を見ていくのがポイントです。「木を見て森を見ず」という言葉はまさにテーマ選定の教訓になる言葉です。
「全体⇒細部」のプロセスなしにテーマ選定すると第1に解決しても効果は微々たるもので、職場全体のロス削減にはほとんど貢献しないようなテーマを選んでしまう可能性があります、第2に効果金額の非常に小さいテーマを管理者クラスが1年もかけて取り組んでしまうといった時間と金のムダを引き起こす可能性があります。
NG テーマ―設定例 対策をきめているテーマ
テーマ名は『A工程における△△ロスの削減』のように、どの工程で、どのようなロスを対象とするか明確に表現します。
テーマ名として不適切なものは「標準化による不良ロス削減」、「材料変更によるチョコ停ロス削減」のように、対策や手段をテーマ名に入れてしまうケースです。
どんな対策が有効かわからないからQCストーリーを使って取り組もうとするのであって、テーマ選定の時点で対策はわかりません。
現状把握
幅広く,いろいろな視点から問題の特徴を調べる活動
①問題の特徴を見つけるために多くの異なった視点から調査する.不良の解析では少なくとも,状態,部位,時間,条件,種類,について該当するものを調べる。
②結果のバラツキ,要因のバラツキを調べる。
③現場に行き,データに現れない必要な情報を集める。
QC7つ道具の層別による現状把握
選定された問題について,多くの視点からその状況を調べ,問題の特徴を理解する、このステップでは,問題を起こす原因には触れず,問題をありのまま見る。
1)問題を解決する手がかりは多くの場合問題自身の中にある.問題を多くの異なった視点から観察すると,結果に関するさまざまな現象を見つけることができる.これらは問題の特徴であり,問題解決のための手がかりである。
2)バラツキを観察する.もし結果にバラツキがあればそれに対応して要因もばらついているはずであり,2つのバラツキを関係づけることにより原因を知ることが可能になる、これは主要な原因を同定する効果的な方法である。
問題の観察のポイントは,ケースごとに異なる.しかし,たとえば不良の解析では,少なくとも状態,部位,時間,条件,種類,などについての調査を行う。
a)状態
・寸法,変形などの状態
・破損,亀裂,漏れの状態
・異音,振動の状態
・ピンホールの形(丸い,楕円,角張っている,その他)
・キズ,汚れの状態(大きさ,深さ,まっすぐ,曲がっている,連続的,不連続,その他の形状)
・その他,欠陥の特徴
b)部位
・上部,側面,下部の部位で不良率に違いがあるか。
・製品が置かれた炉の中の位置(ドアに近い場所,覗き窓のそば,壁のそば,炉の中央)で不良率に違いがあるか。
・方角(東,西,南,北),高さ(頂上部,底部)で差がないか。
・製品が長い場合には,前,中央,後の部分で違いがないか。
・複雑な形をした製品では,まっすぐな部分,曲がった部分で差がないか。
C)時間
・工程からとられた連続する1個1個の単品間のバラツキ
・単品のグノレープ間のバラツキ
・バッチ間・ロット間のバラツキ
・時間ごと,シフトごと,日ごと,週ごとなどのバラツキ
・朝,昼,晩で不良率に違いがあるか
・月曜日から土曜日の曜日で不良率の違いがあるか
・週,月,季節,期,年ごとの違い
d)条件
・使用材料によって差がないか
・工場,ラインによって差がないか
・設備,作業者による違いがないか
・使用者(大人,子供,男,女)による違い
・仕向地(国内向け,輸出先)による違い
e)種類
・他社製品とで差があるか
・自社の異なる型の製品で不良率に違いがないか
・過去に作られた似た製品で不良率に違いがないか
不良の分析では上記の5つの視点のうち,該当するものについて行うことが必要であるがこれだけでは十分ではない.問題を,その特性にもとづいてさまざまな視点から調べる.違いがシャープに出る層別方法が見つかれば成功である
3)このステップでは現象の把握に徹することが大切である.原因は,次の「要因解析」のステップで考察する.ここでは問題の特徴を明らかにするために,結果に関する状況を正確に把握することが必要である。
4)これらの分析はデータにもとづくのが原則で,データにもとづかない情報(記憶や想像)はあくまでも参考である.しかし,これらの情報は時に重要な役割を果たすことがあるので,必要に応じて実験などで確かめる。
5)分析に携わる者は現場に行くべきである.机に向かっているのではなく,実際の現場に行くべきである.現場ではデータに現れない情報を得ることができる。この種の情報は化学反応での触媒のような作用をもたらし,思考過程において問題を解決する新しいヒントを与える。
現状把握の手順
現状を客観的にデーターで示し、悪さ加減を明らかにする。
*現状把握ポイント:
機械別、作業者別および時系列別等、色々な角度でデーターをまとめて、真の原因を追究する。
手順① 特性値の決定
現状把握は特性値を決めることから始まります。特性値とは、改善効果を測るための指標のことです。たとえば、不良ロスに関する改善テーマの場合、「不良率」、「不良件数」、「不良損失金額」などが特性値の候補です。「不良率」を特性値に選んだとすると、この後、不良率に関連するデータを収集し(現状把握)、不良率改善に関する目標を設定し、不良率で改善後の効果を確認することになります。
分類 | 特性値 | 定義 | 単位 | 算出式 |
品質 | 不良率 | 要求を満たしてない不良品の割合 | % | 不良発生数量/生産数量×100 |
直行率 | 要求を満たしている
良品の割合 |
% | 良品数量/生産数量×100 | |
生産性 | 故障率 | 故障の発生する頻度 | % | 故障件数/稼働時間 |
チョコ停止率 | チョコ停止が発生する割合 | % | チョコ停止件数/稼働時間 | |
コスト | エネルギー費 | 消費エネルギーの費用 | 金額 | 電力、水道、ガス代等 |
納期 | リードタイム | 着手から完成までの所要時間 | 時間 | 納期日–着手日 |
手順② 現物の観察
品質不良の改善では、不良品の現物をよく観察することが大切です。現物の観察により、いろいろな情報が得られるからです。たとえば、製品にキズが付いた不良の場合、キズの形状、深さ、場所、発生頻度などからどの工程でどのように発生したかを特定する手がかりになります。品質不良以外の故障、チョコ停などでも現場、現物の観察は重要です。
*ポイント:
ルーペ、顕微鏡等で現物を観察し、可能な限り測定し、真の原因を追究する。
手順③ 工程の調査
品質不良の改善では、どのような工程を経て対象製品ができあがっているのか調査します。工程などわかりきったことだと安易に考えず、今一度、丹念に調べます。
まず、どの工程の、どの設備で生産したか、次に、仕掛がり品としてどのように保管されていたか、どのように運搬されたか、最終工程まで直行したか、それともイレギュラーな検査が行われたか、製造中に異常はなかったかなどを調べます。調査方法は、日常記録している品質チェックシートや、オペレーターへのヒアリングが有効です。
手順④ データーの収集
(1)管理データを活用する
生産現場にはさまざまなデータがあります。みなさんは日々、生産量、稼動時間、不良数、不良項目などをチェックシートに記録していることでしょう。データが自動的に記録される職場もあると思います。これらは管理データと呼ばれます。
管理データの特徴は、すでにデータが手元にあり、あらたにデータを取る必要がないことです。ただし、精度などに難がある場合もありますがまずは管理データを活用し、特性値の現状把握を考えます。
(1)調査データを取る
自分自身で新たに収集するデータを調査データと呼びますが、できるだけ最新データを活用するという観点からも、調査データを取ることは有効です。
あらたにデータを取ることはかなり大変な作業で、時間や費用もかかるので、データを取る前にポイントを整理しておきましょう。
- 必要性………あらたに調査データを取る必要が本当にあるか?
- データの種類と量……どのような種類のデータが、どのくらいの数、必要なのか?
- 実現可能性……………実際に取ることができるデータか?
- データ取得の効果……あらたに取った調査データを活用することによって求める結果は得られるのか。
手順⑤ データーの層別、見える化
データを収集したら、ただ単に、データを表の形で示すのではなく、グラフ化して視覚化したり、層別したりして、何か問題なのか明らかにする必要があります。
(1)時系列で示す
過去から現在までの特性値の変化を、折れ線グラフで表します。たとえば、毎月の不良率の変化をグラフ化します。これにより、ある時期を境に急に悪化した、不良率が増加傾向にある、といった情報が得られます。なぜ不良率が増加したかについては、次の要因解析ステップで調べます。
(2)比較して示す
他の設備、他の工程、同業他社などと比較したデータを、棒グラフで表します。他の設備などと比較してどの程度差があるのか、悪さ加減を示すことができます。
3)バラツキを示す
データの平均値だけでなく、バラツキを調べます。ここで活用するのがQC7つ道具のヒストグラムです。たとえば、製品の寸法や重量などのデー夕をヒストグラムで表します。これにより、データが規格値の上限・下限の幅に入っているか、異常値はないか、などがわかります。
4)層別して示す
機械別、材料別、人別、方法別などデータを層別して問題を明らかにします。層別はQC7つ道具の1つです、簡単に言うと「分ける」ということです。
現状把握のポイント
① 数値、データーで示す。
データで説明するとは裏を返せば「言葉による説明ではない」ということです。不良が少ないと言っても0.1%か5%なのか分かりません。上司や改善チー厶のメンバーなど、誰もが同じように理解できるようデータで示すことが大切です。
ポイント② 現状把握の「現状」は「現時点」だけではない
現状把握の現状とは過去から現在にいたる一定期間の状況と理解してください。現状と言っても現時点のことではありません。つまり、直近1ヵ月のデータを取るのではなく、少なくとも数力月、状況によっては過去1年間のデータを取る場合もあります。
②層別する
層別とはデータを時間別、人別、環境別などいくつかのグループに分けることです。データを層別することによって良いときと悪いときの差が表れます。
たとえば、ある製品を1号機と2号機の2台で製造しているとします。
2台分のデータを層別してみたら不良は1号機が圧倒的に多かった、といったケースです。
層別の仕方
項目 | 内容 |
時間別 | 年別、季節別、月別、週別、曜日別、日別、午前・午後別、時間帯別、作業開始直後と終了直前の別など |
作業者別 | ライン別、係別、年齢別、経験年数別、男女別、作業者別など |
天候別、温度別、湿度別、照明別、作業室別など | |
材料別 | 材料の種類別、グレード別、納入業者別、ロット別、製造工場別など |
方法別 | 作業方法別、測定方法別、サンプリング方法別、運搬方法別など |
加工条件別 | 電圧、電流、圧力、速度、回転数、温度など |
機械別 | 機械の種類別、新型・旧型別、大・中・小型別、メーカー別など |
現状把握と要因解析の混同
現状把握と要因解析を混同している例が少なくありません。
区別の考え方は、データを整理・層別して、悪さ加減を把握する段階までが現状把握、現状把握をふまえて、なぜその状況が発生したか追求する段階が要因解析です。
たとえば、不良低減のテーマで、収集したデータを層別し「機械の2号機が他号機と比較して約8%以上不良が多い」という段階までが現状把握、それを踏まえて「なぜその差発生するのかを調査する」という段階が要因解析です。
目標設定
目標設定では、①どこまで改善するか目標値を決める②いつまでに行うか期限を決める、の2つを明確にします。
目標設定例:○○工程の寸法不良を0%にする(12月迄)
目標設定の手順
手順① 目標値の設定
目標値の水準を決めます、不良、チョコ停などのテーマはゼロを目標とします。
ゼロを目指すことにより、要因を徹底してあげる、従来と同じ発想では解決できないから違った発想が生まれるなど取り組む姿勢がまったく変わります。
ゼロ目標を達成するため、テーマは細分化します。テーマの細分化とは次のように説明できます。品質不良の項目が、汚れ、キズ、寸法不良などいろいろあるとします。このままテーマを「不良のゼロ化」としてしまうと汚れもキズも寸法不良も一気にすべてゼロにすることになります。これではテーマが大きすぎて、どのくらい時間がかかるかわかりません。そこでテーマを細分化します。まず汚れゼロに取り組み、次にキズゼロ、寸法不良ゼロと、不良項目を1つひとつ片付けていきます。
手順② 期間を決める
目標達成までの期間を設定します。期間は3ヵ月程度とするのが一般的です。
長い期間を設定すると活動がマンネリ化するためです。活動期間1年の大テーマを掲げるのではなく、テーマを細分化して期間を3ヵ月程度とするのがベターです。
『目標設定事例』
1日あたりの生産量を300個から400個に増やすため、2000年7月までに、1回当たりの段取り調整時間60分を20分に短縮する。
特性値:1回当たりの段取り調整時間
目標値:20分/1回
期限:2000年7月
目標設定のポイント
① 業務目標は達成しなければならない!
達成したい目標を設定したのだから達成することが基本姿勢です。
特に会社や職場にとって意味のある『目標設定』の場合はなんとしても達成しなければならない必達目標です。
一方、QCサークルのテーマではメンバーのやる気を引き出すために目標を高め設定することがあります。この場合は事情が異なり、メンバーの人材育成を主眼にが達成できれば大いに自信がつく」という理由で目標設定することが多いため、設定値自体の根拠は明確ではありません、目標値達成の優先度はやや下がります。
又、目標設定時点では技術面や費用対効果の面で不確定要素が多く、達成できるかどうかわからないことがある点です。要因解析以降のステップを進めてはじめてテーマ解決の困難さがわかる場合もあるため、目標設定のステップで掲げた目標について、必達か希望か議論することはあまり意味がありません。
NG 目標設定 事例 5%削減目標
ロス削減が進み、乾いた雑巾を絞るような改善を継続している会社ならともかく、ロスが相当残っているのに「5%削減」といった低い目標を掲げるケースです。
5%は誤差の範囲。ちょっと意識を上げるだけで何もしなくても達成できてしまいます。こんな目標は意味がありません。
また、数値目標が入っていない「○○の生産性向上」とか、「○○不良低減」といった目標設定も不可です。目標があいまいだと活動もあいまいになります。
活動計画
活動計画では、誰が、いつ、QCストーリーのどのステップを、どのように進めるか検討します。
活動計画例:○○工程の寸法不良を0%にする(12月迄)
活動計画の手順
手順① 誰が、いつ、何をするか検討する
このステップでは、まず、要因解析以降のステップで、何を、どのように進めるか、具体的に検討します。たとえば、設備に起因する品質不良が発生していることがわかったなら、設備の機構図を描き、機構と不良の関係を分析することになります。
次に、それを誰がいつまでに行うか、日程を決めます。一般的には要因評価、対策立案などのステップごとに担当者を決めます。ここでの担当者は、あくまでそのステップを中心的に進めるステップリーダーであって1人で各ステップを全部やるということではありません。
手順② 活動計画表を作成する
活動計画表でもっともよく使われているのがガントチャートです。ガントチャートはガントが考案したツールで、活動計画やプロジェクト管理などに使われる帯状の図表のことです。バーチャートとも呼ばれます。
ガントチャートでは、実施項目を決め、各項目の担当者を選定し、日程を定めて計画表を作成します。活動を進めながら実績も記入します。すなわち、ガントチャートは日程計画と進捗管理の機能を併せ持っているのです。
ガントチャート作成
計画を破線、実績を実線で記入します。計画の線を引くときは、各ステップで何をするのか、どのくらい時間がかかるのか、具体的にイメージしながら線を引きます。うまく計画ができれば、その後の活動もうまく進みます。
NG 活動計画 事例
問題あリ① 検討不足の「各ステップ1ヵ月ずつ」
各ステップの活動イメージがないまま「各ステップ1ヵ月間」で均等に計画線を引くケース。活動内容を何も考えていない証拠で、後で苦労することになります。
問題あリ② やる前から長期戦の活動計画
1つの改善テーマは3ヵ月程度で解決できるようにします。長すぎると進捗管理が難しく、テーマをたくさんこなすこともできません、本当にそれだけの期間が予想される場合はテーマを細分化してマンネリ化を防止します。
問題解析、要因解析
加工のメカニズムを理解したうえで、不具合の発生メカニズムを明らかにします。これにより真の原因をつかむステップです。
要因解析例:①特性要因図⇒寸法不良の要因の抽出、優先順位決定
②要因の検証
何が主な原因であるかを見いだす活動
①仮説を立てる(原因の主たる候補を選ぶ)
a)可能性のある要因に関するすべての知識を集めるために特性要因図を描く
b)「現状把握」の段階で得られた情報を用い,明らかに関連がないと思わる要因を消去する。残った要因を用いて特性要因図を書き直す。
C)作り直した図で,主な原因である可能性が高いと思われる要因に印をつける。
②仮説を検証する(侯補の中から主な原因を引き出す)
a)新しいデータをとったり実験を行って,原因である可能性が高いと思われる要因が特性に与える効果を確認する。
b)調べたすべての情報を総合して,どれが主な原因であるかを決定する。
C)可能ならば,問題を意図的に再現する。
QC七つ道具の特性要因図によるQC要因解析
このステップは2つの部分に分けられる。1つは仮説を立てることであり,ほかの1つは仮説を検証することである.この2つのステップを踏むのは,原因を科学的に決定するためである.多くの例で,問題の原因が関係者の議論によって,あるいは1人の人間の独断によって決められている.このような類の決定で誤りが起こりやすいのは,仮説の検証のステップが省略されるためである。
原因(仮説)を考えるときは,データを解析する.その結果,妥当と思われる原因(仮説)が見つかると,これで仮説の正しさが検証されているという錯覚が起きやすい。しかし,仮説を立てることとその検証を行うこととは別のことであり,同じデータを両方に用いるぺきではない.仮説の検証に際しては,仮説を立てた時に用いたものとは別のデータが必要である。
————————————————————————
仮説を立てること。
仮説を立てるには,特性要因図が有効な道具である.特性要因図の中のすべての要因は,問題の仮定された原因ある.図には最終的に主な原因と確認される要因が含まれていると期待されしているが,これが抜けていることもないわけではない。
a)図の中で,特性はできるだけ具体的に書く。抽象的な言葉を用いると,要因の数は膨大なものになってしまう.抽象的な表現は一般的であるために,個々のケースには該当しない、部分を含んでいる.たとえば外観特性の1つであるキズ不良をたんに「キズ」と表現すれぱ,特性要因図の中の要因は一般にキズを引き起こす要因を集めたものとなる.これには,すりキズ,押ししキズ,かきキズ,その他すぺてのキズについてその要因を集めることになり,いろいろな要因が入ってくる。しかし,特性として「○○部位のすりキズ」とすれば○○部位のすりキズを発生させる要因に特定されるため,対策に結びつきやすなる。
特性を具体的に表現すればするほど特性要因図は効果的になる。
b)最初に問題解決に関わる者すべての意見を反映させた特性要因図を書く
.しかし,これらの要因の影響をすべて解析することは効果的でないので,次の段階でデータにもとづいて要因の数を減らすことが必要である.このためには「現状把握」のステップで得られた情報が有効である.結果のバラツキに合致しない要素は図から除く。
たとえば,不良が午前に多く午後に少ないとしてみよう.使用されている原料はどちらの時問も同じであれぱ,結果に合わないので「原材料」を図から外す.しかし,午前と午後とで使われる機械の状態が変化している可能性があれば,結果に合うので「機械」を図の中に残す。
ハンダづけの解析で作業者によって不良の発生率が大きく異なることがわかたとしよう、作業者がみな同じハンダを用いていれば,ハンダの組成に関する要因は削除することができる.また,同じワット数のハンダごてを使っていればハンダごての使用電力量に関する要因は削除することができる。
このように結果のバラツキの状況が「現状把握」のステップで調べられていれぱ,可能性があると思われた多くの要因の中で結果と合わないものを図から外すことができる、このように原因では有りえない要因を外した後,残った要因で特性要因図を作り直す。要因の数が少なくなればなるほどよい。
C)作り直された図の中の要因が問題の原因である可能性がすべて等しいわではない、「現状把握」のステップで得られた情報,ここで検討された事柄にもとづき,可能性によって要因のランクづけを行い,主要な原因の候補を絞る。
————————————————————————
仮説を検証する。
これらはいまだ原因の候補である.ここで立てられた仮説が正しいかどかを判断するために新しくデータをとる実験や調査を行い仮説の検証を行い、データーは,注意深く計画して収集しなければならない。
a)取り上げた要因と結果との問に関係が認められれば,どのくらいの強さの関係であるか,言い替えれぱ,その要因は特性にどの程度の影響を持つかを調べる。そのような関係の強さを表すためにいくつかの方法,たとえば,相関係数,分散分析,原因によるパレート図がある、関係の強い要因に手を打つことができれば効果はそれだけ大きい。
b)「投票」をして主な原因を決めてはならない。投票によって決めることは民主的な方法であるが,科学的に正しいという保証はまったくない。全員一致で要因を選んでも,調査の後にその原因ではないとわかった例はたくさんある。
c)原因の解析をせずに是正処置がとられることがある.効果のありそうなすべてのアクションが実施される。もし,結果がよければそれで問題解決が終わったとみなされる。このやり方では,たとえ問題が解決され,是正処置が問題解決に有効であることがわかっても,結果と是正処置が1対1に対応しないので,多くの場合真の主要な原因を見つけることはできない.関係のない要因を主要な原因とみなしてしまい,迷信を生み出す温床となる。
d)原因であることの証拠は,意図的に欠陥を再現することでも得ることができる、しかし,そのような再現実験は慎重に行わなければならない。
原因と思われるユニットを用いて不良品ができたとしても,このことはそのユニットが不良の原因であることを100%意味してはいない。ほかの要因が欠陥の原因であるかもしれない。再現される欠陥は,「現状把握」の段階で明らかにされた不良品と同じ特徴を持っていなければならない。
意図的な再現は,仮説を確かめる効果的な手段ではあるが,人的,社会的,実際的(時間的,経済的)な理由のために突施できないこともある.そのような場合には,「現状把握」「要因解析」の段階をより注意深く行わなければならない。
要因解析の手順
手順① 加エメカニズムを理解する
設備が原因で品質不具合が発生していると考えられる場合、加工点を中心とした加エメカニズム、つまり加工の仕組みを理解することが重要です。
そのために有効なのが設備の機構図を描くことです。
加エメカニズムを理解せずに要因解析を行うと、推測で要因をあげることになってしまい、真の原因を追求できません。
手順②不具合発生のメカニズムを検討する
加エメカニズムを理解した上で、不具合現象をよく観察し、不具合発生のメカニズムを検討します。
再現頻度が少ない不良の場合および高速の場合はビデオカメラを設置し不良現象を観測する方法が良く取られています。
手順③ 要因を洗い出し、検証
不具合発生のメカニズムがわかったところで次は要因の洗い出しです。
要因の洗い出しは4M(作業者・機械・材料・作業方法)の切り口で行います。特性要因図を活用すると効果的です。
4Mの要因例
作業者 | 作業標準を厳守しているか? | 材料 | 等級はOKか? |
スキルは十分か? | ロットのバラツキは? | ||
人員配置は適正か? | 保管状態は? | ||
体調は良いか? | 取扱い方法は? | ||
機械 | 工程能力に合っているか? | 作業方法 | 温度、湿度等の作業環境は? |
清掃は適切か? | 作業標準は良いか? | ||
給油はOKか? | |||
異音はないか? |
手順③ 要因を洗い出し
関連サイト:特性要因図の作り方
手順③真の原因を明らかにする
要因の洗い出しや検証の結果、何か真の原因なのかを明確にします、原因追求に当たっては、なぜなぜ分析も効果的です。
関連サイト:なぜなぜ分析
手順④ 要因の検証
次に、洗い出した要因が「真の原因」であるかどうか検証します。検証作業は再現テストを行ったり、データで関連性を調べたりします。検証のやり方に決まった方法はありません。状況に応じてQC7つ道具のグラフや散布図などを活用することなります。
要因解析のポイント
考えられる要因をもれなくあげること
要因解析で重要なのが、発生メカニズムをふまえて、理屈で考えて正しい要因をもれなくあげることです。要因解析に特性要因図を使う場合、一般にブレインストーミングで要因を数多くあげることが推奨されていることもあり、数多くあげることが目的化して、関係ない要因まであげていることも多いようです。いろいろな視点で要因をあげることは良いのですが、真の原因をつかむステップであるので発生頻度が少ないと思われる要因は除外します。
《用語》
要因と原因…要因と原因はよく似た言葉であるが、要因は容疑者、原因は真犯人と考える。容疑者(要因)が真犯人(真の原因)である可能性もあるが、真犯人と決まったわけではない。捜査過程で複数の容疑者を洗い出し、その中から真犯人を絞り込むように、特性に対して考えられる要因を洗い出し、その中から真の原因を追求する
NG 要因解析 事例
問題あリ① 思いつきで要因をあげる
現象の観察が不十分、設備の機構図を描いていないなど、加エメカニズムや不具合発生メカニズムを理解しないまま要因をあげるやり方は問題です。事実を無視して推測で要因をあげていることになります。これでは効果は期待できません。
問題あリ② 原因を決めつける
せっかく特性要因図などを使って要因を整理したのに、話し合いで重要と思われる要因に○を付け、真の原因としてしまうやり方もいまだに多くの企業で見られます。○を付けたからといつて真の原因と決まつたわけではありません。真の原因かどうか検証する必要があります。
また、重要と思われる要因だけに目を付け、その他の要因を無視するのも問題です。論理的に「問題だ」と考えたなら、影響が小さいと考えられる要因も対策を講じるべきです。小さな不具合を重視する考え方は、特に、慢性化した不良対策に有効です。
要因解析の事例
加工メカニズム
①2個の吸口で用紙を1枚ずつ吸引して分離して引き上げ、フィーダーボードに送る。
②用紙はフィーダーボード上をベルトで送られる。
③ツメが用紙をつかんで、圧胴に受け渡す。
不具合発生メカニズム
用紙が水平に吸い上げられず、左右のバランスが崩れたままフィーダーボードに送られる。
ツメが用紙の一部をつかまないので、つかまなかった側がばたつき、つまるため、チョコ停が発生する。
要因の洗い出し
吸口の破損、左右の吸口の高さが異なる、吸口の位置が要因である。
真の原因
要因を1つずつ検証・再現テストを行った結果、吸口の破損、左右の吸口の高さが異なることが真の原因と判明
対策の立案と実施
応急処置的な対策に終わらずに可能な限り発生源を断つ対策を打つことです。
対策立案 事例:○○工程の寸法不良を0%にする(12月迄)
要因 | 対策 | 実施日 | 担当 |
①ワッシャーの忘れ | 刃先調整後の確認項目リストに追加 | 7月11日 | 小林 |
②刃先の調整ミス | 調整用ゲージを作成 | 7月20日 | 田中 |
③ベルトの緩み | ベルト交換 | 7月23日 | 近藤 |
対策立案と実施の手順
手順① 対策案を検討する
要因解析ステップで追求した真の原因に対し、アイデア出しの方法を活用して対策案を検討します。
(1)ブレインストーミング
多くのメンバーによる話し合いの中でアイデアを出し合うことにより発想の誘発を期待する方法です。次の4原則を守りながら話し合いを進めます。
原則1 判断・結論を出さずアイデア出しを重視
原則2 自由奔放な意見を歓迎する
原則3 アイデアの質より量を重視する
原則4 他のメンバーのアイデアを元にさらにアイデアを出す
2)改善の4原則(ECRSの原則)
排除、結合、交換,簡素化の4つの英語の頭文字を取ってECRSと呼ばれます。これらを単独、または組み合わせて改善案を検討します。
手順② 対策案を評価し対策を決める
どの対策を講じれば安い費用で目標を達成できるか検討します。できれば複数の対策案を評価し、実施する対策を決定します。実施した場合に他の不具合が発生しないかも検討します。評価のポイントは効果、実効性、経済性の3つです。
(1)効果………効果の上がる対策か
(2)実効性……実現可能な対策か
(3)経済性……費用対効果は十分か
対策立案と実施のポイント
ポイント① 発生源対策を心がける
清掃頻度を上げる、点検頻度を上げるといった方法はではなく、バラツキの元を断てないか、といった発想で対策を検討します。
対策事例
現象 | 発生源対策 |
射出成型工程で、スクリューの傷、摩耗、破損が炭化物(異物)の発生源になっていた。 | 破損個所を修復し、メッキ加工を行い、樹脂の滞留を防止した。 |
押し出し機で、排気ダクトからの油漏れがラミネート不良の原因になっていた。 | ダクトの形状を変更し物理的に油が落下しないように改善した。 |
オフセット輪転機の折り工程で、用紙の折り曲げ部が破れる現象が問題になっていた。 | 用紙含水率と破れの発生に相関関係があることがわかった。装置内に加湿装置を設置し用紙含水率を常時監視するようにした。 |
NG 対策立案と実施 事例
問題あり いつ対策したかわからない
対策を実施した日はしっかり記録しておく必要があります。対策実施日がわからなければ効果確認のしようがないからです。たとえば、機械トラブル対策を実施したものの、いつ対策を実施したかはっきりしないとします。
あとになって効果確認しようとしたところ、対策を実施したと思われる日の前後に同様のトラブルが発生していた場合、そのトラブルが対策後に発生していたなら、対策は効果がなかったことになります。
対策の種類 暫定対策と恒久対策
1)対策処置には,2種類ある、1つは,現象(結果)を除去するものであり,他方は結果を引き起こした原因を除去するものである。手直しが可能であれば,それで不具合をなくすことができる。しかし,手直しでその再発を防ぐことはできない、くり返しのある仕事では手直しでは問題の解決にならないのである。
問題の原因を取り除く対策をとり,問題が再発しないようにすることである。
この2つの種類の対策処置を混同してはならない。
2)是正対策処置は,しばしば別の問題を引き起こす。対策処置のもたらす副作用を防ぐために,対策処置についてできるだけ広い視点から評価し,その妥当性を判断しなければならない。可能ならば実験も行うべきである。副作用が起こることがわかれば,ほかの対策処置あるいは副作用に対する対策処置を考えなければならない。
3)対策処置を選ぷ際の重要かつ実際的なポイントは,関係するすべての者の協力が得られるかどうかである。原因を取り除くための対策処置は,現在の仕事にさまざまな変化をもたらす。対策処置はすべての者が受け入れるものであることが望ましい。いくつかの対策が可能であるならば,対策のとりやすさと効果のバランスを考えてもっとも効果的な手段を選定する。
効果確認
目標値をクリアーしたか、改善前と同じ条件でデーターを取り、比較します。
効果確認 事例:○○工程の寸法不良を0%にする(12月迄)
効果確認の手順
手順① 効果をデータで把握する
効果確認のためにデータを取る必要があります。データを取るときは次の2点に留意します。
(1)対策前後を同じ特性値で比較(対策前がキズ発生率なら対策後もキズ発生率)
(2)対策前後を同じ条件でデータを取り比較(対策前が1週間のデータなら対策後も1週間)
手順② 有形効果と無形効果をまとめる
効果確認の最後の手順です。
- 有形効果
特性値がどのくらい改善したか(例:キズ発生率が×%から○%に改善した)を示し、効果金額を算出します。
- 無形効果
第一線オペレーターのサークル活動の場合、有形効果以外に無形効果を期待されている場合が多いものです。無形効果とは、改善手法が身に付いた、リーダーシップが身に付いた、チームワークがよくなった、積極性が出てきた、問題意識が向上した、など数値で測りにくい項目の効果のことです。
効果確認の事例
効果確認のポイント
ポイント① 効果は金額で表す。
企業業績は売上や利益など金額で表され、改善活動の目的は企業業績向上です。ですから改善活動の効果も金額で表す必要があります。この改善でいくらもうかったのか、明らかにするのです。
金額で表すことにより、ロス削減や原価削減計画の達成度を測りやすくなるほか、コスト意識の向上やメンバーのモチベーションアップにつながります。
儲かっていない会社は倒産しますが儲かっている会社は生き残れます。
NG 効果確認 事例
問題あり① いつになっても効果確認できない
製品を対象とした改善活動(A製品に良品率向上など)に取り組んだ場合、対策立案・実施していざ効果確認しようとしたら、次回生産は3ヵ月後たった、ということがあります。効果確認ができないまま無為に時間だけが過ぎていきます。
そもそも特定の製品を対象としたテーマは可能な限り避けること、やむを得ない場合は代用特性などで速やかに効果確認する方法がないか検討する。
歯止め(標準化と管理の定着)
歯止めは問題の原因を恒久的に除去する標準化と管理の定着化のふたつの活動のことです。
①改善を定着させるために,作業にの方法の5W1H,すなわち誰が(Who),いつ(When),どこで(Where),何を(What),何故(Why),どのようにして(How),を定める。
②これを標準として文書化し,正式に発行する。
③この標準の教育と、訓練を行う。
④標準が守られているかどうかをチエックする仕組みを設ける。
歯止め 事例:○○工程の寸法不良を0%にする(12月迄)
歯止めの手順
手順① 標準化する
対策にあげた管理項目を盛り込んだ基準書や標準書を作成します。
同時にチェックシートも改訂し、漏れなく日常作業に落とし込みます。基準書や標準書の制定・改訂は社内手続きに従って行います。守りやすくわかりやすい基準書になっていること、関係者の了解を得ていること、前後工程など関係者に連絡することが重要です。
手順② 必要な教育・訓練を行う
変更内容をメンバーに教育する必要があります。サークルリーダーが基準書を改訂するものの、教育・訓練を行わず、それで終わりというケースが多いようです。
基準書を守って作業するのはオペレーターですから、当該作業を行う全員が基準書を守れるように教育・訓練します。
手順③ 維持管理の定着をはかる
管理図や積上げ棒グラフなどの管理グラフを用いて特性値の推移を日々、月次で確認します。
歯止め(標準化)の事例
新たに追加した作業内容を基準書、標準書に記載し、教育を実施。
歯止め(管理の定着)の事例
管理図を用いて管理の定着化を図る。
歯止めのポイント
ポイント① 標準化は5W1Hで
標準化の際は5 W 1 Hを心がけます。
Why なぜ
When いつ
Who 誰が
Where どこで
What 何を
How どのように
NG 歯止め 事例
問題あり 標準書を作成・改定していない
意外に多いのは、改善活動の報告書には○○のルールをつくり、それを守ります」と書いてあるのに、実際は標準書の作成・改定や周知徹底ができていないケースです。
効果確認まで終えて安心してしまっているようです。何年たっても、人が代わっても、確実に維持管理できるようルールを文書で残します。
歯止めと標準化の意味|QC、小集団、TPM活動のまとめ
問題が今後に再発しないように歯止めすなわち,是正処置を標準化しなければならない、標準化には2つの理由がある.1つは標準化しなければ問題を解決するために取られた処置が,人の移動とともに、忘れられてしまい,定着しないからである。
ほかの1つは標準は新人(新たに採用された者,配置替えできた者,パートタイムの作業者)の教育訓練に必要だからである。
標準化は,作業の手順をたんに文書にするだけでは達成されない。標準は作業者の考え方や習慣の一部にならなければならない.関係者に対して標準を実施するために必要な知識や技術の教育と訓練を行うことが大切である。
1)作業の手順を表現するのに5WlHを用いるとよい.たんに1つの「H(How)」を示したものが標準とよばれたり,「何故(Why)」を除いた4つのWと1つのHが示されれば十分とされることもある.仕事は,「何故」がなくても実施できるからである.しかし,仕事を本当に理解するためには「何故」は大切な要素である。結果を得る方法は標準で定められた方法の他にもたくさんある。
そのため,標準化された方法を用いなければならない理由を作業者が知らない場合には,標準以外の方法で行うことがある.「何故」は標準の必要性の理解に必要なのである.QCストーリーは「何故」を理解するためのよい道具である。標準の教育・訓練を行う場合には,それに関連があるQCストーリーも紹介するのがよい。
2)標準は文書化され,適切に伝達されなければならない.新しい標準が導入されたときに起こる混乱の主な原因の1つはこれが徹底しないことにある。新しい標準を適用するには,仕事のやり方を変えなければならない、この際の些細なミスで混乱が引き起こされる。
とくに仕事を分割して行う職場である。
部署では新しい方法が,別の部署では依然古い方法が用いられると問題が起こる。
3)教育と訓練は,標準が遵守されるためにくり返し行うことが必要である。
組織が教育を怠っている場合には,標準は空文化し,問題が再発する。
4)問題の再発を防ぐために,標準の教育・訓練と合わせて標準が遵守されているかどうかをチェックする管理の仕組を設け,それに従って目常管理が行われることが大切である。
今後の課題
問題解決の手順を見直し,将来の仕事の計画を立てる活動
①残された問題を挙げる。
②今後何をすべきであるかを考えその手だてを講じる。
③改善活動の中でうまくいったこと,いかなかったことを整理する。
TQCサークル発表資料、発表事例に活かす
1)問題が完全に解決されることはまずなく,理想的な状況は得難いものである.しかし,完全を目指して1つのテーマについて同じ活動をあまり長く続けることは必ずしもよいことではない.最初に定めた期限がきたら,活動に区切りをつけることが必要である。目標が達成されていなくても,活動がどこまで進んだか,何が達成されていないかを一覧表にまとめるのがよい。
2)残された問題について今後どのように対処していくかを考え,将来なすべき事項を明確にする。その事項の中で重要な問題は,次の改善のテーマとして取り上げる。
3)最後に問題解決の方法について反省する.これを行うことにより,今後行われる問題解決活動の質を高めることができる.実際に実行された活動と実行されるべきであった活動には常に差がある.間題が解決された場合でも見直しを行うべきであるが,期限が過ぎて問題が解決できていない場合にはいっそう注意してこの「反省」をしなければならない.未解決の問題は,次の機会で取り上げ,別の方法で解決に向けて挑戦する。
*実際にQCストーリーを効果のある活動にするにはファシリテーションのスキルが必要です、良いファシリテーターがQC活動を推進すれば効果の上がる会議ができ、成果がでます。
関連記事:ファシリテーション入門【図解】
QCサークル活動 発表テーマ ストーリー事例集
下記のサイトにてQCサークル、小集団活動発表事例、テーマ事例が掲載されています。
参考になるQCサークル発表資料がありますのでQCサークル活動、小集団活動を進める際にお役に立ちます。
関連記事:小集団活動、QCサークルの発表資料事例
8D とは|問題解決のため米国版 QC手法
日本のものづくりを研究してフォード・モーターは問題解決のプロセスとして「8D プロセス」を開発し、これを元にして品質管理向上への取り組みを行いました。
8D プロセスでは以下の 8 つ+ 1 つのプロセスを踏んで問題解決が行ないます。
0. 計画と前提条件、スケジュールの線引きなど
1. チームの結成(必要な技能、権限を持ったメンバーの招集)
2. 問題の客観的事実の詳述(5W2H、5Why などを用いた問題改善)
3. 応急処置(お客様への影響を最小限とするための応急措置)
4. 根本的な原因解明(QC七つ道具の活用)
5. 原因根絶及び問題解決措置
6. 対策の実施及び監視
7. 次の品質向上テーマ(適応した解決策の標準化)
8. チームの祝福(チームの貢献の明文化と組織全体からの貢献度合いの認知)
QCサークル活動とQCストーリー
TQC活動を進める上での重要な活動がQCサークル活動です。これは,現場の管理者や監督者と作業者の品質意識の高揚と,品質管理活動の推進を目指すための小集団活動のことです。
そしてそのQC活動を支えている手法がQCストーリーです。
TQCの特徴の1つがみんなでやる品質管理ということができます。このため従業員一人一人の資質を向上させることで,より良い品質管理が可能となるのです。
そこで,作業現場で小さな集団を作り,どうすればより良い製品を作ることができるかという意識のもとに,そのメンバーがお互いに意見を出し合ってQCの手法を活用して改善していくことにより,従業員が意欲を持って働く楽しみを味わいながら作業を行う小集団活動,すなわちQCサークル活動が盛んに行われています。
QCサークルによるテレワーク導入
厚生労働省が働き方改革推進の取り組みとしてテレワークを推薦しており、PDCAを用いたテレワーク導入をWeb上で掲載しています。
関連記事:テレワーク導入
まとめ
QCストーリーは、品質改善活動において、問題を科学的に分析し、効果的な対策を立案・実行するための強力なツールです。QCストーリーを活用することで、組織全体の品質レベルの向上に貢献することができます。
関連キーワード: #品質管理 #品質改善、 #問題解決、#PDCAサイクル、#5S
スライドシェアー ダウンロード資料
QCストリー~問題を解決ための手法~がスライドシェアーでダウンロードできます。
おすすめ参考図書
参考イラスト:
QCサークルのためのカット集―OHP・体験談報告にすぐ使える
【アマゾン おすすめ本 QCストーリー 】
コメント
[…] 関連記事:問題解決手法 QCストーリー […]
[…] 日本のものづくり~品質管理、生産管理、設備… 3 users問題解決型手法 QCストーリーとは?【図解】https://takuminotie.com/blog/quality/%ef%bd%91%ef%bd%83%e3%82%b9%e3%83%88%e3%83%bc%e3%83%aa%e3%83%bc% […]