3分で分かる! AIでなぜなぜ分析 概要解説
「なぜ?」を5回ほど繰り返して根本原因(真因)を特定する手法。製造現場や品質管理で使われます。
どうしてAIが活用されるの?
従来のなぜなぜ分析は「人の思考」に頼っていたため、以下の課題がありました。
従来の課題 | AIのメリット |
---|---|
思い込みやバイアスが入る | 膨大なデータから客観的に分析 |
経験の浅い人だと難しい | 過去の類似ケースを自動で参照可能 |
時間がかかる | 瞬時に候補原因を複数提案できる |
AIでなぜなぜ分析をするステップ
-
インプットを与える
-
例:「製品Aで不良率が上昇した」
-
-
AIが仮説を出す
-
「なぜ?」→「温度センサーが誤作動」
-
「なぜ?」→「センサーの定期点検が未実施」
-
-
人がレビュー&選定
-
AIの提案を人間がチェックし、実際の現場と照らし合わせて絞り込み
-
◆ 活用シーン(例)
-
製造ラインの不具合解析
-
顧客クレームの原因調査
-
サービス業のトラブル対応
注意点
-
すべてをAI任せにしない:AIは候補を出すが、現場判断が最終決定
-
データの質が命:過去の記録が正確でないと、的外れになる可能性も
まとめ
ポイント | 内容 |
---|---|
分析手法 | 「なぜ?」を繰り返して根本原因を探る |
AIの役割 | 仮説提案、過去事例との照合、時短 |
人間の役割 | 現場との整合性チェック、意思決定 |
成功のカギ | 良質なデータ × AI × 現場の知恵 |
以下に『トヨタ式 なぜなぜ分析』についての基礎知識を纏めています。
具体的な『chatgptによるなぜなぜ分析をする場合のプロンプトの指示』の解説は最後の章に記載しておりますので『基礎知識』が不要な方は飛ばして読んでください。
トヨタ式 なぜなぜ分析とは?
「なぜなぜ分析」は、品質管理、労働安全管理などの分野で真の原因を探す為に使われる手法です、発生した問題事象の根本原因を探るために、「なぜ?」とくりかえして掘り下げていく。別名「なぜなぜ5回」とも呼ばれる。トヨタが発祥の地であり、トヨタ生産方式の普及とともに、他の業界や分野でも使われています。
トヨタ式なぜなぜ分析とは?
なぜなぜ分析は問題の根本原因/原因に到達するために障害が発生 した理由を5回以上質問して真の原因を追究する手法です。
現場の問題には複数の要因があり、真の原因をタイムリーに現場で 見つけ、現場で解決する為に考えられた根本問題解析(RCA:Root Cause Analysis)の ひとつです。
トヨタでは一般的な5W1H(いつ、どこで、誰が、何を、なぜ、どのように)をさらに深掘りし、「なぜ」を5回繰り返すことで、問題の本質に迫り、真の改善策を見つけるための思考法です。
関連記事:問題解決フレームワーク 5W1H思考とは?
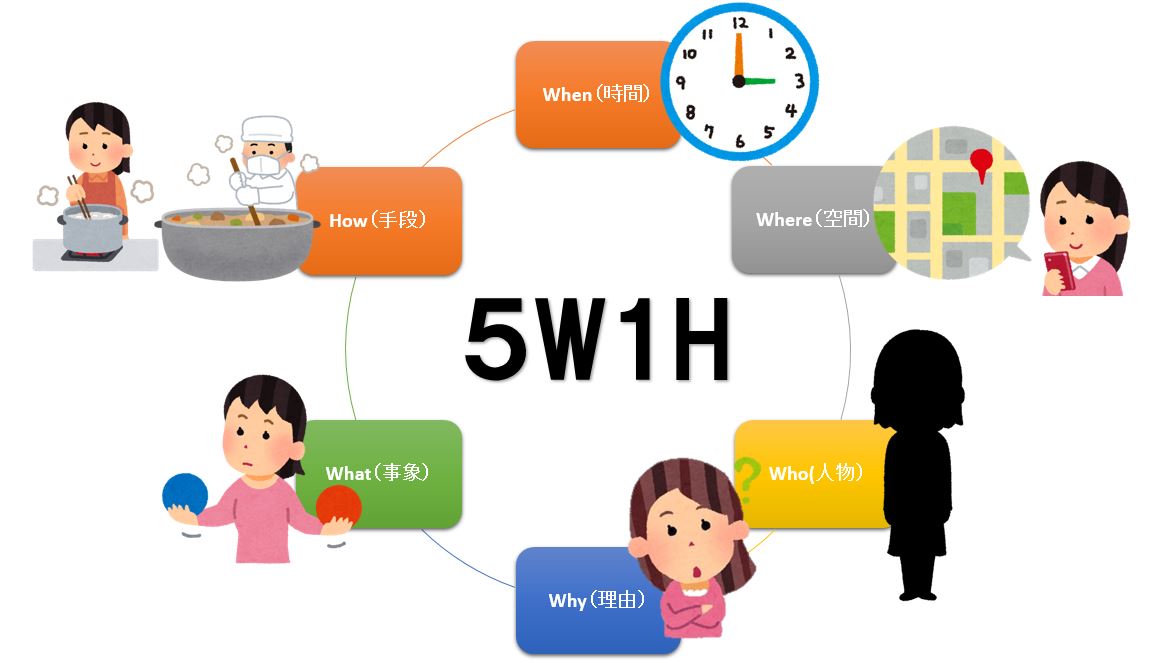
トヨタ式なぜなぜ分析の目的
目的は「問題の真の原因を見つけ、その対策で再発防止する」ことです。 但し、真の原因の追究は現場で即時に改善が対応できる範囲にします。 システム、ヒューマン的な範囲、全会社レベルでの範囲まで拡大しません。あくまでも現場レベルの追究です。
トヨタ式なぜなぜ分析の特徴
・推定定される要因を考えるのではなく事実 (fact)の原因を見つける、存在しない要因や 不明の要因は検討の対象外です。
・ヒヤリングによる現場、現物、現実調査に よる現場の問題解決手法のひとつです。
・現場で対応できる再発防止案を拙速に提起
・新人の解析能力育成の訓練の為の手法
なぜなぜ分析の歴史
なぜなぜ分析はトヨタにて開発され、製造方法の改善手法として社内で使用され、現場での問題解決訓練の重要な一つでした。
TPSの開発者である大野耐一氏は、「5つの理由を繰り返すこ とで問題の性質とその解決策が明確になる」と述べている。
当初この方法を広めるにあたって『なぜ』を5回繰り返えすこと が推奨していたが、現在では、必ずしも5回にこだわる理由はな く、真の原因が追究できて2度と同じ不良が発生しない対策でき るかが重要です。
英語では5whysと訳されており根本原因解析(RCA)の現場での手法のひとつです。なぜなぜ分析≠RCAです。
根本問題解析手法の比較
根本問題解析手法(Root cause analysis (略:RCA)は問題や事象の根本的な原因を明らかとすることをねらいとしており、色々な手法があり、なぜなぜ分析もその中のひとつです。
慢性不良と突発不良
なぜなぜ分析は現場での突発性不良を対象にし、拙速に2度と不良が発生しない様、対策を立案します。
動画解説 問題を解決するなぜなぜ分析のやり方
トヨタ式なぜなぜ分析 事例
~『トヨタ生産方式』著:大野耐一より~
ある工場内のあるマシンが故障して停止した際に「なぜマシンは停止したか?」の問いに、「過負荷がかかって、ヒューズが断線」と答えただけではヒューズを交換して再起動すればいい、という答えしか返ってこない。
しかし、なぜ過負荷がかかったのか?→
(2)軸受部の潤滑が十分でないからだ、と究明し
さらに
(3)潤滑ポンプが十分組み上げていない→
(4)ポンプの軸が摩耗してガタガタになっている→
(5)ろ過器がついていないので切り子が潤滑油に入った。
まで徹底していくと、問題の真因がわかる。そこで、オイル循環系統にフィルターを設置すれば、マシンがたびたび停止するトラブルを恒久対策することができる。これが、大野耐一氏のいう、事実にもとづく科学的解析である。
トヨタ式なぜなぜ分析 事例~発生系分析事例~
トヨタ式なぜなぜ分析 事例~流出系分析事例~
トヨタ式なぜなぜ分析 事例~悪い事例1~
特性要因図のように現場の推測される要因を列記している例。
なぜなぜ分析は真の原因を追究するので現在の事実を対象にする。
トヨタ式なぜなぜ分析 事例~悪い事例2~
A社の製品のシャフト軸が破損しやすい、とのクレームが複数の顧客から入った。調査するとユーザ向けの運転保守マニュアルにある、シャフト軸の周囲の取付図と手順が、現物と異なっており、間違っていることが判明した。ユーザはこのマニュアルをみて保守点検・再組立したのだが、それが結果として破損が生じた。
この時の悪い事例のなぜなぜ分析は下記のとおり。
(1) なぜシャフト軸が破損する? → ユーザの保守点検時に取り付け位置をミス
(2) なぜユーザは取り付け位置を間違えるのか? → 保守点検マニュアルの記述がミス
(3) なぜ運転保守マニュアルの記述が間違っているのか? → 担当者がミス
(4) なぜ担当者はミスした? → 多忙で睡眠不足が続きミス
悪い事例の真因は規定以上の残業をしていた事になり、対策としては「担当者は規定以上の残業をしない事となった。
しかし、これは間違った『なぜなぜ分析』です、正しい『なぜなぜ分析』は個人のミスを追究するのではなく、システムの側に視線を向けられるように追究する事です。
よって良い事例の『なぜなぜ分析』では納期の余裕がないが真の原因になり、その対策として
設計・購買・製造のシステムの適切な納期すなわち、リードタイムの設定が対策となります。
なぜなぜ分析を進めていくと、人のミスやエラーが見つかることがありますが人間が介在する業務を行う以上は、人間のミスやエラーは避けられません。
しかし、なぜなぜ分析を進める中で、人のミスやエラーに固執すると真の原因がわからなくなくなります、大切なのは人のミスやエラーを原因とするのではなく「なぜミスやエラーが発生したのか?」という状況をシステム側から検討する事です。
実践 JIPM式 なぜなぜ分析
JIPM:Japan Institute of Plant Maintenance 日本プラントメンテナンス協会の事。
なぜなぜ分析とは、故障・不良を発生させている要因を思いつきで考えるのではなく「なぜ」「なぜ」と段階を追って規則的に漏れなく出すための分析方法です。
たとえば、設備の同一部品がたびたび壊れるという場合、壊れた部品をただ交換するだけでは一時的な応急処置にしかなりません。
・その部品がなぜ故障するのか、寿命なのか?
・過剰な振動や熱影響などのストレスを受けて、寿命より早く故障するのか?
・もしそうであるならば、ストレスの発生源は何か?
など、原因と疑わしき要因を列挙して要因ごとに調査し、不具合(欠陥)があれば対策を施して問題を解決していきます。
この要因を列挙する過程、つまり「なぜなぜ」と考える過程がなぜなぜ分析です
なぜなぜ分析の基本的な考え方
【原因と要因の違い】
「原因」=1つ。「要因」=複数。
「原因」=ある問題を起こしたもの。「要因」=ある問題に影響のあるもの。
以前の現場問題解析の不具合
・工程、設備の絞りこみができていない。データーで発生している問題の正確な工程、設備の絞り込みが重要です。
・現象の絞り込みができていない。事実の問題を正確にデーターで把握して集中して分析する。
・過去の経験(KKD:勘、経験、度胸)による問題解析で真の原因を見落とす。
JIPM式 なぜなぜ分析 7ステップ概要
以前の現場問題解析の不具合を解消する手法としてJIPMで考え出されたものが『なぜなぜ分析 7ステップ』です。
第一STEP 工程設備の絞り込み
故障や不良をデータでつかみ、対策効果の大きい工程や設備の改善に収り組むためには、絞込みが必要です。まず、どこに問題があるかをデータによって絞り込みます。(下図表)
また、問題の絞込みには層別の考え方が重要で す。故障、不良はいく つかの原因が重なり合っ て影響していることが多いからです。
このようなときには、ある特徴をもとにいくつかの 層に分けて調べてみると、重要な点が見えてきます。 このように層に分けることを層別化と呼びます。 (下図表)
第二STEP 現象の絞り込み
なぜなぜ分析で重要な事は『現象』を正しい把握する事です、これを行えば短時間で真の原因を見つける再発防止の改善案を立案することがで きます。
その為には事実として現象が実際に変化している箇所に見つけ、『集中』し、問題を絞ることです。
問題の要因は沢山あり、我々は時折、 誤った選択をします、それを防ぐため に現象の絞り込みを確実に行います。
第三STEP あるべき姿を把握、理論・原則を知る
次になぜなぜ分析を行う前に現象の発生メカニズム(理論)を知り、そ して現状を正確に調査する事が重要です。
具体に発生メカニズムを知る為には加工、現象に関する4Mと基本原理を知る必要があります。
4MとはMan(人)、Machine (機械)、Material (材料)、
Method(方法)の事であり4Mに問題なければ不良は発生しません。
原理とは「原(もと)となる理屈」「事実、事象の根本法則」であり多くの物事を成り立たせる、根本的な法則(規則)です。
要因が複数存在している場合、原因を追究する際にものづくりの原理、 原則を理解することが必要です。
ものづくりの原理、原則を知る
第四STEP 事実を正しく知る
再発防止の為には下記の事実を把握するポイントが重要です。
・現場、現物、現実を観察する・自分自身が見る
・思い込み、偏見を排除する ・目的を明確にして観察する
・さまざまな角度から見る ・比較してみる
現状を把握する方法には5W1H、4M、原理原則による現状把握があります。
第五STEP なぜなぜ分析
なぜなぜ分析とは、なぜ・なぜを繰り返して、事実を確認してい く手法です。すなわち、現象を引き起こすさまざまな要因をあげて、 そのひとつ、ひとつを調査していきます。 OKと判断した場合には次の要因調査に移ります。 その際、要因に漏れのないようにしなければなりません。そのためには、起こっている現象について、原理・原則を勉強して理解することです。
①分析対象
現象の把握が不十分であると分析要因が広がり、原因探しがぼやけて しまい、真の原因が追究できません。これは、現象の範囲を広く捉え過 ぎたことが原因です。
現象は現場・現物で見たままの事実を素直に表現し、1つの事象に絞り込むと分析展開をしやすくなり、真の要因の発掘を容易にさせます。
②あるべき姿からのアプローチ
不具合の要因とは「あるべき姿(条件)」が変化したものです。
機能を正常な状態で保つための必要な条件が欠落して、すべてが揃わない場合に不具合は発生します。
あるべき姿からのアプローチは、不具合に対し管理されていなければならな い項目(条件)は何かを分析前に調査し、その項目を現場・現物・現象に合わ せて比較、検証します。
そこで差があるモノだけに焦点を絞って「なぜそれが起こったのか」を系統的 に求め、これ以上、分解できない(再発防止策が打てる)ところまで分析をします。
別の言い方をすると「あるべき姿(良い結果を生む条件)」とその問題になっているモノ、事象とを比較することで、問題を探っていく方向性を決定します。
なぜなぜ分析 事例
第六STEP 復元と改善案の立案
真の原因で基準、標準が何らかの理由でズレてしまい不具合が発生する場合も多いのでその際はズレていた基準、標準を修正(復元)して、不具合が直るかを確認します。
基準、標準がズレがない場合は改善案の検討に入り具体的な対策を検討します。
第七STEP 標準化、水平展開
標準化:
改善で明確になった項目を基準書、標準書に落とし込み、維持していけるように標準化を行います、具体的は下記のように行います。
・維持すべき管理項目、管理周期を決める
・チェックシートなど管理の道具を活用する
・作業ルールを明確にする
・ワンポイントレッスンシートなどを作成して活用する
水平展開:
他の機械設備に水平展開することで、数倍の効果が期待できます。
改善項目が活用できる設備を検討し、それらへの展開計画を立てます。
なぜなぜ分析シート テンプレート フォーマット 無料ダウンロード
なぜなぜ分析シート テンプレート フォーマット エクセル版
ぜなぜ分析のExcelテンプレートを選ぶ理由
- 視覚化: 表形式で整理することで、問題と原因の関係を視覚的に捉えやすくなります。
- 共有: チームメンバー間で簡単に共有し、議論を深めることができます。
- 履歴管理: 分析過程を記録し、改善の進捗状況を把握できます。
- 再利用: テンプレートをカスタマイズすることで、様々な問題に対して繰り返し利用できます。
なぜなぜ分析のExcelテンプレートは、問題解決の強力なツールです。適切なテンプレートを選ぶことで、より効率的に問題の根本原因を究明し、改善策を立案することができます。
無料 なぜなぜ分析シート テンプレート フォーマット エクセル版
なぜなぜ分析シート テンプレート フォーマット パワーポイント版
なぜなぜ分析のPowerPointテンプレートのメリット
- 視覚化: 複雑な問題を図やグラフで表現することで、全体像を把握しやすくなります。
- 共有: チームメンバーと共有しやすく、議論を深めることができます。
- 記録: 分析結果を記録し、後から振り返ることができます。
- プレゼン: 上司や関係者に成果を報告する際に役立ちます。
なぜなぜ分析のPowerPointテンプレートは、問題解決の強力なツールです。視覚的に分かりやすく、論理的な思考の流れを表現することで、チーム全体で問題解決に取り組むことができます。
無料 なぜなぜ分析シート フォーマット テンプレート パワーポイント版
なぜなぜ分析 事例集
技術問題とは、モノづくりの現場では、不良、故障、チョコ停、品違い、労災などの固
有技術そのものの問題を言います。また事務・サービス部門では、設計ミス、伝票起票ミ
ス、受注の失敗、計画遅れなど「失敗」の問題を言います。
ここで説明する分析方法は、一般に言われる「問題解決型分析方法」と解釈してください。
又、ソフト課題とは、「不良が減らない」「故障が減らない」といった固有技術の問題を「減
らす活動」や「売上が伸びない」「利益が伸びない」「QCサークル活動がうまく進まない」
といった課題のことを言います。ソフトウェアのソフトとは違います。
ここで説明する分析方法は、一般に言われる「課題解決型分析方法」のことです。
基本的には、技術問題の分析方法もソフト課題の分析方法も、その考え方は同じですが
問題の性質上、若干進め方が異なります。
問題解決型 なぜなぜ分析 事例集
技術問題の分析事例のまとめ方は次の要領です。
①発生現象(不具合現品の調査、観察結果のまとめ)
②発生の性質(必要な情報の調査事項とその調査結果のまとめ)
③加工点(作用点)の構造(絵または図で表して、そこから見える「推定メカニズム」
とその「検証方法」および「結果」のまとめ)
④なぜなぜ分析(メカニズムからその要因を系統図法で深堀りして真因を見極める)
事例1:製品の外径寸法 規格外れ
①発生現象(現物調査結果)
不良内容(発生数3ヶ)
規格を外れる値はプラス側に0.005とプラス側に0.007及び同じくプラス側に0.009mm
②発生性質(現状把握)
・ロットバラツキの確認
バラツキが大きくなった。カタヨリがプラス側に変化している。
不良品は規格を大きく外れてなく同一ロットのバラツキの範囲内と考られる
・カット刃交換前後のバラツキ
其の他 工程の変化点情報を把握する。
③加工点〔作用点)構造
加工点〔作用点)構造を把握するためにスケッチしたり、取扱い説明書、図面等で調査する。
不良推定メカニズムとその検証方法
④問題解決型 なぜなぜ分析
不良推定メカニズム毎になぜなぜ分析を行う。
⑤なぜなぜ分析 考察
この例のような外径寸法にこだわらず、こうした寸法に関する問題は、必ずヒストグラムを求めてバラツキの範囲内、つまりバラツキの大きさの問題なのか、バラツキの外の問題なのかをしっかり見極めることが重要です。
また、寸法精度だけでなく、テーパー、段付といった形状の問題、粗さなど面性状を細かく観察することも大事です、 ほんのちょっとした情報からメカニズムは見えてくる場合が多いのです。
その他、同じような工程を有する他ラインの情報も集めます。
他ラインとの方法の違いが見つかれば、そこからメカニズムは見えてきます。
こうした比較する見方「差の分析」は、特に寸法問題に限らず全ての問題点解決に有効な分析方法です。
課題解決型 なぜなぜ分析 事例集
ソフト課題の分析事例のまとめ方は次の要領です。
①構図(活動のプロセスやあるべき姿を図に表す)
②分析するべき理屈の絞り込み「事実情報の整理から、分析する「理屈」を特定する)
③なぜなぜ分析(理屈からその要因を系統図法で「なぜなぜ」と深堀りする)
④課題3要素でまとめ(連関図法を使って問題の本質を見極める)
事例1:人材のスキルが育成できない
①構図(活動のプロセス)
②現状把握(事実情報の整理)
スキルアップについての問題点を管理者で意見交換して集約。
③なぜなぜ分析
ソフト課題のなぜなぜ分析をする。
④課題3要素(問題の本質の見極め)
QC手法のひとつである『連関図法』を使用して出てきた要因を整理し、本質を絞り込む。
⑤考察
「人材(スキル)が育だない」という問題の本質の原因は「日頃、技術について意見を交わす機会が少ない」です。
スキルを磨くためには、「日頃、技術について意見を交わす機会が少ない」という「環境」の問題が、その本質です。
更に詳細の内容は下記の本に記載されています。
参考文献:なぜなぜ分析 分析事例集
なぜなぜ分析とロジカルシンキングの関係
なぜなぜ分析は、ロジカルシンキングを具現化する具体的な手法の一つです。なぜなぜ分析を繰り返すことで、論理的な思考力、問題解決能力、そして創造性を高めることができます。
なぜなぜ分析とロジカルシンキングは、一見異なる概念のように思えますが、実は密接な関係があります。
なぜなぜ分析とは?
なぜなぜ分析は、問題が発生した際に、その根本原因を究明するために、「なぜ?」という問いを繰り返していく手法です。問題の表面的な原因だけでなく、その奥底にある真の原因を探り出し、根本的な解決策を見つけることを目指します。
ロジカルシンキングとは?
ロジカルシンキングは、論理的な思考に基づいて問題を分析し、解決策を導き出す思考法です。客観的な事実やデータに基づいて、論理的に考え、判断することを重視します。
なぜなぜ分析とロジカルシンキングの関係性
なぜなぜ分析は、ロジカルシンキングを具体的に実践する一例と言えます。
- 共通点
- 問題解決: 両者とも、問題解決を目的としています。
- 論理的思考: なぜなぜ分析は、論理的な思考に基づいて原因と結果の関係を辿っていきます。
- 客観性: 客観的な事実やデータに基づいて分析を進めます。
- 相乗効果
- 根本原因の特定: なぜなぜ分析は、ロジカルシンキングの力を借りて、問題の根本原因を正確に特定することができます。
- 効果的な解決策: 根本原因が特定できれば、より効果的な解決策を導き出すことができます。
- 思考力の向上: なぜなぜ分析を繰り返すことで、ロジカルシンキングの力が鍛えられます。
なぜなぜ分析がロジカルシンキングを育む理由
- 構造的な思考: なぜなぜ分析は、問題を構造的に捉え、因果関係を整理する力を養います。
- 仮説検証: それぞれの「なぜ」に対して仮説を立て、それを検証していくことで、論理的な思考が鍛えられます。
- 批判的思考: 仮説が正しいかどうかを客観的に評価し、批判的に考える力が養われます。
なぜなぜ分析の誤解と注意点
なぜなぜ分析は、問題の原因を深く掘り下げていく上で非常に有効な手法ですが、誤った使い方や注意点を知っておくことで、より効果的に活用することができます。
なぜなぜ分析に対するよくある誤解
- 無限に続ける?: なぜなぜ分析は、ある程度深掘りすれば、最終的に人為的な要因や、もはや解明できないレベルに達することがあります。無限に続けるのではなく、問題解決に繋がる深さまで掘り下げることが重要です。
- 原因は一つだけ?: 問題の原因は、複合的な場合がほとんどです。一つの原因に固執せず、複数の要因が絡み合っている可能性も考慮しましょう。
- 原因が分かれば解決できる?: 原因が分かっても、それを解決するためのリソースや制約がある場合があります。現実的な解決策を模索することが重要です。
なぜなぜ分析を行う上での注意点
- 目的意識を持つ: なぜなぜ分析の目的は、問題解決です。目的を見失わず、分析を進めましょう。
- 客観的な視点: 主観的な意見や感情ではなく、事実やデータに基づいて分析を進めることが重要です。
- 深掘りしすぎない: 深掘りしすぎると、本質から離れてしまい、かえって問題解決の妨げになることがあります。
- チームで実施: 一人で行うよりも、チームで実施することで、多角的な視点から問題を捉え、より良い解決策を見つけることができます。
- 記録を残す: 分析の過程や結果を記録しておくことで、後から振り返ったり、他の問題解決に活かすことができます。
- 解決策に繋げる: なぜなぜ分析は手段であり、目的ではありません。最終的には、分析結果に基づいた具体的な解決策を提案することが重要です。
なぜなぜ分析の陥りやすい罠と対策
- 原因の特定にばかり注力してしまう: 原因の特定も重要ですが、解決策の検討も並行して行うことが大切です。
- 特定の人に責任転嫁: 問題の原因を特定する際に、特定の人に責任を押し付けてしまうことは避けましょう。
- 過去の事例に固執する: 過去の事例は参考になりますが、必ずしも現在の問題に当てはまるとは限りません。
- 複雑な問題を単純化しすぎる: 問題は複雑な場合が多いので、単純化しすぎると、重要な要素を見落としてしまう可能性があります。
*なぜなぜ分析は、問題解決のための強力なツールですが、正しく理解し、注意点を踏まえて実施することが重要です。目的意識を持ち、客観的な視点で分析を進め、チームで協力しながら、問題解決に繋がる具体的な行動に移しましょう。
ChatGPTによる「なぜなぜ分析」プロンプト指示と注意点
ChatGPTへの役割の設定
まず、ChatGPTに対して「どんな立場で回答してほしいか」を明確に伝えることが重要です。
プロンプト例:
あなたは製造業の品質管理に精通したコンサルタントです。これまで多数のなぜなぜ分析(5 Whys)を指導してきました。
理由:
このように役割を設定すると、回答の視点がブレず、専門的かつ現場に即した内容が期待できます。
問題提示のコツ
問題は「簡潔に、具体的に」伝えるのがポイントです。
プロンプト例:
製品Aに貼られるラベルに誤表示がありました。今週3件、夜勤シフト中にラインAで発生しています。正しいラベルが在庫にあるにもかかわらず、違う製品のラベルが貼られました。
補足情報を加えるとより効果的:
-
どの工程で問題が発生したか
-
誰が気づいたか、いつからか
-
過去にも同様の事例があったか
ChatGPTへの分析依頼と出力形式の指示
プロンプト例:
上記の問題について、「なぜ?」を5回繰り返して、原因を深掘りしてください。
各ステップは「なぜ1」「なぜ2」…と順番に番号を振ってください。
最後に、考えられる根本原因と再発防止策を提案してください。
出力形式の指示を追加すると明確になります。
例:
なぜ1:〜だから。
なぜ2:〜が原因で。
…
なぜ5:根本的な原因は〜である。
対策案:〇〇を導入することで防止可能。
現場で使う際の注意点
ChatGPTの出力は“仮説”である
-
AIは過去データと一般的知識から推論しているだけ。
-
実際の現場確認やデータ検証が必須です。
入力する情報の質が結果を左右する
-
抽象的すぎると曖昧な答えに。
-
具体的な事実・背景を伝えることが重要。
機密情報には要注意
-
ChatGPTは外部サービス。企業秘密や個人情報は入力しないように。
活用シーンとメリット
活用場面 | 期待できる効果 |
---|---|
問題発生時の初動分析 | 短時間で原因候補を洗い出せる |
複数メンバーでの会議前 | 仮説として議論材料を準備できる |
新人教育 | 分析手法を体験的に学べる |
ChatGPTは「なぜなぜ分析」を効率的に進めるための有力な補助ツールです。しかし、「人間の知見・検証」と組み合わせてこそ真価を発揮します。道具として賢く使い、最後の判断は現場で。
ChatGPTでなぜなぜ分析を行うためのチェックリスト
ChatGPTへの役割設定
-
「あなたは品質管理の専門家です」と明示した
-
現場に即した立場(製造業、ライン担当など)を指定した
問題の提示
-
問題を一文で具体的に書いた(例:ラベル貼りミス)
-
発生場所・時期・頻度などの背景情報を含めた
-
参考要因(作業手順、人員、教育、機器)を示した
出力形式の指示
-
「なぜ1」〜「なぜ5」の形式を明示した
-
箇条書き or 番号付きで出力するよう指示した
-
最後に「根本原因と対策提案」も求めた
使用時の注意
-
ChatGPTの出力は「仮説」であり、現場検証が必要
-
実際のデータや事実で確認する工程を含めている
-
社外秘や個人情報などを含まないよう注意した
活用目的の確認
-
初動対応の迅速化(仮説のたたき台として使用)
-
会議資料・ブレスト用の原因候補整理に使用
-
新人教育・指導の補助ツールとして使用
このチェックリストは、印刷して現場のデスクや会議室に貼っておくのもおすすめです。
下記から『word版 ChatGPTによるなぜなぜ分析チェックリスト』をダウンロードしてください。
まとめ
なぜなぜ分析は真の原因を追究するために細部まで分析をすすめる方法です。
おおきな事故、問題の真の原因は小さな要因を放置することから始まります。
誰もが気が付かない、見えない小さなところに潜んでいます。
日本では建築家のミース・ファン・デル・ローエの『神は細部に宿る』の言葉が有名ですがアメリカで最近、ミースより半世紀ほど前のGustave Flaubertが唱えた言葉がポピュラーだそうです。
the devil is in the details
悪魔は細部に宿る(諺:あらゆる細部に落とし穴が潜む)
細部には神も悪魔も棲んでいます、それを見つけ、活かすか、殺すかは貴方しだいです。
関連キーワード:
なぜなぜ分析 5why 根本原因分析 問題解決 改善 カイゼン
参考文献:
1.トヨタ生産方式―脱規模の経営をめざして 大野 耐一 (著)
小松 正 (監修), JIPMソリューションなぜなぜ分析研究会 (編集)
なぜなぜ分析 資料 無料 ダウンロード
Googleスライド版 図解 なぜなぜ分析:5Whys
パワーポイントのファイル形式でダウンロードできます。
slideshare ダウンロード資料(PDF) 図解 なぜなぜ分析:5Whys
slideshare ダウンロード資料(PDF)パワーポイントで作成した資料です。
Googleスライド資料(パワポイント版) なぜなぜ分析 演習問題
なぜなぜ分析 演習問題現場でのなぜなぜ分析の具体的事例をにGoogleスライドにアップ
slideshare ダウンロード資料(PDF) なぜなぜ分析 演習問題
なぜなぜ分析 演習問題現場でのなぜなぜ分析の具体的事例をスライドシェアーにアップ
コメント